10 particle analysis tests
The Editors of TLT | TLT Feature Article April 2017
Whatever the test and test frequency, the goal for end-users is cost-effective machine reliability at the lowest cost.
KEY CONCEPTS
•
While particle analysis tests have changed little over the years, end-users are becoming more aware of their significant benefits.
•
Tests range from basic article count to leading-edge SEM-EDX, which can measure and report the size, shape, quantity and composition of particulate.
•
In isolation, each test is usually not enough to provide a complete picture of what is happening inside the machinery.
ALL LUBRICANTS CONTAIN CONTAMINANTS. Even new lubricants contain micron-sized particles deposited during a less-than-pristine manufacturing process. Contaminants can enter the system through a number of processes, including normal wear, repairs and maintenance.
Most particle analysis tests only look at one or two aspects such as composition, size, color, concentration, etc. In isolation, each test is usually not enough to provide a complete picture of what is happening inside the machinery. Because of this, laboratories usually recommend performing more than one test.
There are a number of particle analysis tests available, ranging from the simple and relatively inexpensive to the sophisticated and costly. Each test has advantages in specific applications and limitations in others.
Ken Derra, R&D engineer for Briggs & Stratton Corp. in Milwaukee, Wis., and a consumer of these tests, explains, “We have used particle analysis for our assembly line oil reclamation process to periodically monitor system performance and in-product development as needed to help understand the nature of wear debris and overall oil cleanliness (
see Equipment Selection Criteria).”
EQUIPMENT SELECTION CRITERIA
According to TestOil, an oil analysis company in Strongsville, Ohio, an effective oil analysis program should focus a rigorous test slate and frequency on select pieces of equipment, rather than a minimal test slate on all pieces of equipment.
Selection is based on several key criteria:
•
Criticality. Equipment whose inoperativeness has a significant effect on the overall operation must be sampled.
•
Safety. Equipment whose unscheduled shutdown or failure could result in injury or death must be sampled.
•
Expense. Equipment with costly maintenance, parts, labor or downtime should be sampled.
•
Reliability. Equipment with unpredictable life cycles or failure modes should be sampled.
•
Environment. Equipment operating in an area with significant ambient contamination should be sampled.
•
Efficiency. Equipment operating at less than optimal efficiency may be sampled.
Whatever the test and test frequency, the goal for end-users is the highest level of machine reliability at the lowest cost.
10 TESTS
There are 10 particle analysis tests ranging from the basic, time-tested particle count to the leading-edge SEM-EDX, which can measure and report the size, shape, quantity and composition of particulate. Throughout the spectrum are excellent tests, some with specific applications that stand alone or work in tandem with other tests to accurately determine the health of machinery at a single point or across a period of time.
Here’s a look at the particle analyses Top Ten.
1. ELEMENTAL SPECTROSCOPY
Elemental spectroscopy, which measures the elemental concentration of wear metals, contaminant metals and additive metals in a lubricant, is probably the most fundamental test in the oil analysis repertoire. The test ionizes a measured and diluted sample; the light emitted during ionization is measured at calibrated wavelengths, with the intensity correlating to a concentration. As such, the test accurately measures 20-25 elemental concentrations for particles in the 0-5 micron range but does not provide information on particle shape and size. Large particle (>10 microns) elemental analysis is possible but only with time-consuming and costly sample-preparation techniques (
1). Because of its ability to determine unusual wear, contaminants and additive elements, elemental spectroscopy is an invaluable tool. But with elemental spectroscopy in particular, it is important to trend sequential samples over time.
2. OPTICAL PARTICLE COUNTING
With optical particle counting, a known volume of oil is injected through a sampling cell; on one side of the cell is a beam of laser light and on the other side is a detector. As particles pass through the cell, they block the beam and cast shadows on the detector. The drop in light intensity received by the detector is proportional to the size of particle blocking the light beam. Both the number and size of particles are measured. The particle size is estimated by spherical equivalency, meaning the area of the shadow is converted into the diameter of a circle achieving the same area.
This is a relatively quick and easy test to perform. However, the test can be skewed by water, entrained gas or even soft contaminants, such as varnish, in the fluid unless the extra step of diluting the sample is taken.
3. PORE BLOCKAGE PARTICLE COUNTING
For this test, oil is passed through a screen of known mesh size (typically 10 microns). As particles collect on the screen, the amount of flow decreases. This decrease in flow is measured and the instrument then calculates the distribution in the other predetermined size ranges by extrapolation.
While not directly measuring particles in the fluid, pore block particle counting can be performed for fluids with known water or gas entrainment, such as samples from compressors, without a need for dilution.
4. GRAVIMETRIC
For this test a known volume of sample is filtered and the collected solids are weighed to determine the particulate load in the fluid. It is often used to determine filter effectiveness. To indicate the nature and distribution of the particulate contamination, the gravimetric method should be supplemented by occasional particle counts of typical samples.
Gravimetric analysis in fluids requires less skill and equipment than microscopic particle counting. Once the specification has been established by weight, the gravimetric method provides a simple, inexpensive and highly reproducible routine control measure. This is a quick and inexpensive analysis that requires basic lab equipment, but it only provides particle load by weight.
5. FILTER PATCH TEST (FPT)/OPTICAL MICROSCOPY
For this test membranes are prepared similar to gravimetric but for the purpose of microscopic inspection. The debris is assessed and the particles graded. Observations are usually accompanied by a photo of the wear material on a test report. This method provides a means of accurate detection, counting, classification and measuring of ferrous and non-ferrous particles quickly.
For the micro-patch technique, a fluid sample is mixed with solvent and then vacuumed through a 0.8-micron filter patch. If significant wear is detected, it may require analysis by analytical ferrography. FPT is most appropriate for turbines, compressors, water glycols and natural gas engines and is typically used for ISO 16232/4406/4407 cleanliness standards.
6. FERROUS INDEX/PQ
PQ (particle quantifier) is a quick and inexpensive test that is easily incorporated into routine trending analysis. The PQ instrument is a magnetometer that measures the mass of ferrous particles and displays this as a PQ Index. Results are reported as a relative number of ferrous materials within a sample; the results can be trended. This test does not differentiate between large and small particles, but it can be used to justify analytical ferrography.
7. DR (DIRECT READ) FERROGRAPHY
During this test, the sample passes through a tube over a magnet. Particles gather at two points (five microns and greater gather at the entry point; smaller particles gather further down). The amount of light cut off by particles is used to determine density large (DL) and density small (DS) numbers. DS and DL are used to calculate wear particle count used for trending.
DR ferrography should be routine for large gearboxes and other components prone to wear that produces large quantities of ferrous particles. The test is limited to magnetic particles and may not indicate problems with non-ferrous components.
Because DR ferrography is relatively inexpensive and quick, it is a good screening tool for analytical ferrography. It also is excellent for trending ferrous wear particles (
2).
8. ANALYTICAL FERROGRAPHY
Analytical ferrography is the most powerful diagnostic tool in oil analysis (
see When is Analytical Ferrography Appropriate?). It is the only test that can justify shutting down a piece of equipment. For this test, a dilution of sample and solvent flows across a slide resting on top of a magnet, causing the particles to line up. The slide is viewed under a microscope where detected particle types are analyzed and the overall condition is determined. This produces a very detailed analysis of the particles within a sample. However, it requires highly trained technicians to analyze and report results.
WHEN IS ANALYTICAL FERROGRAPHY APPROPRIATE? (3)
Because it is time consuming and relatively expensive, analytical ferrography is not recommended for all samples. Other tools, such as DR ferrography and particle count, are good screening tools to employ before running analytical ferrography. The following will help determine when this technique is appropriate.
•
Equipment is exhibiting unusual characteristics such as overheating, high-vibration readings, unusual sounds and high-pressure readings across a filter.
•
Equipment is extremely critical, which necessitates making a moderate investment per sample to prevent unexpected equipment failures.
•
High-failure rates experienced on startup of new or repaired equipment caused by material defects, design problems or improper assembly. Analytical ferrography, along with routine oil analysis tests, should be run quickly after startup.
•
A new oil analysis program is established. Analytical ferrography should be run on critical equipment to establish baseline data.
•
Routine oil analysis indicates an unusual condition that necessitates further evaluation.
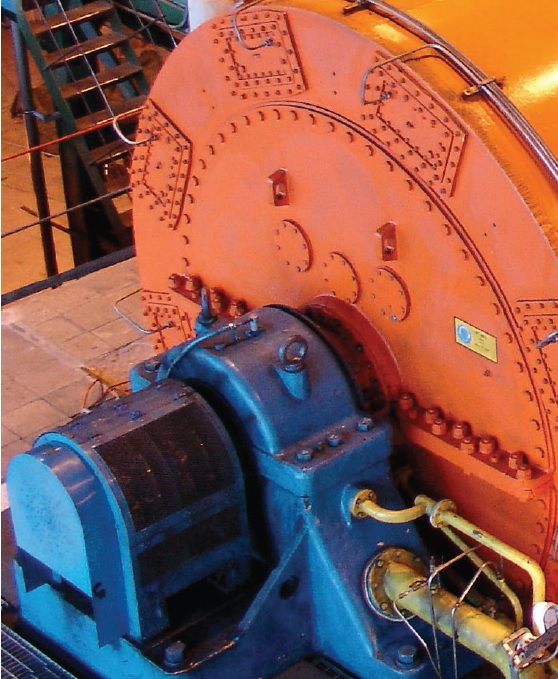
A detailed microscopic examination of a slide will determine:
•
Particle size and relative concentration
•
Metallurgy, both ferrous and non-ferrous
•
The wear mechanism indicating root cause
•
The component that is the source of wear
•
Identification of contaminants (
4).
Analytical ferrography is most useful for trending samples and preventive/predictive maintenance. Because of the time and skill required to perform the test, it is usually considered too expensive for routine oil analysis.
Bill Quesnel, president of WearCheck Canada Inc., explains, “The best application of particle analysis is where customers are using analytical ferrography on critical systems and are using the wear particle information to make informed maintenance decisions such as when to take a machine out of service for an inspection.”
Melissa James, lead imaging technician for Engineered Lubricants Co. in St. Louis, says that analytical ferrography and SEM-EDX are excellent follow-up tools.
“Most often we use advanced particle analysis as part of our used oil testing program,” James explains. “We use faster and more affordable particle-counting methods for trending contamination levels over time. When results from these show a potential issue, we follow up with analytical ferrography and/or SEM-EDX. These advanced methods help us better predict failures and in some cases prevent them. We also use these advance methods for root-cause analysis when questions or problems do arise.”
Trending analysis is credited with preventing catastrophic failure of, in many cases, very costly machines.
9. LASERNET FINES® LASER IMAGING PARTICLE ANALYSIS
Developed in 1998 by Lockheed Martin with the Naval Research Laboratory for military applications, LaserNet Fines® uses direct digital imaging. During the test, a pulsed laser diode passes through the sample with a camera recording the images where the particles are classified by shape and size. Test results classify particles larger than 20 microns into cutting wear, severe sliding wear, fatigue wear, non-metallic material, fibers and water droplets. The analysis cost effectively combines features of particle count with quantifying wear particle classification.
Its main advantage over optical particle counters is the ability to run both dark and water-contaminated samples. It can be used as a precursor to analytical ferrography, which provides more in-depth evaluation.
10. SEM-EDX (5) ANALYSIS
For this, test samples are prepared on a filter similar to optical analysis, but SEM-EDX allows for magnification up to 40,000 times, along with the elemental analysis of individual particles (
see SEM-EDX and Part Cleanliness Testing). Once loaded, analyzers move the electron beam across the field through a sequence of steps, searching for a specific particle and then moving to the next field. When the contrast level of the particle exceeds the predefined threshold background limit set for each analysis, it detects a particle. The system automatically generates reports of the analyses and a database stores all analysis results for trend monitoring.
SEM-EDX AND PART CLEANLINESS TESTING
Melissa James, lead imaging technician for Engineered Lubricants Co. in St. Louis, says she and her people are increasingly using automatic optical microscopy and SEM-EDX for parts cleanliness testing, especially for ISO 16232. As this standard is more widely implemented, more manufacturers are required by their customers to implement parts-cleanliness programs. James says that parts cleanliness is driving the SEM-EDX market.
“For example, one of our customers had a problem they believed was caused by a grease product,” she explains. “They used the grease to pack bearings, purchased from a supplier, before installing into their final product. These bearings were failing quickly once in use and, when opened, they found lots of debris.
“They were concerned the grease was not meeting the needs of this application,” James continues. “We asked for samples of bearings as our customer received them. They sent unopened examples from two different suppliers. Both of these were prepared as the filter above. The bearing from one supplier had significantly heavier debris in size classes that would certainly predict failure. At that time, ISO 16232 and the idea of standardized parts cleanliness was still something new that our customer hadn’t considered for their own business.”
This test provides high detail regarding morphology and elemental information, but it requires specialized equipment and highly trained technicians.
“The biggest advantage SEM-EDX has over analytical ferrography is the ability to get complete elemental composition for each individual particle,” James explains. “Every ferrography analyst at some point has proclaimed, ‘I wish I knew exactly what this particle is made of.’ While heat treatment of the slide and visual inspection allows for some identification of composition, the ability to tell with certainty that the abrasive wear particles are nickel alloy steel versus chromium alloy steel, or the crystals are primarily calcium, can be incredibly valuable. The fact that it does this also while measuring each particle on multiple axes giving detailed morphology also is quite amazing. SEM-EDX can accurately count and categorize all particles by customizable size, class, shape or elemental composition, which makes it unmatched for trending wear.”
She continues, “For some systems analytical ferrography and SEM-EDX will continue to only be done when unusual results from other trending methods trigger the need for further investigation. But increasingly, for more sensitive systems and those deemed necessary, these will be the tools of choice in predictive maintenance.”
There are other particle analysis tests, but these are the 10 most common (
see Integrating Particle Analysis with Other Condition Monitoring Techniques). Considerations for choosing the types and frequency of tests include a number of factors such as the expected cost/benefit, the value of the machinery, the importance of the machinery and OEM recommendations/requirements.
INTEGRATING PARTICLE ANALYSIS WITH OTHER CONDITION MONITORING TECHNIQUES (6)
For critical and expensive machinery, it makes sense to supplement particle analysis with the following complementary condition monitoring technologies.
•
Vibration analysis. Particle analysis and vibration analysis complement each other well. Vibration analysis monitors and controls balance, looseness and alignment while particle analysis monitors and controls lubricant quality and contamination.
•
Thermography. This detects issues that particle analysis can’t, such as the degree of deposit build-up in tanks and the condition of couplings, rollers and high-speed bearings.
•
Ultrasound. This compliments vibration analysis well. Trending values will point to potential bearing defects caused by contact conditions such as rubbing and friction.
While each test has value in isolation, establishing historical baselines and running consistent testing protocols will indicate changes in the status and rate of wear. This trending analysis is a key component of predictive maintenance—which is credited with preventing catastrophic failure of, in many cases, very costly machines.
Quesnel says that while the tests themselves have changed little over the years, end-users are becoming more aware of the significant benefits. “A lot of the particle analysis methods available today have been available for more than 10 years,” he says. “There has been little change to the methods available. More likely, customers have become more aware of the particle analysis testing capabilities of commercial oil laboratories and are beginning to take advantage of these useful tests. An improved direct imaging instrument could easily be a game changer for the oil analysis industry, and many of us are waiting for this improved technology to arrive.”
For end-users like Derra, the answers provided by particle analysis are leading to cleaner manufacturing fluids and better products. “Particle analysis has shown how relatively minor changes to the system provided a large difference in cleanliness of the assembly line oils,” he says. “It also has guided the system maintenance schedule needed to maintain reasonable cleanliness. As a result, our product is much improved and more consistent.”
REFERENCES
1.
While elemental analysis is generally limited to analysis of smaller micron sizes, X-ray analysis (XRF-ED) is not.
2.
From
Improving Predictive Maintenance Through Wear Debris Analysis. Available
here.
3.
Ibid.
4.
Ibid.
5.
SEM: scanning electron microscope; EDX: energy dispersive X-ray spectroscopy.
6.
Van Rensselar, J. (2014), “Leveraging the power of oil analysis,” TLT,
70 (1), pp. 36-46.