What has been your experience using silicone-based lubricants?
TLT Sounding Board February 2017
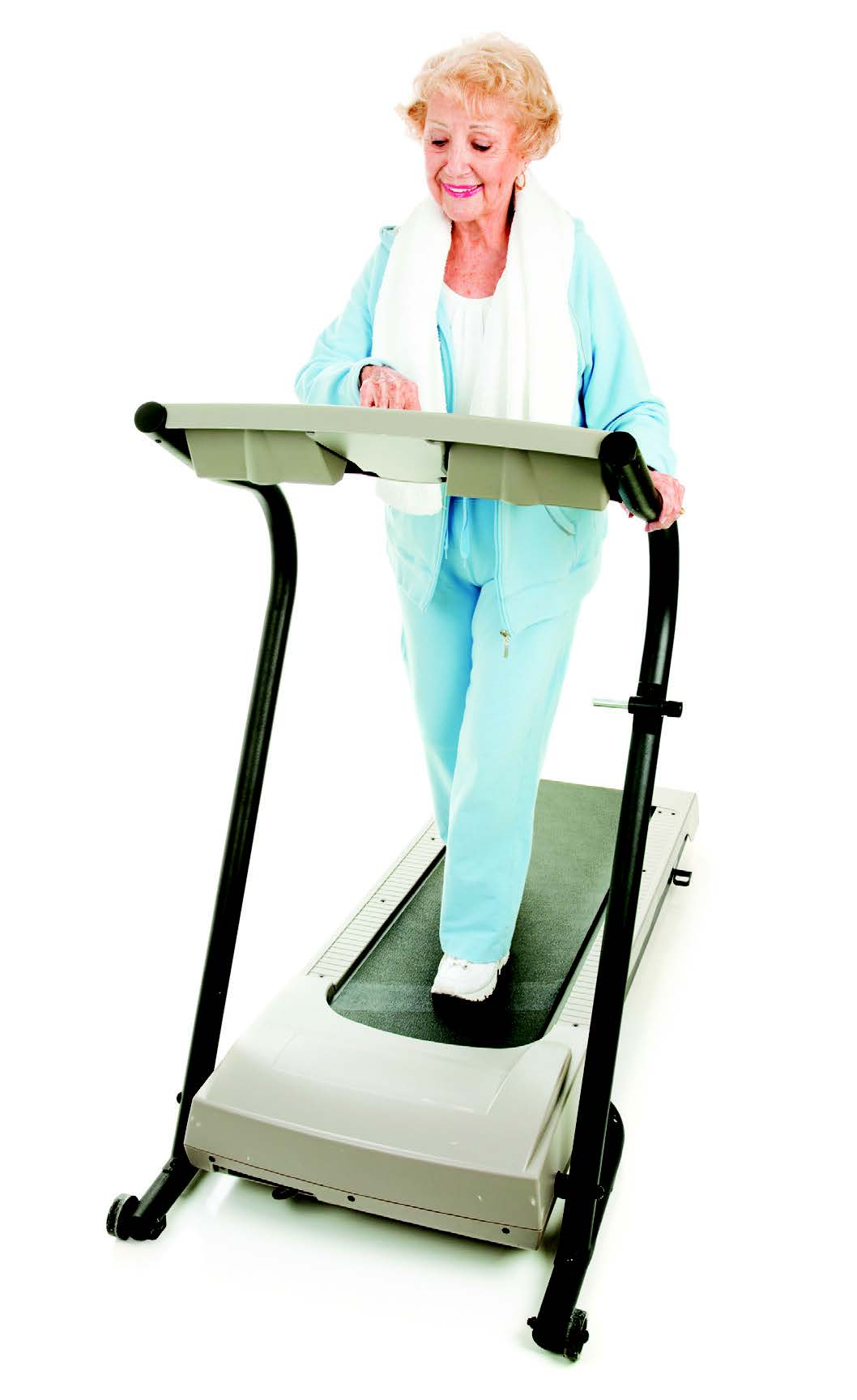
© Can Stock Photo / lisafx
While many TLT readers reported limited experience with silicones, they still noted their unique lubrication properties. Chief among these is their performance in high-temperature applications. They also are a good choice where contact pressures are low and serve as excellent release lubes. Cost and availability can be issues. “They are very good lubricants but very expensive, and there are not very many suppliers,” noted one reader. There are drawbacks to silicones, however. They are not allowed in some industries and are excluded in the EU. Due to their residue, they are not allowed in paint chambers, and many readers commented on their poor load-carrying capacity. Applications where silicones are a good choice include treadmills, chains, ovens, screw compressors, brake fluids and spray shop lubricants.
They can be useful in applications where the effective contact pressure is low.
Silicones are mainly used as antifoam and also for some synthetic oil purposes like pumps and heat-transfer fluids.
Very good as a release agent and for plastics mechanisms.
Silicones are just lubricants for light-load situations. They do not exhibit very heavy performances in medium or highly loaded contacts. Nevertheless, this represents a wide variety of systems, and they can be used for simple systems that need a few lubricants for preserving and assuming more easily their function.
Not acceptable in the EU.
Very good thermal stability, although poor load capacity. However, they’re not advisable if you’re near a painting chamber, since any residue will affect the painting process.
Unfriendly to electronics chips manufacturing (leading to poor electrical current transfers) and difficult to paint manufactured parts where silicones are used.
I established an Australian business based on dimethyl silicone oil in 1951. Even today we make more than 600 different specialty lubricants based on DiMethyl and Methyl Phenyl silicones.
We use for high-temperature rotating and sliding mechanism.
Very expensive and limited performance benefits versus carbon sources.
Silicones are extremely good high-temperature lubricants. They are especially good release lubes.
Some industries will not allow a silicone product in the plant.
It’s used as a defoamant in hydrocarbon lubes. There also are silicone compressor lubes.
They are rather effective.
Applications where chemical inertness is critical.
We use it only in greases.
Silicone grease stays long on a hot surface.
I only use silicone lubricants when carbon-based products are not practical options.
They have some very interesting applications. The most useful property is their extremely high VI, which allows use in low temperatures.
They are good for highly specialized applications: high-temperature/vacuum, very corrosive environments or wet environments where water resistance and material compatibility is an issue. Normally their cost prohibits their use in anything but very small quantities.
I have manufactured organo-functional polysiloxanes, some of which were used for niche lubricant applications.
Aerosol sprays.
Silicones as a base fluid possess some unique qualities and are chemically resistant.
Silica base thickeners are used for making greases.
They are very good lubricants but very expensive, and there are not very many suppliers.
Automotive plants do not approve of utilizing silicone-based lubricants because of paint cratering issues.
Some uses in military greases.
My experience is mostly converting silicone-based lubricants over to other synthetics due to performance issues.
WD-40 and similar aerosol sprays for home use. They last for a while but need to be re-applied roughly on a monthly basis.
In water-based metalworking fluids, most silicone applications are used as defoamers rather than lubricants. Main concerns have been interference with subsequent painting and plating operations.
Silicones have good water resistance and a higher VI in comparison to other synthetic lubricants. Silicones have a tendency to wet out surfaces and cause issues close to Class A surfaces.
They are very inert and environmentally friendly, but they have poor load-carrying capacity.
As a manufacturer of bonded solid film lubes, we only use silicones as binders for high-temp applications. We use no silicone-based lubricants.
They can cause problems with adhesion of surface treatments, etc.
Many if not all automotive OEMs ban silicones rightly or wrongly because of paint-adhesion issues. Outright silicones have always been an issue for fisheyes. Siloxanes are suspect, too.
I have only seen them used as rubber lubricant for inserting press fit diameters to reduce damage and load required to install rubber parts.
Limited to exotic applications that can absorb very high costs.
Good for certain applications but not compatible with most other lubricants.
Only use silicone spray on door sliders.
I haven’t used silicones as lubricants other than for minor miscellaneous applications. But I have seen silicone gasketing materials cause excessive foaming of conventional lubricants.
We use silicones extensively in our specialty thermoplastic compounds.
Very limited due to high cost. I understand the oxidative stability is exceptional.
Great lubricity and high VI, but seal compatibility has been the biggest issue.
© Can Stock Photo / EMarket
Please describe applications where a silicone lubricant is the recommended choice.
Release lubricants in the metal-casting industry.
Treadmills and bike chains.
High-temp applications.
Fine, dry, non-transfer areas, slides, chutes, table, etc. I have heard that silicone greases are good for high heat.
Control instrumentation.
Small delicate items.
High-temp applications: paper boiler, ovens, etc.
H1 silicone aerosol sprays are used on machine parts and equipment where there is potential exposure of the lubricated part to food.
They can be effective release agents.
Vaccum and gas pumps and heat transfer fluids.
If it’s heavy viscosity, then marine.
Plastic conveyors, PTFE bushings.
Light-loaded systems without large expectation. Preserving components. Sprays are quite useful.
Demulsifiers in traces.
Excellent for sealing and for the lubrication of plastic/plastic or plastic/metal contact. Valve sealing as well.
Fresh water tap, rubber/moving parts where food grade is essential without traces of smell!
A wide range of temperatures, including high-temperature applications (primarily for defense equipments), bio-friendly, replacing biological fluids as lubricants.
There are hundreds of such applications, but those that co-lubricate metals working in contact with plastics in contact with elastomers are critical.
Chemical involved, high-temperature applications.
High pressure, two-stage flooded rotary screw compressors.
Brake fluids and spray shop lubricants.
Laboratory glassware connections, especially when reactions being run.
I recommend silicones for applications with temperature extremes, low atmospheric pressures or when material compatibility issues must be managed.
Air compressors.
Sliding windows in automobiles.
Applications under extreme temperatures and pressures can require these types of lubricants. In addition, the stability of the Si-O bond has some unique advantages in terms of materials compatibility versus hydrocarbon or other synthetics.
NSF H-1 designated. Some O-rings and other components of regularly disassembled, cleaned and re-assembled food processing machinery. H-1 designated silicone. Some conveyor belts and minimally loaded sliding components of food processing machinery components.
Chemical resistant, vacuum greases, etc.
Hinges, bicycle chains, garage door tracks, locks.
Applications that require a damping grease such as bearings and moving assemblies for drawers in cabinets.
Cables (wire on plastic), low loads, wide temperature.
Only in solid polymer forms.
Oxygen-exposure applications.
Often used for noise (squeak) reduction.
Marine steering systems, brake systems. Some food-grade applications.
Editor’s Note: Sounding Board is based on an email survey of 13,000 TLT readers. Views expressed are those of the respondents and do not reflect the opinions of the Society of Tribologists and Lubrication Engineers. STLE does not vouch for the technical accuracy of opinions expressed in Sounding Board, nor does inclusion of a comment represent an endorsement of the technology by STLE.