Describe the major type of wear you encounter in your components and your solution.
TLT Sounding Board October 2017
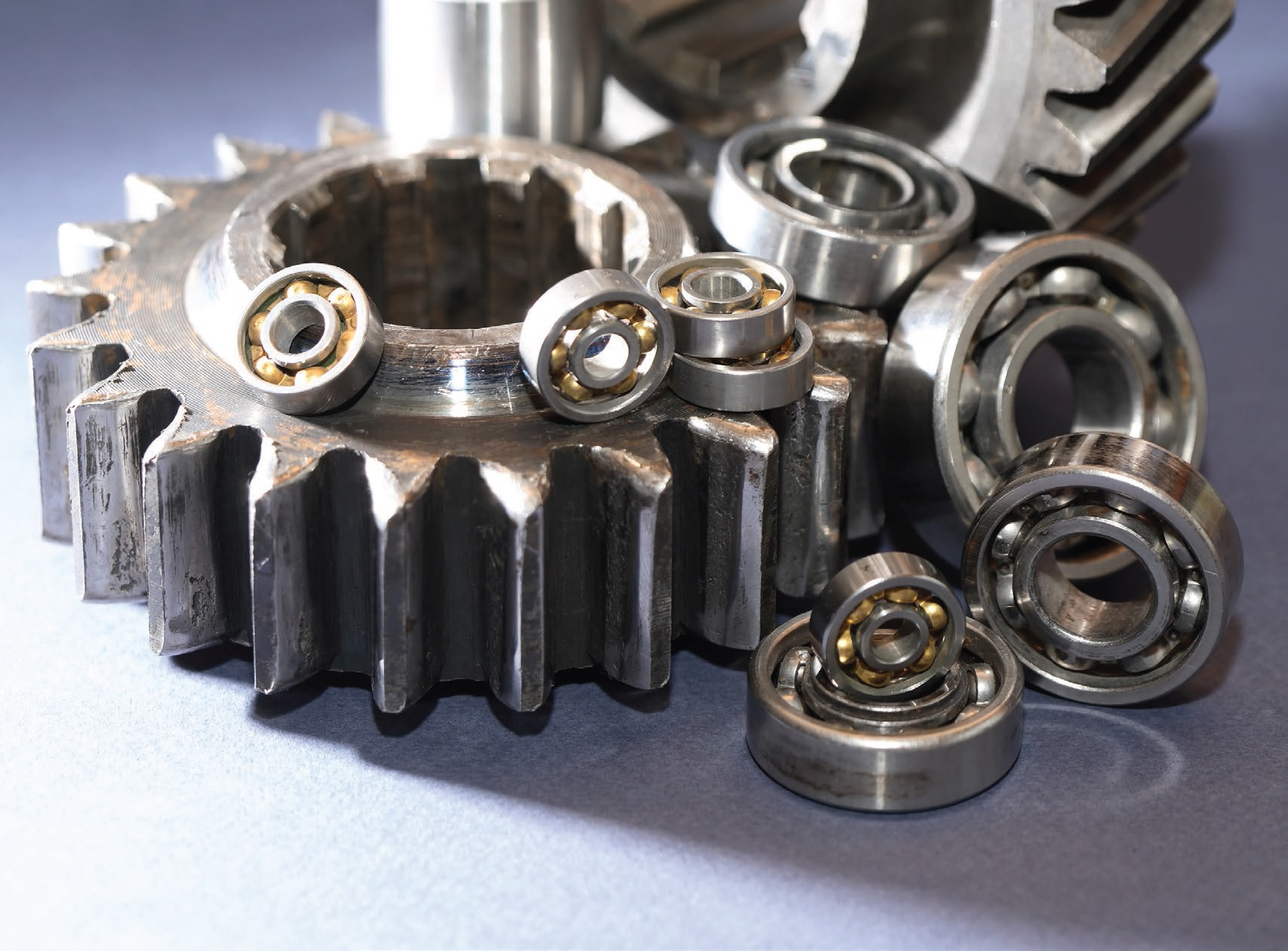
© Can Stock Photo / kvkirillov
Scuffing, pitting, abrasive wear, fatigue wear, adhesive wear, particulate ingression, fretting and false brinelling are among the most common problems lubricant professionals face every day in their jobs, according to this month’s Sounding Board survey. However, while there are many solutions to a wear issue, TLT readers agree that the first step should be a thorough failure analysis, including whether the right type of lubricant was dispensed through the proper system in the correct amounts and in the right places. The answer to the problem likely will require a customized solution that addresses several wear mechanisms and contact points simultaneously, often with the same lubricant. Among the antiwear solutions STLE members employ daily: improving or changing the lubricant, upgrading or using offline filtration, instituting better cleanliness procedures, more frequent regreasing, changing surface parameters and using a combination of antiwear and load-carrying additives.
Friction against skin. Improve surfaces.
Sliding wear at low speeds. Grease at closer intervals.
Open gear components: scuffing and pitting problems caused by mechanical misalignments and improper lubricant.
Aluminum, lead and nickel. Changed oil.
My consulting work involves a variety of forms, but abrasive wear and sliding wear are the main ones. Others include fretting and tribo-corrosion.
We research all forms of wear processes. Most tests we run are aimed at adhesive or abrasive wear. However, fatigue and erosion are important in some applications.
Abrasive wear. Now instituting fine filtration on fill lubricants and magnetic in-service filtration.
Oil film failure. Improved the lubricant.
Abrasion and fatigue. The best steps to reduce these wears is using offline filtration and making sure all the point of particles entering the oil were shut off or reduced.
Surface degradation due to hard particulate. Filtration, upgrade elements and install kidney loops if needed.
Any type of wear. Must first investigate if the correct lubrication method and proper choice of lubricant are adopted.
Valve train wear seems to be the biggest problem we see. We attempt to use computational models to predict our lubrication/hardware system as well as utilizing our expertise in running field trials in order to ensure our motor oils can lubricate effectively.
It is almost always related to particulate ingression, which we mitigate by using better-than-OEM breathers.
Abrasive wear. Use of hard protective layers, plasma nitriding, change of surface parameters.
Abrasive wear. Contamination exclusion and extraction solutions such as breathers, filtration and oil analysis.
Wear attributed to coolant contamination. Set up a used oil program in order to detect any severe problems early on.
Mostly adhesive wear. Lots of graphite.
Primarily abrasive and adhesive wear in lower-speed gears. Major steps for improvement involve improved lubricants and lubricant-application methods.
False brinelling in heavily loaded pivot points that move through less than 20 degrees and are stationary 98% of the time.
We use a number of different mixers and pump. To help control wear, we use the recommended viscosity and the best oil we can find.
Premature failure.
Adhesive wear: proper viscosity and fit for purpose additives. Abrasive wear: proper filtration and environmental controls. Corrosive wear: control water contamination and lube oxidation. Fatigue wear: better component metallurgy.
As a lubricant formulator, we see a wide variety of wear mechanisms. Our challenge is usually to reduce or control it. This requires a tailored approach for each system. We often have to address several wear mechanisms and contacts with the same lubricant.
Abrasive wear can lead to the precision failure of some high-precision rolling bearings. Improving lubrication conditions and surface topography are our main measurements to mitigate the problem.
In the speed reducer. Filtration.
Adhesive wear. Most often another lubricant is sought.
Ball bearing wear in automotive applications. Mitigate the wear with a good combination of antiwear and load-carrying additives.
Rust caused by metalworking fluid. Control water hardness with RO water.
Wear of wire drawing dies. Improve the current lubricants.
Adhesive wear. Replace with a clean and functioning lubricant.
Abrasive wear. Improve filtration techniques.
Sliding wear. Filtration.
Usually abrasive wear from environment. Try to keep it controlled with cleaning and constant re-greasing.
Abrasive wear. Auto lube.
Corrosion. Changed lubrication to a more water-resistant type that reduces washout and corrosion.
Hypoid gear tooth wear. Mitigation was done using improved finishing process for lower surface micro-finish and improved phosphate-coating processing.
Control valves and pump wear on hydraulic systems. To mitigate we improved monitor oil cleanliness with periodic sampling and good filter maintenance.
Mild abrasive wear and smearing/scuffing wear.
How do you resolve tribological failures in your components?
Change geometric design
2%
Use better materials
7%
Proper lubrication
78%
Investigate surface properties
13%
Based on responses sent to 13,000 TLT readers.
What are the major expectations you expect from a computational model in tribology? What are the advantages and disadvantages?
Predictive assessments that correlate with reality.
I do not have much confidence in computational models because they do not represent the problems encountered in actual field work.
Find satisfactory technical and economic balance. Advantages: cost savings with reliability.
Increase lifespan of machines. Disadvantage: It’s expensive.
That it be sufficiently robust to account for geometric (shapes and motions), mechanical, thermal, chemical and material condition effects on wear in the specific system of interest. Results should be predictive in a way that can be validated.
Wear processes begin at the nano or molecular level. It is becoming increasingly important to combine these local effects into what we observe as wear at the macro-scale. A good example is looking at how additives form films at the asperity level under the local conditions that occur in asperity contacts.
Simplicity that enables ease of computation by someone other than an expert. Advantage then is quick resolution of issues.
Turn theory into practice.
I wish computational model could predict exactly what is happening inside the machine, especially in detecting the progression of oxidation and varnish.
Component life. Clean versus dirty oil.
We expect to see if our contact stresses in the valve train are too high for our lubrication system. Since models are only an approximation for real-life situations, sometimes models can point you in the wrong direction. When the model agrees with what we have observed in real life, then it can be a useful tool.
Quick convergence of algorithm, simple interpretation of model parameters. Also, the possibility of including micro and nano scales, fractal description of mating surfaces, full range of friction from boundary to liquid.
Reduction in the number of plant trials required to identify a functioning industrial lubricant!
Show the predicted wear in tolerance loss over time and the effects of increased actuation stress and lubrication.
Ability to measure and monitor wear over a large distribution of components to predict the complex machine reliability.
Computer models can help us lubricant formulators understand the tribological conditions in a contact. However, most models cannot account for lubricant formulation with the degree of detail we need for formulation development.
Our main concern is how to predict the wear coefficient by suitable wear model. We hope to know the relationship between the wear coefficient and the lubrication condition.
Wear simulating in real time.
I have no expectations for wear modeling for practical applications. On a small theoretical scale, I expect that wear volumes and friction losses can be computed. In the long run these calculations will be faster and much cheaper than lab experiments.
How good the model is at predicting wear. It may be a decent model, but it will not take all the real-life aspects of the application into consideration.
Predict behavior instead of describing reality.
At the shop floor level, computational wear models are of little use. We are charged with ensuring asset availability.
With today’s software, simulations are proving to be nearly identical to real-world applications. So really no disadvantages, except the cost of the software and hardware.
Works only when mapping is correct.
Understanding how this translates into improved products on the shop floor.
I am not familiar with this but would expect it to have the typical problems of inaccuracy if initial conditions and all parameters are not carefully understood.
Long-term cost savings as well as information to set up a world-class predictive maintenance schedule.
We are not using any computational methods for predicting tribology, so no expectations at this time.
Major advantage would be to use the results for predictive maintenance scheduling rather than being reactive after a failure occurs.
Prediction of correct wear mode for a situation. Directional accuracy in terms of extent of wear.
Editor’s Note: Sounding Board is based on an email survey of 13,000 TLT readers. Views expressed are those of the respondents and do not reflect the opinions of the Society of Tribologists and Lubrication Engineers. STLE does not vouch for the technical accuracy of opinions expressed in Sounding Board, nor does inclusion of a comment represent an endorsement of the technology by STLE.