Friction and Wear Fundamentals: Characterizing the Tribo-System and Defining the Tribo-Test
Dr. Nancy McGuire, Contributing Editor | TLT Webinars June 2016
Success depends on understanding the properties of the entire interacting system.
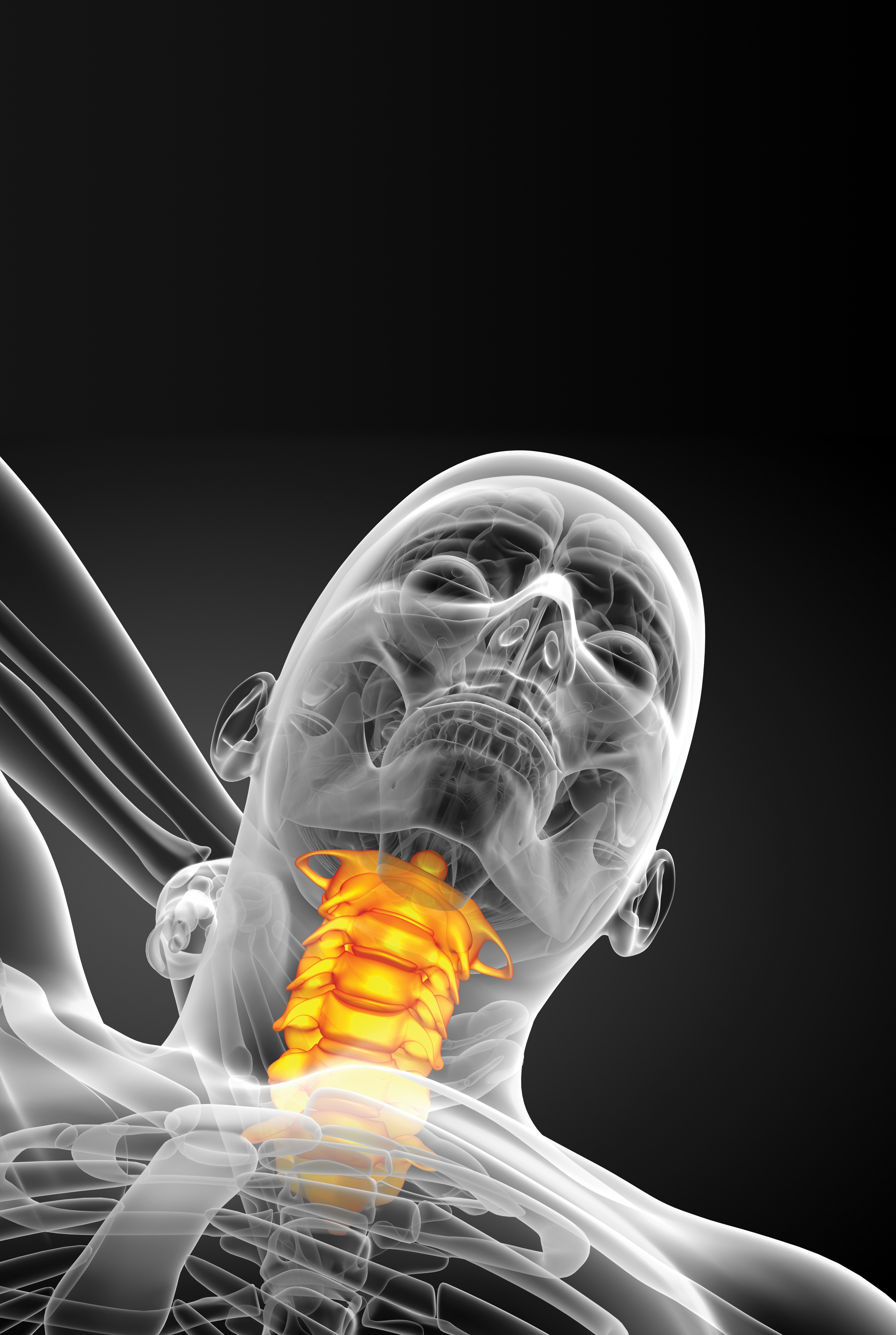
© Can Stock Photo Inc. / maya2008
KEY CONCEPTS
•
Friction and wear are not static numbers you can look up in a reference manual.
•
Wear rate is a system property, not a material property. It depends on the wear mode.
•
By properly understanding the tribosystem, we can make the right choices for materials, contact geometry, motions and chemistry.
MEET THE PRESENTER
This article is based on a Webinar originally presented by STLE University on Sept. 23, 2015. “Friction and Wear Fundamentals: Characterizing the Tribo-System and Defining the Tribo-Test” is available at
www.stle.org: $39 to STLE members, $59 for all others.
Steven Shaffer received his bachelor’s of science in mechanical engineering and his master’s of science and doctorate in materials science engineering from the University of California, Berkeley. He spent 22 years at the Battelle Memorial Institute in Columbus, Ohio, solving practical tribology problems for more than 50 industry and government customers.
During his time at Battelle, he served the tribology community by participating in the ASTM G-02 and D-02 Committees, and he is currently chairman of the G-02 Committee on Wear and Erosion. He has been active in STLE’s and SAE’s Dayton (Ohio) Sections and served on the IRG-OCED group for tribology and on the steering committee for the Wear of Materials Conference, which he chaired in 2009 and 2011.
Steven is an editor for ASTM’s Journal of Testing and Evaluation and is a former TLT technical editor. Three years ago he retired from Battelle and returned to the San Francisco Bay Area. He was recruited to provide tribology expertise and support to Bruker’s global applications and sales team after Bruker purchased CETR, a manufacturer of multi-function triboleters, from Norm Gitis. At present, Steven is a senior application scientist in the tribology, stylus and optical metrology business unit within Bruker’s Nanosurfaces group.
You can reach Steven at
steven.shaffer@bruker.com.
Steven Shaffer
WHAT IS TRIBOLOGY?
The word tribology comes from the Greek word
tribos—meaning to rub—and the suffix
logia meaning the study of. The field of tribology includes the study of friction, lubrication and wear. H. Peter Jost, working with a team of British linguists, coined this term in 1966 in his report to the British Parliament’s Ministry for Education and Science where he predicted “potential savings of over £515 million per year for industry by better application of tribological principles and practices.” (This is the equivalent of about $9.5 billion today.)
However, the field of tribology is older than the term. One Egyptian tomb drawing shows the first recorded tribologist pouring a lubricant (possibly water or olive oil) in front of a sledge transporting a statue of Ti (hairdresser to Egyptian royalty from about 2446-2426 BC, (
see Figure 1).
Figure 1. Transporting the statue of Ti from a tomb at Saqqara, Egypt. (Figure courtesy of History of Tribology by Duncan Dowson.)
Sketches in Leonardo da Vinci’s notebooks from around 1500 describe friction tests that closely resemble the present-day ASTM standard sled friction and 4-ball test geometries.
In 1798 England’s King George III asked H. Cavendish and C. Hackett to investigate the suspicious shrinkage of English coins. Hackett devised what was perhaps the first application-specific wear tester to determine the effect of alloying gold on its wear behavior and to measure the wear rates of coins rubbing other coins, sand, metal filings and gritty powders. He concluded that abrasive wear was not sufficient to explain the degree of diminution, which led him to conclude that people were shaving the coins to get the gold (
see Figure 2) (
1).
Figure 2. The early practical tribotesters of Hackett. (Figure courtesy of History of Tribology by Duncan Dowson.)
FRICTION FUNDAMENTALS
Friction is the resistance to relative motion between two bodies in contact—it’s the result of shearing forces. When objects touch there are microscopic forces between them: molecular adhesion and mechanical abrasion. Adhesive forces include electrostatic, Van der Waals forces, metallic bonds and molecular entanglements. Abrasive forces include elastic and plastic deformation. Friction also is influenced by contaminants at the interface: oxides, adsorbed films and gases and foreign or “domestic” particles (i.e., wear debris).
In its simplest terms, the coefficient of friction (COF) is the ratio of friction to the force normal to the surface (μ = F/N). However, because friction is a system property and not a material property, we need to specify an adequately complete set of parameters for the system. These include surface roughness, lubricant, surface chemistry, contact stress, contact geometry, environment, temperature, sliding speed and more. Measuring the COF under the right conditions will give you a number that is relevant to your application.
DEFINING THE TRIBOTEST
Reasons for conducting a tribotest include:
•
To understand fundamental mechanisms (combined with chemical, microstructural and surface characterization)
•
To determine whether a material choice is correct for an application
•
To compare or rank materials during a development or replacement program
•
To determine the life of a rubbing component or system
•
To check a process for quality control.
Irrespective of one’s motivation, there are logical steps to defining an appropriate tribotest. The first question to ask when you are designing a series of tests is, “What is the intended application?” This helps in selecting the elements to incorporate into the tribotest, which can be divided into the following five main areas. The list may seem extensive, but not everything will have an important or measurable effect—the test can be thorough but pragmatic.
The five main tribotesting areas are:
1.) Materials. Solid bodies consist of bulk materials that generally have one or more surface layers. The bulk material properties, described in handbooks and references, vary with basic composition and the object’s processing history. Surface layers can include oxides, coatings, lubricants, adsorbed layers and contaminants.
Loose particles are characterized by their composition, hardness, size distribution, shape/angularity and, if they are in a slurry, concentration. Particles in a gas stream will have various properties, depending on their concentration, velocity and angle of impact.
2.) Contact geometry. The macroscopic geometry of the contacting surfaces (e.g., flat on flat, conformal, point contact) affects friction and wear. Smaller-scale factors include surface finish and surface roughness, bearing area, peak shape, valley volume and lay (directionality of marks). Edge conditions also can affect the friction and wear. To the extent possible, the test samples should be finished in the same manner as the real-life components.
3.) Contact stress. Contact stress can be elastic (Hertzian), characteristic of rolling contact or plastic, typical of sliding contact.
4.) Loading. Loading can be steady, increasing or decreasing, or it can vary. The load can be unidirectional (ball bearings) or oscillating (pendulum). Motion can be continuous or it can stop and start in a unidirectional or in a reciprocating fashion (changing direction with a dwell time between sliding events).
5.) Environment. The environment in which a tribosystem operates also affects performance. Is the system in a temperature-controlled shop or outdoors? What ranges of temperature, humidity and pressure will the system be subjected to? Will the sliding parts be immersed in water, an electrolyte, biological fluids or lubricant?
Let’s use a steel sample as an example. If we are testing abrasive wear, and the abradant’s hardness is near that of the heat-treated steel, then duplicating the heat treatment of the steel is important. However, if we are running in a fully hydrodynamic regime (where the parts are fully separated by a lubricant layer), then replicating the heat treatment is not as important as replicating the surface finish.
WEAR FUNDAMENTALS
The wear coefficient k is the volume of material removed per unit load and sliding distance in mm
3/N・m. Although it is mathematically possible to reduce this to mm
2/N or 1/kPa, these terms have no physical meaning, so it is best to keep the original units.
The wear coefficient, a constant that can be calculated or measured in a laboratory, can be used to predict component lifetimes providing the tribosystem does not change wear modes. Design parameters are the allowable volume lost and the load (stress). The component lifetime depends on sliding distance (D), wear volume (V) and load (L): D = V/(k•L).
Duty cycle and directionality can influence wear. For example, a start-stop operation—typical of a main engine crankshaft and journal bearings at startup and shutdown—is often much more damaging than continuous motion.
Unidirectional sliding is very different from reciprocating sliding. For example, during unidirectional sliding tests, ultra-high molecular weight polyethylene (UHMWPE) molecules align along the sliding direction, which protects against wear in this direction much better than in a cross-sliding situation. This material is often used for prosthetic implants where it experiences reciprocal sliding in several directions. Thus, a unidirectional sliding test may not give an accurate prediction of wear resistance in the actual component.
Single-point predictions in a wear calculation can under- or overestimate lifetimes by ignoring wear-in or break-in effects or incubation periods, so wear assessments must go on long enough to ensure steady state and give a true picture of the expected wear rate.
Example 1. Wheel on Rail (Train Wheel and Overhead Crane Wheel)
Example 2. Journal Bearing (Hydrodynamic and Boundary Conditions)
SOLVING A PRACTICAL PROBLEM
As a practical example, let’s consider a medical implant: a cervical vertebra replacement. These are generally made from an expensive CoCrMo alloy. Can we make this part from a less expensive alloy with a better surface finish and still get less than 0.5 mm material loss over our desired 30-year lifetime? (
See Figure 3.)
Figure 3. Example of a lifetime prediction: UHMWPE versus CoCrMo or AISI 316 SS alloy.
First let’s describe the tribosystem. The contacting surfaces are UHMWPE and CoCrMo alloy or AISI 316 stainless steel (316 SS). The contact geometry is a disk, 1 cm in diameter, and the contact is conformal (clamshell geometry). The sliding is multidirectional (cross-sliding), and we will assume 3-mm motion per cycle at a maximum speed of 5 mm/sec. If the implant undergoes 1,000 cycles each day, the total sliding distance is about 33 kilometers! In a human body, the implant is immersed in synovial fluid at body temperature.
The load, for the purposes of the test, is about 15-20 lbs. (66-88 N)—the weight of an adult human head. (The load may actually be double that because for stability the skull is pulled downward by muscles.) The contact stress is on the order of 1.2 kPa. Putting all that together gives us a required wear coefficient (k) of 2.7 x 10
–5 mm3/N•m, and there are materials that can achieve that.
Next we define the conditions of the tribotest. We will measure the wear on a 0.25-inch diameter UHMWPE pin versus a polished metal alloy plate with a surface roughness (R
a) of 1–4 μin. We’ll slide 25 mm per stroke but rotate +/–45 degrees eight times each cycle to approximate the 3-mm sliding distance in a real implant. The sliding speed will be 5 mm/ sec, with a contact stress of 1.2 kPa (load = 0.056 N). There will be a one-second pause each half-cycle. The parts will be immersed in a saline solution at 37 C, as a starting condition.
Can we calculate wear volume from the mass loss after less than 48 hours of wear? Under the conditions of our test, the sliding distance over 48 hours would be 720 m. For our desired wear coefficient, the wear volume of the polymer pin would be 0.00054 mm
3, and the mass change would be 4.5 x 10
–7 g (0.45 μg). This mass change is too small to measure using ordinary lab equipment. However, this corresponds to 17 μm in height loss for the pin, from which we can directly calculate the volume loss.
Once the experiment is completed and the data compiled, a designer would have several options depending on the wear results. One option would be to reduce the expected lifetime of the implant to match that of the best data obtained among the materials and surface finishes tested. Alternatively, a design change might lower the contact stress. Improving the surface finish or substituting other materials also could reduce the wear.
LOOK AT THE SYSTEM
It’s important to remember that friction and wear are not static numbers that you can look up in a reference manual. They depend on properties of the entire interacting system. Likewise, measuring friction and wear requires setting up a test system that replicates all of the significant factors of the real-life system (although some factors are not as significant as others).
Tribological tests must be designed to be relevant to the desired application.
REFERENCE
1.
Dowson, D. (1979),
History of tribology. London, England: Longman Publishing.
Nancy McGuire is a freelance writer based in Silver Spring, Md. You can contact her at nmcguire@wordchemist.com.