The chemistry and function of lubricant additives
Debbie Sniderman, Contributing Editor | TLT Webinars November 2017
Their effectiveness depends on the base oil and how they interact with other chemicals.
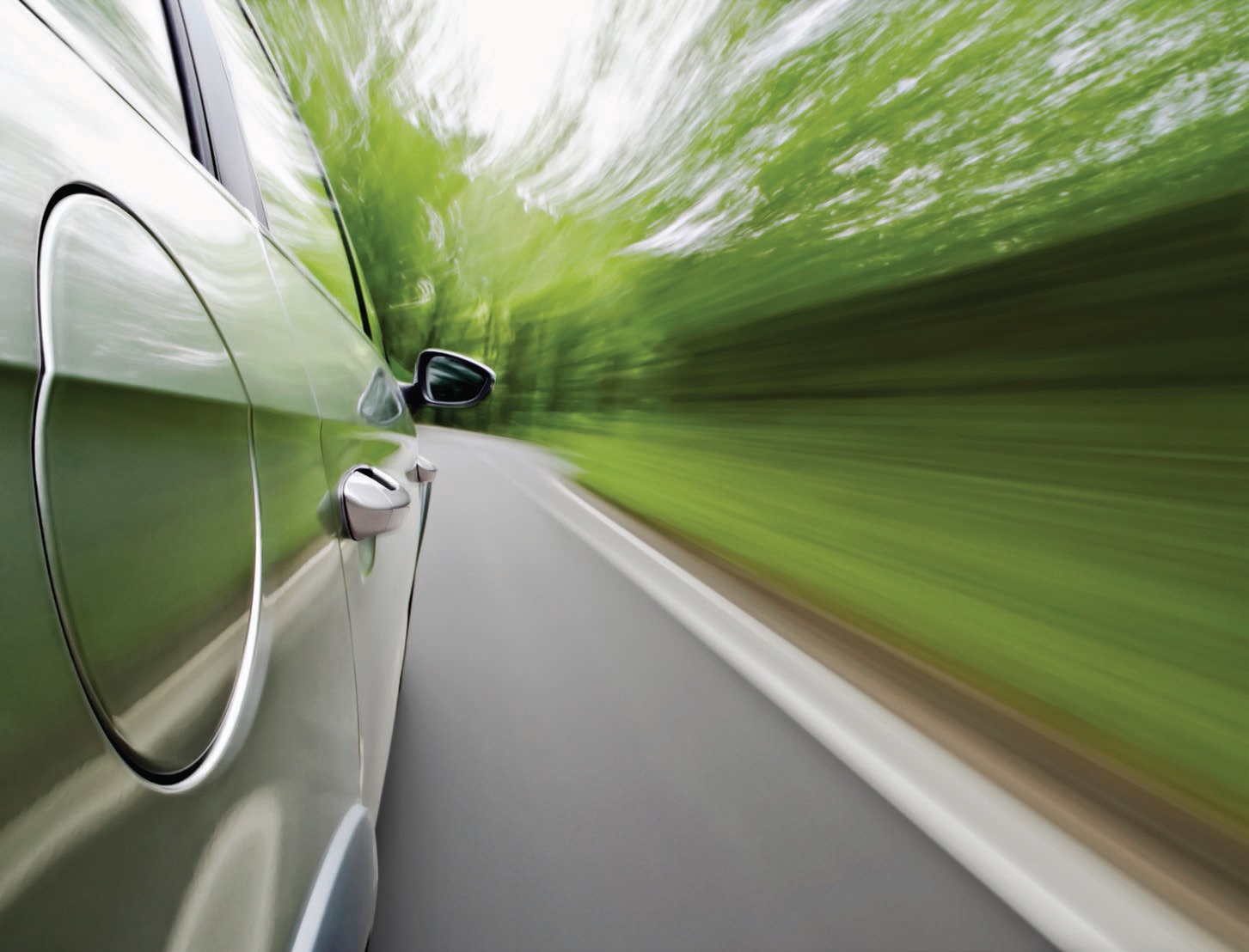
KEY CONCEPTS
•
Additives compensate for the deficiencies inherently present in basic base oil systems.
•
Additive effectiveness depends on the oil. An additive that works well in one oil might not in another.
•
It’s important to understand how additives may interact with each other in synergistic or antagonistic ways when creating additive packages.
MEET THE PRESENTER
This article is based on a Webinar originally presented by STLE Education on June 17, 2015.
The Chemistry and Function of Lubricant Additives is available at
www.stle.org: $39 to STLE members, $59 for all others.
Vincent Gatto has worked for 30 years as a research, applications, technical service and product development scientist in the area of lubricant, fuel and polymer additives. He is currently research director for Vanderbilt Chemicals, LLC, in Norwalk, Conn., working to discover and develop new chemicals for use as additives in the lubricant, rubber and plastics industries. He also directs and prioritizes projects in the Petroleum Applications Laboratory.
Gatto holds approximately 110 U.S. patents, patent applications and technical publications in the areas of chelation, additives for polymers, lubricants and fuels. He was R&D and technical service manager at Albemarle Corp. for 11 years and a lubricant additive scientist at Ethyl Corp. (now Afton Chemical Co.) for 16 years. He received his doctorate in chemistry from the University of Maryland and held a postdoctoral position at the University of Miami. You can reach Dr. Gatto at
vgatto@vanderbiltchemicals.com.
Vincent Gatto
LUBRICANTS ARE USED TO REDUCE FRICTION AND WEAR, dissipate heat from critical parts of equipment, remove and suspend deposits that may affect performance and protect metal surface damage from degradation and corrosion. They serve a diverse range of applications, each requiring a different combination of base oils and additives. With such a complex industry, there are many challenges to developing effective lubricants.
Base oils themselves perform most of the functions of lubricants. But they can only do part of the job. Additives are needed when a lubricant’s base oil doesn’t provide all the properties the application requires. They’re used to improve the good properties of the base oils and minimize the bad. They compensate for the deficiencies inherently present in basic base oil systems (
see Examples of Engine and Non-Engine Lubricants).
EXAMPLES OF ENGINE AND NON-ENGINE LUBRICANTS
Engine Lubricants
Gasoline engine oils
Diesel engine oils
•
Heavy duty
•
Off-road
•
Automotive
•
Stationary
Medium-speed engine oils in:
•
Railroad
•
Marine
Natural gas engine oils
Aviation engine oils
Two-stroke cycle engine oils
Non-Engine Lubricants
Transmission fluids
•
Automatic
•
Manual
Power steering fluids
Shock absorber fluids
Gear oils
•
Automotive
•
Industrial
Hydraulic fluids
Metalworking fluids
Turbine oils
Misc. industrial oils
Greases
Typical lubricants are composed of a base oil, an additive package and, optionally, a viscosity index (VI) improver. Turbine, hydraulic and industrial gears demand much lower treat rates of additive packages compared to automotive gear, ATF and gasoline and diesel engines, which are the most demanding and require the most additives (
see Figure 1).
Figure 1. Composition of base oil, VI improver and additive packages in typical lubricants. (Figure courtesy of Vanderbilt Chemicals, LLC.)
Additives are combined into well-balanced, optimized packages allowing lubricants to meet specified performance criteria in a finished fluid. One example of an additive package is the dispersant inhibitor (DI) package used for engine oils, containing mainly dispersants, detergents, oxidation inhibitors, antiwear agents and friction modifiers. Additives may interact with each other and may have multi-functional properties. Each additive package is a unique blend whose combination produces a complex chemistry with positive and negative interactions (
see Figure 2).
Figure 2. Example of Dispersant Inhibitor (DI) additive package for engine oils. (Figure courtesy of Vanderbilt Chemicals, LLC.)
THE NEED FOR FRICTION MODIFIER ADDITIVES
One of the key functions of lubrication is to reduce friction and wear when moving metal parts are in contact. The Stribeck curve illustrates how friction reduction takes place in a lubricant. In the boundary regime at low speeds, low viscosity or high loads, a lubricant has high friction due to metal/metal contact in the presence of a very thin film of oil. As the speed or viscosity increases, or load decreases, the system moves into the mixed regime where friction is significantly reduced in the lubricant mainly due to a thicker oil film and greater separation between the metal surfaces (
see Figure 3).
Figure 3. The Stribeck curve illustrates lubricant friction regimes. (Figure courtesy of Vanderbilt Chemicals, LLC.)
Both the boundary and mixed-film lubrication conditions can be detrimental to machinery. Without additives, this contact will lead to significant system wear and premature field failure. Properly selected friction modifier additives can significantly reduce the coefficient of friction in these regimes. Low friction can best manifest itself as an improvement in an engine’s fuel efficiency (
see Figure 4).
Figure 4. Friction modifier additives help reduce friction in boundary and mixed-lubrication regimes. (Figure courtesy of Vanderbilt Chemicals, LLC.)
THE NEED FOR ANTIOXIDANT ADDITIVES
When exposed to heat, oxygen and metal contamination, lubricants undergo oxidation. Base oils can perform many lubrication functions, but they can’t protect against the detrimental effects of oil oxidation.
Oxidation creates polymers, oil insoluble high-molecular-weight molecules that increase the viscosity of the lubricant, accelerate wear and eventually leads to varnish. The hard “baked on” polymeric coating of varnish also accelerates wear and is a long-term detriment.
Oxidation also creates sludge, a soft oil-insoluble material made of combustion byproducts that suspend in oil. If it remains too long, sludge can plug oil lines and filters leading to oil starvation in the machinery and adhere to metal surfaces, accelerating wear. Along with other hard accumulations of sludge and varnish typically on pistons and valves in engines, deposits due to oxidation can cause valve and ring sticking, eventually leading to catastrophic increase in wear (
see Figure 5).
Figure 5. Mechanisms of lubricant degradation motivating the use of antioxidant additives. (Figure courtesy of Vanderbilt Chemicals, LLC.)
There is good news however. Even though lubricant degradation processes are complex, the solution is straightforward. Antioxidant additives minimize oxidation and deposit formation. Detergents and dispersants also play a role in mitigating the effects of sludge and deposits.
ADDITIVE USE AND TYPES
An additive’s effectiveness depends on where it’s used. For example, an additive may work well in one oil and not in another. Polar additives compete with each other for metal surfaces. Many additives exhibit either synergistic or antagonistic effects with other additives present in the system. Synergism gives the opportunity to use less overall additives. But antagonistic effects may prevent the use of certain types, and more may be needed to overcome the antagonistic effect.
The dosage or treat rate also depends on the system. Usually effectiveness diminishes as dosage increases. But some additives may need to reach a threshold dosage before becoming active. The dosage is affected by synergism or antagonism with other additives in the oil. Actual treat rates have to be based on specifications and performance requirements.
There are two types of additives: bulk oil additives and surface additives. Bulk additives affect the rheological, interfacial and chemical properties of the lubricant, and surface additives are active at metal surfaces (
see Figure 6).
Figure 6. Lubricant additive types. (Figure courtesy of Vanderbilt Chemicals, LLC.)
DISPERSANTS
Dispersants are non-metallic, ashless cleaning agents that inhibit sludge from forming at low to moderate temperatures. Dispersants make up between 4%-13% of fully formulated oils, and most are diluted with 50%-75% by weight in mineral oil to lower their viscosity and improve handling properties.
Dispersant molecules have a hydrophilic polar head that attaches to agglomerates and a long-chain hydrophobic hydrocarbon tail that functions as a solubilizer. As oxidation occurs in hydrocarbons, polymeric products of oligomerization tend to agglomerate and form soluble particles in the oil. Dispersants’ polar heads attach to these soluble particles and their tails face into the oil, suspending the surrounded particle in the oil, making it look more oil like and preventing it from plugging filters and screens. In this way, they arrest growth and control agglomeration so particles don’t fall out of the oil and become insoluble.
Typical structures are N-substituted long-chain alkenyl succinimides, succinate esters, phosphorus dispersants and mannich bases. The many types of dispersant molecules all have polar functionality in the head group and oil solubilizing tails of either polyisobutylene or polypropylene. The polar head group usually contains oxygen, nitrogen, phosphorus or sulfur atoms to aid in dispersion.
The main polar head group can contain polyamine or polyol. The linking group (succinyl, phenol, phosphate or none) attaches the head to the tail and is an artifact from how the dispersant is made. Caps are a term for a final group of chemistries added to alter overall properties of dispersants. Different types can offer supplemental corrosion and wear properties, act as antioxidants or improve seal compatibility. Most dispersants contain amine functions that are aggressive to Viton® seals. Glycolic acid, boric acid, molybdenum oxide and formaldehyde are frequently added caps to improve compatibility and properties.
DETERGENTS
Detergents are cleaning agents that contain metals. They work at high temperatures to reduce or remove deposits on surfaces and also in the bulk of the oil. They also neutralize acids and provide rust protection. Between 1% and 2% by weight are used in fully formulated oils, and like dispersants, most also are diluted with mineral oil by approximately 50% by weight to improve handling.
They have a similar structure to dispersants, with a polar head and a long, non-polar hydrophobic tail, but detergents contain a metal salt on an acidic organic molecule in the polar head. The other main difference between the two is where they function—dispersants function in the bulk of the oil and detergents clean at the surface of metal parts.
In hydrocarbons, insoluble gum particles fall out of the oil. Since they are polar, they are attracted and stick to polar metal surfaces. Effective detergents act as surfactants when their polar ends stick on polar surfaces and produce a film that displaces gum deposits from the metal surface. The cleaning effect depends on the oil and metal surface temperatures and how quickly gum particles bake on the metal surface.
Depending on the application, overbased and neutral detergents are used. Overbasing gives a detergent a way to neutralize acids formed during combustion or lubricant oxidation. A calcium sulfonate micelle structure is an example of a highly overbased detergent, with calcium carbonate molecules in the structure’s core available to neutralize acids. In the non-overbased portion of the same molecule, neutral calcium sulfonate molecules provide the surface activity to prohibit gum buildup.
Neutral detergents most commonly used in lubricants have structures involving neutral calcium. Salicylates are extensively used in engine oils. Naphthalene sulfonates are used more in industrial fluids, grease and metalworking fluids. Phenates, sulfonates and sulfurized phenates also are used.
ANTIOXIDANTS
Antioxidants inhibit oil oxidation and are the primary defense against lubricant degradation. They prevent viscosity increase and suppress deposit, sludge and varnish formation. They are usually low molecular weight liquids, solids or oil dilutions and are used between 0.1% and 2% by weight in fully formulated oils.
Antioxidants contain primary and secondary types working synergistically to suppress lubricant degradation when combined. Primary antioxidants are radical scavengers that turn reactive peroxy radicals into more stable hydrogen peroxide. However, at elevated temperatures, some hydrogen peroxides are unstable and detrimental. Secondary antioxidants are peroxide decomposers that consume unstable hydrogen peroxides and form stable alcohols.
The two main primary antioxidants are hindered phenolics and aminics, and the application determines which to use. Di-tert-butylphenol (DTBP) and butylated hydroxytoluene (BHT), two hindered phenolics, are inexpensive but are too volatile for certain applications. Methylenebis(2,6-di-tert-butylphenol) (MBDTBP) (a hindered phenolic) and alkylated phenyl-alpha-naphthylamine (APANA) (an aminic) are solids and can be difficult to handle in blending operations. Iso-octyl-3,5-di-tert-butyl-4-hydroxy-hydrocinnamate (BHC) and alkylated diphenylamine (ADPA) are the antioxidants most commonly used because they are fully liquid materials with very low volatility and excellent performance properties.
Secondary antioxidants either contain sulfur or phosphorus. Selection is based on thermal stability levels and whether sulfur is to function as an antioxidant, a corrosion inhibitor or a corrosion promoter. Sulfurized alkylphenols contain both sulfur, which acts as a secondary antioxidant, and phenolic, which acts as a primary antioxidant providing multi-functional behavior. Dithiocarbamates, sulfurized olefins and phosphites are examples of secondary antioxidants.
SURFACE ACTIVE ADDITIVES
Surface active additives reduce friction and wear at the interface of rubbing surfaces. Friction modifiers (FM), antiwear (AW) and extreme pressure (EP) additives all form adsorbed layers of surface films that prevent surface asperity contact, reducing fatigue and corrosive wear each in different ways.
Generally FM additives function by reversible or pseudo-reversible adsorption processes. AW and EP additives chemically alter metal surfaces, forming strong, glass-like elastic materials that perform AW or EP functions.
ANTIWEAR ADDITIVES
AW additives are effective at moderate loads and temperatures. They are used between 0.25% and 3% by weight in fully formulated oil. Depending on the amounts of oxygen present, the applied load and oil temperature, they form durable films mainly composed of sulfate, sulfide and polyphosphates of zinc, iron or other cation species. These films are replenished as long as the additive is present.
Most AW additives are phosphates, and many are supplemented with sulfur or molydenum-containing compounds or other metals to alter performance. Tricresyl phosphates (TCP), amine phosphates, molybdenum dithiocarbamates (MoDTC) and molybdate esters are typical AW additives, but zinc dialkyl dithiophosphate (ZDDP) is the most widely used because of its superior performance in many applications.
There are two types of ZDDP, primary formed from primary alcohols that have greater thermal stability and less volatile phosphorus, which benefits engine oil applications but less effective antiwear action. Secondary ZDDP comes from secondary alcohols and have more effective antiwear action but lower thermal stability and more volatile phosphorus, which is detrimental in engine oils.
The complex zinc and iron-based polyphosphates and glassy films that form on metal surfaces from ZDDP increases modulus under high loads and temperatures allowing the film to maintain integrity and have ‘smart’ behavior. The film becomes stronger when load increases, like during engine startup, to enhance the antiwear benefits when they are needed most. For this reason ZDDP’s effectiveness at protecting machinery of all types against wear is superior to most other options (
see Figure 7).
Figure 7. Mechanism of ZDDP wear protection. (Figure courtesy of Vanderbilt Chemicals, LLC.)
Even though ZDDP is the workhorse and industry standard for transmission and internal combustion engines, limits on its use in engine oils has been mandated because of concerns around phosphorus as a catalyst poison for emission control systems, and zinc, which contributes to ash contents and has detrimental effects on diesel engine diagnostic systems (
see Figure 8).
Figure 8. Yellow lines show circulation path of oil in a typical internal combustion engine to lubricate critical components. The oil pump passes oil through a screen sump strainer and filter for coarse and fine cleaning, then through passages in the engine block and back to the sump where the cycle repeats. Bypass valves ensure oil will reach the engine in case of blockage and ensures continued lubrication. Lubrication also is accomplished by splashing caused by rotation of the crankshaft. (Figure courtesy of Machinery Lubrication magazine.)
For this reason, there is growing interest in ashless AW additives. Two types are thiophosphate based, which contain phosphorus and sulfur, and phosphate based, which contain only phosphorus. Selection depends on the application. Those with higher thermal stability are used in aviation applications. Those containing amines are less compatible with elastomer seals.
EP ADDITIVES
EP additives are used under highly loaded conditions to prevent welding. There are two types, sulfur based (DMTD derivatives, sulfurized olefins, sulfurized fats and oils and dithiocarbamates) and molybdenum based (dithiocarbamates, dithiophosphates).
Typical EP additives contain sulfur compounds, molybdenum derivatives and chlorine compounds. The key feature between the different types is the activation temperature.
Selection depends on the reactivity in an application. Using a highly reactive substance may result in corrosion, so it is important to balance corrosion and high concentrations against maximizing the EP additive’s effect. Chlorinated structures are the least reactive, followed by phosphorous compounds. Sulfur compounds have the highest reactivity (
see Figure 9).
Figure 9. Activation temperature in EP additives. (Figure courtesy of Vanderbilt Chemicals, LLC.)
FRICTION MODIFIERS
FM additives form slippery physical or chemical boundaries between metal surfaces and oil to reduce friction. They are used up to 1% by weight in fully formulated oil and are typically used at higher levels in modern engines because they improve fuel economy. Their effectiveness varies greatly with engine design and type of lubricant formulation used.
Surface active FMs are organic friction modifiers whose polar heads contain oxygen, nitrogen or boron. Many are derivatives of oleic or laurel acids. Chemically reactive FMs are typically molybdate esters, molybdenum dithiocarbamates or molybdenum dithiophosphates. Metallic FMs are molybdenum based and are well known as one of the most effective in the industry. FM lubricants also are available in solid molybdenum disulfide, graphite and PTFE types.
VISCOSITY INDEX IMPROVERS
VI improvers minimize relative viscosity changes with temperature, increasing it at high temperatures and reducing it at low. They show solubility and conformational changes with changes in temperature and extend the operating range of oils to higher temperatures without adversely affecting their low-temperature fluidity. These oil-soluble organic polymers with high molecular weights (10,000-1,000,000) are used to produce multi-grade engine oils and automatic transmission fluids. Common treating doses range from 3%-10% by weight.
These additives work by thickening. At low temperatures their polymer chains are compressed and occupy a low-molecular volume. They behave like low-molecular weight molecules in an oil system, having the effect to lower viscosity. As the temperature increases, the chains expand and incorporate oil molecules to give a higher volume and higher apparent molecular weight, which has the effect of increasing the oil’s viscosity.
When high molecular weight polymers undergo shearing conditions, they decompose to low-molecular weight fragments. They can show temporary viscosity loss at moderate-shear stresses and permanent viscosity loss at high-shear stresses. When choosing VI improvers, it’s important to take shear stability into account as well as viscosity-controlling performance.
CORROSION AND RUST INHIBITORS
Corrosion inhibitors react with metal and form protective coatings on their surfaces to protect from harmful effects of water, polar impurities and oxygen. They are primarily used for copper and iron surfaces, and are used between 0.01% and 0.3% by weight in formulated oils.
Corrosion is an electrochemical reaction between the metal surface functioning as anode and the interface between the metal surface and the lubricant as the cathode. When a metal surface is in contact with oxygen and water, cathodic and anodic reactions take place, releasing metal into the oil.
Corrosion inhibitors prevent this process from taking place by chemically insulating the metallic anode from the cathode. When they are introduced into a system, they coat the metallic surfaces due to their high affinity to the metal and form metal deactivating films. These separate the metal surfaces from oxygen and water and shut off the reactions, preventing corrosion.
Many types exist: those that undergo physical adsorption (fatty amines and acid derivatives), chemical reactions (phosphorus and sulfur compounds), acid neutralization (some dispersants and detergents) and metal chelation (N-salicylidene-propylenediamine used mostly in fuels). Tolutriazoles, thiadiazoles, triazoles and mercaptobenzothiazoles are used, with varying nitrogen and sulfur materials. Some are more effective depending on the molecular weight and their ability to get close to a metal surface and form a strong film on the surface.
The main difference between rust inhibitors and corrosion inhibitors is where they function. Corrosion inhibitors work to protect copper surfaces, and rust inhibitors protect iron surfaces. They both have polar head groups that attach to the metal surfaces and hydrocarbon tails that form a film to protect metal surfaces against chemical attack. They compete with other polar additives (FM, AW, detergents and EP) for the same metal surfaces, an example of an antagonistic combination (
see Figure 10).
Figure 10. Mechanism of corrosion and rust inhibitors. (Figure courtesy of Vanderbilt Chemicals, LLC.)
MULTI-FUNCTIONAL ADDITIVES AND INTERACTIONS
Many additives perform more than one function, making the need for other types of additives much lower. Amine phosphates offer wear and corrosion protection. Molybdenum compounds give effective wear, EP and oxidation protection plus powerful friction reduction. Sulfur compounds provide wear, EP, corrosion and oxidation protection. Diphenylamine derivatives of tolutriazole provide oxidation and corrosion protection. And ZDDP is an AW additive that provides very good oxidation and corrosion protection, requiring much less corrosion inhibitors and antioxidants in a system.
When additives interact, they can either undergo synergism, where the total effect is greater than the sum of the effects independently, or antagonism, where the observed total effect is less than the sum of measuring each additive individually.
Examples of synergistic combinations involve amine phosphates and sulfurized EP, amine antioxidants and organo-molybdenum compounds, and amine and phenolic antioxidants. Antagonistic combinations occur when combining AW and corrosion inhibitors, friction modifiers and AW and dispersants and AW (
see Figure 11).
Figure 11. Example of antioxidant synergism—observed effects of alkylated diphenylamine (ADPA) and molybdate ester (mo ester). (Figure courtesy of Vanderbilt Chemicals, LLC.)
Additives exhibiting detrimental properties must be understood and controlled. A proper balance of additives in a finished lubricant formulation is critical for minimizing the harmful effects observed with many additives.
Molybdenum compounds can be corrosive to copper and lead at high levels or in the wrong application. Amine-based dispersants and antiwear additives can be incompatible with Viton® seals. Sulfurized antioxidants and EP additives contribute to corrosion under certain conditions and are incompatible with nitrile seals. Aminic antioxidants promote deposits, sludge and varnish.
Under certain conditions, ZDDP promotes deposit formation at elevated temperatures (e.g., TEOST™ 33C). It also promotes wear under certain conditions (e.g., timing chains). And the phosphorus from blow-by poisons automotive catalysts. In the early 2000s, the level of ZDDP was reduced in gasoline engine oils. But it is one of the most effective and inexpensive AW agents available, so in recent years the industry has been reluctant to drop it further, fearing that using alternatives could lead to warranty problems long term. Discussions on both sides will continue because it is critical in the automotive segment.
SELECTING ADDITIVES
Whether additives are included as part of a fully formulated additive package or by top treating existing packages, there are many factors affecting additive selection. The type of oil produced determines the types of additives used (
see Figures 12 and 13).
Figure 12. Additives used in engine oil formulations. (Figure courtesy of Vanderbilt Chemicals, LLC.)
Figure 13. Additives used in non-engine oil formulations. (Figure courtesy of Vanderbilt Chemicals, LLC.)
Geometry and metallurgy of the equipment and severity of the application’s temperature, load and exposure to moisture, atmosphere and combustion products can be a guide toward specific chemicals to solve specific problems. Drain interval and desired lubricant life matters. Lubricant going through frequent oil changes would not require as much additive as extended life or fill-for-life applications.
Some additives have a very high solubility in oil, and some of their degradation products may have low solubility, which may impact additive selection. The chemistry of the base oil, whether it is mineral or synthetic, and the type and degree of refining it undergoes also can impact selection.
Finished oils must meet specified properties and performance characteristics outlined by OEMs and trade and standards organizations. Environmental and toxicological restrictions may impact whether an additive is included in a formulation that may have a global reach. Material cost is a critical factor.
FOR MORE INFORMATION
Vanderbilt Chemicals, LLC:
www.vanderbiltchemicals.com
Debbie Sniderman is an engineer and CEO of VI Ventures, LLC, an engineering consulting company. You can reach her at info@vivllc.com.