Monitoring aviation gas turbines
R. David Whitby | TLT Worldwide November 2017
Taking a more proactive approach, manufacturers increasingly are using complex engine management systems.
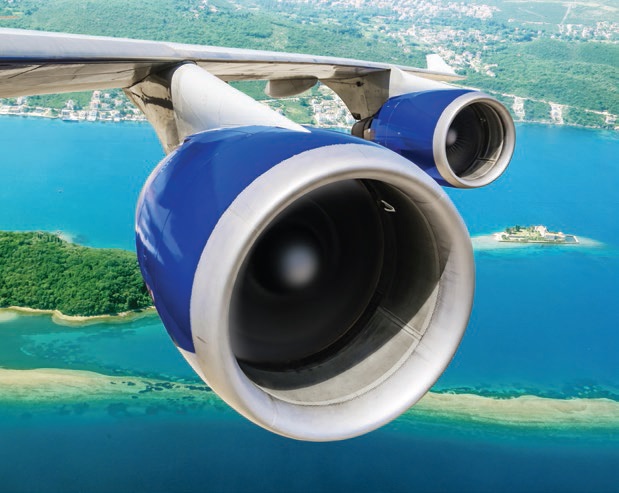
Engine Health Management is a pro-active technique for predicting when something might go wrong and averting a potential threat before it has a chance to develop into a real problem.
© Can Stock Photo / toshket
OILS USED IN ALL MODERN AVIATION GAS TURBINES are polyolester based, with high-performance oxidation inhibitors, corrosion inhibitors, load-carrying additives and deposit control additives. The specifications for these oils are very onerous and, consequently, their performance properties are exceptional. Aviation gas turbine oils are not routinely monitored, as there is almost always a loss of oil during flight and significant oil top-up between flights. Instead, the engines are very closely monitored during flight. Any issues that may be due to oil oxidation, thermal degradation, deposit formation or wear metal generation will quickly show up in engine operation and will be corrected shortly after the plane lands and before the next flight.
Manufacturers of these engines, such as General Electric and Rolls-Royce, use complex engine management systems to monitor the condition of their engines continuously during operation. Rolls-Royce, for example, uses Engine Health Management (EHM) to track thousands of engines operating worldwide using onboard sensors and live satellite feeds. EHM is a pro-active technique for predicting when something might go wrong and averting a potential threat before it has a chance to develop into a real problem. EHM uses a range of sensors strategically positioned throughout the engine to record key technical parameters. Up to 25 sensors monitor numerous critical engine characteristics such as temperatures, pressures, speeds, flows and vibration levels to ensure they are within known tolerances and to highlight when they are not. In the most extreme cases air crew could be contacted, but far more often the action will lie with the operator’s own maintenance personnel or a Rolls-Royce service representative in the field to manage a special service inspection.
The main engine parameters, shaft speeds and turbine gas temperature are used to give a clear view of the overall health of the engine. A number of pressure and temperature sensors are fitted through the gas path of the engine to enable the performance of each of the main modules (fan, intermediate and high-pressure compressors and high-, intermediate- and low-pressure turbines) to be calculated. These sensors are fitted between each module, except where the temperature is too high for reliable measurements to be made.
Vibration sensors provide valuable information on the condition of all the rotating components. An electric magnetic chip detector is fitted to trap any debris in the oil system that may be caused by unusual wear to bearings or gears. Other sensors are used to assess the fuel system (pump, metering valve and filter); the oil system (pump and filter); the cooling air system; and the nacelle ventilation. As engine operation can vary significantly between flights (due to day temperature or pilot selection of reduced thrust), data from the thrust setting, ambient conditions and bleed extraction status also is used.
Oil pressure and temperature are measured in each engine, with displays in the cockpit. A low-pressure warning light is usually included and should not be illuminated during engine operation. Exhaust gas temperature is an indirect indication of turbine inlet temperature. For a long service life of the turbine blades and burner cans, these temperatures may not exceed manufacturer limits under all circumstances.
As soon as the individual reports arrive at the specialist EHM analysts, they are processed automatically. The data is checked for validity and corrections applied to normalize them. The data is always “trended” so subtle changes in condition from one flight to another can be detected. Automated algorithms based on neural networks are used, and multiple sensor information is fused to provide the most sensitive detection capability.
When abnormal behavior is detected, it is confirmed by an analyst based in the operations center before being sent to the aircraft operator and logged by the Rolls-Royce technical help desk. Manual oversight is still an important part of the process, as false alerts can cause unnecessary maintenance actions to be taken by airlines, and these need to be avoided. Trended data also are uploaded onto the Rolls-Royce customer Website so that plane operators can easily view the health of their fleet of engines.
David Whitby is chief executive of Pathmaster Marketing Ltd. in Surrey, England. You can reach him at pathmaster.marketing@yahoo.co.uk.