20 Minutes With Robin McNabb
Rachel Fowler, Managing Editor | TLT 20 Minutes July 2017
This data analysis manager for POLARIS Laboratories, LCC, discusses how condition monitoring and oil analysis testing help save more equipment.
ROBIN McNABB - The Quick File
Robin McNabb is the data analysis manager at POLARIS Laboratories, LLC. She leads a team of 10 data analysts that provide maintenance recommendations and technical customer support. Joining the company in 2005 as a laboratory technician before moving to an analyst role, she understands every facet of the business and can provide detailed insight on testing oil, coolant and diesel fuel.
Robin received her bachelor’s of science degree in biology from Indiana University and holds both the Certified Oil Monitoring Analyst I™ (OMA I) and Certified Lubrication Specialist™ (CLS) certifications through STLE. She is an active member of STLE and serves on the OMA Certification Committee for which she was committee chair in 2015-2016.
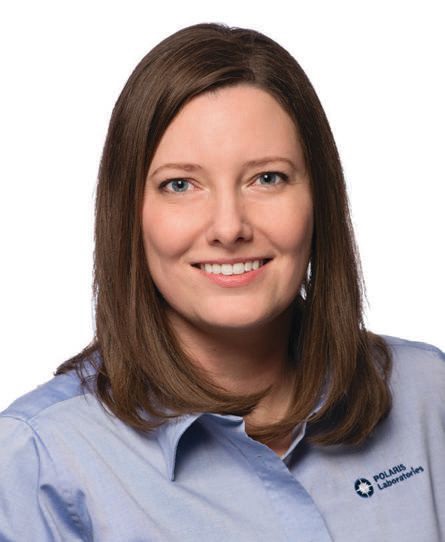
Robin McNabb
TLT: What are key advancements and innovations that you have seen and have been involved with in the field of condition monitoring?
McNabb: I have worked in the condition monitoring industry for a relatively brief 12 years. The advancements I’ve witnessed can be divided into two main categories—technology and end-user education.
From the technical side, each year we see more and more advancements in laboratory equipment automation. This type of innovation directly benefits oil analysis users by removing sources of human error as well as increasing result turn-around time and keeping costs low. With instrument automation, laboratory manpower can be utilized for method improvement and process efficiencies instead of only producing results.
We’re also seeing changes in the way people access their fluid analysis results. When I started in the industry, most customers were getting their results delivered by fax or mail. We’ve seen a drastic shift in those numbers with email becoming the preferred method. Now there is another change occurring. More and more people want instant results at their fingertips and the amount of people retrieving their fluid analysis results via mobile apps is dramatically rising (
see Figure 1).
Figure 1. Maintenance managers can now quickly review fluid analysis reports on mobile devices.
The third technical advancement that comes to mind is the use of inline or onsite condition monitoring such as sensor technology, field testing equipment and vibration analysis. Although some of these technologies have existed for quite some time, end-users are beginning to really realize how well these technologies pair with traditional laboratory fluid analysis. They can get an early indication that something may be going wrong and use laboratory report trending or qualitative testing, such as analytical ferrography, to help pinpoint the issue.
As I mentioned, the level of end-user education also has been a big advancement in oil analysis. By education, I don’t necessarily mean formal schooling but rather the amount of knowledge regarding condition monitoring and how it is changing the way data is used. As few as 10 years ago, many were using oil analysis solely as a way to schedule maintenance. While it is an excellent money-saving tool when used to find issues, there are more dollars to be found with the data.
Using the data to optimize and standardize equipment drain intervals is one of the best ways to utilize oil analysis to save money. Today maintenance programs regularly have more data at their fingertips to prove the return on investment of oil analysis. I’m proud to work for a company that really takes pride in saving customers money. We celebrate this daily with our Wall of Saves, which displays specific examples of how we help keep equipment operational.
TLT: If you could give one recommendation to an oil analysis user, what would it be?
McNabb: One of the biggest mistakes I see oil analysis users make is they are only testing a portion of the fluids that impact their equipment. In many cases we see that a site is sampling less than 50% of the equipment they have in their maintenance system. Companies with this low rate of sample compliance will see a great return on their investment despite their equipment being sampled every other year, at best. If the compliance rates were close to 90%-100%, imagine all of the additional savings that could be realized.
Now think about the additional problems that can be solved if engine coolants and fuels are added to the testing programs. Studies have found that roughly 60% of engine problems are directly related to the cooling system. Testing coolants can detect improper glycol dilution levels, which directly impact engine operating temperatures, metal corrosion issues and contamination that can cause system pitting and plugging. They also can help ensure the coolant has not deteriorated and is still protecting the cooling system. There are similar benefits to testing diesel fuel. Regular testing can help detect potential fuel filter plugging and contamination issues before they are a problem, diagnose low-power issues and ensure fuel meets ASTM specifications—among other things.
I believe it is extremely important to have an overall picture of the health of equipment and the fluids used in them. Expanding testing programs to include testing for the full range of the lubricants, coolants and fuels used in equipment is the best way to detect and prevent premature failures.
TLT: If you had only one test to perform for a typical in-service hydraulic system fluid, which one would it be? And if you had two tests?
McNabb: This is a challenging question because I want to say, “How could you only perform one test?” My response to this may not match popular opinion, but if I could only perform one standard analysis test on hydraulic oil, it would be water by Karl Fischer titration (
see Figure 2).
Figure 2. Samples waiting to undergo Karl Fischer testing.
Water leads to corrosive wear, which can shorten component life. More important, hydraulic fluids are designed to transmit power as well as support loads. The presence of water can hinder this capability. Depending on the size of the system and the load it is carrying, the stress that is put on the fluid can be quite severe. If you add water to the oil, then all of a sudden the oil becomes more compressible, which can allow loads to slip, endangering anyone in the vicinity.
One of the most often overlooked benefits of testing oil is the direct impact it has on safety. Unexpected downtime can lead to hurried repairs, and large maintenance activities allow more opportunities for injury. Ensuring equipment doesn’t fail at the worksite helps keep everyone in the area safe.
If I could do two tests, then I would add particle count. Based on data gathered by POLARIS Laboratories, LLC, roughly 7% of hydraulic samples tested in 2016 had elevated particle count levels. These abrasive particles can directly lead to component wear. Monitoring particle counts and water ingression in hydraulic systems would help identify many of the minor issues that escalate to failure.
Robin McNabb pictured at POLARIS Laboratories, LLC, Indianapolis laboratory.
TLT: If you are presented with consecutive samples a month or two apart, from a truck diesel engine crankcase where Fe, Cu, Al and Pb (all the major wear metals) were normal and fuel dilution was normal but viscosity at 100 C had changed from 13.8 cSt to 10.0 cSt, name at least one condition that might have reasonably occurred. Can you name two? What recommendations would you provide for either, or both, of the two possibilities you cited? Assume no other test results were flagged and that the result is not due to laboratory error.
McNabb: If seeing a data shift in only viscosity, my first thought would be the wrong grade of lubricant was installed. In this specific example, it is likely that the end-user went from using an SAE 40 fluid to an SAE 30. The question to pose to the customer was if they knowingly changed to a different viscosity grade. If they didn’t, do they have an SAE 30 onsite that may have been accidentally installed in the engine? If that is not possible, then I would recommend they test their bulk engine oil delivery to ensure that the correct product was provided. In this case I’m assuming this couldn’t be due to the driver topping off with the wrong grade because of the severity of the decrease in viscosity and the amount of time between samples.
The second most likely scenario would be an incorrect or mislabeled sample. Simply sending a new sample to confirm results would quickly identify or rule out this cause.
TLT: Comparing oil analysis, vibration, thermography and real-time data, do you see one more applicable today compared to when you first entered the field?
McNabb: Rather than one technology being more applicable today than a decade ago, we’re seeing a trend of maintenance programs utilizing a combination of condition monitoring tools. In the past, vibration analysis was probably most comfortable to maintenance personnel because it was another physical tool that gave instant results. Now top-tier maintenance programs are correlating vibration analysis with oil analysis results to better pinpoint root cause. They are using in-line sensors and thermography as early indicators a laboratory sample may need to be sent prior to the normal schedule. The four technologies mentioned all have strengths and weaknesses, and it is becoming more widely recognized that multiple tools are needed to optimally protect equipment.
TLT: What are the biggest obstacles and challenges you see in the industry that will need to be confronted in the next decade and beyond? With that, what are some of the low-hanging fruits to be aware of?
McNabb: This industry is not known for moving quickly. Some of the test methodology has been around for decades with little to no innovation. When new technology or methodology emerges, getting the acceptance of the oil analysis industry as a whole can be very challenging. I can’t tell you the number of times we’ve worked on setting up new business with a customer where they require a specific test or test method. When challenged with why they need it, the answer is either because their last lab performed the test or because their OEM requires it. They can’t tell you how they have ever used the test results or what benefit the testing provides, which means they’ve been paying for data that isn’t useful to them. As an industry, we need to be more proactive about keeping up with the test methods that will provide the most accurate and applicable results to the customer. This will help us ensure customers receive the most benefit from oil analysis.
The first low-hanging fruit is an opportunity to collaborate and share data between oil analysis laboratories and equipment OEMs. There is a constant struggle in addressing OEM published oil analysis limits versus laboratory recommendations. But when there are vast differences between the two, it is the end-user who is left with uncertainty. I would love to say the OEMs have it wrong and the oil labs have all of the answers, but the optimal limits probably lie somewhere in between. The OEMs have the most knowledge about their equipment and the laboratories have collected the most real-time data. By working together, decreased warranty costs and unplanned downtime can be achieved, benefiting everyone.
More companies are trying to find ways to easily correlate condition monitoring results. Finding new ways to provide and assess data are going to be key in the advancement of oil analysis. Maintenance personnel need to be able to look at an agglomeration of condition monitoring data and determine, at a glance, what actions are needed. Timely response is critical in this industry, and any way to optimize reporting to decrease potential ambiguity is where real value can be added. I’m looking forward to exploring how the future sample report should look and what other tools laboratories can provide to help oil analysis users better visualize their data.
You can reach Robin McNabb at rmcnabb@polarislabs.com.