20 Minutes With Tim Walker
Rachel Fowler, Associate Editor | TLT 20 Minutes October 2016
UNIST’s senior vice president examines the pros and cons of minimum quantity lubrication and flood coolants.
TIM WALKER - The Quick File
Tim Walker is a senior vice president at UNIST, Inc., a leading manufacturer of environmentally friendly machine lubrication systems. Walker has more than 20 years of experience in jobs ranging from engineering to senior corporate management. He previously served as vice president of sales and marketing for Dornerworks, an electronic engineering company specializing in safety critical markets that also was named one of the 50 Companies to Watch in Michigan. Prior to that, Walker spent 13 years working for X-Rite, Inc., a $250 million global manufacturer of color quality control instrumentation and software. He held various positions during his time there, including vice president of engineering, vice president of software development and category director for their graphics arts business unit. Walker wrote The MQL Handbook: A Guide to Machining With Minimum Quantity Lubrication, which was published in 2013.
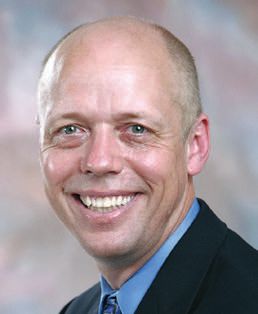
Tim Walker
TLT: Could you tell us the pros and cons of a minimum quantity lubrication (MQL) system versus using flood coolants?
Walker: There are a number of advantages to MQL, and a couple of
gotchas to watch for, but it is helpful to first define MQL.
At the highest level, it is an alternative means to flood cooling to control temperature during metal cutting. Instead of using a stream of (mostly) water to transfer the heat away, a comparatively small amount of lubricant is applied to reduce the heat generated. The MQL moniker does a good job of capturing its two main differences from flood cooling: minimum quantity and lubrication.
Minimum quantity is a somewhat fuzzy term, and there is not, to my knowledge, an internationally recognized definition. However, the Germans have established a good starting point in DIN 69090, describing it as up to 50 mL/hour of lubricant and, in exceptional cases, up to 150 mL/hour. This is in sharp contrast to the 30,000-60,000 mL/hour typically used when flooding. This tremendous decrease in what is used—often so little you cannot see the lubricant being applied—is probably the hardest thing for operators who are accustomed to flood coolants to get used to when moving to MQL.
The other difference is using lubrication to reduce the heat generated instead of simple heat removal. Flood cooling largely relies on conductive heat transfer as the coolant flows over the cut, tool and workpiece. MQL instead relies on the lubricant reducing the heat created in the secondary shear zone, the convective heat transfer created by the air blowing over the hot zone and energy absorbed by the oil as it is vaporized (
see Figure 1). The underlying mechanisms are very different.
Figure 1. A summary of differences between flood cooling and MQL. (Figure courtesy of UNIST, Inc.)
Knowing this helps understand the pros and cons of MQL. The pros fall into three basic categories: environmental, enterprise and economic. The cons fall into the category of process sensitivity.
MQL is a much greener approach than using flood coolants. Most of the lubricants are vegetable-based esters or fatty alcohols that are not toxic and readily biodegradable. It is considered a dry process (less than 2% of the fluid is left on the chips) where the fluid is consumed. There is no fluid that needs to be disposed of or recycled. Since lubricity is key, MQL is usually done with straight oils that do not need biocides and do not go rancid. It is often chosen based solely for its environmental benefits.
The advantages to the enterprise also can be significant. The oils rarely irritate the operator’s skin, eliminating dermatitis, making happier and healthier employees. The reduction in fluid helps keep the floors clean, both an aesthetic and safety benefit. It also means the parts are clean when the machining is complete. This often eliminates the need for a secondary cleaning operation and is, again, a safety benefit if one can avoid having an operator handle a slick, heavy part. Surface finishes are usually better and often tool life is improved because of the reduction in thermal cycling, and micro-particles (smaller than the filter) from previous cuts are not present to act as abrasives as the fluid is recirculated.
There are often economic benefits as well. The most obvious savings is from reduced fluid usage. The oil costs more per drop than coolant, but when calculated per part the costs are usually lower. There also are the savings as a result of tool life improvements. But the savings come in many other less-obvious forms: the equipment you do not have to buy to keep fluids clean and usable, the improved machine uptime when the coolant isn’t getting into parts and panels, the reduced energy use because you are not running the pumps and other fluid systems. MQL helps operating efficiency in many ways.
However, like everything in life, the benefits do not come for free. Flood cooling is quite easy to get right. As long as you have fluid flowing over the cut you have it right. MQL is not as forgiving. Since you are putting on very little fluid, it is critical it goes to the right spot. When using external nozzles, they must be positioned correctly. While easy to do on simple equipment like saws, this can be challenging in machining centers with things in motion. Through-the-tool MQL makes output positioning more automatic but requires more systemic changes such as MQL-specific tool holders and tooling.
MQL also is sensitive to the amount of lubricant used. Empirical evidence indicates that the graph of tool life versus lubricant applied is a bathtub curve. You can put on too much and you can put on too little lubricant, with a fairly broad range in between giving good results. There are currently no practical tools for pre-determining this amount. It is something of a trial-and-error approach.
When moving to MQL, one also must consider chip evacuation. There is no stream of fluid to wash chips away, so thought should be given to how to move them before implementing MQL. A rule of thumb is that the heat distribution between the workpiece-tool-chip is 5%, 5% and 90%, respectively. Having very hot chip stay in contact with the workpiece will increase the workpiece temperature. There also may be issues with re-cutting chips if they are allowed to build up. This can usually be taken care of by using an air blow-off nozzle or a chip fan to blow the chip away. But if not considered, chip issues can catch the inexperienced MQL adopter by surprise (
see Figure 2).
Figure 2. A rule of thumb: The heat distribution between the workpiece-tool-chip is 5%, 5% and 90%, respectively. (Figure courtesy of UNIST, Inc.)
The tool and workpiece will also run warmer with MQL than with flood. As long as the tool is kept within its designed operating range this usually isn’t a problem, and, as previously mentioned, the lack of quenching can have positive side effects. However, depending on the thermal mass of the workpiece, the needed tolerances and the amount of heat generated by the cut, the thermal expansion of the workpiece can affect positional and dimensional accuracy. There are mitigation techniques and this issue is relatively rare, but once again the process may need to be changed to accommodate MQL.
TLT: Can an MQL system easily replace a flood system?
Walker: The short answer is that from the equipment perspective, the answer is usually yes, and from a cutting process perspective it is a maybe. The longer answer depends on what machine type and operations you are doing.
On a fairly simple machine like a saw, the switch is generally easy. Disconnect the flood system (if any), hook up the MQL applicator, install a nozzle (typically one made specifically for sawing) and you are ready to go (
see Figure 3).
Figure 3. Simple MQL system on a saw. (Figure courtesy of UNIST, Inc.)
On a CNC machine it is more nuanced. It depends on the type of machine and if you are applying fluid through the spindle, spraying with external nozzles or both. For example, on a five-axis machine, external nozzles present different issues (where to place them so they spray in the right spot yet are out of the way of tool changers and other moving things) compared to through-the-tool MQL (optimizing the flow through a rotating delivery path) (
see Figure 4).
Figure 4. Sophisticated MQL system on a five-axis CNC. (Figure courtesy of UNIST, Inc.)
TLT: Can the MQL process be applied to untraditional materials such as titanium and Inconel?
Walker: Yes, it can. How well it works and how practical it is depends on the material and the specifics of the operations being done to it.
With titanium there are several laboratory studies that indicate MQL works well. However, my experience has been that some struggle with it in the field. I believe this is, in large part, because of the process sensitivity issues mentioned before. Machining titanium is difficult and MQL adds another layer of process to think about. I think it is a matter of maturity with the process more than a fundamental limitation of MQL, but either way it is a challenge today.
In contrast, MQL typically does very well when cutting Inconel. The focus on lubricating the secondary shear zone seems to help reduce the development of a built-up edge. Many who work with Inconel see significant tool life increase when switching to MQL.
TLT: The automotive industries are extensively using MQL processes. Can you tell us the cost savings from the flooding system?
Walker: Ford, Volvo, Mercedes-Benz, BMW and Volkswagen all use MQL extensively in the machining of crankshafts, engine, gearbox and chassis parts. Ford stated that MQL has given a 13% improvement in total cost of ownership compared to wet operations. These savings came from fluid reduction, increases of 20%-30% in cell uptime due to a reduction in electronics failures and nuisance alarms, the ability to have flat floors, reduced water usage, allowing machining cells closer to transfer lines and a host of other advantages that come with a cleaner operation.
The latest version of the book Metal Cutting Theory and Practice states that 30%-40% of total energy used in machining goes to the coolant system. By eliminating this, Ford reports it sees significant net energy savings. The energy for high-pressure coolant is eliminated, although the energy for compressed air is slightly increased (
see Figure 5).
Figure 5. Example power requirements for flood coolant systems based on cut type. (Figure courtesy of UNIST, Inc.)
All of this does not come without effort on the part of the adopters. In the Volkswagen Salzgitter plant they worked with the toolmakers to optimize a tap MQL performance. They discovered, as have many others, that the optimum design for a low-volume aerosol flow is not the same as optimizing for high-volume liquid flow. Once done, they found they could tap 32% more pieces than they could before.
Refining the process can make a tremendous difference. As Heiko Dormann, a specialist for MQL at Volkswagen Salzgitter, says, “Actually MQL is very simple—once you understand the process thoroughly.”
TLT: What’s in the future for MQL?
Walker: I think we will see MQL adoption continue to grow as the tools and techniques become more refined and understood.
Research today is helping to determine the proper process parameters for cutting with MQL. As this knowledge is grown and spread, the understanding of how to optimize and when to use MQL will become more defined and its adoption made easier.
From the technology perspective, MQL applicators are getting more sophisticated with the ability to integrate closely with the machine and accurately control the amount of fluid and air dispensed. I suspect the next step will be focusing on the last mile: external nozzles will be designed to less intrusive, both nozzles and tool holders will become more adaptive and MQL-specific tools will become more available. This will allow the system to be run much closer to the ideal process.
From the machinist perspective, things will get easier and the art needed to dial in a system will be done automatically by the system. Machining will become cleaner, greener and safer—a big win for everyone.
You can reach Tim Walker at twalker@unist.com.