20 Minutes With Bill Mallory, Jr.
Rachel Fowler, Associate Editor | TLT 20 Minutes August 2015
The president and owner of Royal Mfg Co. discusses the evolution of lubricating greases, from primitive methods to modern formulation technologies.
BILL MALLORY, JR. - The Quick File
Bill Mallory, Jr., nicknamed Dr. Bill in the company, is the president and owner of Royal Mfg. Co., a 100-plus-year-old manufacturer and marketer of lubricating oil and greases. Bill attended Oklahoma State University where he studied mechanical engineering, knowledge he used to help build two world-class lubricating grease plants as well as lube blending plants, one each in Tulsa, Okla., and San Antonio, Texas. Bill has been a member of STLE for more than 50 years. Besides being a creative innovative plant designer, Bill also is a knowledgeable formulator of lubes and greases.
Bill started working for Royal Mfg Co. back in the 1950s while still in high school. He followed the footsteps of his mother and father who initially started working for Royal in the mid-1930s and later went on to purchase Royal and also Tulsa Refined Oil Co. (TROCO) and Wright Oil Co. After completing his studies at Oklahoma State, Bill continued to work for Royal, now a family-owned business.
Bill has witnessed the U.S. lube oil and grease industry grow from infancy to a state of incipient maturity. His “never ever give up” philosophy and business foresight have transitioned Royal Mfg Co. from a small oil blender to a specialized manufacturing and marketing company conducting business across the globe.
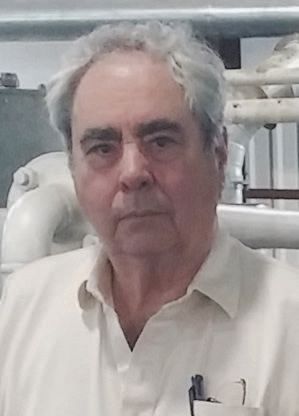
Bill Mallory
TLT: Tell us your long journey in the field of development and manufacturing of lubricating greases.
Mallory: My family’s involvement in the lubricant field started back during the Depression years where my mother (Lee) and father (Dick) started working for Royal Mfg. Co. in the mid-1930s. Later my parents bought Royal, also Tulsa Refined Oil Co. (TROCO) and Wright Oil Co. Following the footsteps and tradition of my family, I started working for Royal in the 1950s while still in high school. I went to college to pursue mechanical engineering at Oklahoma State University and continued to work in the family-owned business. My learnings from college helped me tremendously to think outside the box and pursue something I was always fascinated about.
Making lubricating grease during those early days was primitive at that time compared to current standards and typically looked like cookbook stuff. The popular greases like calcium, aluminum and sodium were made with a simple process requiring not much heat and in simple conventional mixing kettles using animal fats/residues from other processes. After World War II, the U.S., experiencing exceptional industrial growth, demanded better lubricating greases with superior performance characteristics. Lithium greases were coming into the picture and replaced current conventional greases. Then newer technologies like polyurea, calcium sulfonate, lithium complex and aluminum complex started knocking on the door. These newer technologies exhibited superior performance characteristics meeting ever-growing industry demand, but they needed more efficient equipment like larger kettle sizes with counter-rotating mixers capable of handling higher torque and increased heat. Milling and homogenizing, which were seldom used before, and pressurized vessels give better reaction, especially for lithium greases.
These challenging requirements to make these modern greases gave me the opportunity to put together a custom-made manufacturing plant in Tulsa. During this period my parents retired and I took over the responsibility of the family business. In 1976 I acquired Wright Oil Co. in San Antonio to expand our business in and around Texas and for exports. In 1989 a fire destroyed our grease plant at Tulsa, and I redesigned and rebuilt the entire plant with modern facilities, including STRATCO Contactor, Charlotte Mills and APV Gaulin Homogenizers, and with sufficient finished-grease storage capacity. In the year 2000, I built RTW Terminal in Brownsville, Texas, to enhance our base oil storage capacity and support our exports to Mexico and other Latin American countries.
In addition to my keen interest and hobby of making continuous improvements in the manufacturing plants, I wanted to develop tailor-made newly improved greases and be ahead of the curve. For example, in 1976 I commercialized
Royal 760, a superior lithium EP grease with more extreme pressure antiwear and anti-oxidation properties than other EP greases available at that time. In 1987
Royal 876 was developed and is now a series of six heavy-duty greases for the construction and mining industry plus other off-highway applications with exceptional heavy-duty performance characteristics.
During the 1960s Oldsmobile 98 reflected power and speed in the automobile industry, and therefore my newly formulated lithium complex grease’s name designed for high-speed operations was
Royal 98. In 1986, with the guidance from my buddy and mentor, Pat Scott, I started working on improving calcium sulfonate technology. The five goals assigned for this were (1.) better performance than existing lithium complex greases, (2.) improvement in existing performance, (3.) better low-temperature flow ability, (4.) long life in marine applications and (5.) developing a food-grade calcium sulfonate grease. With the aim of accomplishing these five coveted goals, the name of our calcium sulfonate grease series was identified as
Royal 865.
I have been in this industry for more than 60 years and have seen the U.S. lubricant and grease industry go through many ups and downs. However, I feel very proud that the U.S. has been the front runner in developing newer technologies, and I feel honored to have been a part of this industry for so many years and have contributed some to this success.
TLT: What fascinates you about lubricating greases?
Mallory: Lubricating grease formulating and manufacturing is entirely different than lube oil blending. Since the beginning grease making was considered an art; however, modern lubricating grease processing involves a lot of engineering and science. Industry wide, you can find many lubricating oil blenders, but there are only a handful of grease manufacturers. Lubricating oil blending is technically simple. It requires simple blends, a simple kettle without much mixing technology, just a little heat sufficient enough to mix base oil and additives. It is a physical mixing and has practically no chemical reaction involved, whereas lubricating grease formulating and manufacturing is rather complex.
Perhaps that is the reason why grease making initially was considered as art. The knowledge about reaction intricacies and effect of various process parameters on quality of resultant grease was very limited at that time. Unlike oil, grease making needs specialized equipment and processing. Our current understanding on lubricating greases indicates that it involves chemical reaction, which is highly sensitive to processing parameters like heating/cooling rates, speed and type of mixing and pressure/vacuum.
Grease manufacturing does involve phase transition and reaction in base oil in non-polar media; this is quite different than conducting reaction polar media like water with complex reaction kinetics. Conducting reaction with complexities requires very carefully engineered equipment and processing, and there is always learning in every step. All of these complexities make lubricating greases stand out from lubricating oil and other products. These challenges in lubricating greases always fascinate me and keep me involved in the field of lubricating greases.
Bill Mallory (left) and vice president Jim Gott built Royal Mfg Co. together as an established brand.
TLT: How has the lubricating grease industry evolved over time in the U.S. and across the globe?
Mallory: Lubricating greases have been used in the industry since ancient times and probably evolved concomitantly with the discovery of the wheel. Application of lubricating oil mixed with animal fat and lime had been traced to Egyptian times. Since then, until the middle of the 19th Century (though greases would have been used), there is not much information on manufacturing and applications of lubricating greases.
Discovery of crude oil in Pennsylvania spurred the use of mineral base stocks in lube oil and greases. However, grease making since then until World War II was practically a basic style of grease making. Simple mixing equipment like dough mixers and direct-filed kettles has been used to make greases. Coal and wood tar, animal fats, fish oils, pulverized mica, rosin, etc., were used to thicken oil to make journal, block and axle greases. The main purpose of using thickeners in oils was to support its stay-put characteristics.
During, and soon after World War II, there was a general realization that we need to improve our existing quality of lubricating greases in order to meet ever-growing stringent industrial requirements. During- and post-World War II eras had witnessed some exceptional growth in the U.S. Lithium-based greases were on a rise, started replacing conventional calcium and soda-based greases and were regarded as universal multipurpose greases.
The main advantage of lithium greases over other greases was that lithium greases had better high-temperature capabilities compared to calcium greases and superior water resistance compared to soda-based greases. Even with far higher temperatures, lithium complex greases emerged.
Besides this, during the period starting from World War II until close to the 20th Century, many other outstanding technologies like calcium sulfonate, polyurea, aluminum complex, clay-based, etc., came into existence. It is very heartening to note that these almost all outstanding technologies have been invented in the U.S. and are now being used across the globe. Rather than having one multipurpose grease for many applications, there is a large variety of choices for consumers to select grease for their needs.
Bill Mallory standing next to his favorite grease contactor.
TLT: Since the China lubricating grease market is growing at a fast pace and the U.S. grease market is stagnant, where do you see the future of lubricating greases in the U.S.?
Mallory: In last decade, the U.S. used to be the No. 1 manufacturer of lubricating greases. However, in the last few years, China has witnessed unbelievable precedential growth. As per the National Lubricating Grease Institute grease production survey, China accounts for more than 38% of the total worldwide production, leaving the U.S. far behind with about 18% market share. However, it’s interesting to note that lithium greases constitute about 85% of total volumes, whereas market share of lithium greases in the U.S. is only about 67%. In China, out of 85%, high-performance lithium complex greases are about 15%, and in North America out of 67%, lithium complexes are 39%. Therefore, the U.S. manufactures much more high-performance lithium complex greases compared to China.
The volumes of high-performance greases in the U.S. that include lithium complex, calcium sulfonates, polyurea, aluminum complex and clay-based greases account for more than 60% of its total grease production, whereas in China it’s about 25% only. What this indicates is that the U.S. is using more high-performance, long-life greases compared to China. It is interesting to describe here that the U.S. market used to be like China, dominated by lithium and other multipurpose greases. But in the close of the third-quarter of the 20th Century, greases gradually shifted to more high-performance long-life greases. This indicates that the North America market has achieved more maturity and is ahead of development over China and other countries.
TLT: What is the future of environmentally friendly lubricants?
Mallory: There are many misnomers across the industry and many different types of claims and rumors about what is an environmentally friendly lube.
Environmentally friendly lubricants—in my terminology—are the lubricants made out of biobased fluids like soya, canola, rapeseed or biodegradable esters, etc., using suitable additives and/or thickeners. The awareness to make and use such type of products originally started in Europe, and demand for such products in the U.S. also is now picking up. We are getting more and more queries from domestic and even other American countries like Chile, Peru, Mexico, Canada, etc.
The industries where the demand of these kinds of products is emerging are mining, drilling, agriculture, railways, forestry, etc. What I have noticed is that in recent years, having a biodegradable product in the product range is a selling point. Though the demand for such products is not huge, it has started picking up in the recent past.
The couple of reasons for their growth is improvement in quality of products and price parity between mineral oil and biodegradable products. For example, we have recently tried biobased curve rail grease, which is successfully performing equally as well, if not better than mineral oil-based grease. The more encouraging sign to promote this class of product is they are renewable, and at least we have an alternate in case mineral-based oil starts diminishing due to one reason or another.
TLT: How do you see the future of food-grade greases?
Mallory: More and more processed foods are being used globally, especially in countries like China, India and other developing countries. The demand of lubricant in this industry is growing. Earlier, mineral oil-based greases were used in this industry; however, with growing awareness among food consumers, consciousness from food-producing companies and government compliances, the industry is tending toward using food-grade lubricants and greases.
The most noticeable category where these lubricants fall for food grade are for USDA/FDA products approved by NSF H-1 and other agencies. These products are intended for incidental contact purpose. Besides this, there are a few religious organizations like Halal and Kosher that require food-safe lubricants. Also, countries like Canada and the European block have their own specifications and requirements. We are getting more and more inquiries from overseas countries like Saudi Arabia, Malaysia, India, China, etc., for food-grade lubricants than ever, an indication that the market for food-grade lubricants and greases is likely to grow.
TLT: What do you think are the future technology drivers in the field of lubricating greases?
Mallory: In the last few decades, the lubricating grease market has been dominated by lithium, lithium complex, calcium sulfonate, aluminum complex, clay-based and polyurea greases, and there has not been much new development taking place in the recent past. Clay-based and aluminum complex grease for the last few decades have been either stagnant or declining, probably due to cost, limited applications, compatibility and other commercial issues where the demand for calcium sulfonate and polyurea is growing. In Japan, polyurea greases account for more than 25% of their total greases volume. Polyurea greases are considered excellent greases for fill-for-life, constant velocity joints and high-temperature applications.
Calcium sulfonate greases are growing, especially in the U.S. due to their superior performance over more popular lithium greases. This grease also exhibits superior compatibility with others, especially lithium greases easier to change. Calcium sulfonate greases are gaining ground in mining, construction, marine and even the food industry. This class of greases are going to, in all probabilities, be the next generation multipurpose greases. The other technologies that are likely to see more importance are synthetic greases, biodegradable and food-grade greases.
I personally am putting a lot of effort into developing better greases for food-grade application, biodegradable and environmentally sensitive applications. I also am developing a wider group of calcium sulfonate thickened greases for both custom-made requirements as well as multipurpose applications.
Bill Mallory working in his office.
TLT: What are future trends in manufacturing technologies in terms of continuous process over batch process?
Mallory: I think market requirements are tending toward more customized products, which means specialized greases are being developed for specialized application, and the concept of multipurpose and universal grease for many applications is taking the back seat and is not fit for every demand.
Every industry or customer tends to demand custom-made greases, which can only be produced easily if we make grease with batch process. Continuous manufacturing process is more convenient in making lithium greases in large volume having one type of formula. Continuous manufacturing process doesn’t offer much flexibility as compared to batch process. Contactor process for making soap-based and complex soap-based greases will probably still remain important in manufacturing the lubricating greases of quality.
You can reach Bill Mallory, Jr., at billm@royalmfg.com.