Other than cost, what are the biggest obstacles to using new additives in finished lubricant formulations?
TLT Sounding Board September 2016
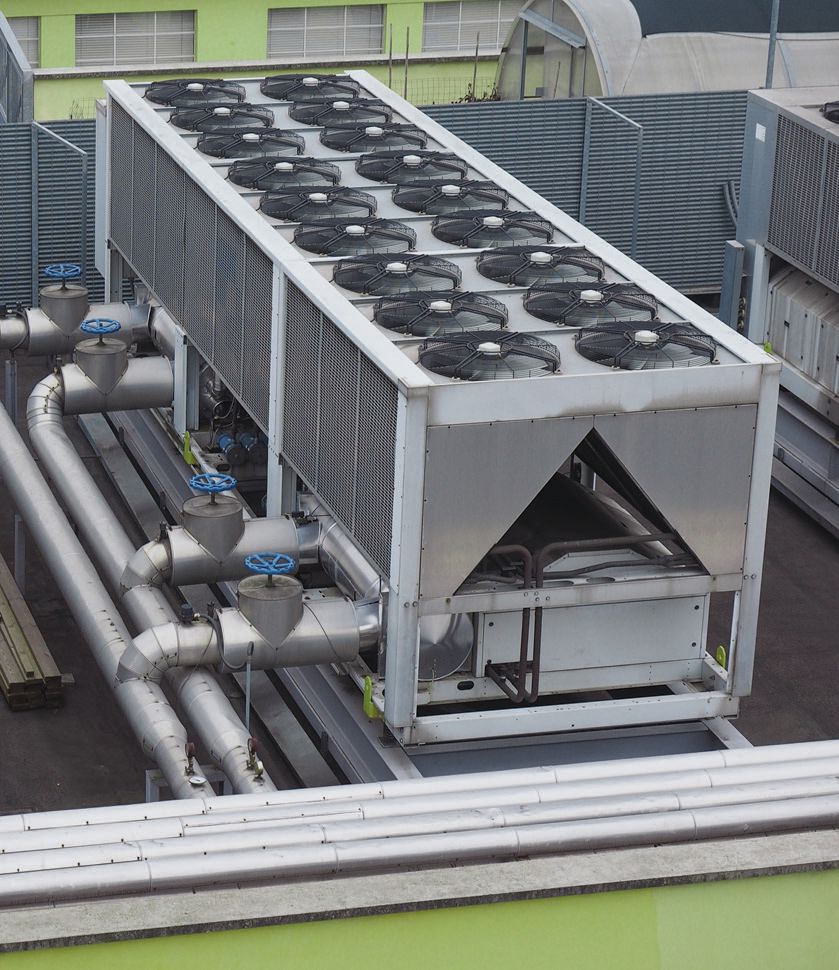
© Can Stock Photo Inc. / claudiodivizia
According to TLT readers, there are quite a few, with global compliance, compatibility, OEM requirements and supply dependability topping the list. Several respondents said cost regulatory issues were causing them to purchase packages rather than developing their own from individual components. For other readers the issues are more subtle. “Finding something new, novel and better than what we already have is an issue,” said one, “the majority of ‘innovative products’ that come through our door are rehashed 30-plus-year-old technologies.” When asked to name which additive technologies must develop the most to meet the demands of future lubrication challenges, the top-cited products were antiwear and EP, friction modifiers and antioxidants and corrosion inhibitors.
Global approvals/EHSA issues.
(1.) Awareness about the additives. (2.) Concern that the additives in oil may negatively affect refrigerants. (3.) Time and resources for testing. (4.) The need and efforts to convince a customer about the benefits of the new additive.
Availability.
Environmental approvals.
Compatibility with the rest of the formula.
Reliability of supply.
REACH and other worldwide registration compliance.
Compatibility and performance.
Contamination.
Getting them incorporated into our system—it takes a lot of time, effort and red tape.
Approval from equipment OEM.
Lack of adequate support data such as performance comparison with other additives, base oil qualification and compatibility data when two formulations are topped up into each other.
Demonstration of no harm.
Ego—product was not invented here.
Changing spec sheets, SDS sheets, computer blending formulas, QC procedures, etc.
Customer approvals, legislative approvals and governing body approvals such as API, FM, etc.
Performance.
Health and safety. Collecting good, reliable field data on new products.
Able to communicate to the customer so they understand the need for change and the benefits of the change.
Large additive packs.
The fear of change.
Culture change.
Lubricant qualification and additive life. Qualifying lubricants for refrigeration applications takes years. Some refrigeration systems also need to last a decade or more without lubricant changes.
Testing new formulations.
Concerns about the unknown—chemistry/interactions/change over time.
Associated approvals and lack of full data sets behind many of them is a real issue. The second biggest would be regulatory concerns in the form of country regulatory lists.
OEM requirements, licensing and testing.
Unknown effects on hardware.
Established track record.
Unknown end-product improvement.
Modifying MIL standards or accepting any changes in formulation to existing products is a very arduous and slow process.
Sustaining an organized effort through a team effort.
How satisfied are you with the additive choices available today for formulating finished lubricants?
90-100%
20%
70-89%
46%
60-79%
21%
50-69%
6%
Less than 50%
3%
Other
4%
Based on responses sent to 13,000 TLT readers.
Over the past decade, what are the two most significant changes that have impacted the way lubricants are formulated?
Regulatory restrictions and competition.
In refrigeration and air-conditioning industries, it was new ozone-friendly refrigerants; their development started per Montreal Protocol in 1987.
Group II base oils.
Base oils and green formulations.
OEM trends and emissions.
Environmental issues, new vehicle manufacturing technology.
Developing engine oil specifications and the need to rationalize plant inventory.
Energy losses.
They need to be lower in viscosity for the requisite fuel efficiency needs but robust at the same time to ensure durability.
Use of PAG fluids as lubricants and hydraulic fluids.
Environmental impact on finished product formulation due to use of low SAP formulations, OEM designs and performance levels.
Development of new specs. Use of distributors for additives.
Viscosities, environmental regulations.
The need for better environmental performance and the need for energy efficiency.
Fuel economy, global usability.
GHS! Types of metals being used.
The government requiring better fuel mileage in all classes of vehicles and moving toward “lighter” SAE grades for gasoline and diesel engines.
Fully formulated packages. Product information off the Internet.
Base oil availability and environmental regulations.
Performance standards and regulatory clearances.
Higher temps, loads, other OEM demands, global registration requirements.
Cost and availability.
First for us formulations have gone in the direction of buying packages more than formulating from individual additive components. This is driven by the cost and number of approval programs in the industry today. Second would be the base oil quality change to higher quality base oils.
Lower viscosity lubricants, hybrid electric vehicle lubricants.
Emission controls using better fuel mileage as the catalyst. Micropitting additives in EP gear oils.
GHS and the availability of information on the Internet.
Wider selection of emulsifiers and base fluids.
Restricted use of proven chemistry.
(1.) Move to lower viscosities to enhance fuel economy. (2.) Increase of OEM specs based on expensive proprietary tests that are not shared with the industry. These stifle innovation because the underlying science requirements cannot be used to form the basis for improved additives design, resulting in empirical approaches that are very inefficient.
Less component knowledge, higher performance base oil pool.
Base oil quality.
Formularies are complex; environmental regulations are more restrictive.
Need for improved efficiency and longer drain intervals from finished oils.
Synthetics.
Price.
Equipment-specific lubricants.
Increased performance expectations and regulatory complexity.
Biocide restrictions. Because I can only use the less-effective biocides, I have to engineer products using bio-hard and bio-resistant chemicals, which are all more expensive.
Changes that improved the thermal oxidative properties of lubricants. Improvements in degradation and hydrolysis.
Regulation and availability of green raw materials.
Lack of resources internally. Customers willing to try new products without field-proven experience.
Environmental impact.
Application demand, equipment design.
Group III base oils and GTL base oil availability.
Engine efficiency, emissions.
Improvements in base stocks and antioxidation additives that allow higher temperature operations.
SCR/DPF usage. Thinner oil films (lower viscosity and higher durability demands).
Efficiency and noise.
Synthetic base oil additivation for special cases (EP, AW, oxidative resistance, etc.).
(1.) People are going for cleaner lubricants. (2.) The environmental norms have become more stringent.
Synthetic formulations and molecular degradation.
Lower viscosity and emission.
Synthetics have increased operating ranges and saved money. More research has been done to the application of lubricants and their impact.
The two most significant changes that have had an impact on formulating a new product would be: (1.) everyone being overly sensitive about the NOACK volatility numbers. It was as if the only way for one major company to beat another’s product was to find anything that was better. Volatility was what they found so it became a big competition. (2.) The TBN numbers for extended change intervals. Too much can actually be too much.
(1.) Difficulty in defining desirable behavior. (2.) Lower viscosity engine oil development and use.
Chemistry development and major demand from customers for the extension of useful life of the equipment.
HVI base stocks and lower grades for engine oils.
Technical advancements.
As an additive supplier to the MWFs industry, I think the availability of fewer registered biocides has had a significant impact on raw material selection.
Demulsability packages, antioxidants.
Base oil availability and chemical regulations by region.
When developing a finished lubricant, is it preferred to:
Use a fully formulated additive package
51%
Start from individual components
38%
Top treat an existing additive package
11%
Based on responses sent to 13,000 TLT readers.
© Can Stock Photo Inc. / Naypong
What additive group must improve the most to meet the demands of future lubrication challenges?
Antiwear and EP
35%
Friction modifiers
29%
Antioxidants and corrosion inhibitors
24%
Detergents and dispersants
12%
Based on responses sent to 13,000 TLT readers.
Editor’s Note: Sounding Board is based on an email survey of 13,000 TLT readers. Views expressed are those of the respondents and do not reflect the opinions of the Society of Tribologists and Lubrication Engineers. STLE does not vouch for the technical accuracy of opinions expressed in Sounding Board, nor does inclusion of a comment represent an endorsement of the technology by STLE.