New grease for jet engine bearing assembly
Dr. Neil Canter, Contributing Editor | TLT Tech Beat February 2017
A roller drop test was developed to help identify a replacement for petrolatum.
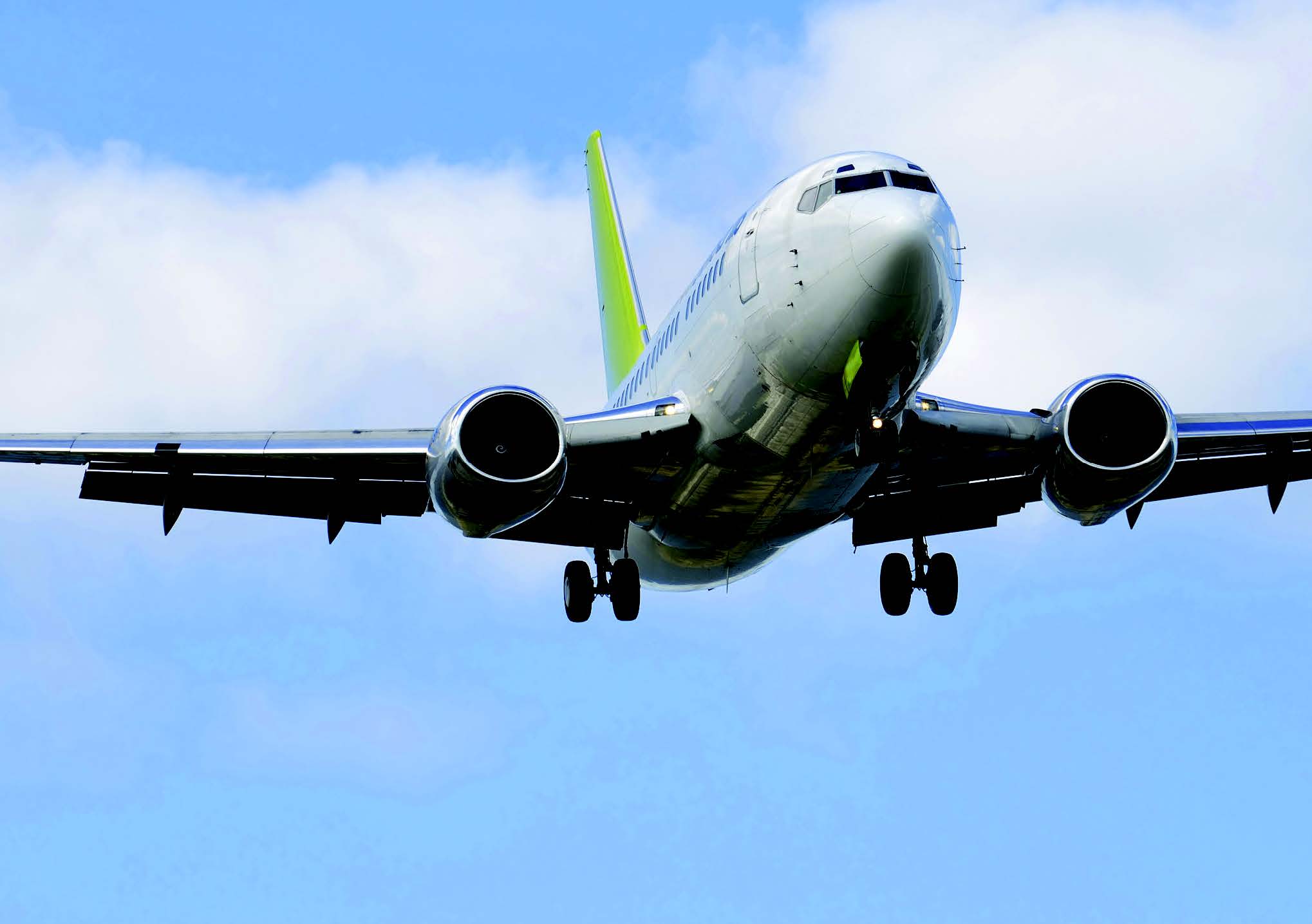
© Can Stock Photo / cfoto
KEY CONCEPTS
•
The incumbent material used in the assembly of cylindrical roller bearings used in jet engines is petrolatum.
•
A series of problems have been encountered with petrolatum, including the material’s low melting point and lack of sticking ability.
•
Several grease candidates have been evaluated as alternatives to petrolatum and have displayed superior performance in a new roller drop screening test.
•
It is hoped that in two years a new specification will be approved that recommends greases to be used in the bearing assembly process.
THE SEVERE OPERATING CONDITIONS UNDER WHICH JET ENGINES OPERATE has led to the development of high-performance lubricants needed to ensure that performance is maintained at an optimum level. Highly refined polyol esters have been used with great success in lubricating jet engines for more than 50 years.
One aspect in the manufacture of jet engines that needs upgrading is the grease used in assembly of cylindrical roller bearings. Alun Williams, manager general mechanical systems engineering for Airbus SAS in Blagnac, France, and chair for the SAE AMS-M Aircraft Greases Technical Committee, says, “Assembly aid materials may be used to prelubricate O-rings and load bearing surfaces during assembly of a turbine engine or turbine engine component that is normally oil wetted. The assembly grease is expected to remain in SAE AS5780 engine oil only for the Green Run and must have dissolved sufficiently to drain out in the oil when the oil is changed.”
In 2009 STLE Past President and Life Member Dr. Robert Bruce of Cincinnati, Ohio, who worked for GE Aviation at the time, proposed that a new grease be developed to replace the incumbent material—petrolatum that is currently used in assembly of cylindrical roller bearings used in all types of jet engines produced by every manufacturer. The bearings are generally manufactured from M-50 and M-50 NiL steel alloys.
Bruce says, “Unadditized petrolatum has historically been used, but engine manufacturers realize there are problems when the bearing is assembled. In the process, the outer race and the inner race assembled with cage and rollers and greased up with petrolatum are brought together.”
The first problem cited by Bruce is the low melting point of petrolatum, which is approximately 37 C (98.6 F). Unfortunately the outer bearing ring is heated to a temperature of 93 C (199.4 F) and heat radiating from the hot outer ring can cause the petrolatum on the cage assembly to soften. Bruce says, “Engine manufacturers tried in the past to keep the petrolatum cold by putting it in the refrigerator before use. But once the petrolatum is exposed to a temperature above its melting point, the material quickly liquefies.”
Other issues cited by Bruce include the lack of sticking ability and tackiness exhibited by petrolatum and the fact that the material is not additized with antiscuff/antiwear additives.
The most significant problem with petrolatum is this material’s inability to hold up a roller during assembly. Bruce says, “The rollers are pushed against the shaft during assembly and covered with petrolatum. Unfortunately the petrolatum sometimes does not maintain the assembly in position and allows the bottom roller to drop.”
“Tangs,” small lugs on the cage, keep the roller inside the cage, but the drop causes the roller to ride up on the outer race, leaving a mark. It is desirable to prevent this mark from occurring with a stickier grease and the addition of a wear additive to this grease.
Development of a stickier grease is very important according to Bruce, particularly for military applications, because many military engines are inspected and re-assembled at a much greater rate than civilian engines, which are often operating for seven years before disassembly.
Several grease candidates have now been identified through testing as providing much better performance than petrolatum.
ROLLER DROP TEST
Bruce developed a roller drop test to evaluate greases versus petrolatum. He says, “The test involves taking a piece of cage holding one roller. The cage contains little retention lugs that keep the roller in place. After filing off the lugs, a polytetrafluoroethylene block is placed on the base to enable the roller to stay in place.”
The next step is to apply the grease to the setup, then Bruce pulls out the polytetrafluoroethylene block and evaluates the resistance of the inner race to falling over time. Bruce says, “Two roller sizes are used in evaluating the greases. When petrolatum is applied to the larger roll as the control, the roll falls instantly.”
Evaluation of grease candidates is promising. Bruce says, “Some greases will enable the roller to stay in place for minutes, hours and in some cases for a few days.”
Bruce indicates that he has received greases from several manufacturers and reveals that several promising options have been found from some of the suppliers.
Williams says, “A “loose” set of requirements for the new grease were put together into a draft specification, with guidance from the members of the SAE AMS-M Committee including representatives from all of the major jet engine manufacturers and the U.S. military. The two most important requirements are that the grease must pass the roller drop test and be soluble, easily removed and have no negative effect on the performance of the polyol ester-based jet engine lubricant. Most of the rest of the final specification, which is still very much a work in progress, will be derived from the properties of the greases that pass the roller drop test.”
Bruce says, “Future work will involve finishing grease testing, setting limits for specifications and approving greases that pass the specification requirements for use. This process will probably be completed in two years.”
The GE Aviation contact that is responsible for working on this specification for the SAE AMS-M Aircraft Grease Technical Committee is D’Arcy Stone, PhD, who is lead engineer – materials, MPED.
Further information about the new specification can be obtained by contacting Stone at
Darcy.Stone@ge.com.
Neil Canter heads his own consulting company, Chemical Solutions, in Willow Grove, Pa. Ideas for Tech Beat items can be sent to him at neilcanter@comcast.net.