Elements of a nuclear power station lubrication program
Jeanna Van Rensselar, Senior Feature Writer | TLT Webinars June 2017
By necessity and design, nothing is simple.
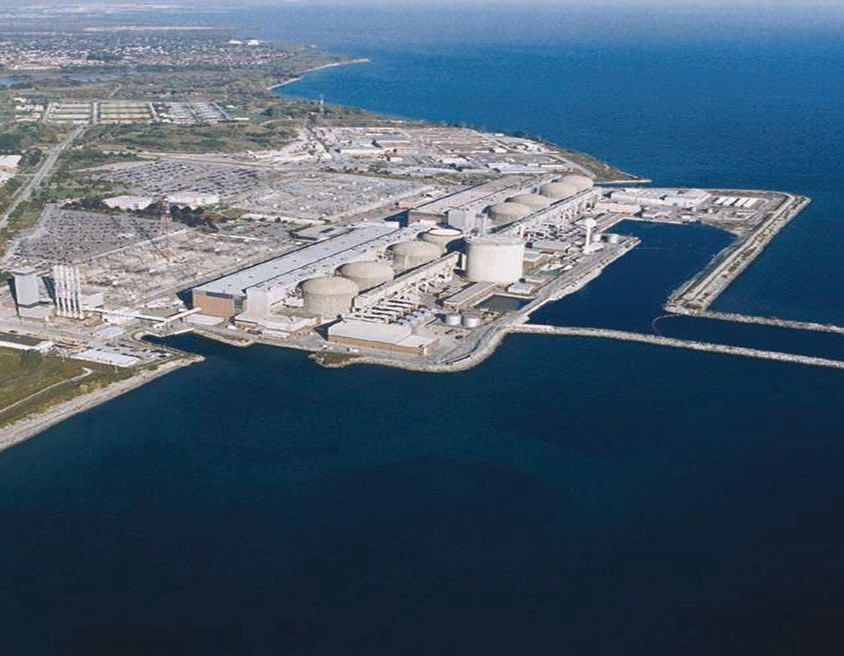
Photo courtesy of Ontario Power Generation.
KEY CONCEPTS
•
The four cornerstone principals of the nuclear power industry are safety, reliability, sustainability and affordable cost.
•
Critical elements of a nuclear power lubrication program include lubricant selection and consolidation, procurement, storage, handling, condition monitoring, disposal, audits, training and certification and research studies.
•
Nuclear stations require permission from the work coordinator before performing any work, making some simple lubrication tasks a significant, time-consuming activity.
MEET THE PRESENTER
This article is based on a Webinar originally presented by STLE Education on Mar. 29, 2016. “Lubrication Programs at Nuclear Power Generating Stations” is available at
www.stle.org: $39 to STLE members, $59 for all others.
George Staniewski received his master’s degree in mechanical engineering and a doctorate in tribology from the Technical University of Poznan, Poland. He spent 11 years working in academia, followed by 29 years in the power industry. The leading tribology expert at Ontario Power Generation (OPG), Staniewski was responsible for providing technical support to the engineering, operations and maintenance departments at all OPG nuclear stations on all aspects relating to lubrication and wear.
He also is an internationally recognized expert on phosphate ester fire-resistant fluids used in electro-hydraulic steam turbine control systems. Following retirement from OPG, he was hired by the CANDU Owners Group as a technical consultant on a project to develop a new mechanical seal for the fueling machine head ram responsible for online replacement of fuel bundles. Staniewski has published several papers and provided numerous presentations relating to different aspects of lubrication and wear. He is a professional engineer in the province of Ontario and an active member of both STLE and ASTM.
Staniewski is currently chair of ASTM Subcommittee D02.96.04 on Guidelines. As a part of this committee he was the leader of the working group to develop ASTM standards on applying FMEA for oil analysis. Currently he is preparing a next draft, which is under subcommittee ballot, on applying this method for monitoring lube oils in rolling element applications. He also is an active member of the D02.C1 Subcommittee on Turbines. For this group he is the lead person on a new standard on oil sampling for condition monitoring. The draft passed the subcommittee ballot last year and currently is under Main D02 committee ballot. You can reach Staniewski at
gstaniewski@gmail.com.
George Staniewski
THIS ARTICLE IS AN OVERVIEW OF THE LUBRICATION PROGRAM at nuclear power generating stations. The information reflects the experiences of the Webinar presenter, George Staniewski, at Canadian multiunit stations as well as observations from other nuclear stations, primarily in the U.S. Many elements also are applicable to other industries.
The nine critical elements of a lubrication program covered here include:
1.
Lubricant selection and consolidation
2.
Procurement
3.
Storage
4.
Handling
5.
Condition monitoring
6.
Disposal
7.
Audits
8.
Training and certification
9.
Research studies.
LUBRICANT SELECTION AND CONSOLIDATION
Preferably, the initial lubricant selection process should be performed during the station design phase when a decision is made as to which equipment will be purchased for a specific system. In most cases the equipment manufacturers recommend a list of approved lubricants for their equipment, or they may specify a performance standard that a lubricant must meet. However, it must be recognized that for some safety-related applications, equipment manufacturers may approve only one specific lubricant. This recommendation is usually based on extensive testing and evaluation of equipment performance in high radiation and temperature conditions.
Although it is important to follow recommendations from original equipment manufacturers, there also is a need for stations to maintain a reasonably small number of different lubricant types to simplify the procurement, storage and handling processes. This is achieved through lubricant consolidation. However, the consolidation process must always be done with caution, and it is recommended that the equipment manufacturer and lubricant supplier be involved in making the final decision.
During a station’s lifetime, changes may be initiated due to product harmonization, the continual need for lubricant improvement, legislation requirements, as well as the need for more energy efficient and environmentally friendly lubricants. Changes also may be initiated by station staff as a result of root cause investigations, which may recommend an improvement in specific lubricant properties such as foaming or air release.
At nuclear stations anybody can submit a proposal for a new lubricant. However, it is always the responsibility of the station lubrication engineer to lead the review process. This review process should evaluate the new lubricant in relation to equipment performance, compatibility, energy consumption as well as human safety and environmental impacts.
In addition, all associated issues related to the procurement, storage and handling of the new lubricant also must be reviewed before the final decision is made. All of this information must be documented and stored for future reference. For that reason, a change of lubricant type at a nuclear station is an expensive process and, therefore, made only when required.
The lubricant selection process for safety-related equipment is particularly important. In most cases, information on lubricant resistance to radiation is not available and it is the responsibility of the lubrication engineer to arrange a special test to assess the lubricant’s ability to maintain its properties in high radiation and temperature conditions.
In general, radiation accelerates oxidation of lubricants or produces similar symptoms of lubricant decomposition. It increases viscosity, acid number and sludge volume. With a mineral oil, the effects of radiation become significant only after prolonged exposure at a high radiation level.
Since lubricants are normally replaced at specific intervals, a typical in-service radiation dose is not a major concern. However, radiation becomes a concern when the lubricant receives a radiation dose that exceeds its radiation threshold during a nuclear accident.
The final assessment of lubricant ability to perform its function during a nuclear accident is done by comparing critical lubricant properties before thermal aging, after thermal aging and after the irradiation step (
see Figure 1).
Figure 1. Thermal aging process. (Photo courtesy of Ontario Power Generation and Kinectrics.)
PROCUREMENT
Lubricant procurement is a responsibility of supply chain personnel. They review the list of station lubricants, their required volumes and expected usages. Based on this information, the supply chain establishes the minimum volume of lubricants required at the station and the re-order quantity. They also might need to negotiate the acceptance criteria for each lubricant during shipment as well as lubricant cost, delivery process and required documentation.
Since safe operation is one of the cornerstone requirements, nuclear stations may prepare separate specifications for lubricants used in safety-related applications. Each specification should include a list of critical properties and their acceptable ranges, as well as the content of the Certificate of Analysis supplied with the lubricant.
Another essential requirement is the nuclear stations must always be informed in advance of any potential changes being considered to formulations of lubricants under the contract agreement. This is required to allow the stations to have adequate time to arrange thermal aging and irradiation tests of the re-formulated lubricants or to look for new ones.
Another critical responsibility of the supply chain is to review the lubricant manufacturer’s quality assurance processes and decide if additional steps are necessary to maintain consistent lubricant quality. Theoretically, the station may depend on the lubricant manufacturer’s quality assurance process and approve a new lubricant shipment only based on the Certificate of Analysis.
Lubricant storage is usually the responsibility of the station warehouse group. In general, the majority of fresh lubricants have flash points over 200 C (392 F) and therefore are not classified as flammable products. However, they are still combustible materials, and for that reason most stations store their lubricants in a separate building outside the powerhouse. The lubricant storage building must comply with national and local fire regulations, and the room must have an adequate ventilation system to prevent build-up of dangerous fumes.
Although there is no precise definition or methodology in establishing an optimum shelf life, the typical shelf life for lubricating oil and grease in original, unopened containers, stored at controlled ambient temperature at nuclear stations, typically is five years. It is required that all delivered lubricants have at least 75% of remaining shelf life when shipped to the station. In practice, this means that typically lubricants can be accepted only within the first 15 months of their manufacture date.
Although the station lubrication engineer is not directly responsible for lubricant storage, he or she must be actively involved in this process to ensure the suitability for use of the product in plant equipment.
HANDLING
Lubricant handling is primarily related to topping off oil or regreasing. This work is a shared responsibility between the maintenance and operations groups. Typically the operations group is directly involved in maintaining oil levels in large oil recirculation systems while handling of lubricants for smaller equipment is usually the responsibility of the maintenance group. However, to ensure that handling activities are done in an efficient way, the lubrication engineer must first review all critical lubricated equipment and decide if any design modification is required, such as retrofitting new oil sampling ports.
Another common design modification is the installation of quick-disconnect fittings to allow in situ filtration for maintaining the desired ISO cleanliness level in critical equipment. This is particularly necessary for large oil volume applications such as steam turbine lubricating oil systems. However, in situ filtration also is a recommended practice for smaller equipment if their design function requires continuous operation.
In the case of grease-lubricated equipment, installation of an automatic regreasing device may be considered to maintain a consistent supply of grease at recommended intervals. However, the design engineering group must review the benefit of these automatic regreasing devices against equipment safety to ensure that during nuclear or seismic accidents, safety-related equipment is able to perform its specific design functions.
One unique requirement at nuclear stations is that permission must be obtained from the work coordinator before performing any work task. This can make some simple lubrication tasks a significant, time-consuming activity. Therefore, it is required that all staff involved, even in such simple activities, are properly trained so that no error is made during job execution.
CONDITION MONITORING
The objective of a proper fluid sampling process is to obtain a representative fluid sample from critical location(s) that can provide information on both the equipment and the condition of the lubricant or hydraulic fluid.
There is great variation in the methods of sampling lubricating fluid and control fluid in the power generation industry; however, the same method or procedure should be used for a single piece of equipment. This is to provide sample consistency and improve sample repeatability, which are important for trending sample results.
In the last three decades, lubricant monitoring has been incorporated into the station’s condition-based maintenance program, which is a maintenance philosophy used by the industry to effectively manage company assets.
Stations prioritize their equipment for condition-based maintenance according to the importance of its design function. For example, all equipment required for safe shutdown of the nuclear reactor and for the continuous circulation of cooling water through nuclear fuels after reactor shutdown belongs to Criticality One group. The Criticality Two group comprises equipment responsible for production, and the Criticality Three group includes any remaining equipment with only supporting functions (
see Figure 2).
Figure 2. Criticality levels.
At all nuclear stations the full monitoring program is applied to the Criticality One group. The Criticality Two group has a reduced monitoring program, and the Criticality Three group is operated with very limited monitoring.
Performance and diagnostic indicators are selected based on failure mode and effect analysis. After identifying all potential failure modes for critical equipment, a risk probability analysis is performed to determine which of these failure modes has to be monitored. This analysis reviews all failure modes from the perspective of severity for a particular application and their frequency of occurrence.
After all failure modes, causes and effects have been identified, the next step in this methodology is assigning severity and occurrence numbers using the end-user’s own judgment. The product of the severity and occurrence numbers is called the criticality number. This number allows the user to establish a ranked hierarchy of the risk associated with failure modes for equipment (
see Figure 3).
Figure 3. Condition monitoring: failure mode and effect analysis.
The final step in this methodology is identifying all available oil test methods or instrument types that are capable of detecting the specified failure mode, cause or effect as well as the preferable sampling location.
In addition to general condemning limits, the lubrication engineer should develop equipment-specific limits based on statistical analysis of past test results. This can be done according to methodology provided in the ASTM D7720 standard. The engineer also should develop equipment-specific limits based on statistical analysis of past test results. This can be done in accordance with methodology provided in the ASTM D7720 standard.
A proper assessment of test results should not be limited to simple confirmation that a specific parameter exceeds condemning limits. It also should predict future trends and the expected time when a condemning limit may be exceeded, as well as correlate test results for different parameters.
DISPOSAL
Disposal of waste lubricants is handled by a dedicated group within the maintenance department. In general, the term waste oil is used to describe oil that has been contaminated with substances that may be hazardous. The contaminated substances might result from oil chemical degradation or by contamination processes and must properly be disposed of or recycled to avoid creating an environmental problem. Waste oils may be burned in permitted hazardous waste incinerators or sent to land disposal facilities. Large quantities of the same waste oil type collected in dedicated storage tanks can be sent for re-refining or used in less demanding applications by other industries.
Additional steps are required for radioactive waste oils to reduce their radiation level prior to disposal or burning. If station treatments do not reduce the radiation level below the acceptable limit, then the waste oils must be sent to special companies for additional, more sophisticated processing. The primary responsibility of the lubrication engineer in regard to disposal is reducing the unnecessary generation of waste oil.
AUDITS
There are two types of verification processes applied to the lubrication program: audits and self-assessments (
see Figure 4). The need for conducting audits has recently been supported by the ISO 55001 standard, which describes a requirement for conducting internal audits to determine whether an organization’s asset management system conforms to both its own requirements as well as those of international standards.
Figure 4. The two types of verification processes applied to the lubrication program are audits and self-assessments.
Since audits are a more formal review process, they are usually performed on major programs such as equipment reliability. The self-assessment process is much smaller in scope and less formal, but it focuses more on specific details.
TRAINING AND CERTIFICATION
At nuclear stations, most individuals are assigned to a generic training program describing basic design and operation requirements of major station systems. In addition, special courses are provided on radiation protection. Depending on individual responsibilities, there also are additional training programs for specific technical fields such as lubrication.
In general, lubrication is not a subject very well covered by typical programs offered by colleges and universities. Therefore the lubrication program should include implementation of a proper training and certification plan to suit the needs of different individuals involved in lubrication activities.
Additional certification is available from leading engineering organizations such as STLE and the International Council for Machinery Lubrication.
RESEARCH STUDIES
Research projects related to lubrication are always expensive, exceeding the ability of an individual station to carry them out on its own. Such projects are managed by external organizations such as the Electric Power Research Institute or in Canada by the CANDU Owners Group.
Occasionally joint projects are arranged by a group of nuclear stations if they operate the same equipment and experience similar operational problems. Lubricant manufacturers also may conduct studies to enhance the performance of their products. Input from end-users is always appreciated, and there are examples of changes to additives due to initial poor performance in a specific environmental condition. It also is important that the lubrication engineer attend conferences to learn about the latest industry research.
Since the scope of the lubrication program is so wide, and the fields of lubrication and tribology so extensive, the position of lubrication engineer offers a lifetime opportunity for learning and job satisfaction.
The bottom line is that a comprehensive and well-implemented lubrication program can significantly support the four cornerstone principles of the nuclear power generating industry: safety, reliability, sustainability and affordable cost.
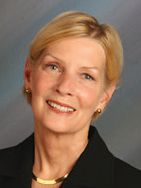
J
eanna Van Rensselar heads her own communication/public relations firm, Smart PR Communications, in Naperville, Ill. You can reach her at jeanna@smartprcommunications.com.