How Coatings and Surface Engineering are Shaping Tomorrow’s World
Debbie Sniderman, Contributing Editor | TLT Feature Article June 2016
Wind, automotive and aerospace will be the principle beneficiaries of today’s R&D
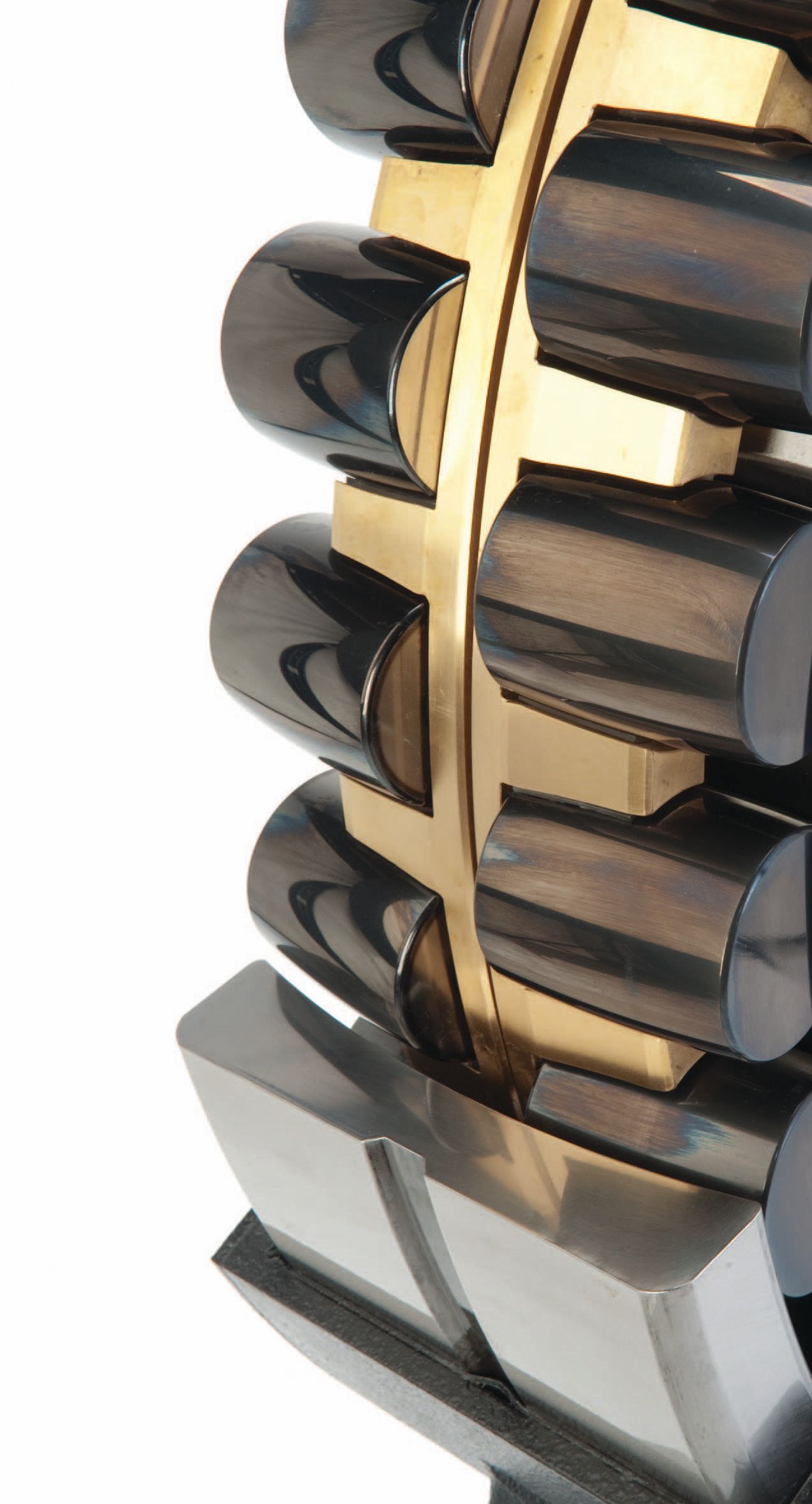
KEY CONCEPTS
•
Commercial need is driving research in surface coating technology with many successes.
•
The challenge for coatings manufacturers is achieving functionality at a lower price point.
•
The auto industry is using diamond-like carbon coatings in many applications.
The field of surface engineering has developed rapidly during the last few decades. Four commercial and academia experts from the materials R&D side of thin film coatings and surface texturing contributed to this discussion on recent commercial successes, how problems were solved as well as where their current and future research is taking them. Wind turbine and automotive applications topped the list.
RECENT INDUSTRIAL SUCCESSES
Ali Erdemir, Argonne Distinguished Fellow at Argonne National Laboratory (ANL) in Argonne, Ill., says the major recent successes for coatings are in the automotive field. Diamond-like carbon coatings (DLCs) can be made intensely hard, making them good at protecting against wear. They also can provide low friction when lubricants are or aren’t available on the surface. These results can’t be achieved with other coating systems.
Structurally, Erdemir explains DLCs could be mostly diamond-bonded (sp
3) or they could be highly graphitic-bonded (sp
2). It also is possible to make DLC contain a lot or no hydrogen. The degree of hydrogenation has a lot to do with surface interaction. Higher hydrogen has more free hydrogen termination in the surface, preventing chemical interactions with other species in the environment forming benign surfaces.
Hydrogen-free DLC surfaces are more reactive due to more dangling bonds looking for the right kinds of additives in oil to produce a slick surface with a low coefficient of friction. “Japanese car makers like Nissan are the largest users of hydrogen-free DLCs and have special oil formulations (i.e., organic friction modifiers) that promote surface reactivity and lower friction. They use it in all types of sliding or rotating surfaces in their engines— piston rings, liners, gearbox systems, transmission parts and clutches—and claim all together it improves fuel economy by 2%-3%,” says Erdemir.
There is a chapter in Erdemir’s book Coating Technology for Vehicle Applications covering DLCs meeting the needs of automotive manufacturers, and he says interest is increasing daily. In Germany, INA offers automotive parts coated with DLC by the millions. He says U.S.-based companies were sluggish to start but are now embracing DLCs for low-friction coatings.
As the viscosity of motor oil has decreased over the years bringing efficiency gains, more rolling, rotating and sliding parts become more in direct metal-to-metal contact. Less viscous oil doesn’t provide a hydrodynamic lifting effect to keep the surfaces separate. Instead, the fluid deforms and dissipates away, leaving surfaces subject to high friction, high wear and even promoting adhesion between them. Erdemir says one reason engine companies are very interested in using lowfriction coatings like DLCs is to circumvent the problems when using low-viscosity oils.
The other mechanism promoting use of DLCs is that the oil additives are changing constantly. “There are huge pressures on oil formulators to reduce the amount of effective antiwear additives like ZDDP for emission and environmental reasons. Reducing antiwear additives however makes rubbing surfaces more vulnerable to wear, and in these situations low-friction and high-wear coatings like DLCs are needed,” says Erdemir.
He continues, “Coatings in general are becoming a mainstream application in the automotive field for a broad range of applications, not only for engines but for accessories and forming dies, too.” They also are used in industrial metal forming and working, but the automotive field is the largest field for DLC coatings.
Large spherical rollers with and without DLC coating. These rollers are used in bearings that support the moveable roof of Miller Park in Milwaukee. (Roller image courtesy of the University of Akron.)
STLE-member Dr. Gary Doll, Timken professor of surface engineering and director of the Timken Engineered Surfaces Laboratories at the University of Akron in Akron, Ohio, agrees, saying there have been a significant advances made in engine coatings, both in the powertrain and valve train.
“Manufacturers now use different versions of DLCs on the valve train to reduce friction and wear,” says Doll. “Other than Nissan advancing that technology, almost every automotive producer coats fuel system injection components like plungers with some sort of DLC for wear resistance. The fuel injection systems on some technologies using fuels with high ethanol content or diesel won’t work and run without them, but most producers need coatings. Some companies still use titanium nitride, but not many.”
One gear and bearings combination DLC coating Doll worked on for a truck axle that used ultra-low viscosity oil achieved more than 50% efficiency improvement. While racing teams in NASCAR have been coating valve trains for a while for wear resistance, a recent success was to use DLCs on the lifters on engines that run higher than 10,000 rpm that use steel billet cams without welds. When they switched to weldless cam shafts, wear became a big issue for cam loads on the shaft. Now, Doll says, there are many commercial suppliers of DLC-coated lifters for NASCAR.
DLC coatings also are used for durability and longevity on 9-inch ring and pinion systems, and they also provide some friction reduction as well. Doll says a few teams even use coatings on wheel bearings.
According to Dr. Stephen Johnson, Timken director of research and development at the Timken Co. in North Canton, Ohio, “Increasingly now, It’s all about the surface. The primary failure mode for components has moved to the surface from traditional material-based modes, such as nonmetallic inclusions that would become stress risers. It’s less about what’s going on subsurface and more about what happens on the surface now. In the past, functional components, such as bearing and gear systems manufactured from similar materials running in close contact used a lubricant layer to keep surfaces separated. Increasingly that is no longer possible for many reasons. Adhesive and abrasive wear at the surface are the new primary modes of failures. That is where the coating story comes into play,” he says.
The Timken Co. has developed thin film, hard, metal carbide-doped DLC coatings that fundamentally don’t like to stick to steel. Johnson says that’s the advantage. Benign surfaces of dissimilar materials in close contact fundamentally break the adhesive wear mechanism and offer substantial advantages in performance.
Johnson says the aerospace industry is increasingly interested in embracing coating technologies. There has been recent commercial success and Timken has intellectual property on a bearing coating that improves wear behavior and it says provides a level of oil-out protection never achieved before.
“This is increasingly important, because in the drive toward improved efficiency in all types of machines, many aspects of powertrain and drivetrain are now under the microscope to see where there are parasitic losses (e.g., reducing drag and churning losses caused by the lubricants). In many cases, bearings share the same lubricants as gears in a transmission. With reduced viscosity lubricants, thick separation layers aren’t possible. We have to accept now that increasingly more gears and bearings have to survive in boundary lubrication regimes where direct surface interaction is unavoidable. This is where coatings come into play,” says Johnson.
The Timken Co.’s most publicized commercial coating success has helped solve multiple problems in wind energy generation. Turbines are designed to last more than 20 years and typically the bearings inside modular turbines were not designed to be routinely replaced. Many are failing after three or four years, which is a large concern since there are more than 10,000 of one particularly challenged 1.5 megawatt design in the U.S. alone.
The 2013 Wind Turbine Technology and Test Center built by Timken and Stark State College. Ultra-large bearing system tests and harsh operating conditions similar to those found in large multi-megawatt wind turbines are simulated at this $14 million center, the first of its kind in the Americas. (Image courtesy of the Timken Co.)
Bearings inside modular wind turbines have to be capable of surviving very high dynamic loads while also being relatively lightly loaded most of the time in an environment, which is inclined to produce high amounts of slip between the rolling elements and the bearing rings. In some designs, Timken’s competitors used spherical roller bearings due to the perceived need to accommodate large amounts of shaft misalignment. However, spherical roller bearings are prone to slip due to the nature of their design geometry. When coupled with the dynamic environment of a modular wind turbine, excessive slip occurs and the bearings exhibit micro-pitting and other types of early failures due to surface distress.
Timken developed a coating for the roller bearings that broke the wear mechanism. Since the turbine design was not changed, the slip is still present, but now the system can tolerate the level of slip. The wear-resistant bearing has surpassed the life expectancy of the uncoated bearing and is now an aftermarket item that Timken is offering to OEMs (
see Figure 1). “Will the bearings get to the 20-year life expectancy of the overall machine? That still will be seen, but there definitely is value there,” Johnson says.
Figure 1. Wear-resistant bearings for wind energy applications reduce life-limiting wear problems including micropitting on main shaft spherical roller bearings and micropitting, smearing and brittle flaking on wind turbine gearbox bearings. They also provide up to 3.5 times greater L10 life for main-shaft and gearbox bearings. (Figure courtesy of the Timken Co.)
While coatings reduce friction and wear by adding material to a surface, laser surface texturing (LST) is like an “inverse coating”—the same results can be obtained by removing material from the surface. It produces micro-dimples by ablation. STLE Life Member Izhak Etsion, Professor Emeritus at Technion Israel Institute of Technology, says anything that suffers from friction and wear, any material, can be ablated by a laser beam. Surface texturing works best in parallel sliding applications and not as well but still may help when the mating surfaces are non-conformal.
Cutaway view of a flexpin tapered roller bearing design for planetary positions in wind turbine gearboxes. (Image courtesy of the Timken Co.)
According to Etsion, although LST has existed since the mid-1990s and there have been hundreds of publications on the topic, it has not yet been commercialized. “There is clear proof as seen in the many publications that LST is beneficial for reducing friction and wear, and many mechanical components can benefit from it,” he says.
“Even though end-users loved it because it prolonged the life of mechanical components by a factor of three on average, I was surprised to encounter resistance from large manufacturers that did not want the technology to spread,” Etsion says. “Hopefully, with time and pressure from the end-users it will become more widespread.”
CURRENT RESEARCH AND THE SOLUTIONS TO COME
At the Timken Engineered Surfaces Laboratories at the University of Akron, Doll is involved in a number of areas of coatings research with varying degrees of success. He says the wind turbine application is the area where new coatings have had the most success. Tapered and spherical steel roller bearings in turbine gear boxes and main shafts were exhibiting micropitting wear. He says new DLCs solved these problems.
Micrograph of DLC coating consisting of nanometer-sized precipitates of metal carbide and an amorphous hydrocarbon matrix. (Image courtesy of the University of Akron.)
DLC coatings also have made their way into the aerospace industry, for rotorcraft oil-out protection. When applied to bearing or gears, it gives a considerably longer amount of time the aircraft can fly if it loses oil. Doll’s laboratory worked on new coatings for a new turbine engine’s geared turbo- fan and special bearings that were never used in aircraft before. The coating enabled bearings to withstand full throttle during an oil-out condition. It has completed prototyping and is in a test production line.
Doll says DLCs are so prevalent because they are one of the few coatings that can be deposited at temperatures compatible with heat-treated carbon steel less than 180 C. “For many years, DLCs were the only family of coatings that gave good tribological performance without damaging the steel or degrading its properties. That’s no longer the case,” he says.
Doll also is excited about new dichalcogenide coatings like molybdenum disulfide. He says other materials can be added to them and their durability and longevity can be improved by removing their crystallinity. “They are outperformed in everything else in automotive steel cutting applications. And they surprised us by the wear-inhibiting and life-increasing performance gains they can impart to ball bearings,” he says.
Doll’s group has had success developing a new thermal diffusion-type coating processes for applying tantalum and vanadium carbide coatings. These surface treatments reduce wear and provide corrosion resistance for collaborators in the oil and gas industry.
He also is working on coatings for medical imaging systems, such as special coatings for ball bearings used in MRI systems that reduce the amount of vibration the patient hears and the amount of time the patient has to stay inside. Typical ball bearings in x-ray tubes are coated with silver by vacuum or solution processing. During application this silver can transfer to the raceway in clumps, forming a mogul-like surface, which causes enough vibration to dither and destabilize the electron beam and fluctuate the x-rays that come out. If the new coating transfers to the raceway, it doesn’t clump, producing a smoother surface without vibrations.
Doll’s other research is helping replace steel alloys with titanium alloys. “While titanium 6-4 has a good strength-to-weight ratio, it may be the world’s worst tribological material since it forms bonds with just about everything. We’re working to develop new duplex surface treatments involving nitriding and coatings that impart better wear resistance to Ti 6-4. With these we hope to achieve equivalent or better wear resistance than what steel provides. This new surface treatment has only been implemented in firearms so far, but automotive, biomedical and aerospace industries can also benefit,” he says.
At ANL Erdemir is designing and producing much better and higher-performing coatings that will meet the needs of next generation engines. He uses nanocomposites designed to not only have extra wear resistance but also heat dissipation capacity and higher reactivity toward some oil additives, much higher than what is normally seen on steel surfaces. “We are working on more intelligent coatings that can react with even the least amount of antiwear and friction additives in oil, which makes oil formulators nervous. They think if these agents are removed, the oil will become less effective and won’t last as long. We are demonstrating that coated surfaces still provide what’s needed in terms of friction and wear, not only to serve the purpose but to last the lifetime of an engine,” says Erdemir.
ANL’s nanocomposite coatings are very thin, no more than 2um-5um thick. The challenge is to design coatings that last the projected lifetime of engines that last a few hundred thousand miles. Erdemir says sophisticated coating systems using nanocomposite architectures last three to four times longer than other coatings like chromium nitride when exposed to extreme engine conditions.
Etsion says that current requests for laser texturing comes from end-users of mechanical components in a variety of industries who believe they can benefit from it and are interested in prolonging the life of their components, not the product manufacturers themselves. Much of his current work involves consulting to end-users to see if they can use laser texturing by themselves so they don’t have to depend on a company that commercializes it.
In addition to working on surface texturing at the Technion, Etsion is researching optimization of the thickness of coatings. After asking many hard surface coating users how they chose the thickness of their coatings, he found that almost always it was by trial and error. He is investigating if there is a way to theoretically study the contact mechanics of coated surfaces to see if, as with surface texturing based on application, there is an optimum thickness that minimizes friction and wear.
Spherical roller bearing with DLC coating on rollers and tapered roller bearing with uncoated rollers. (Image courtesy of the Timken Co.)
“We’re developing universal basic models that may be extended to complicated configurations and be validated by experiments. The dimensionless results are good for any type of substrate or coating material and will work with almost any coated component in dry contact with relative sliding. We are starting to see good chances that there is an optimum thickness. Trial and error isn’t needed. The problem can first be dealt with theoretically and then proven by lab testing,” Etsion says.
He continues, “The models show there’s an optimal thickness for getting the best resistance to plastic yield inception. We’ll soon start modeling how the friction coefficient is affected by the thickness. Lab tests show there is indeed an optimum coating thickness with sliding contacts. When hard coatings on soft substrates are too thin, there is a weakening effect, so it’s better not to apply it at all.” He believes this work will eventually help many industries prolong the life of their tools by reducing wear.
Johnson says the main challenge for the industry is developing coatings with the level of performance of metal carbide DLCs at lower cost. Metal consumables of high enough purity are expensive and limit what can be done with coatings from plasma-based systems because of the value proposition. Research is taking The Timken Co. toward creating coatings with similar chemistries and performance at a different price point using techniques other than plasma deposition systems.
10-YEAR FUTURE OF COATINGS
In the future, coatings will continue to flourish. They will provide greater synergy between lubricants and surfaces. Currently various lubricant formulations are tested on surfaces to check compatibility and performance. Doll says with the development of new coatings, the functionality of lubricant additives will change.
For example, coated automotive products may reduce or remove the need for antiwear and extreme pressure additives in motor oil or at least call them into question. Future coatings will raise questions about finding less toxic or better solutions to changing motor oil in a car.
Doll says coatings also will help satisfy the power density argument. Current coatings have allowed components such as gears, bearings and lifters to carry more load and have the same or greater life while higher amounts of power are put through them. The industry has been putting more power into the same size components. But Doll says there will be opportunities in the future to keep the power the same while reducing the size. “We haven’t seen the size side of that coin yet for mechanical components. Keeping the power the same but reducing the size. But the future will hold this,” he says.
Another area Doll believes coatings will skyrocket is in the biomedical area. “Although now there are very few coatings approved by the FDA for use in the U.S., they are being used in other parts of the world. Eventually a company will take on the burden of becoming the first to obtain approval, and then we’ll see an explosion of work in this area,” he says. “There have already been high-profile legal cases involving all-metal joints in prosthetics, which have failed or caused issues. Surface treatments like the ones we have developed for titanium materials might help the industry if it had FDA approval.”
Creating wear-resistant surfaces that also are highly corrosion resistant is another dimension in which coatings will evolve. In the past, materials like nickel phosphate, cadmium and chromium offered excellent corrosion resistance, but they weren’t wear resistant. Steel landing gear in the aircraft industry used cadmium plating to inhibit stress corrosion cracking. But erosion due to rain meant it had to be reapplied, and cadmium plating is being regulated away. “There needs to be a better solution that offers both properties. This is one direction where our work is headed,” Doll says.
Engine and transportation applications need low friction and highly wear-resistant surfaces, and the demands from sliding parts on higher power density designs on the materials side will be much higher. Erdemir says, “In the next 10 years, the engine market will double in size in terms of expenditures and value to the customer. I wouldn’t be surprised if coatings continued to be better, beyond DLC, as the need for higher performance will be there.”
Erdemir agrees that the trend for engineered surfaces to combat friction as well as wear will continue. Combining advanced coatings with surface treatments, whether it’s texturing or duplex treatments, may provide the best kind of support for auxiliary components like cam shafts or those used in high impact applications like gears and bearings.
“Combining multiple surface approaches together to achieve highly multi-functionalized surfaces may deliver what one technology doesn’t. Hybridization in an intelligent manner will meet the needs of the next generation mechanical systems as demands for higher performance, more compact and higher power density systems continue,” says Erdemir.
Typical magnetron sputtering system used for the deposition of tribological coatings. (Image courtesy of Argonne National Laboratory.)
Etsion says, “The range of applications that could benefit from using LST is tremendous. It’s almost impossible that it will remain a curiosity. The same reactions occurred with coatings when they were first introduced to the market. Pressure from end-users forced them to become used. I hope the same thing happens with surface texturing. They prolong the life of mechanical pump seals by factors of three to 10. It’s hard to believe the resistance of big manufacturers will last too long.”
The trend is clear. The world needs increasing efficiency to be sustainable. Johnson says in time, coatings will play more important roles in the continuous drive toward more efficient machinery and the coatings market will grow to solve the problem of being a cost effective method. The challenge for coatings now is learning how to achieve the same functionality at a lower price point to make them more available than they are today,” he says.
Doll agrees. “Everyone asks if there is a way that coatings can be less expensive to apply,” he says. “The search for equivalent or better performance at a fraction of the cost is not an easy problem. But future coatings will see price reductions. Not one company hasn’t asked me for that,” he says.
Almost all cutting tools now have coatings to enhance performance. Coatings will begin to significantly impact new industries such as durable brass physical vapor deposition coatings; decorative coatings that improve the look, feel and longevity on new devices; razor blades; watches; and plastic automobile components.
Aside from solving the general problem of reducing friction and parasitic losses, in the upcoming decade Johnson predicts that new worlds of intelligent devices will become available as coatings become smarter. “Embedded metal carbides give wear characteristics. But future coatings could tell you something about the environment it is in, the load and the temperature it sees, creating dramatic and tremendous opportunities for improvements. Internet of Things (IoT) is a buzzword now, but coatings with embedded sensors will allow new devices to be even more intelligent and higher performing,” he says.
FOR MORE INFORMATION
The University of Akron:
www.uakron.edu
Coating Technology for Vehicle Applications:
www.springer.com/us/book/9783319147703
Argonne National Laboratory:
www.anl.gov
Technion Israel Institute of Technology:
www.technion.ac.il/en
The Timken Co.:
www.timken.com
Debbie Sniderman is an engineer and CEO of VI Ventures, LLC, an engineering consulting company. You can reach her at info@vivllc.com.