Afton Chemical Corporation
The Importance of Lubrication in Sheet Metal Selection for Automotive Body Construction
Introduction by Bill Harwood, Marketing Manager-Metalworking, Afton Chemical Corporation www.aftonchemical.com | TLT CMF Plus November 2017
Article by Daniel J. Schaeffler, Ph.D., President, Engineering Quality Solutions, Inc., www.EQSgroup.com
The Drive to Lightweight Materials
Introduction
Automakers today are met with a unique manufacturing challenge: balancing efficiency with safety.
While vehicle manufacturers have embraced lightweighting, or using lighter metals to help produce lighter vehicles that meet government efficiency standards, they most also work to use material that is robust enough to provide crash and safety regulations.
In this article, Daniel J. Schaeffler, Ph.D., President, Engineering Quality Solutions, Inc., discusses how the right lubrication can help automakers achieve a smooth transition to lightweight materials without sacrificing safety and performance.
For more information about how Afton additives can help achieve the ideal lubrication, contact your Afton representative at www.aftonchemical.com/contact.
Magnitude of the Challenge
Just under 18 million cars and light trucks were sold in the United States in 2016 – representing 20% of the global total. In each of these vehicles, there are about 250 stamped parts in the body-in-white (BIW). This doesn’t include the additional 350 stamped parts found in the powertrain, instrument panel, and interior components like seats. Sales of most vehicle models are between 100,000 and 750,000 units per year – meaning that hundreds of thousands of each of the 600 stampings must be produced over the course of a year, with each being dimensionally identical and split-free. This requires an optimal combination of sheet metal, part design, and stamping process design.
Manufacturers target using as few parts as possible to create the vehicle. Any additional parts take more resources to design, fabricate, and join, and contribute to unnecessary additional weight. Consequently, this means having the goal of forming fewer shapes of greater complexity (larger, deeper parts) rather than more stampings of simpler shapes. The simpler the shape, the easier it is for a conventional sheet metal grade to successfully form that shape. Conversely, with complex shapes, there is an increased risk of cracking.
Balancing Safety & Efficiency
Every vehicle sold in the United States needs to meet numerous crash regulations–front end, rollover, and side impact, to name just a few. The easiest way to satisfy these requirements is to use thick and strong metal in the body construction. Unfortunately, thicker metals are the enemy of the lightweighting that is necessary to meet the fuel economy and emission targets mandated by the government. The challenge for automakers is to use the material that offers the best balance of weight, strength, rigidity, and cost for every part of the vehicle.
Conflicting constraints from increasing vehicle safety requirements and fuel economy targets are leading to an increased use of advanced steel and aluminum alloys. A study released in 2014 (Reference 1) projects that by 2025, 40% of all body and closure panels will be made from advanced high strength sheet steel alloys (AHSS) and 16% will be made from sheet aluminum alloys. Based on 250 stamped parts in a BIW and a sales volume of 17.5 million light vehicles, by 2025 it is forecast that 1.75 billion stampings will be made from AHSS and another 700 million aluminum alloy stampings.
Compared with the conventional grades commonly used in high volume automotive body construction, however, these products are more challenging to form into the complex shapes needed to meet the lightweight high strength requirements. The steel and aluminum producers are creating new alloys that are lighter, stronger, and more formable, but these advances are not enough. Not only is proper lubrication crucial as more parts transition to these challenging sheet metal grades, new additives may also be necessary to ensure optimal friction behavior under the forming conditions encountered.
Stiffness, Formability, and Lubrication
An important factor in the choice of sheet metal is its contribution to vehicle weight. With aluminum alloys having one-third the density of steel, these grades are being considered for an increasing number of applications in which lightweighting is critical. Even some of the advanced high-strength steels have a significant portion of aluminum, silicon, and manganese in their composition, which lowers their density compared with conventional steels.
Elastic modulus – also known as Young’s modulus – is a measure of a material’s inherent stiffness. Although aluminum alloys are less dense than steel, they have one-third the modulus and therefore one-third the stiffness. This means that when subject to the same loading conditions and part design, aluminum will deflect 3 times as much as steel. To counteract the lower inherent stiffness of aluminum alloys, it is necessary to increase the rigidity of the formed part. This is usually done in a combination of two ways; first, the aluminum part will be thicker than the comparable steel part, negating a portion of the weight savings. Second, additional shape is added to the part with embossments or other contours (Figure 1).
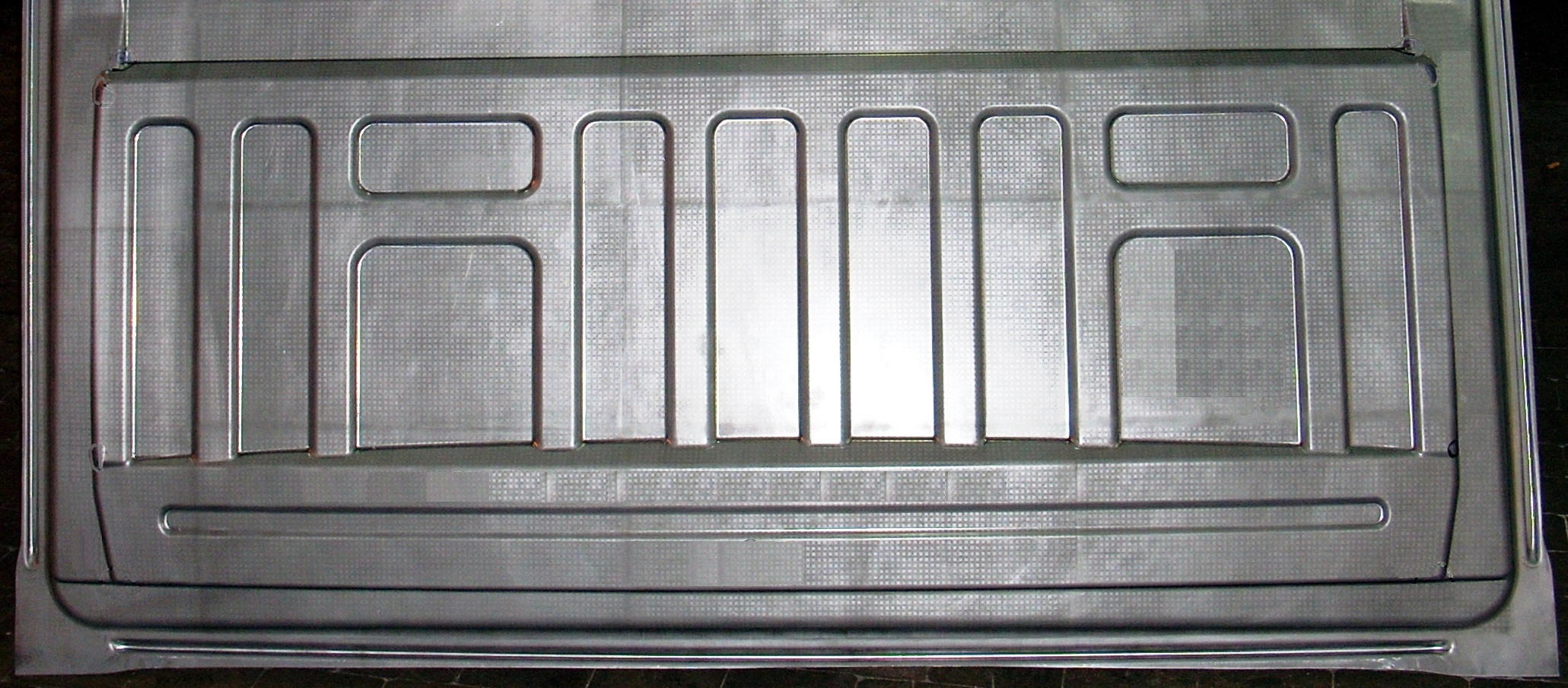
Figure 1. Truck Bed Cab Back With Embossments Added for Rigidity.
The Importance of Lubrication
Compared with the mild steels of the past, aluminum alloys and advanced high strength steels are more difficult to form into complex stampings targeted by vehicle manufacturers. These grades usually require higher press forces, which will increase the contact temperature between the tool and the sheet metal (Figure 2). These higher temperatures can lead to breakdown or burning of the metalforming lubricants commonly used, leading to insufficient metal flow and premature tooling wear.
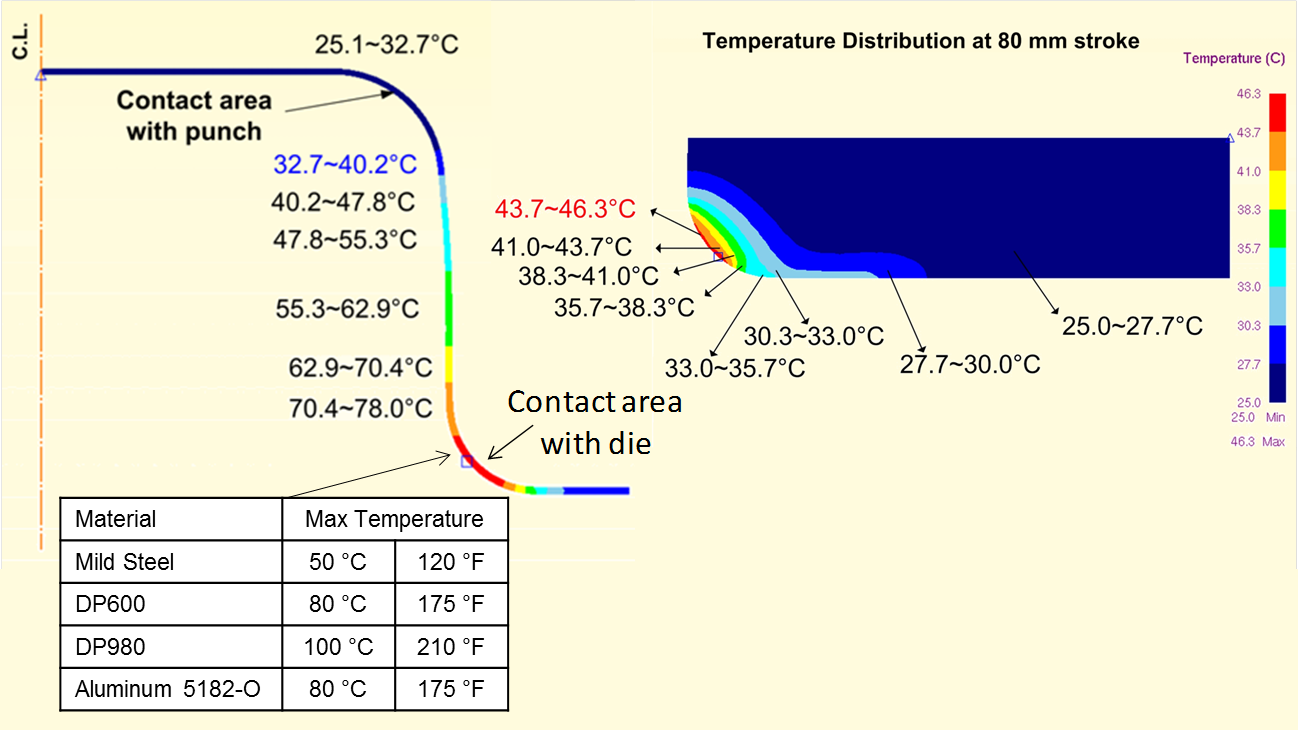
Figure 2. Maximum Contact Temperature Between Tooling and Various Sheet Metals.
(Source: A. Fallahiarezoodar and T. Altan, Center for Precision Forming, Ohio State University, used with permission)
In addition to the technical reasons discussed so far, there is another big driver in materials selection: the cost of the product. Sheet aluminum alloys are 3 to 4 times as expensive as most steel grades. Even though the advanced high strength steels are more expensive than conventional steels, they are still less costly per pound than aluminum alloys. Some of the extra cost with aluminum alloys is offset since fewer tons are needed, but this does not fully eliminate the cost premium over sheet steel grades.
With the cost premium to purchase these advanced sheet metals and the costly plant infrastructure changes necessary to form these grades (Ford spend $3 Billion on developing and renovating their factories to produce the aluminum-intensive F-150, Reference 2), there is ample justification to employ advanced lubricants engineered to meet the necessary characteristics required to form these new sheet metals.
Properly engineered lubricant formulations need heat resistance, lubricity, and cleanability from room temperature through 150 °C – 250 °C. They need to be compatible with joining and bonding methods, and must be removable prior to e-coat. The need for aluminum and advanced high strength steels in vehicle structures will only grow, and the lubricant characteristics must keep pace with these changes.
For more about Afton’s metalworking product offerings, go to www.aftonchemical.com.
References
(1) Click here.
(2) Click here.