What are the advantages of high-performance grease? What would promote greater industrial use of high-performance grease?
TLT Sounding Board August 2015
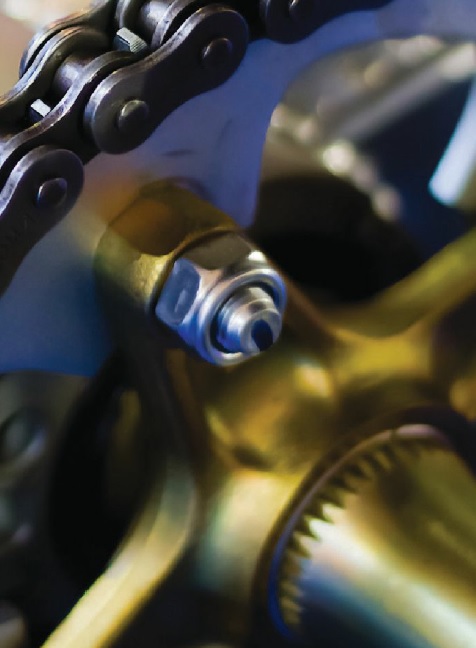
www.canstockphoto.com
As you might expect from an organization of tribologists, respondents to this month’s survey were uniformly enthusiastic in their praise of grease. Among the benefits they stated are longer component life, increased high-temperature stability, extended relube intervals, energy savings and better equipment performance. Several noted that grease can even be a less-expensive option over the life of the equipment. Almost all agreed that education is the key to helping end-users understand the advantages of high-performance grease. Said one reader: “Education is needed—most people have little idea what grease is or its benefits over and above light oil or graphite spray.” More than half of the respondents are confident in their technical knowledge of grease, and nearly two-thirds say that creating grease is half exact science and half an art.
All the advantages of grease plus lower wear. Better marketing.
In most applications high-performance lubes can lead to less down time and more efficient operations. The best way to promote them will be to have experienced professionals who can promote the benefit and the associated cost savings.
High-temperature performance, better water wash off, cost savings, energy savings, extended life. The industry needs to do a better job at explaining the benefits to the end-user.
Addressing high heat and water concerns. Using high-performance grease will lead to better performance and will become more cost effective over time.
Less frequent service interval.
Long-term reliability with less maintenance.
Reduced consumption, longer life intervals and high temperatures before oxidation takes place. It needs to be sold with attributes and not commoditized.
Extended service life of the grease and fewer failures from lack of lubrication on critical applications resulting in less maintenance cost and improved productivity.
Longer grease life for extended regreasing intervals and superior water resistance. Obtaining these benefits requires recalculation of regreasing intervals breaking habitual greasing practices.
After lithium greases, which one of the following greases has the greatest potential to be considered as a future multipurpose high-performance grease?
Calcium sulfonate grease
48%
Polyurea grease
33%
Aluminum complex grease
21%
Clay-based grease
5%
Based on responses sent to 13,000 TLT readers. Total exceeds 100% because some respondents chose more than one answer.
Longer relube periods, longer component life in the application, therefore less downtime.
We need case studies to determine actual benefits.
Grease has the ability to hold the oil where it needs to be in situations where a liquid would not stay.
Longer service time and extended life of equipment.
More stability at higher temperatures, higher speeds and higher pressures.
Increased specificity of the product should lead to decreased maintenance requirements and better equipment performance.
It depends on the application and the specific product being considered—testimonials can help a customer make a decision.
Oil is always the preferred lubrication. However, grease provides an alternative form of lubrication. The benefits of grease are that viscosity can be varied and synthetic lubricants can be used to extend grease intervals. Education is always the key to upselling the customer. The greatest obstacle is that companies and individuals love the status quo.
The primary benefit is improved reliability. I think the biggest detriment to using high-performance grease is a lack of knowledge on the user’s part.
Increase productivity, less maintenance.
Greater conservation and efficiency of the equipment.
Wide operating temperature range to minimize number of greases on site with an NLGI 1 or 2 and synthetic base oil plus high drop point thickener.
Grease is more likely to stay where it is put and lubricate/protect where it is needed. Education is needed—most people have little idea what grease is or its benefits over and above light oil or graphite spray.
Lifetime lubrication, lower lube consumption and releases to the environment. Longer lifetime of the equipment and higher performances.
Are you confident in your knowledge of grease—both its creation and applications?
Yes
67%
No
25%
Other
8%
Based on responses sent to 13,000 TLT readers.
Reliability, machine uptime and availability so as to maximize production. We need to educate maintenance teams. Grease isn’t just grease—and all greases aren’t the same!
The value/cost savings they deliver. HP greases/lubricants do outperform general industrial greases in 15%-20% of the applications on lube life, component life and machine availability.
Lubrication, EP, sealing, noise reduction, water protection. Clear definition for which group of applications certain types of grease can be used.
Extended maintenance intervals, fewer bearing failures and ultimately lower costs.
Better equipment life, lower temperatures. They need to be marketed as they are widely spread by word of mouth.
Long-term resistance to degradation. Withstanding high heats and corrosion resistance.
Less wear, less downtime. Educate plant maintenance professionals.
Better lubrication in certain applications.
Explain to purchasing and maintenance the cost savings of using the proper grease.
Better properties for specific applications, which contribute to improved reliability, while possibly reducing the frequency necessary for greasing the component.
The right application can result in a cost reduction and money savings. Clarifying the characteristics of each main kind of grease and matching them to the correct applications.
Environmental protection and energy saving requirement.
The benefits far outweigh the added costs. You can pay for the right grease in short order just by the energy savings, let alone the ROI on labor, downtime and related costs.
Temperature extremes, extended reapplication time.
Longer bearing life and less failure by using high-performance greases.
Better temperature resistance in high-temperature areas. I think advertisements in industry magazines would help promote the use of high-performance greases.
Creating grease is:
An exact science
25%
More art than science
7%
A combination of science and art
68%
Based on responses sent to 13,000 TLT readers.
Cost savings, case studies.
It stays in place longer and can withstand higher operating temperatures. High-performance greases are more cost effective in the long run.
Depends on the application. Issues such as temperature and load have a lot to do with grease selection. One additional issue that impacts grease use is the level of difficulty in maintaining the greased location. Remote and difficult applications make high performance a valuable feature.
Teach the customer and the tech/maintenance team. Explain the benefits of specialty greases on saving and increasing machine liability.
Grease lasts longer and performs better in lubrication-starved applications where regular maintenance is a problem.
Less grease lost, longer equipment life.
High-performance greases are a requirement in applications where an extreme condition exists such as temperature, moisture, load, ease of relubrication and similar situations.
Less wear, higher temperature service. Education of users, technical papers in trade publications.
Longer service life and better equipment protection.
Improved component life, reduced downtime, reduced man hours for repair and greasing.
Understanding what the term “high performance” really means.
Longer component life.
They obviously deliver greater value by working better and longer than greases produced in the price wars. I refer to “high performance” as “engineered and enhanced” and these products are formulated, blended and packaged with the best results in the forefront. With these greases you find greater wear protection, less parasitic drag on the power source and if specified correctly, they will overcome the L.E.T.S. (load-environment-temperature-speed) parameters.
Editor’s Note: Sounding Board is based on an email survey of 13,000 TLT readers. Views expressed are those of the respondents and do not reflect the opinions of the Society of Tribologists and Lubrication Engineers. STLE does not vouch for the technical accuracy of opinions expressed in Sounding Board, nor does inclusion of a comment represent an endorsement of the technology by STLE.