Describe best practices for a good gear drive cooling system.
TLT Sounding Board May 2017
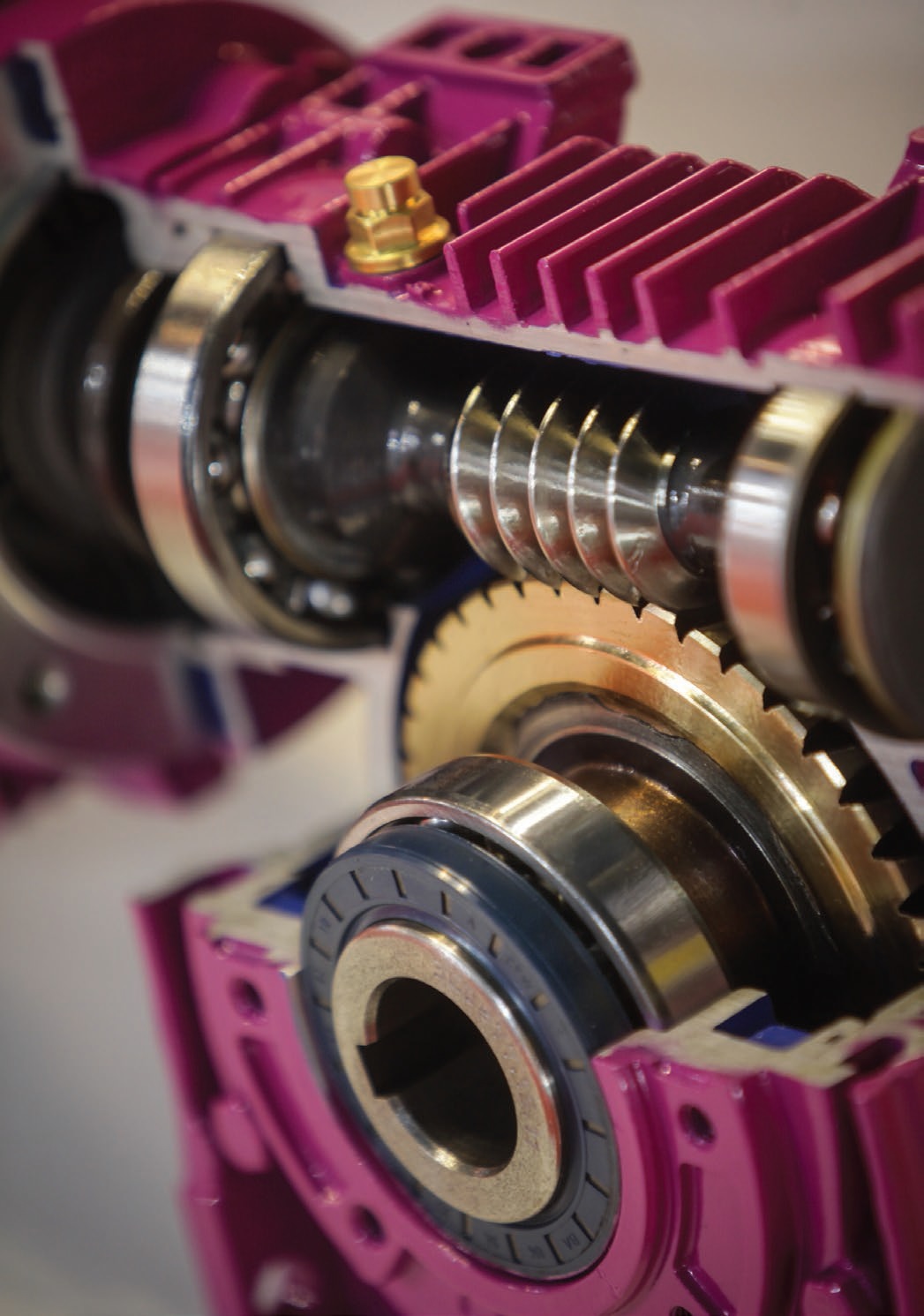
© Can Stock Photo / bizoon
Size the unit correctly. That was among the most frequently cited responses from TLT readers answering this month’s survey on elements of good gear drive cooling systems. Other readers stressed the importance of using high-quality lubes in the right amounts. Several STLE members emphasized the need to get the correct viscosity oil to the right locations at the proper temperatures and quantities while maintaining gearbox cleanliness. Good housekeeping practices must be strictly adhered to with gearboxes, and that means proper installation and good preventive maintenance programs and practices. Asked about the elements of poorly designed systems, the top two readers’ answers were too-small sumps and insufficient, if any, sample ports.
Keep in an open area if possible.
Size the unit correctly.
Unconstricted flow.
Two-stage filtration. Sufficient oil residence time. Proper filtration.
Oil isolation from cooling medium.
Ability to control across operational and seasonal considerations.
Apply the right amount and quality of lubricant. Choose a lubricant that minimizes friction (and frictional heating). Too much lubricant can cause churning and unnecessary fluid heating.
Variable self-adjusting.
Adequate flow rate to allow heat exchange. Coolers need maintenance and are best avoided if possible.
Stopping water and contamination ingression. Checking viscosity, particle counts and water content on new oils.
Depends on design and weight/space available. But variable levels of cooling maintain steady nominal oil temps and enable the longest lube life.
Getting the right viscosity oil to the right locations at the right temperature, plus cleanliness in the gearbox.
Oil with air cooling system.
Air.
Good housekeeping practices, proper installation and good preventive maintenance program and practices.
High-performance gear oil, housekeeping, overloading.
Integrated circulating system with lube spray nozzles directing fluid to entrance and exit of each gear mesh and bearings. Circulation system includes filtration to five or six micron and fluid temperature control (heating/cooling). Dry sump reducing energy loss through fluid churning. Gear housing breather with filtration and desiccant. Use of fluid with best additive system and traction coefficient for the application.
Optimum circulation with minimal air entrainment.
Water coolers, although they add time to maintenance.
Positive oil supply to the gear meshes and bearings. For splash lube, oil catchers and deflectors so the oil gets where it’s needed. For circulating oil, directed nozzles and tubes. Aim high on available sump oil volume—more is better. Allow means to easily filter and monitor the lube system. Use a lube monitoring system.
Good design, good lubricating system maintenance, excellent record-keeping and ongoing preventive maintenance of equipment.
For larger gearboxes, oil circulation with external cooling (water or air exchanger). For smaller gearboxes, fins for heat dissipation.
Allow for the worst case scenario, then add a margin.
External air-finned cooler driven off the main drive motor.
One that does not allow water/moisture into the system.
Being able to add circulation and cooling systems after the gear drive is constructed.
Radiators are always necessary. If needed, use an additional circuit with forced oil flow to and from the cooler.
Set it up similar to the way you would set up a good hydraulic system.
Periodic cleaning and sampling are the best practices to get a good feel for how the gearbox is doing.
Lambda ratios sometimes are insufficient. Surface bearing curves should be developed as a lubricant efficiency indicator.
Before replacing the drive, treat the bearings with oil that has a detergent to flush the water.
Oil mist systems.
Enough cooling capacity for the specific application.
In-line temp monitors on the downstream side of the cooler would help customers be proactive in the event of a pending cooling system failure.
Adequate heat transfer.
Spray lubrication in critical areas.
Oil coolers and heat transfer.
Ease of access. Ease of maintenance.
Is it more cost effective to manage gear lube temperature or gear lube quality?
Gear lube temperature
38%
Gear lube quality
62%
Based on responses sent to 13,000 TLT readers.
What gear drive cooling system do you use?
Grease
6%
Internal slingers and catchers
20%
Circulating oil
62%
Oil mist
9%
Air-oil
3%
Based on responses sent to 13,000 TLT readers.
What are the shortfalls that gear drive designers make when it comes to lubrication systems?
Sumps are too small.
Accessibility.
Too little oil, not enough residence time, filtration too fine, heating the oil too much or chilling the oil too much.
No easy sampling ports.
Ignore bearings in favor of the gearing.
Getting the right amount of lubricant in the right place.
Efficient distribution at low temperature for system located outside.
No sample ports.
Providing adequate fill, drain and level check access.
The right oil viscosity, the right quantities of oil to bearings and gear meshes, proper oil filtration.
Low-quality gear oils and overall low level of customer knowledge about maintenance practices.
Current lubrication grades are not efficient. The heavy grades create a lot of drag coefficient.
Friction.
Insufficient lube reservoir.
Reservoir size is too small. Not providing for optimum bearing lubrication.
Circulation.
Oil bath systems without proper cooling systems.
The oil volume is too small for adequate cooling.
When they are an afterthought for the application.
They have only the gear drive equipment in mind when designing system and pay minimal attention to the lubricant and the lubricating equipment.
Depending only on splash lubrication in gearboxes that are in intermittent service. The gears need to be coated with oil before they start turning.
Having to make it cheap rather than cost effective for a long life.
Internal lube systems take suction from the bottom of the gearbox where sludge precipitates. Filtration is only for gross particles.
Lack of an easy way to fill and drain the system properly. Also, the manufacturer needs to put the min/max fluid level, running or when cold.
Not incorporating oil sampling, addition and filtration fittings into the gear housing.
Not considering the influence of rapid changes of environmental temperature for the oil viscosity and its durability.
Do not take filtration and temperature into consideration.
Filtration on gear drive lubrication circulation has been a reoccurring theme for older pieces of equipment.
The type of grease.
Using simpler more economical lubrication systems than is ideal.
Sump volume too small, and the cooling system is inadequate.
Many gear drive designers and manufacturers limit their customer options by designating a lubricant by brand and product name. This prevents competition in the service market.
Oil film strength requirements.
Not enough lubrication in critical areas.
They do not compensate for the aging process of the lubricant.
Failing to design the system so that all parts are well lubricated.
Usually not including a method to visually inspect fluid levels.
Ease in applying a system at the jobsite.
Do promises made by gear lube suppliers generally come true?
Yes
58%
No
42%
Based on responses sent to 13,000 TLT readers.
Editor’s Note: Sounding Board is based on an email survey of 13,000 TLT readers. Views expressed are those of the respondents and do not reflect the opinions of the Society of Tribologists and Lubrication Engineers. STLE does not vouch for the technical accuracy of opinions expressed in Sounding Board, nor does inclusion of a comment represent an endorsement of the technology by STLE.