20 Minutes With Nico Broekhof
Rachel Fowler, Associate Editor | TLT 20 Minutes December 2016
This organic chemist with international credentials examines trends in fire-resistant fluids, cold rolling oils and green formulations.
NICO BROEKHOF - The Quick File
Dr. Nico L.J.M. Broekhof has a doctorate in organic chemistry from Leiden University, The Netherlands, and currently works for Quaker Chemical. During 1982-1989 he worked for Quest International (Givaudan) and was involved—as manager of the organic research group—in the development of new fragrances and flavors. In 1989 he joined Quaker Chemical. He held several positions in research management, recently as global R&D director for fluid power. He specializes in the development of novel product concepts for industrial process fluids.
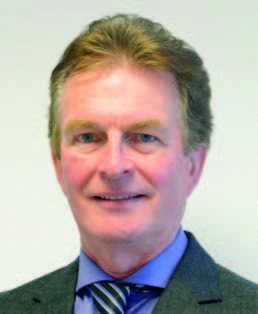
Nico Broekhof
TLT: What first attracted you to pursue a career developing fire-resistant fluids?
Broekhof: Throughout my career I have been involved with structure-activity relationships (SAR), the relationship between the chemical and three-dimensional properties of a molecule and its physical behavior.
At Quest International (formerly Naarden International, now Givaudan), we tried to develop novel fragrances. One project involved leather fragrances. By analyzing several types of leather available on the market, we found that most likely phenolic compounds were responsible for the typical leather fragrance, although the exact molecules could not be determined. Via synthesis we prepared a number of these compounds and, via a selection process by various perfumers, some of these were selected and found their way as key ingredients in leather fragrances. Examples are tetrahydro-α-naphthol (
see Figure 1) and m-Cresol (
see Figure 2). Note the structural resemblance.
Figure 1. Perfume compositions and perfumed articles containing dihydro- and tetrahydro-α-naphthol as fragrance material (U.S. Patent 4643844).
Figure 2. Perfume compositions and perfumed articles and materials that contain derivatives of m-Cresol as perfume component (U.S. Patent 4689175).
TLT: Can you explain more about your role at Quaker Chemical?
Broekhof: At Quaker Chemical we were involved in several SAR projects. In order to improve and optimize the lubrication properties of our cold rolling oils, we closely cooperated with several universities such as Imperial College, Georgia Tech and University of Twente.
Some of the key parameters studied were the viscosity pressure coefficient such as the Barus a-value or the Roelands z-value, coefficient of friction and film forming properties. Next to the theoretical considerations, equally important is the development of test methodology that will allow you to actually measure the relevant parameters for certain lubricants. Only then will you be capable of linking lubricant film-forming properties to the molecular structure of your selected base lubricants. All this has finally allowed us to select specific synthetic esters as superior lubricants in this specific application.
Results have been implemented in many formulations, specifically Quaker’s Quakerol series of cold rolling oils.
A summary of recent work can be found in a recent article (
1) by my colleague Dr. Bas Smeulders.
Another key project has been executed with Dr. Tharwat F. Tadros, Imperial Chemical Industries (ICI). In order to optimize emulsion properties such as droplet size, long-term stability under shear and lubricant delivery, polymeric surfactants were studied. These surfactants provide multiple anchoring points as well as excellent steric stabilization for an emulsified lubricant droplet. Consequently the resulting emulsion is far less sensitive to shear compared to an emulsion stabilized by traditional surfactants. As a result, the emulsion behavior during actual usage in the field is much more robust and stable in time. This research led to Quaker’s defined particle-size distribution series of products:
•
Tadros, T. (2006), “Principles of emulsion stabilization with special reference to polymeric surfactants,”
J Cosmet Sci., Mar-Apr,
57 (2), pp. 153-169.
•
EP 1 063 280 A1.
Nico Broekhof with the Dry-TOST Test equipment. (Photo courtesy of Theo Willems.)
TLT: Why are fire-resistant fluids needed and why are there so many different types?
Broekhof: In fire-hazardous areas—such as hot rolling plants, die-casting plants or hot stamping plants where hydraulic equipment is in operation close to hot or even liquid metal (steel, zinc, aluminum and magnesium)—it is strongly advised to use a fire-resistant hydraulic fluid. Standard mineral oil-based hydraulic fluids have a low fire resistance and can create a high danger when a leakage near a hot surface or liquid metal occurs (
2).
Here is an example: A large automotive components manufacturer had a series of fires on its hot stamping lines. All were caused by oil—from ruptured hoses or leaky couplings—that ignited when the oil came into contact with the hot metal being formed. In 2012 a particularly bad fire injured workers and caused 12 days of downtime, resulting in €5.3 million ($5.9 million) in damages from lost production and repairs.
The most commonly used fire-resistant hydraulic fluid is water glycol (HFC). This hydraulic fluid type is a mixture of approximately 40% water, 40% glycol, 15% thickener and 5% additives. Although HFC has good fire resistance and is cost competitive, it also has clear disadvantages. Due to the nature of the base fluid, HFC is prone to give corrosion in valves or heat exchangers. Due to the poor lubrication characteristics of HFC, pump wear is relatively high and pump life is low (
3).
A good alternative to water glycol are water-free products based on natural and synthetic esters (HFD-U). In our research in the last decades, we have focused on improving almost every property of this type of fire-resistant fluid.
TLT: Can you share any experiences where fires caused by the incorrect choice of fluid have resulted in major damage?
Broekhof: With respect to fire resistance, we have followed the guidelines provided by Factory Mutual Global. Getting our fluids on their approval list has been a prime target. Factory Mutual Approval Standard 6930 focuses on the so-called spray flammability parameter (SFP):
SFP (normalized) = 11.02 × 106 × Qch / (ρf qcrmf)
Q
ch: chemical heat release rate (kW)
q
cr: critical heat flux (kW/m
2)
ρ
f:
density of the fluid (kg/m
3)
m
f:
fluid mass flow rate (g/s)
When you work out the key fluid parameters that determine the SFP value of a given formulation you will find that the heat of combustion, the density and the fire point of that formulation are by far the most important. These three parameters can be measured relatively easily and, thus, you can start designing optimized formulations. Additives such as antioxidants (AOs) have a limited impact on these parameters, so you can focus on designing base fluids—synthetic organic esters—that are optimized for fire resistance and will pass Factory Mutual approval.
TLT: Tell us more about how lubrication is related to hydraulic fluids.
Broekhof: With respect to lubrication, numerous publications demonstrate that esters are superior lubricants compared to mineral oils. Because of the polar ester moiety, they have the ability to form reaction films, which protect metal surfaces under thin film, boundary lubrication. As a result, the coefficient of friction provided by esters is lower than that of mineral oils. This explains the improved energy efficiency of ester-based formulations.
The viscosity index (VI) of organic esters is much higher than the VI of mineral oils, resulting in a much wider window of operation with respect to temperature.
Nico Broekhof with the TRACE Gas Chromatograph (GC) Ultra machine. (Photo courtesy of Theo Willems.)
TLT: Tell us more about how oxidation stability is related to hydraulic fluids.
Broekhof: Hydraulic systems become increasingly more compact with tighter filtration, smaller fluid reservoirs and higher pressures resulting in higher fluid temperatures. This places greater demands on the hydraulic fluid. Its oxidation stability will be tested considerably.
Numerous articles have been written on the mechanism of oxidation. Equally many articles have been devoted to the various types of AOs and their interaction with, for example, radicals, peroxy radicals and hydroperoxides. However, very little is known on the specific impact of these AOs on the lifetime of ester-based hydraulic fluids. Also, little is known about the
interaction—synergistic or antagonistic—between various types of AOs.
Using design-of-experiment (DOE) techniques, we have been able to build in-depth knowledge on AO behavior as well as greatly improve the lifetime of our ester-based hydraulic fluids.
The key oxidation tests that we used in this study were the Dry-TOST Test (ASTM D943, ISO 4263) and the RPVOT Test (ASTM D2272, IP 229).
As an example, we studied, in a three-way ANOVA, the impact of three phenolic AOs on the Dry-TOST lifetime of a base fluid. This base fluid has a lifetime of about 75 hours without phenolic AOs. In this design with 18 tests, we received an average value of 108 hours, but the variation was huge: 67-140 hours. So Chemist 1 comes back and will tell you: “These AOs are useless; I got only 67 hours,” while Chemist 2 says: “Great AO package! I got 140 hours.” This clearly demonstrates the benefits of DOE versus trial and error (
4). Applying these techniques allowed us to double the lifetime of our Quintolubric 888 series of hydraulic fluids.
TLT: Do you see changes in current fluid technology in the near future? If so, what may that be?
Broekhof: Future developments will be driven by changes in the approval requirements of companies like Factory Mutual and the major OEMs of hydraulic equipment.
Another major global trend is the development of green formulations, for example, as regulated in the European Ecolabel for environmental friendly hydraulic fluids and the Vessel General Permit from the U.S. Environmental Protection Agency.
Finally, as formulators of value-added hydraulic fluids, we depend on novel raw materials—base lubes or additives—that will become available on the market.
As an example of a novelty that combines various aspects described above, I would like to mention the development of unique synthetic esters based on algae technology. Companies like TerraVia (formerly Solazyme) offer tailored triglycerides via genetically modified algae. Some of these triglycerides have unique fatty acid distributions resulting in greatly enhanced oxidation stability.
The corresponding synthetic esters (e.g., neopentyl glycol, trimethylolpropane or pentaerythritol esters) offer excellent oxidation stability as well as good low-temperature properties and hydrolytic stability, making them suitable for a range of industrial lubricants.
FOR MORE INFORMATION
•
Novel Synthetic Esters Based on Tailored Triglycerides by Nico Broekhof, Leo Hoogeveen and Lex Herrendorf. Presented at the 2015 STLE Annual Meeting.
•
International Patent Application No. PCT/US16/33056 for Synthetic Esters Derived From High Stability Oleic Acid.
REFERENCES
1.
Smeulders, B. (Feb. 2015), “Novel laboratory lubrication tests for cold rolling emulsions,”
Iron & Steel Technology. Available
here.
2.
See
QUINTOLUBRIC® fire-resistant hydraulic fluid test compilation. Available at
www.youtube.com/watch?v=bEtlikCMRWM.
3.
See
Benefits of converting from water glycol to synthetic water-free fluids in die casting hydraulic fluid systems. Available
here.
4.
Development of Optimized AO-Packages for Ester-Based Hydraulic Fluids Using DOE-Techniques by Nico Broekhof, Lex Herrendorf and Peter Skoog. Presented at the 2010 STLE Annual Meeting.
You can reach Nico Broekhof at broekhon@quakerchem.com.