ExxonMobil Chemical
The enhanced oxidative stability of metallocene polyalphaolefin base stocks
By Michael P. Sheehan, Marketing Technical Services, ExxonMobil Chemical Company | TLT CMF Plus November 2015
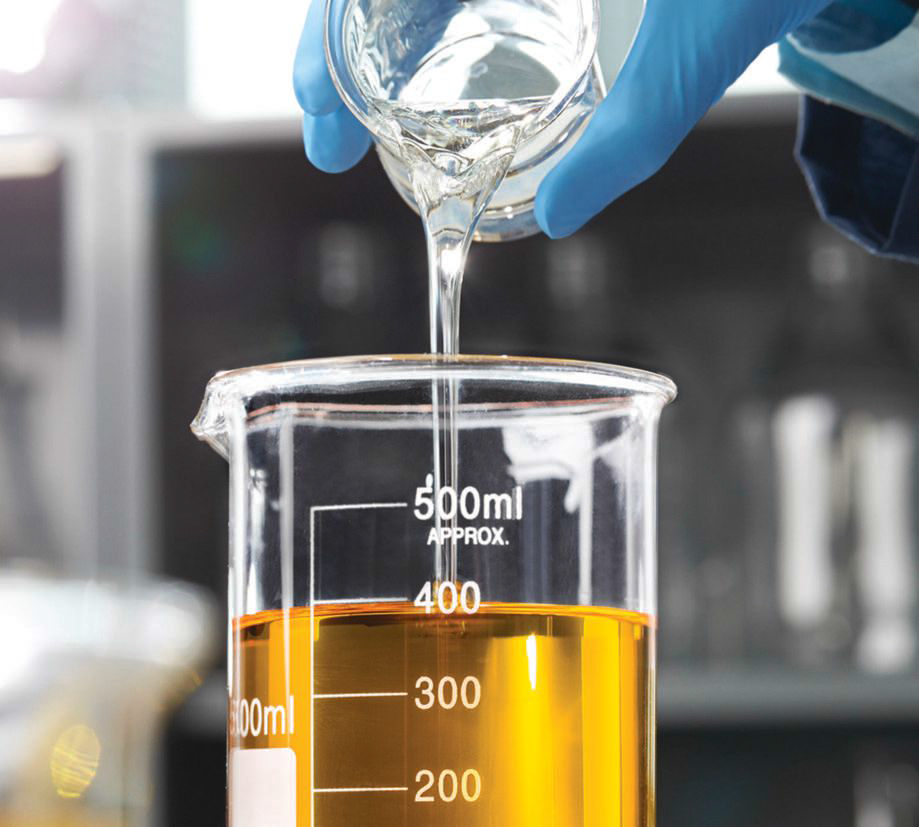
Polyalphaolefin (PAO) base stocks have long been used to formulate high performance lubricants for automotive and industrial applications. Their high viscosity indices (VI), very good oxidative stability and excellent low-temperature properties help formulators create lubricants that operate for longer periods under wider operating temperatures than equivalent viscosity grade mineral oils. PAO-based lubricants also typically can offer energy savings through reduced traction and improved low-temperature fluidity.
When they were introduced, PAO-based lubricants tended to be used for very high performance, top-tier products or for applications in which mineral oil performance was insufficient, such as in extreme temperatures. However, over the years, the use of PAO has increased as industry trends demand higher lubricant performance. More compact equipment running under more severe operating conditions creates higher stress on the oil, which at the same time is expected to provide longer drain intervals. Under these conditions, lubricants are exposed to higher oxidative and thermal degradation, creating a greater need for products that offer enhanced oxidative stability.
In the past few years, a new family of PAO products has been developed to meet the rising demand for high viscosity synthetic base stocks. Based on metallocene catalyst technology, this new metallocene polyalphaolefin (mPAO) base stock can provide improved properties over conventional PAO (cPAO) — higher viscosity index, better low-temperature fluidity and greater shear stability. The oxidative stability of these PAOs was initially thought to be equivalent, but subsequent testing shows that mPAO offers enhanced capability in this key performance area.
The importance of oxidative stability
Oxidation is the breakdown of a lubricant due to aging and operating conditions in the presence of oxygen (air). Oxidation results in oil thickening with the formation of acidic byproducts. Depending on the severity of the oxidation, the oil could form polymeric byproducts leading to varnish and lacquer deposits on metal surfaces.
The rate and ease of a lubricant’s oxidation depend on:
•
Temperature — each 10°C increase doubles the oxidation rate
•
The type of carbon-hydrogen bond — CH
3 primary carbons being the least reactive
•
Concentration of oxygen
•
Catalytic effect of metals
•
Presence and concentration of antioxidant and metal passivator additives
Improved oxidative stability leads to less oil thickening, lower production of acidic byproducts and better deposit control. These improvements could translate into longer service life, better energy efficiency, longer equipment service with less downtime and possibly lower maintenance costs.
Comparing the structures of mPAO and cPAO
Given the advantages of greater oxidative stability, the structure of mPAO suggests it should provide this enhanced capability (
Figures 1 and 2). Metallocene catalysis is a very stereospecific reaction, creating a product with little to no olefin isomerization during polymerization. The residual olefin is terminally located. Production of cPAO, on the other hand, uses a strong acid catalyst, resulting in extensive isomerization of the olefin bond during polymerization, which internalizes the residual olefin.
After polymerization, the base oil is hydrogenated to remove unwanted residual olefins to improve stability. Terminal olefins are easier to hydrogenate than internalized olefins, resulting in a base oil with a lower level of unsaturation, which improves oxidative stability. Although the unsaturation level for cPAO is very low, ExxonMobil tests show that it is two to three times lower in mPAO.
A second structural difference that could impact oxidative stability is tertiary carbon (C-H) content. The reactivity rate of the C-H bonds shows that tertiary carbons are next in the ease of oxidation after olefins. Due to the difference in isomerization rate (
Figure 2), mPAO should have a lower level of tertiary carbons than the same molecular weight cPAO.
Demonstrating the difference
To prove that mPAO offered enhanced performance, alternate tests were considered that provide greater flexibility to safely stress the oils. ASTM D4636, which is used to evaluate aviation turbine lubricants, was chosen because it offered many of the same parameters found in accepted industry tests (
Figure 3), but allowed safe modifications of the test.
To determine if a performance difference existed between the two base stocks, the temperature, test duration and air flow rate parameters were modified and examined. The spent samples for viscosity change (oil thickening), total acid number change, sludge content and metal catalyst weight change were tested.
The first set of experiments focused on the impact of test temperature on oil viscosity change (
Figure 4). The test was limited to ISO VG 320 base oil blend (no additives) to minimize effects associated with an additive system.
The results showed that a test temperature of 204°C provided a clear performance break point, while minimizing test duration (72 hrs) and air flow rate (5 l/hr air). The neat base oils were then accessed to get a clear understanding of the performance differences without clouding the data with other issues, such as co-base oils or additive impact. The results are shown in
Figure 5.
The mPAO base oils demonstrated lower oil thickening, better acid number control and improved corrosion toward magnesium metal. Although the test looks at five metals (Al, Ag, Cu, Steel and Mg), the only one impacted was the magnesium. The sludge control data was mixed, with mPAO 65 providing an improvement over cPAO 40 while the mPAO 150 offered equivalent performance to cPAO 100.
Evaluating blends
Next, the performance of a combination of low and high viscosity PAO to make a non-additized ISO VG 320 blend was evaluated. Again the results (
Figure 6) show that mPAO blends offer better viscosity and sludge control than cPAO-based samples. It is notable that the cPAO 100 and mPAO 150 are at the same treat rate, whereas the blend using cPAO 40 has a slightly higher concentration compared to the mPAO 65 blend.
Testing formulated lubricants
After testing the neat and base oil blends, would mPAO offer any benefit to a fully formulated lubricant? ISO VG 320 industrial oil samples were formulated and tested in the modified method. cPAO 100 and mPAO 150 were compared to keep the formulations consistent by maintaining the same concentration of the high viscosity component.
As expected, the additives in fully formulated products negated the differences seen in earlier tests. As shown in
Figure 8, the formulated samples displayed no difference in performance because the additive package minimized oxidation and extended service life.
An effort was then made to identify conditions to offset the additive response. Wanting to maintain the existing test temperature, test duration was extended. By extending it from 72 hours to 144 hours, the antioxidant additive was sufficiently consumed, and the difference in performance between the base oils was seen. In fact, when the test duration was extended to 168 hours, the cPAO formulation was solid at room temperature while the mPAO-based sample flowed.
After identifying the new 144-hour test condition, several experiments were run to assess performance of the formulated samples (
Figure 7). The results indicated the mPAO-based formulation offered enhanced viscosity and sludge control, as well as lower total acid number change compared to the cPAO-based product.
Conclusions
Through alternate test methods that create more severe operating conditions, mPAO was found to offer performance advantages over cPAO base stocks (
Figure 9).
The enhanced oxidative stability of mPAO lessens oil thickening, allowing a formulated lubricant to better retain its lubrication capabilities even in extreme conditions of temperature and stress. The mPAO also reduced sludge and varnish generation.
Before these tests, it was known that mPAO provides higher viscosity index, improved low-temperature performance and superior air release and foaming properties when compared to cPAO. With this new awareness of enhanced oxidative performance under severe conditions, formulators can now make a more informed decision when choosing which PAO base stock is right for the lubricant they want to blend.
All product/performance data herein based on ExxonMobil Chemical SpectraSyn™ high viscosity products. Other cPAO and mPAO products may have different characteristics.
© 2015 Exxon Mobil Corporation. All rights reserved.
All trademarks used herein are trademarks or registered trademarks of Exxon Mobil Corporation or one of its affiliates unless otherwise noted.