Complexity in ISFA (in-service fluid analysis): Part XXV
Jack Poley | TLT On Condition Monitoring January 2016
Mining for dollars—making it easy on the intelligent agent.
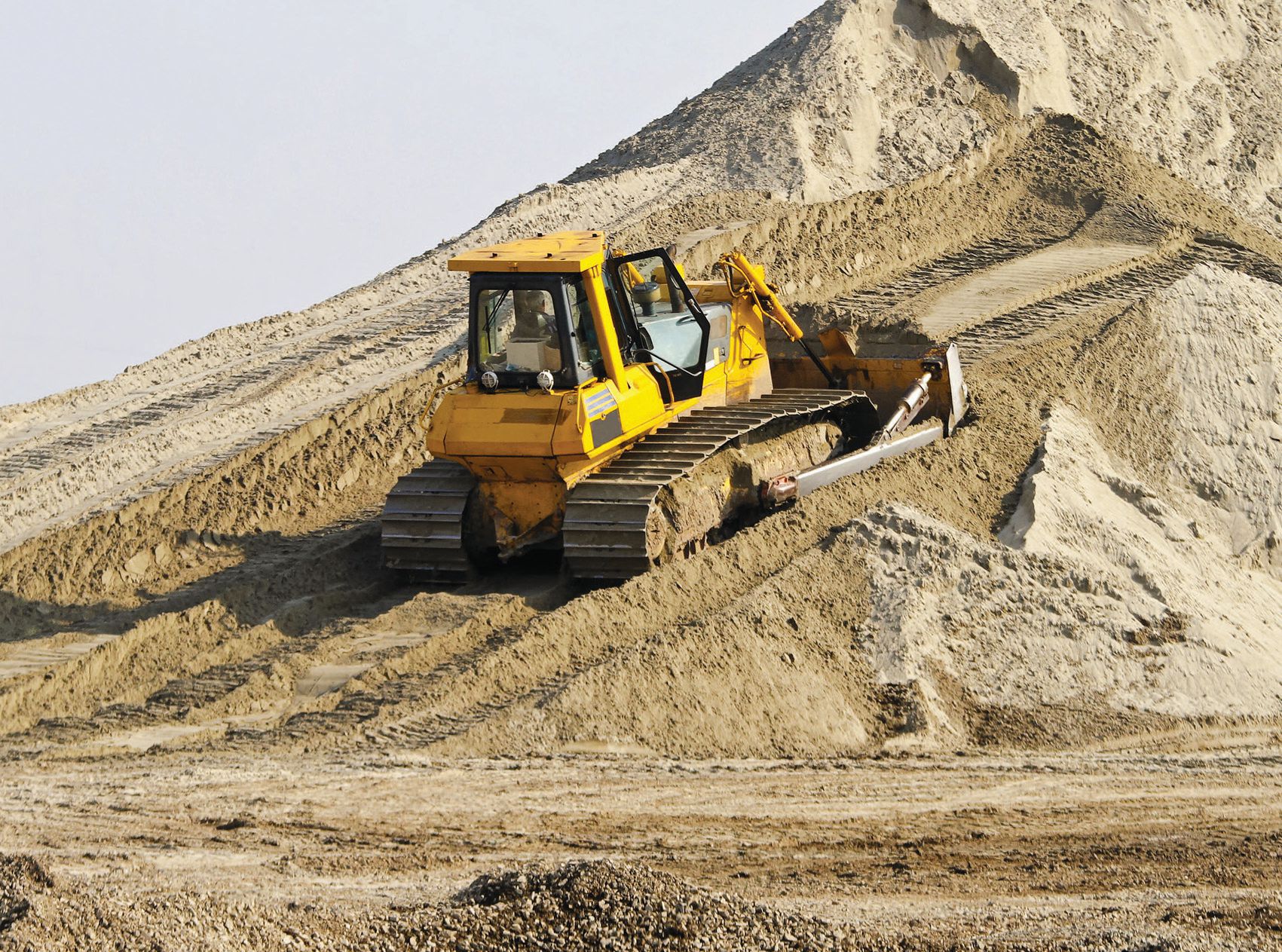
© Can Stock Photo Inc. / Baloncici
TWO COLUMNS AGO I PRESSED HARD TO GET YOU INTERESTED IN INSPECTING your lubricated components database for full, accurate information as well as consistent terminology. Let’s explore this a bit further, particularly with the idea of having an intelligent agent (IA) in play. Because the IA is precision it doesn’t play well with inconsistency.
First and always, it’s about money. A well-managed, informed database would enhance potential dividends ongoing.
There are three pieces of information that are necessary in order for an IA to function in minimal fashion:
1.
The component name (ID), a unique designation for the lubricated asset being monitored
2.
The sample date (no date, no trending)
3.
The component type (diesel, gas turbine, gear set, etc.).
What about time on the lube and component? Well, that’s useful, for sure, but not necessary to get an IA to function. Besides, well over half the world’s samplers don’t get this information to the evaluator anyway (and it is often wrong when furnished). But if they did, one could use normalizing algorithms and calculate wear rate with a modicum of precision.
The component name and the sample date are straightforward, therefore the component type is where the specification of the sampled sump begins.
But sample sumps, i.e., components, are sometimes attached to
equipment, another reserved name for IA usage, and this needs to be accommodated. A basic example of this might be a bulldozer, which may have an engine, a transmission, a hydraulic system and two final drives. A total of five compartments (components) with lubricated sumps.
So let’s say one has sampled a hydraulic system. Is it a good idea to say one has sampled a hydraulic system without further definition? There are hydraulic systems that are simple gear pumps, but there are more sophisticated systems such as axial-piston pumps or vane pumps. In fact, you would want the person (or the computer program, the IA) evaluating your hydraulic system to know what type of system it is, would you not? Then you should say so, i.e., inform the database.
Of course one could specify the MFR and model of the hydraulic system and that would enable the evaluator to determine the pump mechanism. Unless the evaluator has specific experience with that particular MFR/model combination, it may not happen. Better to specify the hydraulic system more completely at the outset. Certainly one should follow with identifying the MFR/model but that comes later. Get the component type fully correct first and the rest is gravy.
Thus, we can create component type codes (for absolute consistency) that will allow us to segment the types of hydraulic systems according to their pump mechanisms:
•
BH. A generic hydraulic system without further detail.
•
BHAX. An axial-piston pump type system.
•
BHVN. A vane pump.
•
BHGR. A gear pump.
•
Etc.
If the system is more precisely described, the IA has something to grab onto and can provide pertinent comments that make sense for a particular hydraulic mechanism.
If a component is simply identified as a (generic) hydraulic system (BH), the IA is somewhat handcuffed (so should a human evaluator be) and cannot use more specific terms such as piston, swash plate or vane in attempting to assess wear and its probable location. This is a big deal when one later wishes to assess systemic problems by mechanism type.
So we now have postulated that the first technical fact one needs to know about a sampled compartment, the component, is its mechanism type (component type) described as fully as possible. Every component type has possible subcategories that can make an IA more powerful. In addition to the hydraulic example, also note these component types:
Diesels. There are liquid-cooled and there are air-cooled diesels. There are diesels utilizing biodiesel and other alternative fuels. There also are diesels configured with opposed piston crowns—two blocks bolted together and, thus, have no cylinder heads. These types of variations, however, are differentiated by the MFR and model aspects of a hierarchical component database.
Compressors. There are vane, centrifugal, reciprocating, axial and rotary screw (lobe).
Again, the object is to mechanically define the component as fully as possible to take advantage of specific domain expertise in the IA.
Now we must back up a bit and once again start with
where the component is situated.
Using another reserved term for what houses the component, we try
equipment.
EQUIPMENT NAME (ID)—UNIQUE
Equipment houses the component that has been sampled. Equipment can have a name, possibly a company tracking number, a serial number, possibly some descriptive text, etc., but it must be unique.
EQUIPMENT TYPE
Examples of equipment types are a
truck, bulldozer, cruise ship, drilling rig, or stationary
plant (e.g., a factory or building housing the component such as a compressor for air utility).
EQUIPMENT MFR/MODEL
If we have enough information about the equipment and its model, we actually could look up the component type information with confidence since most models reflect standardized components in use, but that’s a tedious chore. Again, tend to the component type and everything else will fit. The real purpose of the equipment MFR/model is to be able to track performance of that particular configuration as a group as well as standardize on wear table limits and the like.
Now we get to placing the component:
COMPONENT NAME (ID, SOMETIMES CALLED SPID)—UNIQUE
The component is the sampled item (the lube sump or source). It can have a name, possibly a tracking number for the company it belongs to, a serial number (separately, if necessary), etc. As with the equipment name, component name must be unique.
COMPONENT TYPE
This piece of information about the sample’s origin is essential in order for auto-evaluation to operate (e.g., gas turbine, diesel, gear set, hydraulic and subsets when possible). If we don’t know whether the sample is from a gas turbine versus a lawn mower engine, no test data can be usefully rated.
COMPONENT MFR/MODEL
Knowing who manufactured the component is always useful. This helps the IA locate possible metal sources and other tables that provide more stringent constraints for potentially deeper commentary. Model designation is equally helpful, further narrowing the data rating and evaluation, often for better precision.
APPLICATION
How a component (or its equipment) is used is often significantly influential toward assessing test values. Off-highway, marine, or oil and gas are completely different applications, where like component types or MFR/models will perform noticeably different, yielding different levels for test results. IAs should allow for such differentiation.
GRADE
What viscosity should the IA expect to find? If grade is not provided, some IAs will attempt to estimate the lube grade on the initial assumption that the VIS value is within a normal range for the product under test. Thereafter it is up to the customer to advise to the contrary or else the estimate remains and is used as the evaluation pivot for viscosity severity assessments, unless or until the customer intervenes.
LUBE MFR/BRAND
Both are needed to affect evaluation. Straightforward, but caveat: Advising one to utilize “MobTexShellChev” lube is well and good, but unless one also designates the brand (the name given to the lube by the MFR), the IA won’t know how to set additive metal and other limits. New lube reference samples are very important at the outset of a program in order to set limits appropriately as the IA may not have such on file.
FILTER MFR/BRAND
Combined info is needed to affect evaluation. Who made this filter and what name does the MFR use as a designation (brand) for this filter? As with lube MFR, not knowing the filter brand, as well as the MFR, negates these fields.
FILTER TYPE
What is the physical nature of the filter? Screen, paper, synthetic fiber, centrifugal, etc.
We’ll tie all these together in the next installment of On Condition Monitoring.
Jack Poley is managing partner of Condition Monitoring International (CMI), Miami, consultants in fluid analysis. You can reach him at jpoley@conditionmonitoringintl.com.
For more information about CMI, visit www.conditionmonitoringintl.com.