Fundamentals of rust preventives used for temporary corrosion protection
Dr. Nancy McGuire, Contributing Editor | TLT Webinars September 2016
A lot of things can happen between the steel mill and the finished metal part. Corrosion doesn’t have to be one of them.
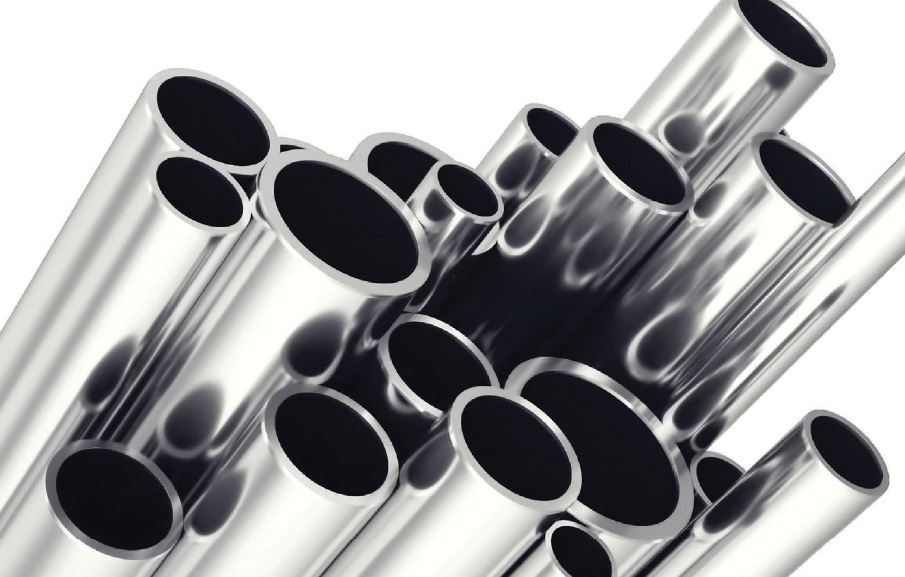
© Can Stock Photo Inc. / Rost9
KEY CONCEPTS
•
Rust preventive films provide weeks to months of corrosion protection.
•
Sulfonates, waxes and oils in rust preventives interact synergistically to keep water away from metal surfaces.
•
Rust preventive testing evaluates a range of attributes, including corrosion protection and water separation.
MEET THE PRESENTERS
This article is based on a Webinar originally presented by STLE University on Nov. 5, 2014. “Fundamentals of Rust Preventives Used for Temporary Corrosion Protection” is available at
www.stle.org: $39 to STLE members, $59 for all others.
Greg Moran is a project manager, technical services, with The Lubrizol Corp.’s metalworking group. He has 24 years of experience with rust preventive additive technology, development, formulation, applications and testing. Greg received his bachelor’s of science degree in chemistry from the University of Pittsburgh at Bradford. He worked as a research and development chemist for anticorrosion product development with RPM Inc.’s Alox metalworking additives business. After Lubrizol acquired Alox, Greg joined Lubrizol’s metalworking group. You can reach Greg at
gregory.moran@lubrizol.com.
Ben Faber is the metalworking North America product manager at The Lubrizol Corp. where he has worked for seven years. He is a Certified Metalworking Fluids Specialist™. He has a bachelor’s of science degree in chemistry from Case Western University, and he began his career doing research and development of rust prevention products. His current focus is on product management. You can reach Ben at
ben.faber@lubrizol.com.
Greg Moran
Ben Faber
IN THE JOURNEY FROM A STEEL MILL TO A FACTORY MAKING FINISHED PARTS, metals are often subjected to machining processes, heat treatments, chemical washes and other aggressive operations. There are many instances in this journey where unfinished metal is exposed to corrosive environments that require temporary corrosion protection. Keeping corrosion at bay requires the right kind of protection for each stage of the process.
Rust preventives are not the same as the corrosion inhibitors that protect metal surfaces during machining and grinding. Corrosion inhibitors, surface-active additives that are soluble in metalworking fluids, are typically composed of organic acid salts or similar compounds. Corrosion inhibitors are effective at protecting metal that is immersed in a cutting fluid, and they provide a few weeks of protection if the cutting fluid residue is left on the metal.
Rust preventives are applied as barrier films to metal surfaces after the machining and grinding stages. They displace water and protect metal parts from corrosive environments during shipping or storage.
Roller bearings, for example, could be flooded with a water-based coolant during the final polishing step. If the coolant is left on the metal, it could stain and corrode the bearings, so after polishing the bearing assembly is dipped into a rust preventive to displace the coolant and leave a protective film.
Rust preventives are used in many other applications for temporary corrosion protection, including protecting unfinished pipe, steel consumer products, car underbodies, steel fasteners and coiled steel. They are often chosen in applications where removal is important.
MARKET SUMMARY
Rust preventives are generally included in the metalworking fluids market because they share many of the same suppliers and customers. In 2012 an estimated 300,000 tons of metal protecting fluids were used around the world—about 12% of the total market for metalworking fluids (
1).
Asia uses about half of the world’s supply of rust preventives, driven in a large part by China’s large metal parts exporting industry, which requires parts to be protected during shipping. The remainder of the market is split about evenly between the Americas and Europe. Asian markets use solvent-based or oil-based protective fluids almost exclusively. These fluids also dominate in American markets, representing about 80% of market share. European markets, where environmental regulations can be more stringent, uses a higher percentage (about 40%) of water-based rust preventives (
1).
TEMPORARY VERSUS PERMANENT
Painting metal surfaces is another way to keep rust away from finished parts, but not every metal surface can be or needs to be painted. For example, parts that will later be put through a metal-forming application should not be painted. Alternatively, some metal parts that have a short life cycle are better served with a short-term rust preventive instead of a long-term paint.
Permanent coatings, of which paints are one example, are typically 25–200 microns thick and can be applied as multiple coats. Many are water based, and they are applied to clean, dry surfaces. These coatings can be durable and damage-resistant, providing protection against hundreds to thousands of hours of exposure to corrosive environments.
Rust preventives are typically applied as a single coat that is 2–20 microns thick. Most rust preventives are solvent based, and they can be applied over oily, wet or soiled surfaces. These coatings are meant to be temporary—they are typically removed after they have served their purpose. They are also easily damaged, but when left intact they can provide as much as 200 hours of protection against salt spray (one common way to measure protection against corrosion and the basis of several standard testing methods).
FORMULATING RUST PREVENTIVES
Many rust preventives are made by mixing additives into a diluent of choice. The diluent can make up 80%-95% of the finished fluid, and it is generally chosen based on the desired film characteristics as well as other factors like flash point and volatile organic compound (VOC) emissions.
Solvent-based diluents, including mineral spirits, evaporate off and are not a part of the dried protective film. This makes for a more durable film, but the solvent fumes can cause health, safety and environmental problems, as well as concerns because of their low-flash point.
Oil-based diluents provide rust protection as well as lubrication. Their VOC content is lower than for solvents but not completely absent. Because oil diluents are a part of the final film, the coated part will have an oily surface and will never fully dry. Traditional rust preventives use naphthenic oils, but cost-effective Group II paraffinic oils are gaining in popularity. Older additives may not dissolve well in paraffinic oils, but newer additive packages with better solubility are now available.
Water is an attractive diluent because it is inexpensive and has no VOC content. Water fully evaporates and is not a part of the final film, which increases the protection offered by the film. However, drying times are slow and impurities (e.g., hard water minerals) can be a source of problems. Water-based rust preventives do not effectively displace water, so additional cleaning may be necessary to remove coolant residues prior to application of the rust preventive.
Rust preventives are formulated using a mixture of additives with the formulator carefully balancing performance with cost. Ingredients commonly used in rust preventives include waxes, sulfonates, oils and specialty ingredients (
see Figure 1).
Figure 1. Metal sulfonates combine synergistically with waxes or oxidized waxes to form a corrosion protection layer over a metal surface. Oils or solvents act as diluents. (Figure courtesy of The Lubrizol Corp.)
Waxes, which are highly crystalline and have a flaky texture, often are oxidized to improve their performance. Oxidizing a wax, oil or petrolatum produces a product with more chemical polarity, lower crystallinity (which gives it a smoother texture) and a lower melt point. These chemical changes produce a rust preventive with a stronger attraction to a metal surface, better solubility and better lubrication.
Metal sulfonates are typically salts of sulfonic acids with barium, calcium or sodium. These polar compounds enhance the ability of the rust preventive to wet the metal surface, giving a more intact and uniform coating. The sulfonates’ affinity to metal can displace water from the metal surface. Metal sulfonates also assist in solubilizing the waxes and oxidized waxes in the fluid.
Barium and calcium sulfonates offer the best water-displacement properties, while sodium sulfonate is best for making emulsifiable (water-based) rust preventives. Barium presents some environmental concerns, but some regions continue to use barium sulfonate because historically it was known to separate water better than calcium and sodium sulfonates. However, improvements in rust preventive formulation have produced calcium sulfonate-containing fluids with equal or better water separation performance compared with barium sulfonate.
Metal sulfonates have hydrophilic (polar) heads that adhere (chemisorb) to metal surfaces and hydrophobic (nonpolar) tails that protrude away from the metal and provide a barrier film. The organic tails of the sulfonates can vary in molecular weight and branching, and the number of tails can vary.
Metal sulfonates by themselves provide a barrier between a metal surface and the outside environment, but that film can have defects that leave parts of the surface exposed. Wax or oxidized wax molecules become entangled with the hydrophobic tails of the sulfonate molecules, forming a more robust, more hydrophobic film than either the sulfonate or wax component alone. For example, 10% of either a sulfonate or an oxidized wax in a solvent might provide 30 days of protection to a metal part in a humidity cabinet (a common testing environment). However, a 10% combination of wax and sulfonate could provide more than 60 days of protection (
see Figure 2).
Figure 2. Metal sulfonate molecules have polar heads that bind to metal surfaces, driving off water. Their long organic tails become entangled with the long molecular chains from the wax component, forming a water-repellent protective layer. (Figure courtesy of The Lubrizol Corp.)
Specialty ingredients also are added for niche products to enhance protection against acid fumes and provide better surface wetting and a range of other properties. Formulating metal protection fluids requires a balance between several factors, including performance factors (barrier properties, wetting and water separation) and the cost and solubility of various components.
RUST PREVENTIVE REMOVAL
Rust preventives can be applied using a dip tank, sprayer (conventional or electrostatic), roller, brush or by wiping, and the application method often depends on the size and shape of the part. After the film has served its purpose, it is removed, commonly using alkaline degreasing cleaners. Clean removal of the rust preventive is essential to the performance of subsequent processing steps like painting, phosphating or galvanizing, or welding.
To see how well a rust preventive coating can be removed after use, The Lubrizol Corp. does an in-house cleaning test. Panels coated with a rust preventive are allowed to dry completely, and then soaked in a 5% alkaline cleaning solution. During the soak, the panels are submerged halfway in the cleaning solution, where they sit for 7.5 minutes at 45 C. Afterward, the panels are rinsed with deionized water and dipped into a copper sulfate plating solution. Panels where the rust preventive has been cleanly removed show a more uniform copper plating. Harder to clean formulations show gaps in the plating, indicating that the rust preventive was not well removed by the cleaner (
see Figure 3).
Figure 3. Dipping test panels into a copper plating solution shows differences in the ease of removal of various rust preventive fluids by an alkaline cleaning solution. Here, barium sulfonate films are removed less completely than similar calcium sulfonate films. (Figure courtesy of The Lubrizol Corp.)
Interestingly, the copper plating test shows that barium sulfonate products are more difficult to remove compared to calcium sulfonate products. This might lead to the assumption that barium-based products offer more protection against corrosion. However, the salt spray test described below reveals that traditional barium and calcium sulfonate products protect about equally well against corrosion, while new-generation calcium sulfonate products offer much better protection (
see Figure 4).
Figure 4. Having a rust preventive (RP) film that is difficult to remove does not guarantee the best protection against corrosion. Top to bottom: traditional barium and calcium sulfonate products offer less corrosion protection than either of two new-generation calcium sulfonate products. (Figure courtesy of The Lubrizol Corp.)
TESTING METHODS
Several standard methods are used to evaluate and compare the performance of rust preventives. Some tests use a simulated environment to accelerate corrosion, while other tests evaluate rust prevention under actual usage conditions.
In ASTM B117 Salt Spray, an accelerated testing method for extreme atmospheres, test panels are housed in a chamber held at 35 C. A 5% aqueous sodium chloride solution is continuously sprayed throughout the chamber. Coated metal panels are run to failure (disregarding the outer eighth-inch of the panel). The test method does not provide a criterion for failure—the vendor and the customer generally define suitable criteria. The Lubrizol Corp. defines failure as more than 5% rust on the surface of the panel.
ASTM D1748 Humidity Cabinet is an accelerated testing method for indoor storage. The test chamber is held at 49 C and 100% relative humidity. Polished carbon steel test panels are run to failure, defined as one or more dots of rust larger than 1 mm, or four or more dots of any size. Again, the outer eighth-inch of the test panel is disregarded, as well as areas surrounding the holes for the hanger hooks.
The salt spray test gives results much more quickly than the humidity cabinet test. Coated test panels can withstand as much as 60 days in a humidity cabinet without showing signs of corrosion, whereas salt spray can initiate corrosion in the first couple of hours. The speed of the salt spray has made it a common test method, even though metal parts in a given application might never be exposed to salt in actual use.
A stack stain test based on the military specification MIL-C-22235A can determine the effects of water contamination, heat and metal-to-metal contact on coiled or stacked metal surfaces. Test panels are coated with a neat rust preventive solution or one contaminated with water and stacked in a sandwich arrangement. The panel stack is stored for 24 hours at 82 C. Failure is defined as any sign of staining or rust. This test is useful for situations where air does not penetrate between the layers of metal. Here, corrosion does not appear as red rust, but rather as a dark stain. Specially formulated non-staining rust preventive fluids are called for in this situation.
A rust preventive’s ability to displace water from a metal surface can be tested using MIL-PRF-16173E. Clean test panels are submerged in distilled or deionized water for five seconds and then immediately submerged in rust preventive solution for 15 seconds. The panels are stored in a static humidity chamber at 25 C for one hour. Failure is defined as any sign of rust, mottling or surface stains.
For rust preventives applied by dip application, water carried on the part into the dip tank can interact with a rust preventive fluid, which can reduce its ability to offer effective protection. One method for measuring water separation is ASTM D1401. The Lubrizol Corp. has its own water separation test, in which a room-temperature mixture of 75 mL rust preventive solution and 25 mL water is placed into a 100-mL graduated cylinder and inverted six times. The time needed to separate out all 25 mL of water is recorded—anything less than five minutes is considered good. This method can be modified to better simulate specific real-world conditions (
see Figure 5).
Figure 5. In this water separation test, shown after 2.5 minutes, a traditional barium sulfonate product expelled 20 mL of water (out of 25 mL added), and a traditional calcium sulfonate product only separated out five mL. Two new-generation calcium sulfonate products separated out all 25 mL of water. (Figure courtesy of The Lubrizol Corp.)
The protection that rust preventive fluids offer may be only temporary, but this protection is a key factor in reducing loss during storage and shipping, making these fluids a worthwhile investment.
REFERENCE
1.
Kline and Co. (2014),
Global metalworking fluids: Market analysis and opportunities. Report #Y650C. Available at
www.klinegroup.com/reports/y650series.asp.
Nancy McGuire is a free-lance writer based in Silver Spring, Md. You can contact her at
nmcguire@wordchemist.com.