Complexity in ISFA (in-service fluid analysis): Part XXVI
Jack Poley | TLT On Condition Monitoring March 2016
Mining for dollars Part II—making it easier on the intelligent agent.
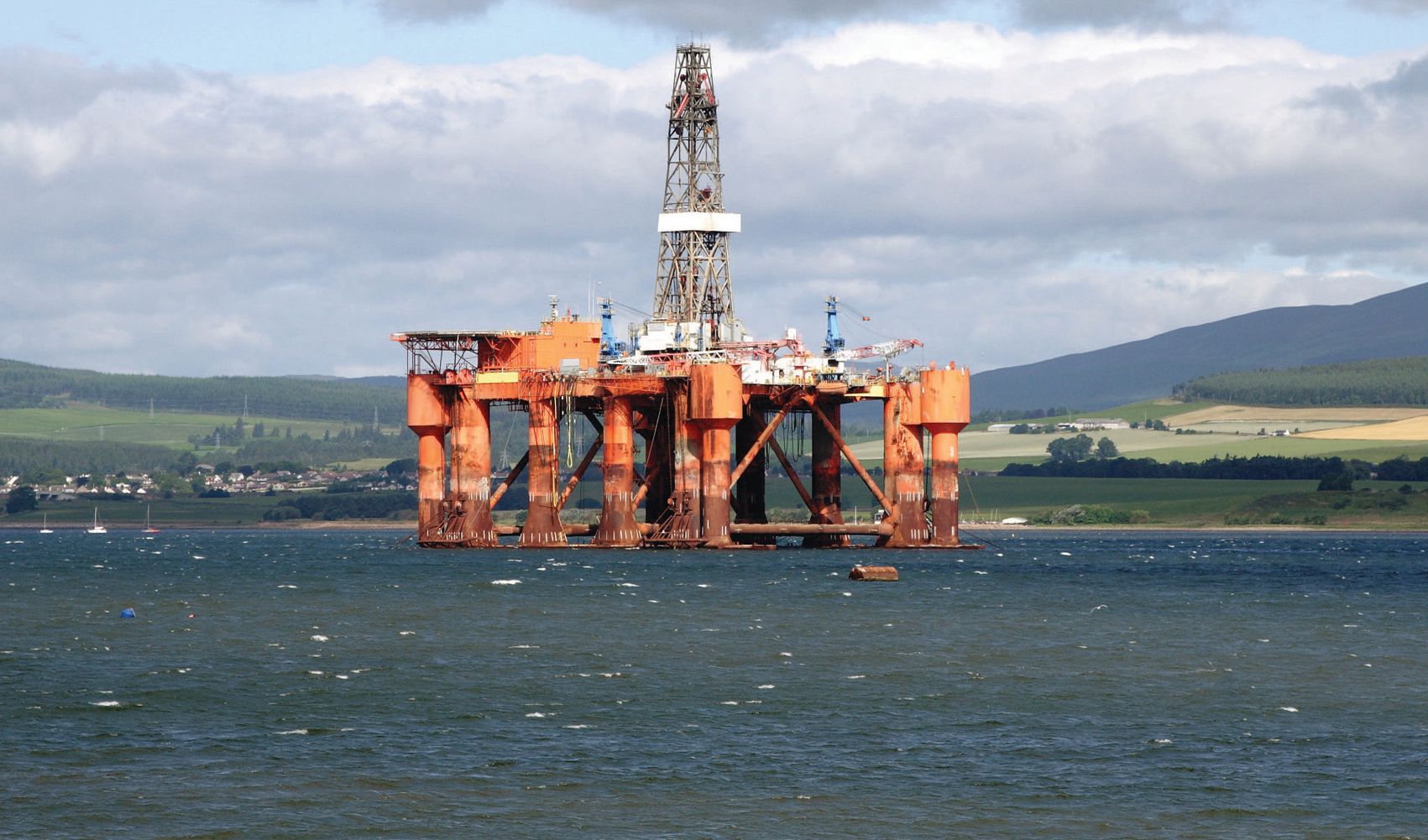
© Can Stock Photo Inc. / doubleus
LAST COLUMN, I PRESENTED THREE REQUIRED INFORMATION PIECES IN ORDER for an intelligent agent (IA), domain knowledge-infused expert system:
1.
The component name (I.D.), a unique designation for the lubricated asset (the sump) being monitored
2.
The sample date (no date, no trending)
3.
The component type (diesel, gas turbine, gear set, etc.).
Let’s revisit the conceptual difference between equipment and component once more. The equipment houses the component and the component hosts the lubricant (or other fluid being tested). You may prefer different labels—well and good—but if so, it’s essential you still translate your terms correctly to the IA data template so that appropriate tables of boundaries and commentary are availed. Figure 1 shows some relationships between equipment and component.
Figure 1. Relationships between equipment and component.
Notice that some equipment like
plant is strictly conceptual, but it’s important to recognize that relationship to the sampled component. The important thing is to differentiate properly.
Note as well that a top drive (the principal drilling apparatus on most drill rigs these days) is a
sub-equipment in effect. Most every top drive has a gear set (the main drive) plus a hydraulic and, often, seals. Multiple sample points therefore exist and must have separated records. It would be slightly wrong using our dictionary for this article to call it a
sub-component since we’ve already postulated that components house the lubricant or other fluid. In this case I suggest the proper thing to do is violate the rule we posited and create an exception, calling the top drive a sub-equipment but treating the top drive’s individual sumps as components called Top Drive Gear, Top Drive Hyd, etc., until all sumps sampled are accounted for. Also note that you’ll still need to identify these components as simply
gear (and type of gear if you know: Helical, Pelatoid, Herringbone) and the
hydraulic (and type if you know: axial-piston, gear, vane, etc.). Then you will have everything sorted out.
Yes, this is a semantics exercise, but it’s important you conduct it correctly when you set up or redress your database. As I warned early on, there is a bit of work and some tedium, mostly paying close attention to detail that is necessary to have something close to an idealized, pristine database. I hope by now you know why I’m pressing so hard with this notion. Here’s a hint: $$.
Occasionally the component is stand-alone, i.e., it belongs to no plant or recognizable equipment. However, it could be in a group of transformers that are part of a specific grid configuration, i.e., are clustered near each other, creating a logistical equipment.
I gave some examples of component types; however, Figure 2 is a more thorough list, though there might always be a component that requires its own unique component type designation. I have found this list to be >99% complete thus far. We may have created as many as five (if that) new component types in the last three or four years.
Figure 2. Examples of component types.
It stands to reason: The component is the
key to good evaluation. So one should always aim to provide as much information as possible as to a component’s classification. And by the way, it’s also a good key to help the lab guide one to the best test package possible. Labs often have difficulty rendering incisive evaluations when samples enter the door labeled crudely: diesel engine, compressor or hydraulic, and nothing else—not an MFR, not a sump size. (You wouldn’t be so quick to recommend a drain on a 5,000 gallon sump, would you?)
Sampling should not be an exercise in inadvertently misleading an evaluator. On the other hand, I’ve always advised evaluators never to guess the sub-classification of, say, a
hydraulic system. About all one can do when limited to such basic nomenclature, even if one is using an IA, is state:
Wear is normal, abnormal, very high, severe and lube is or is not suitable for continued use; fluid needs to be drained (and filtered, if applicable, also changed); or
fluid needs cleaning or polishing, though we’re not sure what the contamination limits might be. We would take a middle-of-the-road approach perhaps. One surely should not mention
axial pistons or
vanes because one just doesn’t know.
We’ll conclude the database construction/redress next article.
Jack Poley is managing partner of Condition Monitoring International (CMI), Miami, consultants in fluid analysis. You can reach him at jpoley@conditionmonitoringintl.com.
For more information about CMI, visit www.conditionmonitoringintl.com.