20 Minutes With David B. Gray
Rachel Fowler, Associate Editor | TLT 20 Minutes January 2017
How this 29-year-industry veteran switched his focus from automotive tribology to developing industrial oils for OEMs.
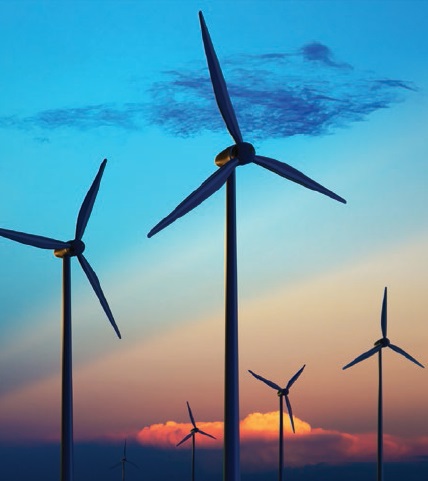
There is a marked trend to deliver energy more efficiently, and this is where well-designed lubricants can provide measurable gains.
© Can Stock Photo / JohanSwanepoel
DAVID B. GRAY - The Quick File
David B. Gray is North American (NA) original equipment manufacturers (OEM) manager for Evonik’s Oil Additives business. A 29-year veteran of the industry, Gray started his career with a focus on engine oils, working in both the UK and U.S. He began working with Evonik in 2008 as a technical service manager at Evonik’s Oil Additives global headquarters near Frankfurt, Germany. In 2010 Gray returned to the U.S. where his role evolved into his current position as the NA OEM manager. His responsibilities include working with automotive and industrial gear oil and heavy-duty diesel OEMs. More recently Gray has transitioned to working exclusively with the industrial, hydraulic and off-highway equipment OEMs in response to Evonik Oil Additives’ expanding industrial product line. He holds U.S. and EU patents for off-highway transmission lubricants and fuel-efficient engine oils.
Gray attended Portsmouth University in the UK where he graduated with an honors degree in mechanical engineering. In addition to his current responsibilities, he serves as a proud staff member of Evonik Technical University.
David B. Gray
TLT: Can you define the role of an OEM manager for industrial products?
Gray: The role is primarily one of communication. It is critically important to stay close to the original equipment manufacturer (OEM) to understand his or her current needs, future needs and, most important, unmet needs. In this way, our company’s products can be designed and developed to directly address the challenges that our partners at the oil and additive companies will be facing. Similarly we can keep the OEM updated regarding both incremental improvements in technology and exciting new products that offer tangible benefits.
A critical aspect of the OEM manager is to develop strong relationships at multiple levels and functions within the OEM’s organization. It is perhaps the nature of the market that compels OEMs to focus on factors such as logistics and back integration in making their supply decisions, sometimes to the detriment of more basic performance needs. Therefore, these strong relationships ensure that the longer term strategic needs of the OEM are identified, research is focused and performance-driven technological solutions are developed.
TLT: How have your responsibilities changed and how has that impacted you?
Gray: The majority of my 29 years in the industry has been focused on automobile applications encompassing engines, transmissions and drivelines. The industry’s focus clearly continues to be fuel efficiency in order to meet emissions targets. However, over the last few years I have transitioned in my role to one of providing exclusive support to the OEMs within the industrial gear oil market. This change has been challenging—as I have to quickly ramp up my understanding of a market that responds to a very different set of forces compared to automobiles—but, for the same reasons, the change also has been very rewarding.
Currently the main driver in this market is durability, but we are starting to see some significant interest in efficiency. This is an exciting development, as existing technology must be improved and new technology will have to be developed, which will present significant opportunities for the suppliers who are prepared to commit resources. In summary, my role evolves and grows every day as the pace of technological development increases.
TLT: What do you see as a major focus in developing next-generation wind turbine gear oils?
Gray: As I mentioned, hardware durability remains a constant focus within the industrial gear oil market. Durable service life, especially in a large gearbox such as that of a wind turbine, is critical. However, there is a marked trend to deliver energy more efficiently, and this is where well-designed lubricants can provide measurable gains. The end result is a direct cost benefit to the end-user. For example, Evonik has developed NUFLUX™ technology to facilitate this necessary improvement in efficiency in the industrial gear oil market.
TLT: How do you stay informed about the industrial gear oil industry?
Gray: It’s fortunate that the industry has some first-class trade associations such as the American Gear Manufacturers Association and the American Wind Energy Association that facilitate everything from local informal meetings to national conferences and seminars. We are members of the Gearbox Reliability Consortium (GRC) hosted by the National Renewable Energy Laboratory, which is an excellent opportunity to stay abreast of the latest hardware and tribology developments. The GRC’s recent renaming to the Driveline Reliability Consortium and inclusion of topical workshops ensures that lubricants are now front and center when considering large gearbox issues. Of course, I would be remiss not to mention STLE and the work it does to ensure the issues of the day have a venue for discussion, dismantling and developing concepts, ideas and solutions. I find the Tribology Frontiers Conference to be especially valuable.
TLT: Are there any unmet needs today?
Gray: There has been considerable focus recently on resolving the bearing failures, which can be categorized by the tribological phenomena of white etch cracking (WEC). Significant time and resources have, and continue to be, applied to solving the problem, and I am confident that the cause(s) will be understood shortly and solutions implemented. However, until an across-the-board solution is developed, these bearing failures and WEC will be regarded as an unmet need.
One possibly more challenging need is the need for more efficient delivery of energy. Evonik’s Oil Additives team is committed to developing innovative solutions and has dedicated considerable resources to improving the properties of lubricants. Our research has shown that improvements in efficiency is an area where considerable gains can be achieved without compromising durability. I think we will see a lot more focus in this area in the near future.
TLT: The market tends to be very conservative. How can a new supplier engage an OEM and supply him or her with new technology?
Gray: That is a very good observation. It is a conservative market for many reasons. For example, with the significant cost of replacing a gearbox ‘up tower,’ the OEMs and wind farm operators naturally prefer to continue using what is working for them. Experimentation can be extraordinarily expensive. In addition, some of the reluctance to try new technology may be due to the lubricant not being regarded as a design element. However, by qualifying new products in advance against key industry specifications and performing in-service trials, one can both remove the fear of the new and credibly demonstrate the benefits. While the initial efforts are time consuming and resource intensive, Evonik’s recent successes with its fuel- and energy-efficient DYNAVIS® and NUFLUX™ technologies are very promising. Moving forward, we believe these successes will enable us to work even more closely with OEMs and successfully co-develop many additional innovative new lubricants.
TLT: Why is this market so interesting to you?
Gray: I am an engineer by training and remain an engineer at heart. New technology fascinates me and I see the pace of change and innovation as incredible and inspiring. As such, being able to bring new and exciting technologies from Evonik that make a difference to the market is both challenging and highly rewarding.
TLT: I have heard this role will allow you to cross an item off your bucket list. Can you explain?
Gray: Ever since I first saw a wind turbine in the UK many years ago, I always wondered what the view from the top would be like. As part of my work with wind turbine gear oils, it is sometimes necessary to go to the top of a wind turbine to inspect the hardware. I eagerly look forward to this opportunity, and I hope that in the not too distant future I will get my wish. Although, it must be stated that extensive safety training is required in advance. Nonetheless, I am sure the view will be worth the effort. And I will let you know.
You can reach David B. Gray at david.gray@evonik.com.