Metalworking fluids: Global challenges, trends and opportunities
Gabriel Tarle | TLT Market Report August 2016
How OEMs, suppliers and end-users are affected—and responding.
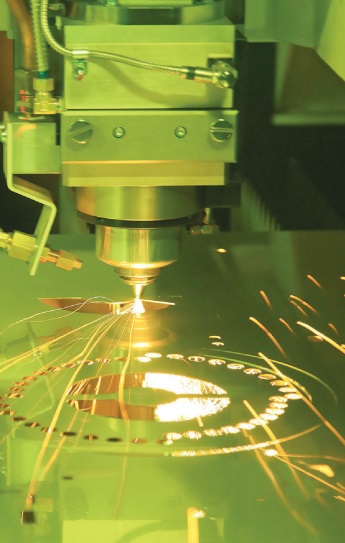
© Can Stock Photo Inc. / sspopov
KEY CONCEPTS
•
MWF additives comprise nearly 16% of the global lubricant additive market.
•
Regulatory bodies worldwide are substantially changing how MWF additives are labeled, traded and registered.
•
Machining trends such as high-speed cutting and minimum quantity lubrication also are strongly impacted MWF additives.
Even though metalworking fluids (MWFs) account for a little less than 6% of total lubricant volume, additives for these substances account for nearly 16% of the total lubricant additive market. This makes MWF additives the third most important product class in volume after heavy-duty and passenger car engine oils.
MWF additives are one of the most challenging product classes both for blenders and additive suppliers. MWFs are the most treated lubricant by number of components and treat levels. On average a removal fluid has 12 components, and a cold aluminum rolling synthetic additive pack could go as high as 97% of total lubricant weight. Health, safety and regulations, new machining techniques and new material technology are reshaping metalworking fluid formulations.
REGULATORY TRENDS
From a health and safety standpoint there are currently three main regulatory bodies influencing the industry: Registration, Evaluation, Authorization and Restrictions of Chemicals (REACH) in Europe, the U.S. EPA and the Globally Harmonized System (GHS) at a global level.
The GHS of classification and labeling of chemicals, a new system for chemical hazard reporting, was created in 2012 by United Nations-member countries to facilitate trade while safeguarding the environment and human health. The UN-member countries agreed to implement national systems similar to the GHS by scrapping the material safety data sheets and replacing them with new safety data sheets (SDSs).
The new hazard classification encompasses new symbols intended to create a standard and uniform international way of communicating hazard information to end-users. Though GHS is supposed to standardize the hazard information globally, suppliers affirm that U.S. SDSs will be very different from their European and Canadian counterparts. It is expected that India, China and Southeast Asia together with the Middle East will implement the GHS at a later stage.
EPA protects the environment and human health by enforcing regulations passed by the U.S. Congress. Following the recent legislative developments, the industry has created a new category of chlorinated paraffins—the very long chain chlorinated paraffin (vLCCP)—with chain length between C21 and C30. The vLCCPs are cleared for use by EPA and not classified by the European Union (EU) as hazardous.
In January 2015 EPA gave two options to chlorinated paraffin producers: stop selling MCCP and LCCP (C18-C21) immediately or don’t sell MCCP and LCCP after May 31, 2016. However, in September 2015 EPA delayed the ban on chlorinated paraffins until mid-2017. Since chlorinated paraffins are an important category of EP additives, this development will influence MFW formulations.
REACH requires all chemical substances on the European market to be registered by 2018. For the next registration phase (May 31, 2018), manufacturers and importers are required to submit a detailed substance dossier to the European Chemicals Agency (ECHA) for each substance within a given period if they market between one and 100 tons of the substance per year in Europe. According to the “no data, no market” principle only registered substances can be manufactured, imported and used in Europe.
The next REACH deadline imposes an innovation barrier due to the high cost associated with REACH registration procedures. Blenders might have difficulties getting some products after May 2018, as some of them that are sold in small volume might not be economically feasible for the expensive REACH registration.
Following recent regulations, MWF additives like some of the chlorinated paraffins will be increasingly restricted. MWF additive producers possibly will build innovation centers outside the EU after 2018 and choose not to register new chemistries with REACH because of higher costs. The EU will certainly lag behind other regions in terms of new chemistries, and this could also prevent smaller niche additive producers from entering the market. The GHS is certainly burdening the labeling process and increasing production costs, and end-users likely will cover the additional cost. Uncertain is how long it will take to have a functioning GHS across the globe.
Non-ferrous metals, alloys, exotic metals and composites will continue to change MWF formulation.
© Can Stock Photo Inc. / yuran78
MACHINING TECHNOLOGY TRENDS
Machining technique trends include high-speed cutting (HSC), minimum quantify lubrication (MQL) and dry machining. Non-traditional cutting methods that are gaining ground include laser, electrical discharge and water jet machining. For example, laser cutting is replacing work previously done by turret punch presses, plasma cutters, shears and mills. An advantage of laser machining includes the ability to machine burr-free edges. The aerospace industry, with its emphasis on increasing quality and accuracy while reducing costs, is a strong market for laser machining technology.
With HSC the neat oil is sprayed on under high pressure as an aerosol. Otherwise, the air layer turning with the tool bit would prevent the fluid from reaching the tool bit. Foaming and misting can be a problem.
In removal fluids, the dominant applications for MQL are boring and drilling. Some engineers affirm that MQL is limited in some applications because the machine can get overheated. In the automotive industry, for instance, machines work continuously for three shifts, and MQL cannot be used as the machines can overheat. Apart from this, automotive aluminum alloys are used, which can be very demanding of the machine. MQL is mostly used in drilling operations on aluminum and other non-ferrous metals. In casting, there would be a dusting issue if MQL is used. MQL reduces the amount of oil needed to machine a part by 80% or more.
In forming fluids microlubrication technology is successfully employed in forming operations such as blanking, stamping and tube drawing. Technically and commercially effective application of microlubrication requires appropriate metering systems, tool coatings and suitably designed machines and tools.
MWF additives have worked in favor of various machining techniques. HSC, MQL, dry machining and laser cutting have been available for a while, in some instances reducing the volume of fluids and implicitly the additives required. Some applications have benefited from such techniques, but experts agree that HSC, MQL, dry machining and laser cutting are limited to particular applications and tailored to the needs of individual producers.
As general machining technology improves with higher cutting speed and better precision cutting, the need for properly additized fluids increases primarily because of machine depreciation associated with wear. Factories have to stay competitive by efficiently managing production while maximizing machine lifetime.
NEW MATERIALS
New materials continue to penetrate the global automotive and aerospace industries. Increased use of aluminum is expected to be a growth factor for semisynthetic and synthetic fluids. Globally there is a trend toward improving vehicle fuel economy by using lighter metals and metal-reinforced fibers to keep overall weight of vehicle low.
Lighter non-ferrous metals or alloys, such as aluminum, magnesium and higher-strength steels, are used to manufacture lightweight vehicles. Exotic metals such as compacted graphite iron also are being used to manufacture certain vehicle parts to reduce vehicle weight for increasing fuel economy. These new metals or alloys could result in additional machining challenges for the metalworking industry. For example, there is a trend away from amines to other chemistries that are less aggressive in non-ferrous alloys.
Strong growth of the composites in the aerospace industry, particularly commercial air transport, will lead to changes in corrosion inhibitors and removal fluids. Composites do not generally have metal components, and there is no need for corrosion inhibitors. The most preferred polymer material is carbon fiber reinforced due to its durability and superior mechanical performance. However, any polymer-based composite cannot safely operate at temperatures above 150 C, well below the high pressure turbine operating temperatures. The high costs associated with machining the high-temperature metal alloys, as well as their heavy weight, make the alloys candidates for future substitution. Currently ceramic-based composites are being researched to replace metal alloys in some instances.
Non-ferrous metals, alloys, exotic metals and composites will continue to change MWF formulation. From the beginning of the 2000s, the complexity of automotive and aerospace manufacturing has demanded different types of fluids for ferrous and non-ferrous metals. Nowadays, weight reduction has prompted the use of composites and other polymer-based materials demanded more suitable fluid types.
NEW OEMS
The competition in the passenger jet industry intensifies as China’s first homemade plane just started service. Japan’s Mitsubishi announced it also is entering the market. This comes in addition to Russia’s Sukhoi and Brazil’s Embraer each launching a line of commercial aircraft.
MWF ADDITIVES
On the functional additive classes, regulatory drivers will have a major impact on the future use of EP additives. In the U.S. the transition to vLCCPs will be more prominent in metal-forming fluids due to their higher viscosity compared to MCCPs and LCCPs. But the vLCCP will be at disadvantage for metal-removal fluids where the sulfurized chemistries are easier to formulate. Both sulfurized olefins and fats will grow as a result. Phosphate esters are a good substitute for chlorinated paraffins when the cost is justified. They provide good antiwear and staining protection for aluminum alloys. However, they are used in less severe applications. From the same class, phosphonates are good for stain-free application.
The use of aluminum alloys have been increasing and pushing formulators to reduce the fluid pH to avoid alkaline-driven staining. However, the reduction of the pH generally results in reducing the fluid life when using phosphate esters, which are food for microorganisms. TEA could be a good fix due to its buffer abilities but only in small volume to avoid staining. Amine carboxylate and lactic acid have no health and environmental issues, but only the demand for lactic acid is growing. The demand for DCHA, a permitted secondary amine, has been growing for a while but is subject to the hazard label. DCHA, lactic acid and carboxylate are good alternatives to the boron technology. Boron compounds are used both in semisynthetic and synthetic metalworking fluids formulations and not so much in soluble water-based fluids. Their use is growing in India, but in other parts of world, particular North America and Europe, their use is declining.
There is a growing use of bio-additives, such as those made out of palm oil, as co-emulsifiers in the MWFs industry. They are used along with water-miscible MWFs and not with straight oils. Co-emulsifiers are used mostly in removal fluids. Distilled Tall Oil and diacids are the two major bio-additives used. Sulfonates had been the preferred emulsifier type due to their low cost; however, they are vulnerable to microbial breakdown and currently account for 50% of demand.
Microbial contamination is one of the most widespread problems in MWFs, and triazines dominate MWF application with more than 50% of the global demand. Although triazines are the leading biocides used, they also are a very effective corrosion inhibitor in water-based fluids. In Europe the market for metalworking fluids is regulated and many biocides have been removed due to the Biocidal Products Directive since 2006. Triazine dosages have been reduced to 500 ppm from 1500 ppm by EPA in metalworking fluids. France has banned the usage of formaldehyde-releasing agents, which is the case for the triazines. New biocides, which are not formaldehyde releasers or phenols, might gain ground in other European countries as well.
Globally MWFs are going through a challenging yet rewarding period. There are costs involved both in the upstream and downstream of the lubricants business associated with implementing the GHS. A major factor to consider when labeling metalworking fluids is trade secrecy. The U.S. makes it easy to claim trade secrecy, creating a backdoor to much of the GHS labeling procedure. And the GHS labeling would or would not be effectively applied. In such instances downstream players (blenders) should ask for more information about health and safety. In Canada and the EU, trade secrets are registered and are scrutinized by government agencies. Similar to Europe, in Canada trade secrets need to be renewed periodically.
Regulatory changes, changes in machining technology and new materials and emergence of new OEMs all pose significant challenges and opportunities for MWFs and additives suppliers. High value-added industries such as automotive and aerospace manufacturing are growing more demanding and seeking new solutions. Additive suppliers who can meet these challenges will succeed in this market.
Gabriel T. Tarle is a senior consultant at Kline’s Petroleum and Energy practice. He is responsible for both ad-hoc and syndicated studies across the entire supply chain of finished lubricants and related specialties, ranging from base stocks (virgin and re-refined), waxes and additives to automotive and industrial lubricants, as well as various process oils.
His key contributions for Kline’s market studies include Metalworking Fluids: Global Market Analysis and Opportunities; Global Lubricant Basestocks: Market Analysis and Opportunities–Europe; Global Wax Industry: Market Analysis and Opportunities–Europe; Global Lubricants: Market Analysis and Assessment–DACH, Romania, and other Eastern European countries; Global Synthetic Lubricants: Market Analysis and Opportunities–DACH.
Tarle has worked on a number of studies for Kline’s consulting projects related to market entry, niche market assessment, new products/services and material demand models.
Gabriel T. Tarle