Please describe the role of low friction and wear coatings to meet the needs of current tribology applications in your area of expertise.
TLT Sounding Board March 2017
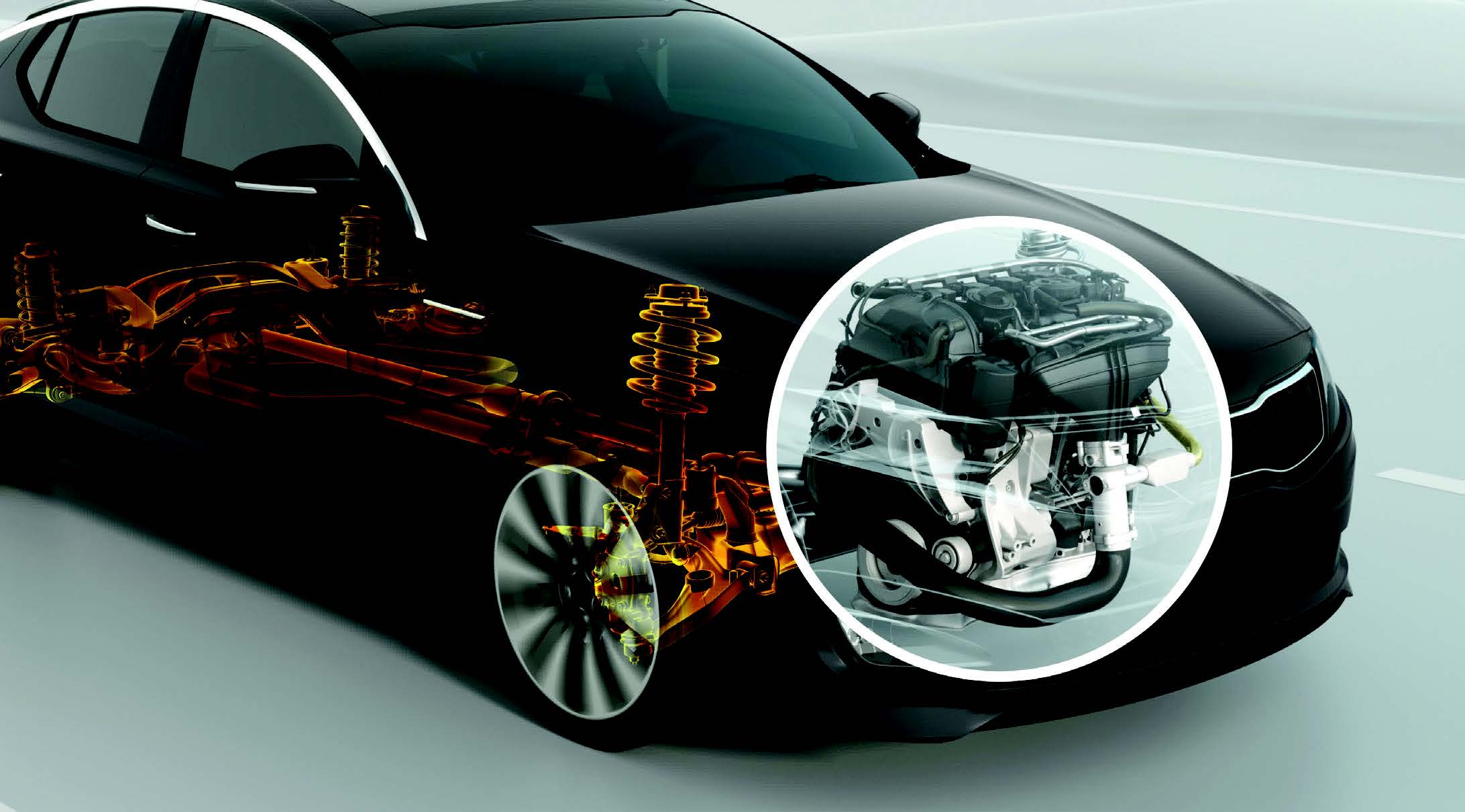
© Can Stock Photo / cgteam
Although they might cover just a sliver of lubrication applications, low friction and wear coatings play an important role in almost all industrial machinery lubrication. That was the conclusion reached by the majority of TLT readers responding to this month’s survey question. Low friction and wear coatings come into play where full film lubrication does not allow for sufficient contact/surface separation. They can be a cost-effective solution, are easily applied and help extend bearing life. These materials do have their limitations in that they are not particularly suitable for harsher applications such as agriculture or tougher jobs in the plant. Although there were some naysayers, most TLT readers agree on the effectiveness of low friction and wear coatings in the right usages. “They will gradually spread as cost comes down and application severity warrants their use,” says one reader.
To prevent skidding damage within rolling bearings.
We manufacture some resin-bonded, aerosol-applied solid lubricant coatings. Because of their ease of application and ease of re-application, they can produce excellent results. However, they will not usually last as long as a PVD, hot-cure or thermal-sprayed equivalent.
Solid lubricant coatings.
Non-structured coating by CVD reduce friction and torque values in ball valves products.
D-Gun thermal spray tungsten carbide coatings—very effective on reciprocating piston rods when finished properly.
They are very, very interesting where full film lubrication does not bring sufficient contact/surface separation. In my experience wear values may be OK, but in industrial applications friction still is at the high side.
I think a very little section of lubrication is covered by low friction and wear coatings.
Drive line lubricants for automotive gear applications and CV joints.
Most of the coatings for gears are lubricated (P, Mn based). The OEMs have migrated to shot peening and fine grinding.
Coatings in some cases are cost-effective additions to machine element performance. They have found large-scale use in engine parts and roller element bearings after decades of research.
They provide thin, hard surfaces resulting in low friction, reduced wear and longer bearing fatigue life.
Electroless deposition of coatings and thermal spray coatings.
Their role is very important as there are many applications where fluid or semi-fluid lubricants cannot be used, i.e., on-car applications, aerospace, aviation, appliances, etc.
Highly effective for reducing friction and wear.
Low friction is important in terms of energy conservation and prolonging the life of machines.
They play a very important role in almost all industrial machinery lubrication.
Key enabler for automotive solutions.
Heat-activated, antiwear coatings.
Thermal sprays.
They extend and/or maximize the usable life of mechanical components and presumed wear items.
Lip seal areas on sleeves have ceramic coatings.
Wear coatings are not used very often in the agriculture industry, but where they have been used they do not hold up well to the harsh conditions they are exposed to.
Engine tribology.
These are used primarily for wear resistance on turbine shafts and compressor rods. We typically use either chrome-carbide or tungsten-carbide.
There are no off-the-shelf high-temperature solid lubricant coatings deposited by any technique that can withstand thermal cycling to temperatures >700 C (1,292 F). More materials development work/research is needed to address this issue.
They’re not very reliable.
Give me good old petroleum.
Diamond-like carbon coatings.
They’re essential in piston rings.
They enable the use of lower-viscosity lubricants by improving component surface durability in boundary-lubricated conditions.
They help support heavy loads.
My experience is limited to TiN coatings and the like on tooling. These coatings extend tool life in the cutting of hard steels. They work.
They’re good for low-friction liquid components in engine oils to improve fuel economy and reduce emissions. Allows lower-viscosity lubricants to be used.
Ceramic metal-sprayed coatings on critical engines parts.
Mostly tool coatings.
Solid lubricants can be used in bearings used in high-temperature applications.
I typically only see open-gear lubricants, moly or silicone. Coatings have solved many friction/heat issues resulting in cost savings.
Ceramic coatings seem to work best for my needs. Teflon has a tendency to flake off and swiftly shows wear in my theater of operations.
Metalworking tools are often coated with materials such as nitrides to reduce friction and enhance tool life.
Efficiency is one of the major tasks in applied tribology engineering today. Smooth finishes and low-friction lubricants are state of the art. Further development can mainly be expected by special coatings. Similar applies to wear reduction.
Significant applications for small motors.
Sputter-deposited MoS2-based coatings continue to be the solution of choice for space applications. Highly hydrogenated DLC coatings could prove ground breaking in space and vacuum applications but lack adequate commercialization. Thermal spray and cold spray coatings are increasing in utility in the aerospace industry as well increasing terrestrial applications.
Tool coatings on higher strength steels.
UNCD coatings are the best.
What is your assessment of the effectiveness and reliability of current low friction and wear coating technologies?
Very effective
24%
Just OK. We need more research on current coatings technologies
73%
I don’t trust them. We need new coatings technologies
3%
Based on responses sent to 13,000 TLT readers.
Which solution do you prefer to solve a friction or wear problem in a design or application?
Add a low friction and wear coating
49%
Use a higher grade material for the part
25%
Redesign the part to reduce load or temperature to elevate the tribology problem
26%
Based on responses sent to 13,000 TLT readers.
Editor’s Note: Sounding Board is based on an email survey of 13,000 TLT readers. Views expressed are those of the respondents and do not reflect the opinions of the Society of Tribologists and Lubrication Engineers. STLE does not vouch for the technical accuracy of opinions expressed in Sounding Board, nor does inclusion of a comment represent an endorsement of the technology by STLE.