Shale energy development trends and utilization
Stuart F. Brown, Contributing Editor | TLT Webinars April 2016
Hydraulic fracturing is the production method broadly used in Pennsylvania.
MEET THE PRESENTER
This article is based on a Webinar originally presented by STLE University on Nov. 19, 2015. “Trends in Shale Energy Development and Utilization” is available at www.stle.org: $39 to STLE members, $59 for all others.
David Yoxtheimer, a registered professional geologist (P.G.), is a hydrogeologist and extension associate with Pennsylvania State University’s Marcellus Center for Outreach and Research (MCOR). He also serves as a liaison to advise stakeholders on key environmental issues.
Prior to joining MCOR, he spent 18 years as a consulting hydrogeologist with expertise in water supply development, karst hydrogeology, geophysical surveying, environmental permitting, shale energy geology and integrated water resource management. He earned his bachelor’s of science degree in earth science from Penn State University where he is currently completing his doctorate in geosciences.
You can reach Yoxtheimer at day122@psu.edu.
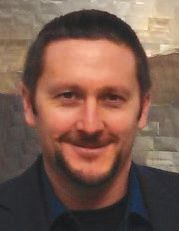
David Yoxtheimer
AMIDST ALL THE FRACAS ABOUT FRACKING—OR HYDRAULIC FRACTURING of underground shale deposits—it helps to get an idea of what gas and oil drillers are actually doing down where the sun doesn’t shine.
Shale energy deposits exist in many locations around the world, but so far the U.S. has led the way in harvesting the rock-bound hydrocarbons. A lot of visitors make the trip to Pennsylvania these days to see how it’s done. There lies the vast Marcellus deposit containing about 500 trillion cubic feet (TCF) of recoverable natural gas, which is a supply sufficient to provide for the gas needs of the entire U.S. for 20 years. The Marcellus is the country’s largest producer, putting out about 35% of the yearly total (
see Figure 1).
Figure 1. The depth of the Marcellus, the country’s largest producer. (Figure courtesy of Penn State University’s Marcellus Center for Outreach and Research.)
This presentation draws on a Webinar given on Nov. 19, 2015, by David Yoxtheimer, hydrologist and extension associate at the Pennsylvania State University’s Marcellus Center for Outreach and Research, a research organization focused on shale energy.
To date the Marcellus Shale has produced 10 or 11 TCF of natural gas, leaving much more to be recovered from the remaining reserves. Shale energy production has shown strong growth over the past five years. Running along a southwest/northeast axis in the Marcellus is a line known as the wet/dry gas boundary. There are 220,000 acres of shale to the west of that line containing methane and also a liquid natural gas, which includes ethane, propane and butane, along with some oil. There are 210,000 acres of shale east of the wet/dry boundary containing mostly methane.
Figure 2 shows the anatomy of a typical shale well. Multiple strings of steel casing are each surrounded by a sheath of specially designed cement sealant. Such wells go down vertically until they have reached a depth about 1,000 feet above the shale formation. At this point special mechanical features of the drill bit enable it to make a transition from drilling vertically to drilling horizontally.
Figure 2. This cross-sectional drawing shows the anatomy of a typical shale formation. (Figure courtesy of Penn State University’s Marcellus Center for Outreach and Research.)
Once the drill is pointed laterally it can pierce the shale for a distance of 10,000 or more feet. Sending the bit sideways for thousands of feet greatly increases the well’s contact with the reservoir and the amount of hydrocarbons it produces.
Efficiency is everything to companies drilling for hydrocarbons. One of the keys to drilling efficiency—especially in the Marcellus Shale—is for rig operators to select an underground target zone that will yield more hydrocarbons from the ground per time spent drilling. Drillers working on the Marcellus deposits like to make the 90-degree turn from vertical to horizontal in the lower portion of the shale layer, where exploration has shown that the brittleness and porosity of the rock permit drilling more feet per day.
Situated at a lower depth than the Marcellus Shale and beneath it is the Utica-Point Pleasant Shale, which contains an estimated 800 trillion cubic feet of gas and 2.0 billion barrels of recoverable oil. About 9,000 wells have been drilled to date in Pennsylvania. The Utica-Point Pleasant Shale is actually a bigger field than the Marcellus and could meet U.S. hydrocarbon needs for 30 years. Lowered gas and oil prices, however, have reduced exploration spending in these two basins.
There’s a reason the production method in broad use in Pennsylvania is called hydraulic fracturing. After a drill has turned the corner from a vertical to a horizontal path, crews send a perforating gun down the hole, where it punches hundreds of dime-sized openings in the steel casing forming the well’s exterior walls. Next the crew sends water, sand and a mix of chemicals under high pressure down the well, where it flows outward through the perforations and forces its way at a pressure of about 10,000 psi into holes and cracks in the shale layer, greatly increasing their surface area. Once the pumps are shut down, the flow reverses with pressurized fracking fluid and new gas and oil flowing back up to the wellhead where it can be captured and refined into saleable energy products (
see Figure 3).
Figure 3. Gas and oil production. (Figure courtesy of Penn State University’s Marcellus Center for Outreach and Research.)
Technical advances over the past several years have greatly increased the productivity of gas and oil wells. A well that would have produced three million cubic feet of gas per day a few years ago can now produce more than 10 million cubic feet today. The trend has been toward making a greater number of perforations per foot in well casings. For a 5,000-foot section of horizontal well, current practice is to divide it into about 200 three-foot intervals, each of which are fractured individually. By spacing the perforations more closely, drillers are able to inject a greater volume of fluid and “proppant” (a special type of sand) into the shale formation. As the liquid component of fracking fluid flows back into the well casing and up to the surface, the sand stays behind in the fractured zones, holding the cracks open so that hydrocarbons can continue to flow out of the shale. As the landscape above becomes populated with fewer drilling rigs, hydrocarbon output stays the same, thanks to the large efficiency increase the new methods bring. It’s a combination of longer laterals with more perforation and fracturing intervals.
Water gets consumed in abundance during frack drilling (
see Figure 4). It is used at the rate of 1.0 to 1.1 million gallons per 1,000 feet of lateral well completed. In the northeast region, surface water is used for fracking, while groundwater prevails in the west. Once drillers stop pumping fluid down a fracking well, the pressure release permits fluid to begin flowing back up the well and to the surface. These quantities can range from 5%-50% of the initial amount of fluid originally injected into the well. Fracking fluid additives consists of 1% or less of the total fluid volume.
Figure 4. Water use in fracking operations. (Figure courtesy of the EPA Hydraulic Fracturing Study Workplan, Penn State University’s Marcellus Center for Outreach and Research.)
Fracking operations often rely on fleets of heavy trucks to bring water to drilling sites where it is mixed with chemical additives that can include a friction reducer, a scale inhibitor and a biocide. A typical well can require about 1,000 truck trips of water. The high cost of all that trucking has led some drillers to construct local pipelines to carry water to and from well sites.
At a mountainous Pennsylvania location, drillers studied the cost of trucking in all the water needed for fracking about 100 wells and concluded that it would be about $20 million when truck fuel and maintenance and access road upkeep were factored in. Further study revealed that they could build a 12 km pipeline through the area at a much lower cost of about $10 million, which was the chosen method. On jobs such as this one in the Marcellus basin or in the nearby Appalachian basin, about 90% of the fluids used are recycled and used on the next fracking job. In parts of Texas where lots of disposal wells exist, just 10%-20% of the fluid might be recycled with the rest pumped back in an injection well.
You can reach free-lance writer Stuart F. Brown at www.stuartfbrown.com.