Describe a grease incompatibility problem you faced and your solution.
TLT Sounding Board December 2016
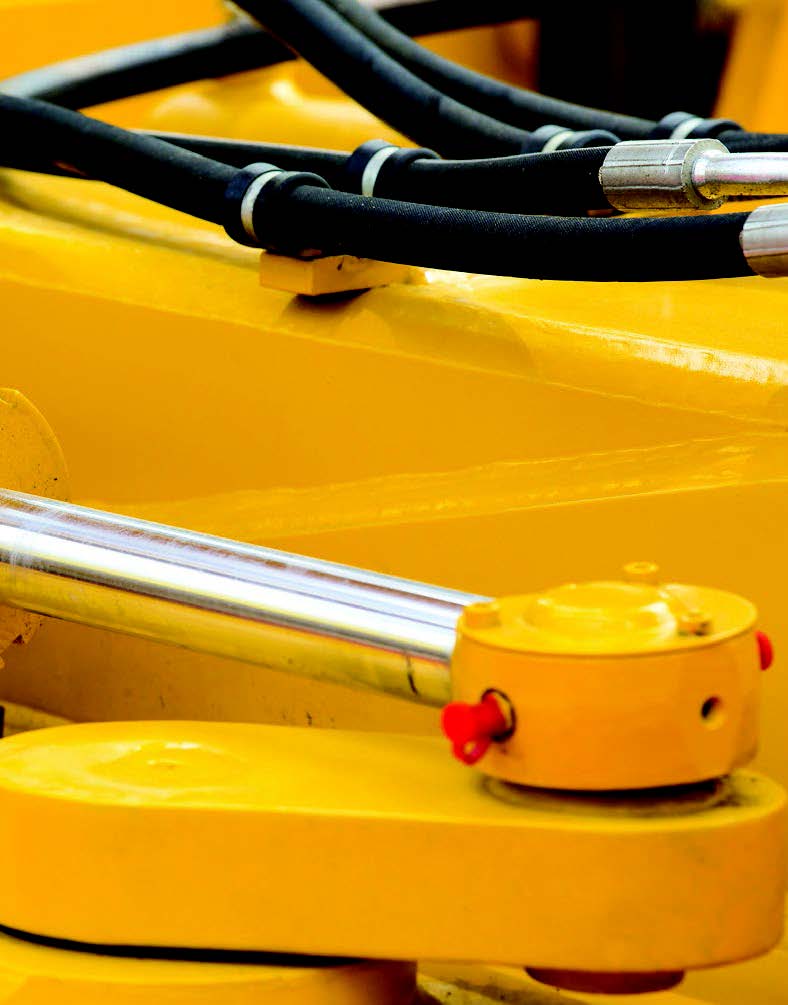
© Can Stock Photo / Lester120
Whether it was in the field or lab, TLT readers reported many issues involving grease incompatibility. The typical cause of incompatibility is mixing different greases such as aluminum complex with simple lithium, or combining greases with different thickeners. Readers noted that combining incompatible greases can occur in many stages during the transport, storage and maintenance of machinery and greases. Often it occurs when maintenance personnel are introducing new grease to what was issued by the machine OEM. The result of incompatibility issues typically is grease oozing out of the component. Instituting procedures and better training of personnel usually solves the problem. Many readers said they never change or mix greases without testing for compatibility first, while others do a complete grease purge before introducing the new product. When asked about the most significant grease technology developed in the last 20 years, the No. 1 answer cited by readers was calcium sulfonate complex grease.
Changing from lithium complex to calcium sulfonate caused significant softening, so more purging with the new grease was needed. It would have been better to have stripped down the machine and cleaned it thoroughly before re-greasing. That would have saved a lot of messing about and testing of mixtures.
Not in practice but many times in the laboratory. The solution is to purge as much of the old grease out of the application as possible.
In fact, compatibility between greases and sealing materials is one of the most important issues. A good balance of oils, additives and thickener could improve it significantly.
Clotting. Solution was to purge, flush and refill.
No, we make sure to do our homework and test prior to making switches.
Yes, thickener was a polymer base and it seemed to suffer from shear stress in a large exhaust fan spherical bearing.
Mixing aluminum complex with simple lithium. Solution: Use lithium complex greases.
Conventional polyurea grease not being compatible with lithium-thickened grease. In a food plant, where H1 lubricants were being used, bearing failures were occurring because bearings were factory packed with conventional H2 polyurea grease, which was not compatible with the aluminum complex grease that was the standard grease being used through the facility. The problem was solved by finding a shear stable H1 polyurea grease that not only solved the incompatibility problem but also increased the life of other bearings that had been being greased with aluminum complex grease.
Not really. The real problem was mixing different types of grease.
No, my biggest issues seem to be air pockets. It’s almost impossible to get all the air out of a complex continuous grease system, especially an NLGI 2 or thicker.
Yes. A client took a small gearbox in a critical area that had a lithium complex gears grease and added incompatible grease that rapidly leaked past the marginal seals. Another did a similar action on a process cooling tower reducer shortly before replacing the reducer.
I have not, but I have heard stories of it gelling up.
Mixing PFPE-based greases with grease made with synthetic hydrocarbons.
Tixitropic characteristics. We changed products.
Yes, I have encountered incompatibilities between different types of grease thickeners. Solution was performing a grease flushing in the bearings.
Yes, bearing failure with significant additional damage to the machine when grease with an incompatible thickener was added during maintenance.
Grease in a bearing application. Customer wanted a cross-referenced product due to the inability to find the product presently utilized. When the competitive supplier looked at the application, he failed to do a compatibility check between the grease recommended and the grease presently in use. Incompatibility between the two thickeners caused the grease to run out of the bearing, causing excessive heat, etc.
We see problems all the time when electric motors are sent out for service. Polyurea-thickened grease gets mixed with lithium-based greases and, once put back into service, all the grease runs out of the motor. The solution is to send the grease you want to use with the motor when it goes for service.
No. We always test and purge old grease.
I have not encountered a problem of this nature in the field. However, we have had issues where misalignment and contamination were strongly indicated. Clients were advised to improve their cleanliness practices and to adhere stringently to their OEM guidelines governing bearing installation.
Yes. There are frequent problems with incompatibility when recommending a grease to replace a grease with a different thickener.
Yes, the grease softened and there was a negative effect on the four-ball wear performance. We flushed the system to minimize the effect of the previous grease. We found that if there is less than 10% of the previous grease contaminating our grease, then the performance of our grease was maintained.
Not really. I always recommend that if the grease type is not known to be compatible, you should flush the bearing with new grease.
Yes. We switched a customer from his product to ours. We knew it was not compatible because of testing done. We formulated a plan to purge and flush, and it worked just fine.
No, although it is a concern. Between constant vigilance regarding incompatibility and the scarcity of incompatible thickeners, I have never had a problem.
Yes, of course, we see it all the time. Lube technicians pumping unidentified grease into a bearing and then wondering why the grease is running out of the same bearing. We are then asked why our grease has started to run, and the reason invariably is because incompatible grease has been added to it. Our solution is simple—the use of color coding on all grease zerks as well as the use of color-coded clear grease guns so operators can clearly see which grease is in the gun.
Yes, grease incompatibility caused the mixture to turn into a sticky paste. We had to tear the equipment apart and clean out the whole system.
Additives can soften some greases, especially corrosion inhibitors. An intensive study of alternative chemistry was required in order to properly achieve a high level of salt water corrosion inhibition without affecting long-term mechanical stability in a polyurea grease.
Working in the R&D lab of a grease manufacturer, we occasionally hear of incompatibility-related issues in the field. These are usually when greases are accidentally mixed in a machine. The best solution is often preventative measures—a new procedure or lubrication equipment that allows only the correct grease in the correct application (dedicated lubricators, individual fittings, color coding, grease rationalization, etc.)
Yes. Initial blends hardened in the container while in storage. Once that happened the grease’s reputation was severely damaged. We were on site during the conversion process to a competitive grease. It was a very time-consuming, expensive lesson. Our reputation survived and was enhanced; the grease manufacturer’s not so much.
Reformulating greases from Group I to Groups II and III base oils. Required much work to balance thickener content and oil separation.
Yes, I think I have seen everything. From structural collapse to grease mixtures becoming stiffer than either grease being mixed.
Yes. A thickener issue between lithium complex and organoclay. It was early in my career, and not being aware I lost a good client.
A customer replenished a bearing we supplied with our equipment with high performance grease, which was incompatible with the original grease. It
caked out, the oil came out of suspension and the bearing failed multiple times. Once we learned of this maintenance practice, we sold new bearings to him with no grease, and he could pack the expensive, high performance grease into the bearing to his heart’s content. Problem solved.
Yes, motor grease mixing. Flush the entire housing and stick with one grease type only. Procedures help a lot too.
Yes, had big globs of grease/additive. Went with a different supplier of the additive and it worked!
Softening due to different thickeners. Clean or purge out old product before using new product.
No, because we always conduct compatibility tests first. There is an ASTM procedure for this, but our testing goes beyond that.
Do you consider compatibility of greases when using or recommending grease for a particular application?
Almost never
0%
It depends on the application
11%
Yes, I consider general information on grease thickener compatibility
49%
Yes, I almost always complete or request compatibility testing
40%
Based on responses sent to 13,000 TLT readers.
© Can Stock Photo / sspopov
What are the most significant technical innovations/developments with lubricating greases during the last couple of decades?
The development of new synthetic greases.
That lubricating greases can last longer than ever before. Also, new and innovative lubricants such as graphene are becoming popular in many technology arenas.
Calcium sulfonate grease technology, lithium hydroxide dispersions for making lithium complex greases, new aluminum complex technology.
(1.) Development of vastly improved polyurea greases, especially regarding shear stability. (2.) New and better calcium sulfonate greases regarding low temperature pumpability. (3.) Development of PU and CS food grade formulations. (4.) Boron-based complexing agents.
Calcium sulfonate complex grease.
Thin film sheer strength.
New thickeners and base oils.
The rise of calcium sulfonate greases and our success with them in the field. New technology is far better than alternatives.
Improved additive packages.
Technological advancements, extended service intervals and the reduction of various soap thickeners for applications.
Polymer-thickened greases.
The introduction of calcium sulfonate greases versus lithium complex greases.
The development of shear stable polyurea grease, which is compatible with many other types of grease.
High-temperature performance.
Food grease technology and health and environmental compliance.
Ultrasound technology.
Continuous grease manufacturing capability versus batch/kettle blends.
Generally the improved additives, but I look forward to more data on the performance of greases based on calcium sulfonate thickener.
The fact that lithium ion battery technology may be a significant factor in lithium supplies not formerly threatened for lithium complex grease production. Calcium sulfonate complex greases should become more prevalent and cheaper as well and more accepted as a result of the potential for lithium shortages. I thought the real catalyst would be that it is a better overall universal solution. Grease technology is becoming more of an exact application—specific solution than just “slathering some of that thick black stuff on the pins to lube ’em up.”
The use of synthetic lubricating oils.
The consolidation on largely lithium and lithium complex greases.
Boron-free additives.
Additives to prevent corrosion of engines.
Some of the grease additive and thickener technologies that shorten and simplify the grease-making process. Less black magic and more science.
I am impressed with the complex soap thickeners and the organoclay thickeners. I am not sure that I fully appreciate the polymeric grease thickeners.
Electric motor greases and synthetic upgrades.
Longevity.
Discovery of PFPE greases.
Grease technology involved in the use of lithium multipurpose greases.
Inline blending.
Grease additive packages that improve the performance of lithium-based greases.
Non-metallic soap thickener systems.
Affordable ultrasound applications for greasing.
(1.) The introduction of novel polymer-based greases. (2.) The development of calcium sulfonate complex greases.
The wider availability and application of greases with different thickener systems. The greater willingness and understanding within the industry to use different grease technologies for specific applications to get the best performance results.
The art of combining new thickeners with synthetic base oils have significantly enhanced performance of grease and extended reasonable service intervals.
Development of diurea thickeners and incorporation of synthetic base fluids for higher performance and longer life expectancy.
The slow move away from multipurpose toward greases that are adapted for specific applications.
Automatic greasing becoming more prevalent, at least in our industry (mining.)
Cross-linking agents for better heat capacity.
Polyureas, improved lithium complex thickeners, polymers, continuous manufacturing techniques.
Editor’s Note: Sounding Board is based on an email survey of 13,000 TLT readers. Views expressed are those of the respondents and do not reflect the opinions of the Society of Tribologists and Lubrication Engineers. STLE does not vouch for the technical accuracy of opinions expressed in Sounding Board, nor does inclusion of a comment represent an endorsement of the technology by STLE.