The Lubrizol Corporation
Lubrizol MC9330: A Heavy Duty Lubricity Additive for Water-based Metalworking Fluids
By Ben Faber, Metalworking Product Manager, The Lubrizol Corporation | TLT CMF Plus November 2015
What if you could make a mineral oil-free metalworking fluid that could replace chlorinated soluble oils?
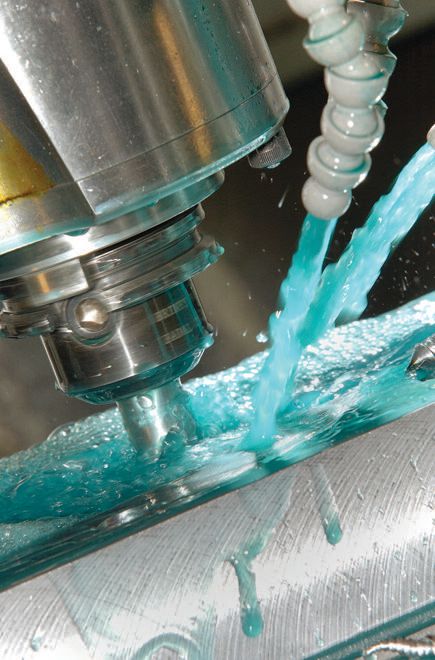
Heavy duty metalworking fluids are under a lot of pressure with increased regulations proposed against chlorinated paraffins. Because of the proposed rules, many fluids that have been used for years will need to be reformulated or replaced. This will create competition among fluid compounders, as end-users will expect to transition seamlessly from chlorinated fluids to chlorine-free.
The trend in North America has been to move away from straight oils and soluble oils and towards semi-synthetic and synthetic metalworking fluids. Said another way, the market is trending towards metalworking fluids with less and less oil content. This transition has been happening for years where possible, but there are still many operations that use the high oil content fluids because they require the heavy duty lubricity offered by oil. End-users would like to switch to semi-synthetics because they can be much more stable, and provide a longer sump life compared to soluble oils when properly maintained. The idea of making mineral oil-free fluids is appealing, allowing for water-clear fluids that can provide excellent cooling and chip removal.
Using Lubrizol® MC9330 technology, new fluids can be made that can run clean like synthetics but lubricate like soluble oils. Lubrizol MC9330 is easy to use, requiring only simple formulations, but delivers multifunctional performance. And Lubrizol MC9330 is flexible, so you can use a small amount for an easy application or load up a formula to do strenuous operations.
Introducing Lubrizol MC9330
Chemically, Lubrizol MC9330 is a hydrophilic polymeric ester. Functionally, Lubrizol MC9330 performs as the lubricity additive and the emulsifier in a metalworking fluid. It can do both of these functions because the polymer backbone is built with different pieces that provide the lubricity and the emulsification. Additionally, there is no mineral oil, no chlorine, no sulfur, and no phosphorus in Lubrizol MC9330, so a formulator can shape whatever type of fluid they would like to make. The product can always be supplemented with more lubricity additives (like EP additives) to enhance fluid performance.
As-is, Lubrizol MC9330 will not go into water, but when it is neutralized with an excess of amine it becomes self-emulsifying and forms a stable microemulsion. A properly formulated metalworking fluid should have an excess of base and an alkaline pH, and Lubrizol MC9330 incorporates this feature to align with how fluids are designed today. Using Lubrizol MC9330, corrosion inhibitor, and a biocide, and you can create a simple and complete product from only a few ingredients.
Multi-Metal Machining Fluid
A large portion of the metalworking fluids used are put into central systems and are expected to handle different metals and machining operations. The term “general purpose” is commonly used for these fluids, and Lubrizol MC9330 can be used to make an excellent general purpose machining fluid. Lubrizol MC9330 is well-suited for this because of its flexible performance on both steel and aluminum.
Once again, formulating with Lubrizol MC9330 is simple. To demonstrate this, Table 1 shows a starter formulation used to highlight the performance of Lubrizol MC9330 as a multi-metal machining fluid. In this formula, a coupling solvent (Dowanol™ DPnB*) has been added, which helps to keep the formulation together and helps with the fluidity of the concentrate.

The term neosynthetic can be used to describe this type of fluid. A neosynthetic metalworking fluid is a mineral oil-free product that still contains an emulsion. This differs from a synthetic fluid, which is a true solution and is a single phase and not an emulsion. It also differs from a traditional soluble oil or a semi-synthetic since those typically contain emulsified mineral oil. For use in the field, this concentrate should be diluted from 5 to 10% in water, and it will create a stable microemulsion with a slightly hazy appearance. Figure 1 shows a photo of Lubrizol MC9330 on the left, and a photo of a fully diluted finished fluid based on the recipe in Table 1.
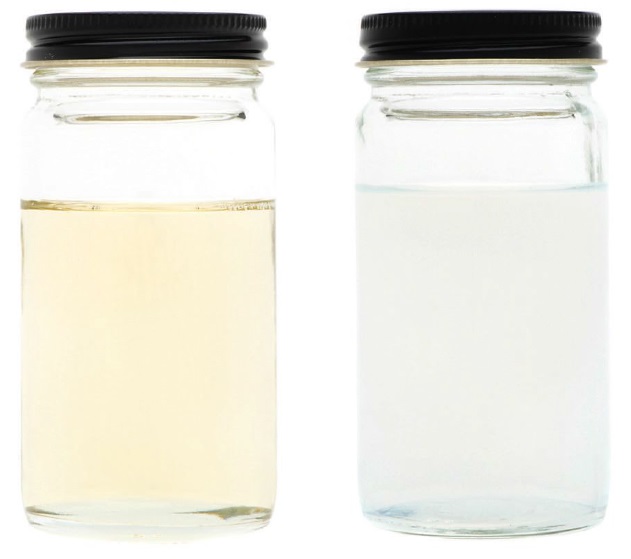
Figure 1. On the left is a photo of Lubrizol MC9330 as-is, and on the right is a photo of a fully diluted neosynthetic fluid based on Lubrizol MC9330.
To evaluate the lubrication performance of this product, Microtap testing was completed on both 1018 steel and 6061 aluminum. For comparison, two controls were run alongside Lubrizol MC9330. The first control is a soluble oil product, and contains roughly 80% mineral oil in the concentrate as well as lubricity additives. The second control, a high oil semi-synthetic, also contains a large amount of oil and lubricity additives.
Figure 2 shows the Microtap performance for form tapping 1018 steel. The testing shows that the fluid based on Lubrizol MC9330 has a higher relative efficiency (better performance) compared to the soluble oil, and slightly lower versus the high oil semisynthetic. This is an impressive result considering there is no mineral oil in the neosynthetic. Figure 3 shows the Microtap performance on 6061 aluminum, and this testing shows a huge advantage for Lubrizol MC9330 on aluminum vs. the other two fluids tested.
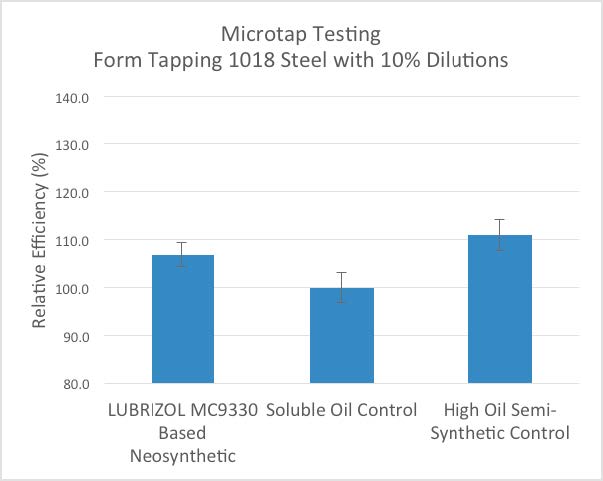
Figure 2. Microtap testing on steel comparing the relative efficiency of Lubrizol MC9330 versus a soluble oil and a high oil semi-synthetic.

Figure 3. Microtap testing on aluminum comparing the relative efficiency of Lubrizol MC9330 versus a soluble oil and a high oil semi-synthetic.
Low Foaming
A major concern for metalworking fluids is foam. Since Lubrizol MC9330 was created to work in different systems (including high pressure systems), the emulsifier portion of the molecule was designed to give low foaming properties and quick foam dissipation. To highlight the foam properties, Figure 4 shows the performance of the multi-metal machining fluid in the Lubrizol Pump Foam Test. This test is a recirculation test, and 600 mL of fluid is pumped through a modified graduated cylinder while the height of the foam is measured. The fluid is circulated for 300 seconds (5 minutes) with measurements taken every 30 seconds. The pump is turned off (represented by the black line in the chart below) and the foam dissipation is measured in the final 300 seconds. Overall, a result of 400-600 mL of foam in this test describes a low to moderate foaming product, and the strong foam breakdown to almost zero tells us that the foam will dissipate fast enough that it will not be an issue.
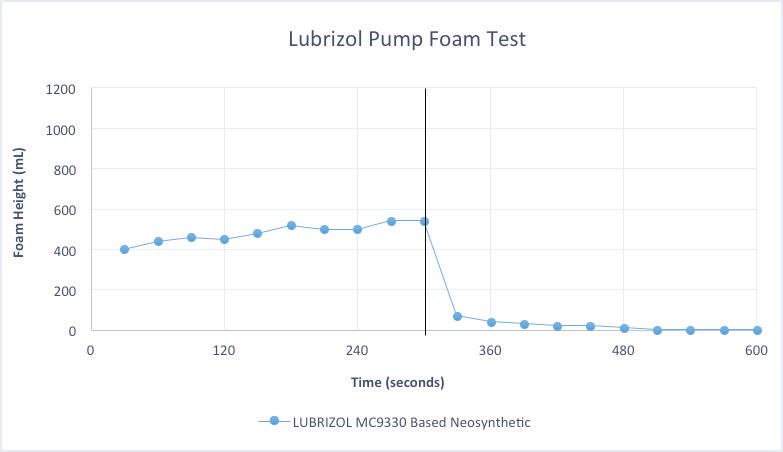
Figure 4. Lubrizol Pump Foam Testing on a 5% dilution of the neosynthetic in 120 ppm hardness water. In this test, a fluid is circulated for 5 minutes (300 seconds) and then allowed to rest for the remaining 5 minutes.
Heavy Duty Stamping Fluid
Lubrizol MC9330 is a versatile product. Not only is it capable of making a high quality general purpose machining fluid, but it is also capable of making a heavy duty drawing and stamping lubricant. To demonstrate this, a starting formula for making a stamping fluid is included in Table 2.
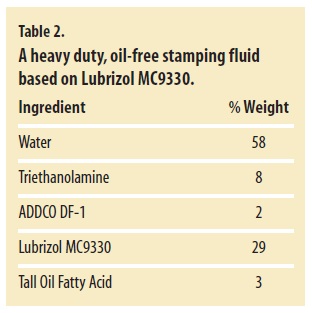
Metalforming and stamping fluids are commonly used at high concentrations. This concentrate can be used anywhere from 10-50% concentration, and the following field trial was done using a 50% dilution in tap water. This particular fluid was designed for a one-time use and not to be recycled. If the fluid were to be recycled, it is suggested that biocide is added.
Field Trial
In collaboration with a parts manufacturer, a field trial was done to confirm the performance of Lubrizol MC9330. This manufacturer was stamping out tractor-trailer wheel assembly parts from ¼ inch carbon steel sheet stock. The roughly 2 feet in diameter parts (shown in Figure 5 below) were made with a 3000 ton press with 3 stages. The lubricant was sprayed with a mist onto each part before the first step, and was carried on throughout the full process.
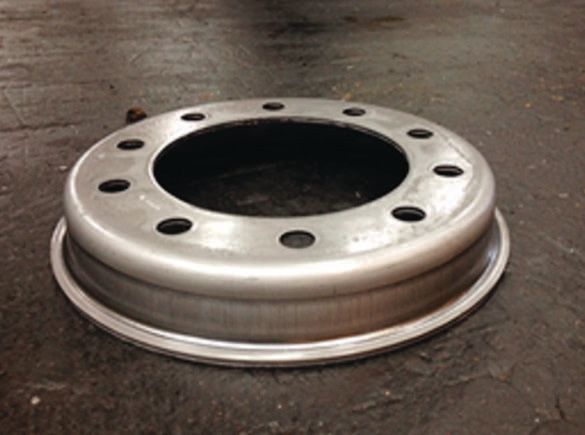
Figure 5. A photo of the tractor trailer wheel assembly parts produced during a field trial using Lubrizol MC9330.
The machine shop running the trial was currently using a chlorinated paraffin based soluble oil to manufacture parts, and was looking for a chlorine-free alternative. In the past, they had tried using a synthetic, mineral oil-free lubricant with no success. The only fluid to pass their approval process was the chlorinated soluble oil. Lubrizol’s laboratory tests gave clear enough proof that Lubrizol MC9330 was better than the synthetic previously tried, and similar in performance to the chlorinated soluble oil.
On the day of the field trial, the machine shop replaced their existing fluid with the formulation found in Table 2 and was able to make an entire shift’s allotment of 4400 parts without a single rejection due to lubrication. They also saw no change in wear on the dies, and gave the mineral oil-free product their glowing endorsement. They were very impressed to be able to switch from a chlorinated paraffin-based product to a mineral oil-free product without making any serious adjustments to their process.
A New Tool in the Formulator’s Toolbox
With regulators set to ban the use of medium chain and long chain chlorinated paraffins in mid-2017, the tool - box for formulators is losing a crucial heavy duty additive. Lubrizol MC9330 is meant to fill that spot and allow for fluids that can run cleaner and longer without compromising on lubricity. This flexible and multifunctional additive enables the formulator to simplify metalworking fluid design and achieve extraordinary performance.
*Dowanol is a trademark of The Dow Chemical Company. All other tradenames referenced herein are trademarks of The Lubrizol Corporation.