20 Minutes With Mihir Patel
Rachel Fowler, Associate Editor | TLT 20 Minutes November 2016
This scientist for Vanderbilt Chemicals shares his three-pronged approach for researching lubricant additive chemistry.
MIHIR PATEL - The Quick File
Dr. Mihir Patel is a scientist in petroleum R&D at Vanderbilt Chemicals, LLC, in Norwalk, Conn. As a member of the R&D team, he conducts fundamental research focusing on tribology, additives-surfaces interactions, tribofilm characterization, partial additive package formulation and optimization, lubricant additives evaluations and developing new testing protocols. He also provides technical support to external and internal customers for the issues pertaining to tribology and lubrication.
Patel leads and facilitates new product development of the additives and additive packages for engine oils and greases. He has authored and co-authored 35 peer-reviewed papers and presentations along with four patent applications. Patel received a bachelor’s degree in mechanical engineering from Pune University in Pune, India. After obtaining an a master’s of business administration from Sardar Patel University in Gujarat, India, he earned a doctorate in materials science and engineering from the University of Texas in Arlington, Texas. He also holds STLE’s Certified Lubrication Specialist™ designation.
Mihir Patel
TLT: What interested you in pursuing a career in tribology?
Patel: After finishing my undergraduate degree in mechanical engineering, I started working as an application engineer for a company that provides condition monitoring services for various equipment in sugar and chemical industries such as gearboxes, bearings installed with steam turbine and induced and exhaust draft fans for boilers. During that time I experienced the importance of lubrication and the enormity of downtime due to improper lubrication practices. This made me curious to comprehend the mechanism of how lubricant provided surface protection at the atomic level.
After toying for a number of years with the puzzle, I made a decision to pursue doctoral studies, but the task felt overwhelming and wherewithal was uncertain. STLE-member Dr. Pranesh Aswath, professor at the University of Texas at Arlington, helped me overcome my sense of unease and hesitation. Once the decision to pursue my doctorate degree was made, ensuing years of doctoral research indelibly deepened my interest in tribology and lubrication. During that time I studied the interactions of various surface active additives and the roles they play to protect surfaces from wear.
TLT: What is your approach to research and how has it influenced your career?
Patel: One of the foremost qualities of a researcher is the aptitude for simplification and improvisation to achieve a practical solution to the field problem. To do so, my approach is always three pronged. For instance, formulating robust lubricating oil—irrespective of the application—typically faces two challenges: (1.) to optimize friction and (2.) to improve reliability of mechanical system. Challenges to meet these demands using lubricant require the fundamental understanding of (1.) mechanical system, (2.) additive chemistries and (3.) interaction of lubricant additives with mechanical system. My bachelor’s in mechanical engineering helps me understand the mechanical system; my doctorate in material science enables me to understand interaction of lubricant additives with different metal surfaces. My experiences at Vanderbilt Chemicals enable me to understand lubricant additives chemistries. This three-pronged approach gives me a larger perspective to understand the research subject from different viewpoints. This has been influencing my research and career.
TLT: What are some recent technological advances or challenges that have a strong impact on tribology and lubrication?
Patel: Customer expectations to extract more power with better fuel efficiency and governmental regulations to reduce greenhouse gases from the internal combustion (IC) engines drives the innovation in the IC engines, base oils and additives technologies. We tried to map out innovation in these areas using published technical literatures and patents, as shown in Figure 1. We observed the significant increase in the innovations and advances in the engine technology after 1995. Various major technological advances such as turbocharger, direct injection, variable valve timings, cylinder deactivation, use of light weight metals, hard coatings, cylinder honing, use of clean fuel, exhaust gas recirculation, selective catalytic reduction, etc., have contributed significantly toward the innovation in the engine design.
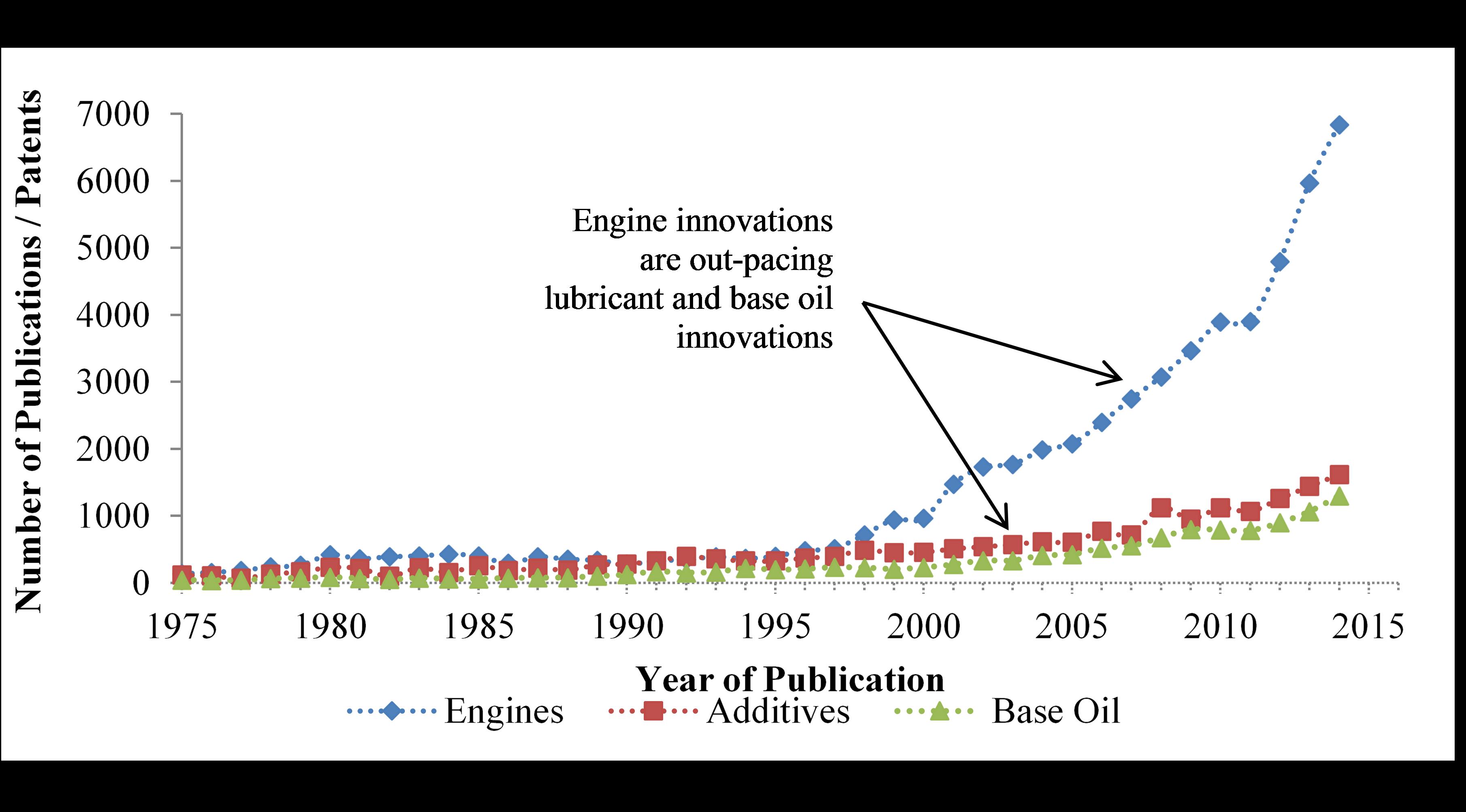
Figure 1. Published technical literatures and patents. There was a significant increase in the innovations and advances in the engine technology after 1995.
On the other hand, innovation in the additives and base oil technologies is not growing at the same pace. Various factors could be responsible. Health, environmental and safety regulations, time-consuming evaluation and approval process for additives, slow adaptation of novel technology, cost, lack of fundamental understanding of interactions of additive-additive and additive-surface interactions and more prohibitive patents than innovative patents are among the factors that could hamper and delay the innovation in the additive technologies.
This gap could be a point of concern. For example, today’s engines are smaller, hotter, powerful and more efficient than their previous generations. Hence, new generation engines require robust lubricating oils that keep engines clean from sludge and deposit in high-temperature environments, provide improved wear resistance for the components that operate in tighter tolerances than their predecessors and provide longer drain interval and—at the same time—maintain fuel efficiency throughout the useful life of the lubricating oil. In addition, chemical limits on the phosphorus, sulfur and sulfated ash demand for more innovation in the additive technology. Oil formulators are relying on older additive technology to solve the new sets of challenges posed by new-generation engines. Low-speed pre-ignition is one perfect example of it.
I believe that significant innovation in engine technology but sluggish innovation in additive technologies will strongly impact upcoming engine oil technology. This requires additives companies to continue investing on research and development of novel and robust additives chemistries.
TLT: Vanderbilt Chemicals has an applications laboratory that supports fundamental, developmental and applied research in additive chemistry and tribology. What type of work is this laboratory engaged in?
Patel: The Petroleum Applications Laboratory is equipped with various instruments to measure wear, friction, oxidation, corrosion and emulsion properties of engine oils, greases and industrial oils. The Petroleum Applications Laboratory supports six important activities: (1.) Provide customer technical support to evaluate products according to their specifications. (2.) Evaluate novel additives developed by additive synthesis group. (3.) Conduct fundamental research to understand the interaction of various surface active additives within the fluid and on different surfaces. (4.) Participate in round robin and ASTM proficiency tests. (5.) Develop new test protocols for lubricant evaluation. (6.) Qualify production batches of commercial products for their performance according to the specifications.
TLT: What factors led to the decision by Vanderbilt Chemicals to invest and upgrade the applications laboratory?
Patel: Vanderbilt is well known for molybdenum and friction-reducing chemistries, and we believed (and still do) that we are well positioned to contribute to the global macro-demand for improved vehicle fuel economy and associated reduction in greenhouse gas emissions with our existing product range and innovation efforts. In addition, current engine oil technologies and additive technologies are going through a period of revolution to cater the need of the next-generation engine.
Next-generation crankcase lubricant requires robust additives with higher thermally and oxidatively stable molecular structures. These additives will need to do this with environment friendliness, cost competitiveness and operational robustness. So we decided to invest in facilities that could help screen novel additives and promote these technological solutions to cater the need of next-generation lubricants.
Mihir Patel and his coworkers in Vanderbilt’s Petroleum Applications Laboratory.
TLT: Describe an important instrument the lab has recently acquired for supporting research in additives and tribology.
Patel: Vanderbilt Chemicals’ Petroleum Applications Laboratory is equipped with various instruments that evaluate oxidation, wear, friction and corrosion properties of lubricating oil accordingly to ASTM test methods. One of the crucial and most difficult parameter to develop fuel efficient lubricating oil is to retain its fuel efficiency throughout the drain interval of oil. With the oxidation of lubrication oil, fuel efficiency of lubricating oil also reduces. Hence, to develop the robust friction modifier molecule that can retain friction after aging, we invested in various instruments that can simulate aging characteristics of engine oils.
Internally developed test methods on these instruments help us understand the impact of molecular structure on the aged oil friction retention performance. For instance, one way to understand friction reduction and aged oil friction retention properties of engine oil in different lubricating regimes is with Stribeck curves. We recently purchased a Mini Traction Machine that generates Stribeck curves in different rolling and sliding conditions. In addition, we also purchased SRV–5 and configured it to simulate piston-cylinder contacts to evaluate frictional and wear characteristics of lubricants in pure sliding conditions.
We also purchased high-temperature corrosion bench setup and use it as a bulk oil oxidation apparatus to age the engine oil in studying aged oil friction retention properties. We use other supporting instruments to study the submicron film formation using thin film interferometry, optical profilometer to study the surface properties and measure wear volume of worn surfaces.
Vanderbilt Chemicals’ Dr. Mihir Patel working at his laboratory computer.
TLT: How does the applications lab support the petroleum industry? Can you provide an example of a research project or challenge that was solved?
Patel: Apart from providing technical support to our customers, the Petroleum Applications Laboratory also conducts fundamental research to help synthesis chemists design robust molecules. As I mentioned previously, the lubricant industry requires innovation in the additive technology. We continually work to develop robust additives. Vanderbilt is known for producing organometallic-based antiwear additives, extreme pressure additives and friction reducers. One of the key products that Vanderbilt has developed is molybdenum dithiocarbamate (MoDTC). Many commercial MoDTC additives are available. These MoDTC additives vary based on their synthesis method, amount of molybdenum and sulfur in the molecules, types of branching attached to the core, etc.
One common misperception is that all MoDTCs behave very similarly in terms of their tribological performances. However, little information is available on the impact of different MoDTCs prepared with different synthesis methods.
In addition, MoDTC is a well-known multifunctional additive that reduces coefficient of friction and also acts as an antioxidant. MoDTC acts as both peroxyl radical trapping and hydroperoxide decomposing antioxidants. During engine operation MoDTC is consumed and affects friction reduction capabilities and, hence, lower fuel efficiency. Thermally and oxidatively stable molecular structures of MoDTC are very important to retain lower friction throughout the drain interval.
Three MoDTC samples were used with the same amount of molybdenum (10%) and sulfur (~11%) to understand the impact difference on synthesis methods on the friction reduction and aged oil friction retention properties in low viscosity oil.
MoDTC samples were added at 320 ppm molybdenum to a prototype engine oil with SAE 0W-20 viscosity. The 0W-20 prototype engine oil was prepared by blending typical lubrication additives such as antiwear, antioxidant, detergent, dispersant and viscosity index improver in a Group III mineral base oil. The 0W-20 prototype engine oil was prepared without any friction modifiers.
Figure 2 compares the performance of different MoDTCs before and after aging. Stribeck curves were acquired at 140 C and 254 minutes of prolonged rubbing time. As shown in Figure 2a, MoDTC samples blended at a 320 ppm molybdenum treat rate exhibit significant and similar reductions in the coefficient of friction. However, these formulations after aging exhibit a significant difference in the coefficient of friction. In particular, frictional performance of commercial MoDTC is significantly deteriorated after aging. MoDTC-Vanderbilt also shows an increase in the coefficient of friction after aging but lower than commercial MoDTC samples. Contrarily, frictional performance for MoDTC-Vanderbilt Experimental sample before and after aging remains the same.
Figure 2. (a) Stribeck curves acquired on lubricants before aging and (b) after aging at 140 C and after 254 minutes of prolonged rubbing time.
It is worth mentioning that all MoDTC samples are made with different synthesis methods and stoichiometry. Although they have similar molybdenum content in the molecule, they exhibit drastically different behavior after aging. This suggests that synthesis method, overall composition of MoDTC and robust molecular structure makes a significant difference in the aged oil friction retention performance and fuel efficiency of engine oil.
You can reach Mihir Patel at mpatel@vanderbiltchemicals.com.