Evonik Resource Efficiency
Delivering Resource Efficiency to the Industrial Lubricant Market
By David Gray, Evonik Oil Additives USA, Inc. | TLT CMF Plus November 2017
Every industry struggles to achieve the highest possible levels of efficiency, and the industrial sector of the lubricant industry is no exception. Industrial lubricants have, until comparatively recently, been functional, durable, and effective but were not formulated to improve system efficiency. However, in direct response to changing end-user needs, lubricants that offer improvements in efficiency without compromising the existing high levels of performance have been developed.
The drivers for this shift to efficient lubricants are many. They include economic forces, including total cost of ownership, the desire for higher productivity, and technological changes such as higher power density and smaller fluid volumes, in addition to environmental issues, social trends, and changing regulations.
In response to this clear and unmet need, Evonik’s Oil Additives Team has developed two efficient technologies: DYNAVIS®, to provide energy-efficient hydraulic fluids, and NUFLUX™ technology, formulation concepts, and services for cost-effective, high-performance industrial gear oils.
In order to support DYNAVIS® and NUFLUX™, a new approach to performance demonstrations has been developed and real world data is now available to support the positive results previously demonstrated only in the laboratory.
DYNAVIS® technology for mobile and stationary equipment
Hydraulic equipment is now working harder than ever, due to higher operating pressures, smaller and lighter equipment, and reduced sump sizes for packaging. This leads to higher fluid temperatures, further exacerbated by encapsulation for noise reduction. While most efforts are focused on the mechanical configuration of these systems, Evonik has taken the approach of improving the overall efficiency of the hydraulic fluid which simultaneously addresses many of the ‘mechanical’ concerns.
Today’s hydraulic fluids are used in both mobile and stationary equipment and until comparatively recently monograde fluids dominated.
How can properly selected hydraulic fluids help end users?
Fully developed multigrade hydraulic fluids can help end users reduce energy consumption (fuel or electric power), maintain optimum power and productivity, and enjoy the benefits of a long service life with reduced operating temperatures. In addition, if end users utilize a top tier multigrade, all this can be achieved while ensuring first-class equipment protection and excellent system durability.
High viscosity index (VI) fluids have lower viscosity at lower temperatures and require less power at start-up. Additionally, at higher temperatures, they protect against internal leakage and prevent overheating, maintaining pump efficiency over a much wider range of temperatures. In addition, the stable viscosity over a wider temperature range allows the use of the next lower ISO grade. This reduces friction while simultaneously preventing internal leakage, resulting in significant improvements in efficiency.
While any multigrade fluid widens the temperature operating window (TOW) and therefore avoids the need for seasonal oil changes, a top-tier fluid must be utilized to improve efficiency.
Total system efficiency is a function of mechanical and volumetric efficiency, as shown in Figure 1.
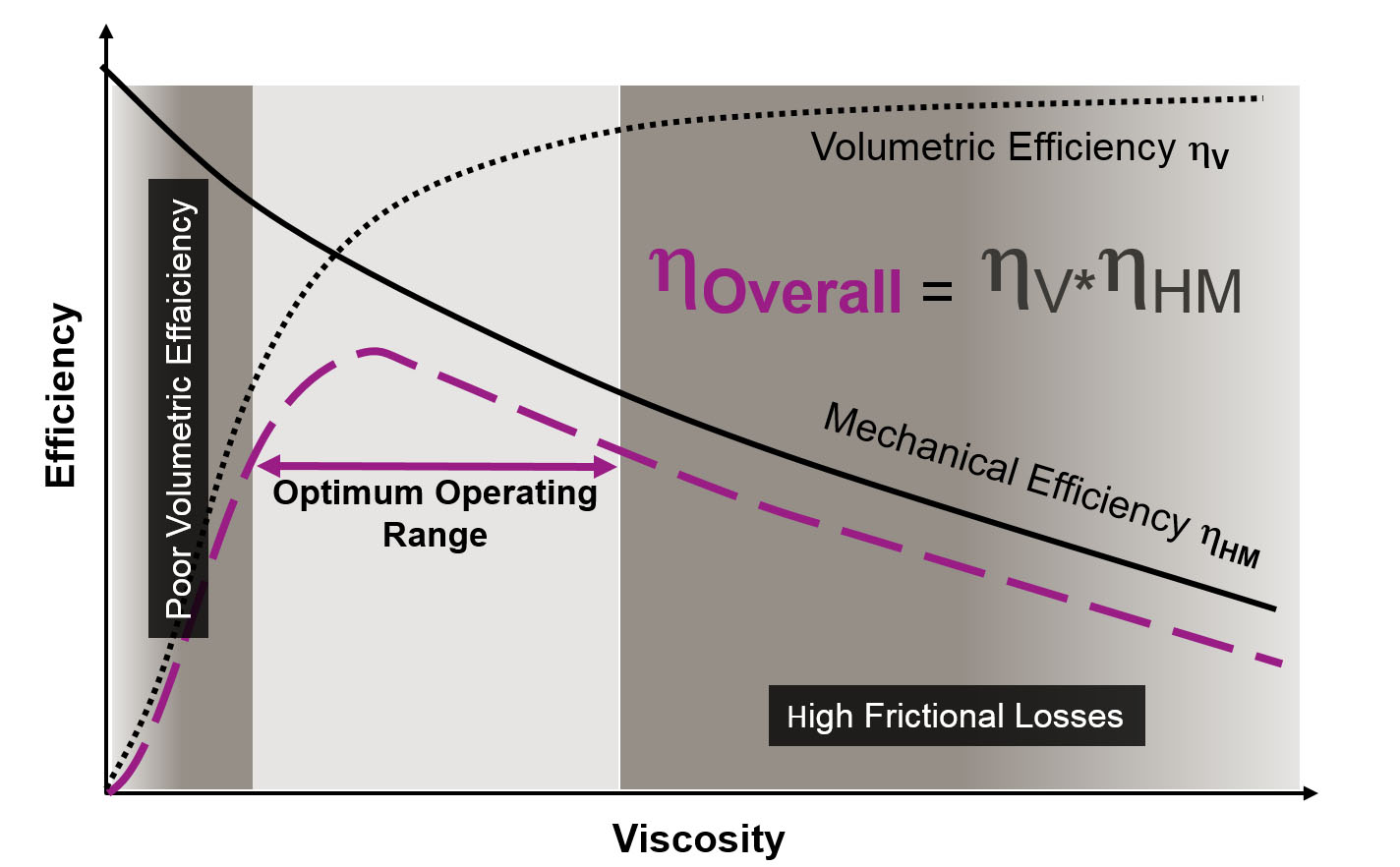
Figure 1. The influence of viscosity on the overall efficiency of a hydraulic pump.
Performance demonstrations—mobile equipment
Evonik has been developing and testing top-tier hydraulic fluids for more than 15 years. In that time, working with OEMs and end users, Evonik has painstakingly developed specialized test protocols that ensure robust and meaningful data. In developing these protocols, it was equally important to develop the user language in order to communicate the exact nature of the measured improvements in efficiency.
• Energy efficiency = work done/energy consumed
• Productivity = work done per unit time
In a wide range of mobile equipment, improvements in energy and productivity have been demonstrated. The following is a summary of efficiency and productivity gains at the 95% confidence level.
• Efficiency increase (unit weight per liter of fuel): up to 15%
• Productivity increase (unit weight per cycle): up to 15%
The efficiency increases translate into direct savings in energy consumption for the end user while contributing positively to conservation of fossil fuels and a related reduction in emissions. The increases in productivity allow the end user to get more work done in a day or to finish a job more quickly, which when considered along with the reduction in energy consumption is a very attractive combination.
Performance demonstrations, stationary equipment
DYNAVIS® fluids have been tested in a range of plastic injection molding applications.
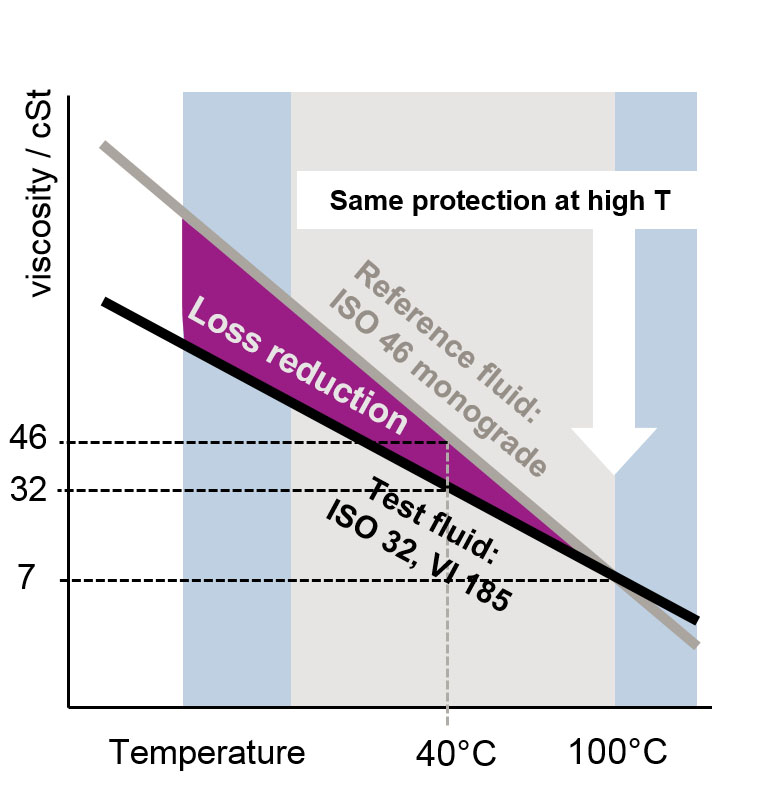
Figure 2. Efficiency benefit of a high VI fluid over a conventional monograde hydraulic fluid.
The equipment utilized included injection molding machines from Husky, Krauss Maffei, Engel, Dr. Boy, and Haitian. Energy consumption was compared with that for standard fluids, and the results were meticulously recorded and analyzed. Energy savings in the range of 4% to 11% have been recorded in a range of operations, in addition to reported improvements in clamping force.
NUFLUX™ technology for industrial gear oils
The industrial gear oil landscape
While the market for industrial gear oils is growing at a very moderate rate, demand for synthetic industrial gear oils is increasing rapidly. One of the main drivers of growth for these synthetic fluids is the need for improved in-service performance of wind turbine gear oils. This has resulted in an increased focus on research and development for all industrial gear oils. Compared with mineral-oil based fluids, synthetic fluids offer significant improvements in critical performance areas and provide the user with enhanced in-service reliability and extended fluid lifetimes.
Historically, synthetic gear oils have been formulated using polyalphaolefins (PAOs) and, in some application-specific cases, polyalkylene glycols (PAGs). A novel synthetic base oil has been developed and utilized to formulate industrial gear oils. These industrial gears oils have been compared with current ‘conventional’ synthetic gear oils and mineral gear oils.
The gear oils formulated with the novel synthetic base oil have been extensively bench tested; the results of the performance comparisons made have been summarized in an earlier paper. In addition, industrial gear oils formulated with the novel synthetic base oils have been tested in service in wind turbine gearboxes and other industrial applications.
Gear oils formulated using the novel synthetic base oil and conventional synthetic base oils have demonstrated significant performance advantages over those formulated with mineral oils. In addition, the novel chemistry of the synthetic base oil has been shown in an in-service evaluation to reduce lubricant operating temperature and measurably improve gearbox efficiency.
A new class of novel synthetic base oils
A new class of novel synthetic and highly viscous base oils has been developed. They can be used to formulate a wide variety of lubricants but due to their high viscosity they are particularly suited to synthetic industrial gear oil applications.
In addition to a high viscosity index, they offer excellent low temperature performance and are good solvents, eliminating the need for compatibilizing additives in lubricant formulations. Additionally, lubricants formulated with the novel synthetic base fluid have been shown to improve fluid films, providing improved bearing and gear protection. When used in combination with hydroprocessed Group III base oils, extremely cost effective synthetic industrial gear oils can readily be formulated.
The combination of high quality Group III base oils with the novel synthetic base oil has been demonstrated to show many of the advantages of the PAO-based fluids and to address some of the potential disadantages.
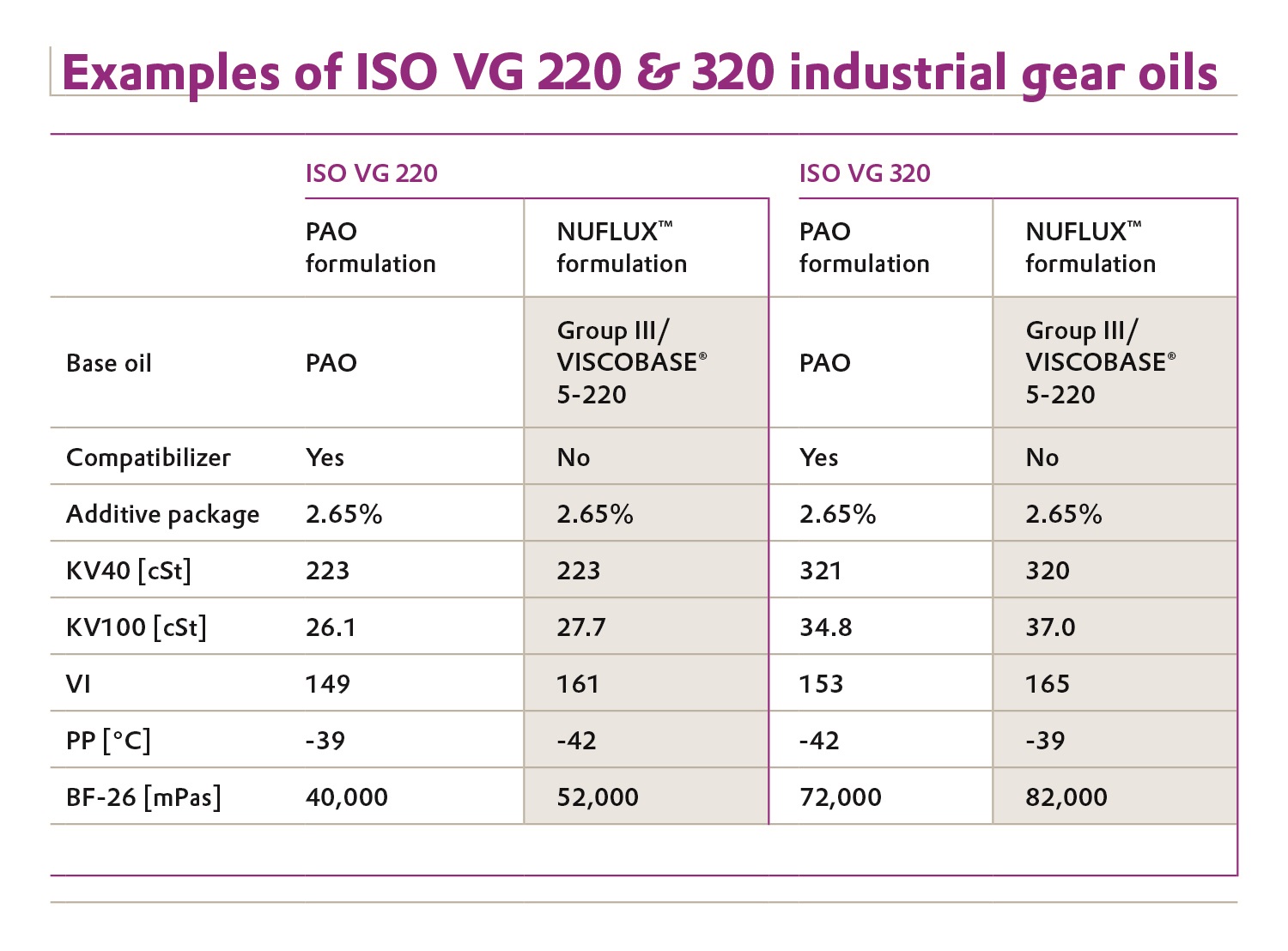
Figure 3. Examples of ISO VG 220 and 320 industrial gear oil formulations.
In the above example, two synthetic industrial gear oils have been formulated to meet ISO viscosity grade 220 and ISO viscosity grade 320. These ISO viscosity grades are typical of those used in industrial gear boxes.
While the physical properties of the two fluids are very similar, there are significant differences in their compostions. The novel synthetic formulation does not use PAO and does not require the use of an ester for compatibility with the performance additives.
Performance
Industrial gear oils formulated with NUFLUX™ technology have been tested and certified to meet DIN 51517-3, ANSI/AGMA 9005-F-16, ISO 1292501, and AGMA 6006-A03. In addition, they have received approvals from OEMs such as Siemens Flender, Hansen, and FAG Schaeffler. A field trial approval for wind turbine gear oils has also been granted by Winergy and Moventas. NUFLUX™ is currently being used in wind turbines from Siemens and GE for up to 2.0 MW in Europe and North America, with more than 3 years of uninterrupted service.
Industrial gear oil formulations containing NUFLUX™ technology have been extensively bench tested and evaluated for their performance in relation to mineral and traditional synthetic industrial gear oils.
In respect of wear, micropitting, and efficiency, the NUFLUX™ industrial gear oil performed at an equivalent level to a PAO-based gear oil and exceeded the performance of mineral gear oils in all cases. In respect of gearbox efficiency, the NUFLUX™ fomulation showed a marked perfomance advantage over the mineral gear oils and performed at the same level as the PAO-based gear oils.
Conclusions
Evonik’s new technology offers users of industrial lubricants alternative formulation approaches delivering cost effective improvements in efficiency and productivity. Through the development of robust protocols, statistically significant data has been generated that testifies to the benefits of these efficient lubricants in real-world applications.
In addition, DYNAVIS® and NUFLUX™ technologies offer novel chemistry, formulation concepts, and services that allow Evonik to fulfill its commitment to deliver resource efficiency to the industrial lubricants market.