What stalled the Wankel?
Dr. Edward P. Becker | TLT Automotive Tribology August 2016
Acceptance of the rotary engine slowed due to issues related to fuel economy, emissions and, yes, lubrication.
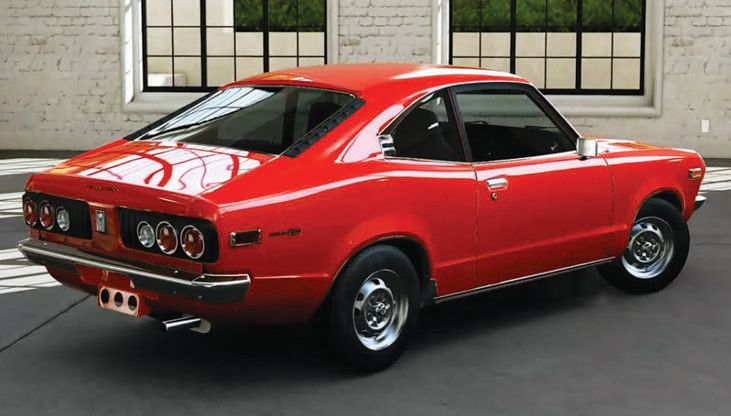
Although the Mazda RX-3 climbed to sales of 90,000 units in the U.S. by 1973, Wankel fever was short lived.
NOT EVERY AUTOMOTIVE INNOVATION that reaches the marketplace is destined for widespread adoption.
In 1970 Mazda began selling vehicles in the U.S. equipped with the Wankel rotary engine, achieving a respectable 0.02% market share. By 1973 the Mazda RX-3 captured 0.82% of U.S. sales, nearly 90,000 units.
This growth rate resulted in a bout of what could fairly be called “Wankel fever” in the automotive industry. Virtually every automaker (including General Motors, Ford, Chrysler and Toyota) signed licensing agreements for the technology, and many announced plans to take the Wankel into production. However, no commercially viable Wankel-powered cars were ever introduced by other manufacturers, and today even Mazda sells only piston engine vehicles in North America.
So what happened?
The best way to understand the operating principles of the Wankel is to view one of the many excellent animations available online. The key advantage of the Wankel is that it produces rotary motion directly (as opposed to the piston engine which must convert reciprocating motion into rotary motion). This results in fewer moving parts, and the mechanical simplicity translates into ease of manufacture and maintenance, as well as a high power-to-weight ratio.
There are some key disadvantages, however. The constraints on the shape of the combustion chamber means that combustion is relatively inefficient in the Wankel; therefore, fuel economy is usually lower than a comparable output piston engine.
Also, the large surface area of the combustion chamber contributes to higher emissions. By 1973 the U.S. was struggling with rising fuel prices and gasoline shortages due to an oil embargo. At the same time, the Clean Air Act required automakers to have plans in place to reduce emission.
As bad as this was, the Wankel was also faced with a daunting tribological problem.
An interesting (and necessary) property of the roughly triangular rotor is that all three apexes remain in contact with the roughly oval housing throughout the engine cycle. A device called an apex seal is required to keep the gasses in each chamber confined. Sealing the chamber during combustion is particularly critical, as pressure loss during this phase results in both loss of power and increased emissions. The apex seal performs functions similar to the piston rings in a reciprocating engine.
Piston engines typically use three rings per cylinder. The uppermost is the top compression ring, which confines the combustion gasses. Next is the second compression ring, also sometimes called the scraper ring, which adds some redundancy to sealing the cylinder and also removes oil from the cylinder bore walls on the down stroke. At the bottom is the oil control ring, which meters a small amount of oil (which splashes up or is sprayed up) onto the bore as the piston travels upward, to lubricate the rings in order to manage friction and wear during the power stroke.
In the Wankel engine, a single apex seal must perform all these functions and, further, there is no inherent mechanism for oil to reach the seals. Also, the apex seal moves in one direction only, so there is no opportunity to place and remove lubricant. Finally, while piston rings are circular seals and provide sealing force only in the radial direction, the apex seals are linear seals, and must provide sealing force in both the radial and axial directions.
Development continues on the Wankel engine, and its devotees maintain that the problems are solvable, and its time is yet to come. We shall see!
Ed Becker is an STLE Fellow and past president. He is president of Friction & Wear Solutions, LLC in Brighton, Mich., and can be reached through his website at www.frictionandwearsolutions.com.