Industry Report: The Ongoing Challenges of GHS Compliance
Jeanna Van Rensselar, Senior Feature Writer | TLT Feature Article May 2016
As deadlines come and go, disharmonies persist.
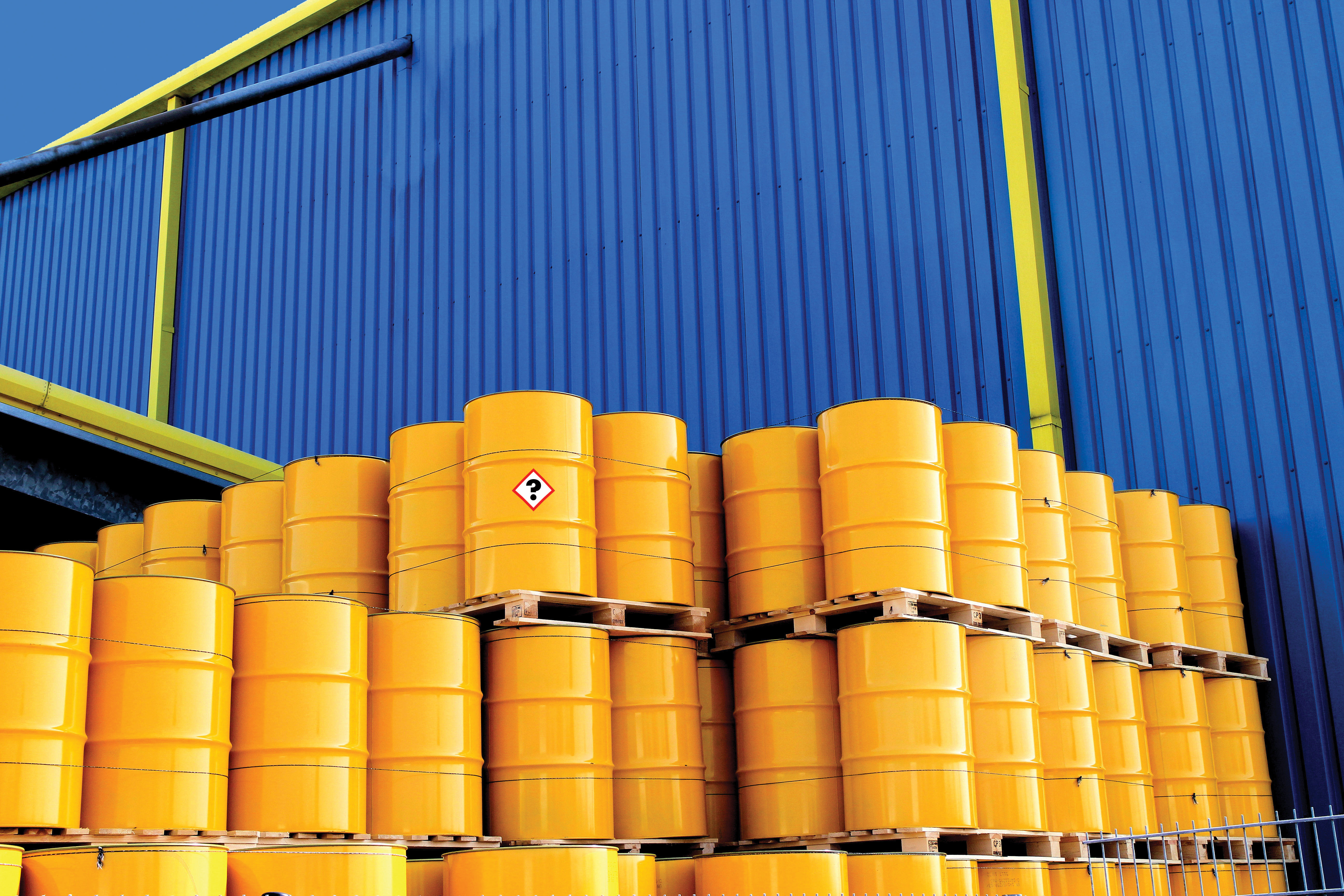
© Can Stock Photo Inc. / aremac
KEY CONCEPTS
•
The issue of disclosing proprietary information to comply is still not resolved in the U.S., but other countries, notably Canada, have developed a workaround.
•
Accurately identifying the hazards of reactive compounds is tricky—especially for greases.
•
While most countries’ GHS compliance deadlines have already passed, many organizations say they still are non-compliant due to circumstances they don’t control.
ALTHOUGH A KEY OBJECTIVE OF THE GLOBALLY HARMONIZED SYSTEM of Classification and Labeling of Chemicals (GHS) is to unify hazard communications, entities have modified and implemented GHS principles differently (
see GHS Bridging Principles). Several elements of the GHS also are subject to scientific interpretation. It is not uncommon for a chemical to be classified differently across organizations and even within a single organization across countries.
GHS BRIDGING PRINCIPLES (1)
The following six GHS bridging principles are used to classify untested mixtures:
•
Dilution. Tested mixture A is diluted with less or equally hazardous ingredient B: A+B=A.
•
Batching. Mixtures A and B are two batches produced under the same conditions: A=B.
•
Concentration of highly hazardous mixtures. Mixture A is classified at its highest hazard category; B is more concentrated than A: B=A.
•
Interpolation. Mixture A and B share the same hazardous ingredient and classification; if the concentration of the hazardous ingredient in mixture C is in the same range as A and B, then C=A=B.
•
Substantially similar mixtures. For two mixtures A+B and C+B, if A is similar to C in concentration and hazard data and B’s concentration is similar in two mixtures: A+B=C+B.
• Substantially similar
mixtures. For two mixtures A+B and C+B, if A is similar to C in concentration and hazard data and B’s concentration is similar in two mixtures: A+B=C+B.
•
Aerosol. A mixture in aerosol form is considered to have the same classification as the non-aerosol form of a mixture provided that the propellant does not affect the hazards of the mixture.
The sheer complexity and expense of consistently communicating hazards to workers and consumers, while at the same time protecting confidential business information, can be daunting. Also daunting is the changing liability landscape in terms of regulatory enforcement, litigation prevention and commercial harm that the GHS engendered.
Then there are the issues of greases containing reactive compounds and requirements (in some cases) to disclose trade secrets.
Although most compliance deadlines have come and gone, many raw chemical manufacturers and distributors still have not updated their documents and labels (
see Label Elements). This creates problems for downstream partners who cannot complete their own documents and labels without that raw material data.
LABEL ELEMENTS
The GHS specifies hazard communications that need to be on the label—what signal word, pictogram and hazard statement should be used—and that they should be located together. The standardized label elements included in the GHS are:
•
Symbols (GHS hazard pictograms). These convey health, physical and environmental hazard information assigned to a GHS hazard class and category.
•
Signal words. Danger and warning are used to emphasize hazards and indicate the severity level. Only one signal word corresponding to the class of the most severe hazard should be used on a label.
•
Hazard statements. These are standard phrases assigned to a hazard class and category that describe the nature of the hazard. For products with more than one hazard, a statement for each GHS hazard should be included on the label.
Additional label elements included in the GHS are:
•
Precautionary statements. These are measures to minimize or prevent adverse effects. They cover prevention, response in the case of accidental spillage or exposure, storage and disposal.
•
Product identifier (ingredient disclosure). This includes the name or number used for a hazardous product on a label or in the SDS. For mixtures, the label should include the chemical identities of all ingredients that contribute to any one of the 12 GHS articulated health hazards when these hazards appear on the label.
•
Supplier identification. This includes name, address and telephone number.
•
Supplemental information. This is information that is not required or specified under the GHS. Supplemental information may be used to provide further detail as long as it does not cast doubt on the validity of the standardized hazard information.
CLASSIFICATIONS AND DEFINITIONS: A SYSTEM
Dr. Allan Jemi-Alade, environment, health and safety (EHS) technical advisor for Afton Chemical Corp. in Richmond, Va., and most others see the intrinsic value of a unified system. “A common set of pictograms, hazard statements and precautionary statements that are widely used internationally should help downstream users quickly recognize the hazards of the materials that they are using and ensure their ability to handle these chemicals safely,” he says.
The GHS was first developed at the United Nations Rio Conference in 1992 and adopted by the UN in 2003. Its intention is to serve as one universal standard for all countries, replacing diverse classification systems across governing bodies. Compliance is not compulsory under UN law.
The GHS includes criteria for the classification of health, physical and environmental hazards. It also specifies information that should be included on hazardous chemical labels and safety data sheets (SDS) (
see Figure 1).
Figure 1. Pictograms of new GHS warning labels.
The system provides the tools to institute a hazard classification and communication standard, which many economically disadvantaged countries—often those most vulnerable to hazardous chemicals—would not be financially capable of developing and enforcing themselves.
Beyond just clarifying chemical hazards, the GHS aims to further the awareness of chemical health hazards and encourage the eventual elimination of carcinogens, mutagens and reprotoxins (
2). To that end, the GHS created categories and common definitions that can be uniformly applied across all governing entities.
Hazard classification. In the GHS classification system, substances are assigned to one or more of the following 17 hazard classes (
3):
1.
Explosives
2.
Flammable gases
3.
Aerosols
4.
Oxidizing gases
5.
Gases under pressure
6.
Flammable liquids
7.
Flammable solids
8.
Self-reactive substances
9.
Pyrophoric liquids
10.
Pyrophoric solids
11.
Self-heating substances
12.
Substances which, in contact with water, emit flammable gases
13.
Oxidizing liquids
14.
Oxidizing solids
15.
Organic peroxides
16.
Corrosives to metal
17.
Desensitized explosives (added in GHS Rev. 6).
GHS health hazard definitions. The GHS also defines the following 12 health hazards that can be manifested in those exposed to hazardous chemicals:
1.
Acute toxicity
2.
Skin corrosion
3.
Skin irritation
4.
Serious eye damage
5.
Eye irritation
6.
Respiratory sensitizer (inhalation induces airway hypersensitivity)
7.
Skin sensitizer
8.
Germ cell mutagenicity (leads to increased occurrence of mutations in cells and/or organisms)
9.
Carcinogenicity
10.
Reproductive toxicity
11.
Specific target organ toxicity: Single and repeated exposure (all significant health effects not included in the GHS that can impair function—both reversible and irreversible, immediate and/or delayed)
12.
Aspiration hazard.
Environmental hazards. The GHS also categorizes the following two types of aquatic environmental hazards:
•
Acute aquatic toxicity. A material that causes injury to an aquatic organism after a short-term exposure.
•
Chronic aquatic toxicity. A material that causes adverse effects to aquatic organisms during exposures considered long (relative to the organism’s lifecycle).
ISSUES WITH GHS SAFETY DATA SHEETS
There are four primary issues with SDSs:
1.
The classification of mixtures
2.
The thorough identification of hazards
3.
Timely compliance
4.
Confidentiality and trade secrets.
SDSs for mixtures. Of particular interest to lubricant formulators is the way the GHS classifies mixtures. The GHS uses a tiered approach that depends on the amount of information available for the mixture and its individual components. The principles were derived from existing systems and are based on the following criteria:
1.
Where toxic or eco-toxic test data are available for the mixture, the classification of the mixture is based on that data.
2.
Where test data are not available for the mixture itself, then GHS bridging principles that use test data for components and/or similar mixtures should be applied.
3.
If test data are not available for the mixture itself and the bridging principles cannot be applied, then the mixture should be classified using cutoff values described in the specific endpoint.
Identifying hazards. “As an EHS technical advisor within the organization, one of the major challenges my team faces is determining accurate hazard classifications,” Jemi-Alade says. “Many additive-package formulations can contain anywhere from two to over 50 chemical substances.”
The hazard classification for each formulation is derived either from calculations using the hazards of each substance (calculation approach) or testing the formulation itself (testing approach).
According to Jemi-Alade, while the testing approach is the most accurate method, the calculation approach is preferable. However, the calculation approach relies on having accurate hazard classifications for each of the ingredients. There is not one specific source for hazard classifications—variations in hazard classification for a substance often differ from one supplier to another. This differentiation can be as simple as one raw material having different impurities than another.
Jemi-Alade explains that European Union (EU) authorities have tried to encourage convergence and agreement on hazard classifications of substances, and have made certain useful sources of information available such as:
•
Annex VI to the CLP Regulation
•
REACH registration dossiers on more than 13,000 substances
•
The Classification & Labeling Inventory.
“However, much discernment needs to be made in using these sources,” Jemi-Alade says. “One example is the common chemical, acetone. The Classification & Labeling Inventory lists more than 70 different hazard classifications for this substance. As such, additive manufacturers and suppliers would still need to expend significant effort reviewing ingredient hazard classifications and the underlying toxicological and eco-toxicological data supporting them. So relying on the inventory list would not be the only step necessary for classification.”
Raw material suppliers and SDSs. Many chemical manufacturers are still missing important GHS deadlines (
see Country-by-Country Implementation Deadlines). Because this had been and continues to be an issue, on Feb. 9, 2015, OSHA’s director of enforcement programs, Thomas Galassi, issued a memorandum advising regional administrators and their inspectors to take into account the overall effort, attention and action that chemical blenders are taking to comply with deadlines. In the memo, Galassi sets the tone with phrases such as “circumstances beyond their control” and “reasonable diligence.”
U.S. Army engineers inspecting GHS-labeled drums.
COUNTRY-BY-COUNTRY IMPLEMENTATION DEADLINES (4)
Following are the GHS adoption dates in alphabetical order by country (there is no set international implementation schedule):
•
Australia. In 2012 it adopted regulations for GHS implementation, setting Jan. 1, 2017, as the GHS implementation deadline.
•
Brazil. It established an implementation deadline of February 2011 for substances and June 2015 for mixtures.
•
Canada. Canada’s new GHS regulation came into force on May 31, 2015, with implementation by most sectors required by June 1, 2017.
•
China. It established the GHS implementation deadline of Dec. 1, 2011.
•
European Union. It published regulations for GHS implementation on Dec. 31, 2008. The deadline for substance classification was Dec.1, 2010. For mixtures, the deadline for implementation was June 1, 2015.
•
Japan. It established the GHS implementation deadline of Dec. 31, 2010, for products containing one of 640 designated substances.
•
Korea. It established the GHS implementation deadline of July 1, 2013.
•
Malaysia. The deadline for substances and mixtures was April 17, 2015. Malaysia published its Industry Code of Practice on Chemicals Classification and Hazard Communication on April 16, 2014.
•
Philippines. It issued Guidelines for the Implementation of GHS within the Chemical Safety Program in the Workplace in 2014. The deadline for substances and mixtures was March 14, 2015.
•
Taiwan. Full GHS implementation is scheduled in 2016 for all hazardous chemicals with physical and health hazards in the workplace.
•
Thailand. The deadline for substances was March 13, 2013. The deadline for mixtures is March 13, 2017.
•
Turkey. It published Turkish CLP regulation and SDS regulation in 2013 and 2014 respectively. The deadline for substance classification was June 1, 2015. For mixtures, the deadline for implementation is June 1, 2016.
•
U.S. Published the final rule for implementation of GHS on March 26, 2012. It required product manufacturers to adopt the standard by June 1, 2015, and product distributors to adopt the standard by Dec. 1, 2015. Workers had to be trained by Dec. 1, 2013. All employers that use, handle or store hazardous chemicals must update alternative workplace labeling and hazard communication programs, as necessary, and provide additional employee training for newly identified physical or health hazards by June 1, 2016.
•
Vietnam. The deadline for substances was March 30, 2014. The deadline for mixtures was March 30, 2016.
In order to determine the good faith effort that tardy chemical blenders are making to comply, the memo directs OSHA inspectors to review documented communications between raw material suppliers and blenders (
see Five Tips for Making a Smooth Transition from MSDSs to SDSs). To avoid a citation, non-compliant manufacturers and distributors need to let the OSHA inspector know when they plan to comply. What the memo does not do is extend the deadline (
5).
FIVE TIPS FOR MAKING A SMOOTH TRANSITION FROM MSDSs TO SDSs
Even though some deadlines have come and gone, most organizations are still dealing with the transition from material safety data sheets (MSDS) to safety data sheets (SDS). Following are tips for getting that done.
1.
Perform a physical inventory of hazardous chemicals.
2.
Make sure to include the most up-to-date SDS for every chemical on the list.
3.
Consider software. Many companies are turning to electronic management of SDSs to help them control the influx and multiple versions of MSDSs they need to process.
3. Consider software. Many companies are turning to electronic management
of SDSs to help them control the influx and
multiple versions of MSDSs they need to process.
4.
Carefully review every safety data sheet in order to determine if there are new hazards that require employee training.
5.
Discuss with suppliers their plans to update to the GHS format and apply pressure if necessary.
SDSs and confidentiality/trade secrets. Jemi-Alade says, “Confidentiality is an important issue to all additive manufacturers. While additive manufacturers understand the necessity of the hazard information being conveyed to customers and the necessity of downstream users being open and transparent, these companies also have the need to safeguard their formulations.”
Some authorities (like the EU and Canada) have made it relatively easy to secure protection for trade secret substances by requiring that companies only disclose the exact chemical identities of potentially hazardous ingredients to the regulatory authorities in order to get approval to use generic or alternate chemical names on their SDSs.
In Canada, when a supplier or employer wants to be exempt from having to disclose confidential business information (CBI), such as the chemical identity of one or more trade secret hazardous ingredients, it must file a claim for exemption with Health Canada. Once the application is reviewed and approved, Health Canada assigns it a registry number. That number must be included on the SDSs and, in some instances, on the label, in order for that product to be sold on the Canadian market or imported into Canada without disclosure of the CBI.
“However, these protections are not global,” Jemi-Alade says. “Therefore securing confidentiality agreements with customers and downstream users that require more specific information for their environment, health and safety needs also can ensure confidentiality and the best protection for the additive manufacturer.”
PREPARING SDSs FOR LUBRICATING GREASES
According to Paula Laux, senior regulatory specialist, and Karen E. Lintz, regulatory affairs director for Information & Insights, The Wercs, a division of UL, in Latham, N.Y., preparing SDSs for lubricating greases comes with its own set of issues (
6).
“Lubricating greases as a class of compounds can be diverse and as such can have varying hazards,” they say. “While many of the synthetic greases can have low levels of toxicity, the mineral base lubricants, which are identified by Chemical Abstract Services (CAS) numbers, can contain substances of unknown or variable composition, which may themselves be regulated as carcinogens or reproductive toxins. The challenge is that, depending on how refined the mineral oil is, an SDS for the same chemical identified by the same CAS number can result in different SDSs.”
They add that since lubricating greases come in various delivery systems, different physical hazards may be present. For instance, aerosol-dispensed lubricants can pose a flammable hazard. This means an SDS for the lubricant itself might differ from an SDS prepared for the end (aerosolized) product as delivered to the customer.
Aspiration hazards as part of OSHA’s Hazard Communication Standard (HCS, 2012) pose another challenge (
7). Chemical aspiration may cause chemical pneumonia with long-term complications such as persistent cough, shortness of breath, increased risk of further respiratory illness and progressive illness leading to death.
“Unless there is appropriate human evidence to classify the lubricant, a kinematic viscosity measurement at body temperature might be necessary to classify the lubricant correctly,” they say. “Existing data for viscosity are usually only available at standard temperatures and might not be useful in making the classification.”
For example, STLE-member and TLT technical editor Dr. Anoop Kumar, director of R&D and business development for Royal Mfg Co. LP, in Tulsa, Okla., explains that in making soap-based greases, lithium, sodium, calcium, etc., their hydroxides are reacted with long-chain fatty acids. Where these metal hydroxides have potential health hazards, however, the fully reacted thickener with the proper stoichiometric ratio is either neutral or very slightly alkaline—indicating that an alkali was reacted.
He says, “For the resultant product, as in the case of lithium 12 hydroxystearate for lithium grease, whose toxicity information is not fully available and information on side reactions not well understood, it becomes very difficult to justify the SDS information. Because of this, there is much confusion in the grease industry regarding what to put and what not to put on an SDS. In another case, polyurea greases where isocyanates and amines (which have known toxicity) are used to make these greases, the toxicity information on the finished thickener is not well understood and that leads to confusion.”
© Can Stock Photo Inc. / mary981
Kumar summarizes that, in the majority of cases, grease preparation involves a chemical reaction in order to form a new product. The toxicity information of the resultant product is either not known or is very limited. “This makes it more complicated to get the right information for greases,” he says.
On the other hand, he points out that it is very challenging to protect the confidentiality of the formulation if the information is fully disclosed. “Anybody who is skillful with chemical formulations can figure out at least some details for duplicating the product,” he says.
SOFTWARE
There are a number of SDS preparation software options. One of these is UL’s The WERCS Studio software, and the online do-it-yourself ULGHS.com service, which helps users prepare SDSs by generating consistent and reproducible results using preloaded classifications, formulations, physical properties, available data points and logic.
“Depending on the system used, software allows for SDSs to meet the country-specific requirements and manages the differences between regulations through automation,” Laux and Lintz say. “Some software packages also may aid in SDS management by providing the ability to make wholesale updates if the classification changes for a given substance, automate SDS distribution and tracking and manage professionally translated phrases so that SDSs can be provided in the appropriate languages.”
Since OSHA does not provide a base list of classifications, software users need to provide self-classifications where valid classifications from other regulatory sources do not exist. Another consideration is that European classifications might not be acceptable in the U.S.
COMPARING U.S. COMPLIANT SDSs WITH OTHER COUNTRIES
Although the GHS has unified the hazard identification and communication foundation, many differences in how individual countries have adopted the regulations exist. There is no single SDS that can concurrently comply with all the country-specific regulations and still effectively communicate the true hazards of the chemical.
Laux and Lintz explain, “If one only compares the format of the SDS, the differences are subtle and in fact barely noticeable except for country-specific information such as occupational exposure limits or whether a given substance within a product is listed as carcinogenic by IARC or NTP (
8).”
They continue, “The U.S. compliant SDS has 16 sections just like all other GHS-style SDSs but is unique in that certain sections are deemed unenforceable by OSHA. This means that while Sections 12-15 must appear on the SDS, and while there are suggestions as to the content of those sections, the content is non-mandatory. The information covered in these sections may be important for the user of the chemical product, however. The content in those sections is governed by other U.S. agencies such as the EPA and DOT (
9).”
According to Laux and Lintz, the most notable differences between U.S. compliant SDSs and those from other countries occur at the substance or mixture classification level, with the biggest difference being that the U.S. uses different threshold levels for classification.
“For example, reproductive toxin categories 1 and 2 are required to be disclosed and classified when they are present in a mixture at 0.1% or greater, rather than the 1% or greater threshold required in
most other countries,” they explain. “These noted threshold differences also exist for skin sensitizers, carcinogens categorized as category 2 and specific target organ toxicity for both single (STOT-SE) and repeated exposure (STOT-RE). Canada and Brazil are two exceptions as these countries adopted the same threshold limits as the U.S. in their GHS implementation.”
Another difference they cite is that the U.S. requires classification of combustible dusts, asphyxiants, pyrophoric gases and hazards not otherwise classified (HNOC). HNOC includes anything that may cause an adverse physical or health reaction that does not meet the specified criteria for the physical and health hazard classes addressed. These additional OSHA-adopted classifications are not currently defined by the UN GHS guidelines. An example Laux and Lintz give is that a powdered, organic chemical that has the potential to explode when mixed with air must carry an additional classification in the U.S.
So is a universal SDS even possible? Jemi-Alade says maybe: “The main challenge in preparing a universal SDS is laying out the information in such a way so as not to confuse SDS users but at the same time ensuring compliance with the regulatory requirements of each country/region. The success of a universal SDS would rely a lot on the goodwill of regulatory authorities.”
The answer to this lack of uniformity, according to Laux and Lintz, is software solutions that provide cost-effective and efficient means of providing compliant SDSs for global GHS requirements.
CONCLUSION
No one argues that the GHS was necessary and is, for the most part, working The bugs that still need to be worked out, such as downstream compliance and uniform adoption, are relatively minor considering the potential that the GHS has for improving worker safety and protecting the environment equally in every country.
Jemi-Alade concludes, “Training downstream users to find and interpret information within one harmonized 16-section format, GHS SDSs would undoubtedly be beneficial for anyone handling chemicals in the global lubricants industry, likely leading to fewer accidents and incidents.”
REFERENCES
1.
Available
here.
2.
Reprotoxins are hazards associated with chemicals that interfere with normal reproduction. They include adverse effects on sexual function and fertility, as well as developmental toxicity in offspring.
3.
From
Globally Harmonized System of Classification and Labelling of Chemicals (GHS). Available
here.
4.
From Wikipedia entry:
Globally Harmonized System of Classification and Labelling of Chemicals. Available
here.
5.
From Enforcement Guidance for the Hazard Communication Standard’s (sic) (HCS). Available
here.
6.
Note: Laux and Lintz commented jointly.
7.
Aspiration is the entry of a chemical directly through the nose or mouth, or indirectly from vomiting, into the respiratory system.
8.
IARC: International Agency for Research on Cancer and U.S., NTP: National Toxicology Program.
9.
OSHA does not enforce environmental hazards such as aquatic toxicity and ozone damage. Therefore these hazards are not required to be included on the SDS. Other differences such as the slightly altered precautionary phrases and the percent unknown toxicity requirement for Section 2 of the SDS do exist, but these variations are more cosmetic than substantive in their difference.
10.
Available
here.
Jeanna Van Rensselar heads her own communication/public relations firm, Smart PR Communications, in Naperville, Ill. You can reach her at jeanna@smartprcommunications.com.