Evonik Resource Efficiency
Base oil selection optimizes Evonik’s NUFLUX™ formulation to deliver durability and long-lasting performance attributes
By Dr. Justin Langston, Evonik Technical Service Manager | TLT CMF Plus November 2016
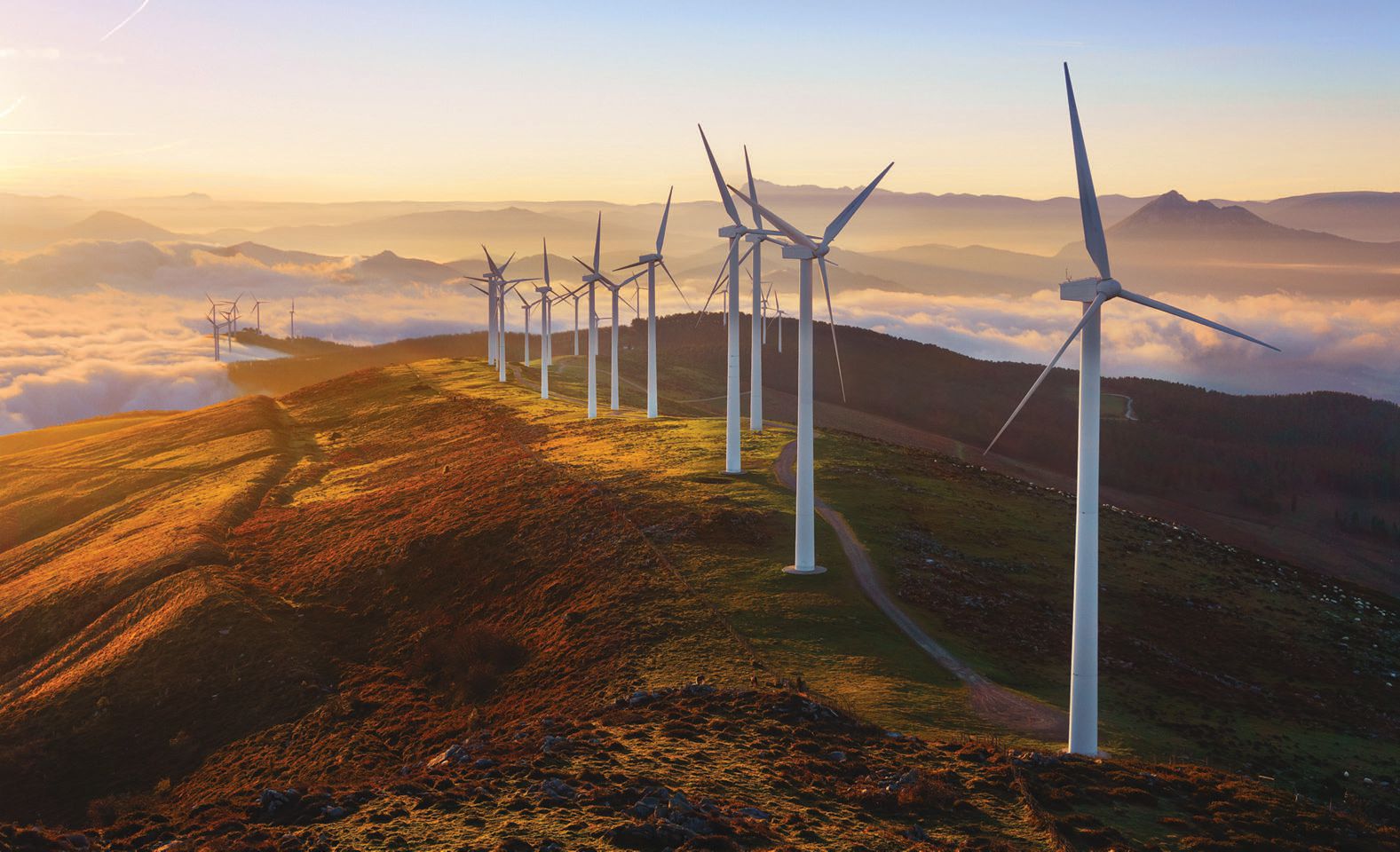
Evonik’s industrial gear oil formulation has earned approvals that include Siemens MD approval for Flender gear units, approval by Hansen Industrial Transmissions, and an approval from Winergy.
Premium synthetic base oils have long been the choice for some of the world’s most severe industrial applications. Their selection frequently hinges on several features and attributes, not the least of which is cost balanced against overall value.
To reliably provide long-lasting durability for vital equipment as well as other high-value performance attributes, such as cooler and cleaner operation, Evonik’s solution is a formulation that optimally combines its premium VISCOBASE® high-viscosity synthetic base oil with NESTE’s low-viscosity Group III oil and a high performance additive package. And now, after many years of conducting successful bench tests as well as numerous field tests, Evonik’s VISCOBASE® formulations have earned the key approvals that are recognized as “musts” in the industry.
Meets industrial standards and OEM specs
Significant approvals earned include the Siemens MD* approval for Flender gear units, approval by Hansen Industrial Transmissions, as well as an approval from Winergy. Evonik’s formulations also meet the requirements of DIN 51517-3 CLP and AGMA9005-EO2. Evonik has named this collection of products, formulation concepts and services to customers in need of resource-efficient industrial lubricants – NUFLUX™ Technology.
“Our goal is to transfer the value of NUFLUX™ technology and its key approvals and endorsements to our customers as they formulate high-performance lubricant solutions for their industrial gear oil customers,” explains Dr. Justin Langston, Evonik’s industrial gear oil technical service manager.
Evonik’s bench test regime for its NUFLUX™ technology lubricants included the performance aspects in which its customers would likely have the most interest: low temperature performance, wear and fatigue, propensity for oxidation and seals compatibility. Wear and fatigue were tested using the FE8 roller bearing rig and micropitting was tested according to FVA 54/7.
From bench tests to field testing
As the industrial gear oil technical managers at Evonik transitioned from bench tests to field testing, they sought out some of the most severe operating environments. Wind turbine gear boxes came up high on their list. Through its NUFLUX™ technology, Evonik aimed to develop a synthetic gear oil lubricant formulation that would provide a high-performance alternative to conventional PAO formulations.
As the field tests began, Evonik’s NUFLUX™ formulation began proving itself in a number of ways. Running at lower temperatures, and running cleaner in terms of fewer particles, reduced sludge, and improved varnish control, the NUFLUX™ technology formulation was providing reliable operation over an extended period of time.
“In one test, “notes Dr. Langston, “the NUFLUX™ formulation operated for two years with no evidence of lubricant degradation while continuing to provide the desired level of protection. “The cleanliness and reduced rate of oxidation contributed to the long life of the oil and the extended drain intervals it enabled,” he adds.
Today, NUFLUX™ technology is operating in a variety of different types of turbines and gearboxes with many field trials underway.
Reduced lubricant oxidation and reduced chemical attack
As its field tests have confirmed, lower-temperature operation achieved with NUFLUX™ technology means reduced lubricant oxidation and reduced chemical attack on seals. “And for wind turbine operators, NUFLUX™ technology also shows strengths in other ‘common heartburn’ problems such as foam, sludge, deposits, and water contamination,” Dr. Langston adds. “In fact,” he goes on, “we’ve witnessed cases in which a NUFLUX™ – formulated lubricant has replaced the previous in-service oil, and it has had a remedial effect on varnish deposits left by the previous oil.
Additional mechanical efficiency
In addition, the improved viscosity index of the lubricant formulated with NUFLUX™ technology provides opportunities for reduction of churning losses and additional mechanical efficiency [
See Chart 1]. Because of the improved viscosity index, equipment owners, who are currently using a mineral oil gear oil, are able to employ a synthetic industrial gear oil that is a full grade lower without any loss of protection [
See Chart 2].
*Siemens Mechanical Drive
Chart 1.
Chart 2.
VISCOBASE® and a high-performance additive package …
In summary, the Evonik “recipe” for NUFLUX™ technology consists of high-viscosity synthetic VISCOBASE® base fluid, NESTE’s low-viscosity Group III oil, a high-performance additive package, advanced formulation concepts, and a strong measure of technical support. Remember too, that formulations based on NUFLUX™ technology have passed extensive bench test programs and have approvals from leading industry OEMs. Numerous proof-of-performance tests have been, and continue to be conducted in the field.
To get the latest data on NUFLUX™ technology, contact the Oil Additives specialists at Evonik at
evonik.com/oil-additives, OR, learn more at our YouTube channel: “The Oil Additives Specialists at Evonik.”