Pulp Friction
Evan Zabawski | TLT From the Editor April 2017
Measuring paper-thin friction and wear.
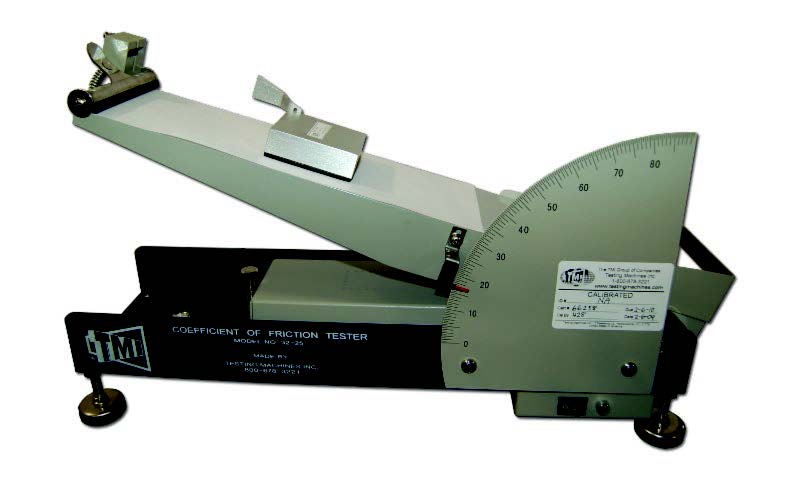
One key characteristic of sack paper is its coefficient of static friction, which is evaluated using an inclined plane method (TAPPI T815). (Photo courtesy of TMI Testing Machines, Inc.)
“WHAT DO YOU MAKE HERE?” This is a question I asked at a kraft pulp and paper mill, and the answer was that kraft paper is used to manufacture products like corrugated cardboard, butcher paper and sacks. My initial curiosity about kraft products mostly fixated on the name; I wanted to know why that particular kind of pulp and paper was called kraft, and the simple answer is it is named after the kraft process.
Papermaking basically involves pulping of plant fibers that are then spread onto a screen and dried. In the 14th Century, the fiber feedstock in Europe was primarily cotton and linen (from flax) rags, but by the early 19th Century mechanized papermaking was exhausting the supply and a timber substitute was being explored.
In the early 1840s both Canadian inventor Charles Fenerty and German inventor Friedrich Gottlob Keller independently created wood-pulped paper. Fenerty sent his first example to a Halifax, Nova Scotia, newspaper on Oct. 26, 1844; Keller sent his to the German government a couple months earlier. Fenerty and Keller had two things in common: neither knew of the other’s work and nobody liked their idea.
Fenerty never bothered trying to patent his idea, while Keller sold interest in his wood-cutting machine to Heinrich Voelter, and they jointly patented his process in 1845. Keller made such little money from his invention that when the patent renewal came due in 1852 he could not pay it, and Voelter became the sole patent holder, going on to earn significant profits without needing to pay royalties.
In 1857 American inventor Julius Roth developed a process to treat wood with sulfurous acid. Then in 1866 American chemist Benjamin Chew Tilghman also added sulfite or bisulfite of lime (calcium) to produce a lighter product that could be easily bleached. The sulfite process was first commercialized in 1874, in Sweden, using magnesium sulfite.
In 1879 German chemist Carl F. Dahl invented a new process that used a hot mixture of water, lye (sodium hydroxide) and sodium sulfide (not sulfite), known as white liquor, to break down lignin and cellulose. The pulp from Dahl’s new process yielded stronger paper, so he chose to name it after the German word for strength: kraft. About 65%-75% of the current global pulp production uses the kraft process.
One type of kraft paper is commonly referred to as sack paper, and it is a porous paper with both high elasticity and tear resistance, well-suited for producing packaging sacks. Commonly a light brown color, it can be bleached very white, allowing for colorful print.
One key characteristic of sack paper is its coefficient of static friction, which is evaluated using an inclined plane method (TAPPI T815). Higher coefficients are desired in sacks since they will resist sliding in unit loading or on packaging lines. Printer paper and currency paper, on the other hand, require a lower coefficient so that individual sheets or bills will slide over each other to prevent double feeding.
Generally the frictional characteristics of paper decrease with each successive measurement, and this has been thought to be due to progressive damage to the paper surface or the creation of surface debris. One study found that no debris could be collected; another found that a high level of friction was maintained if the direction was reversed after each slide, suggesting that orientation of structural elements plays a role.
Paper products also are evaluated using the Parker Print-Surf (PPS) method to measure surface roughness, a factor affecting the printing process. Surface integrity is evaluated using the Adams Wet Rub test or the Taber Abrader test. As you can see, tribology exists in paper mills and not just with the lubrication of paper machines. Many facets of the finished product are evaluated using tribological tests, ensuring the paper product performs predictably during handling and printing.
Evan Zabawski, CLS, is the senior technical advisor for TestOil in Calgary, Alberta, Canada. You can reach him at ezabawski@testoil.com.