A little fretting about fretting
Dr. Robert M. Gresham, Contributing Editor | TLT Lubrication Fundamentals July 2015
Jet engine manufacturers have devised tribological methods to reduce failure in their products due to fretting wear.
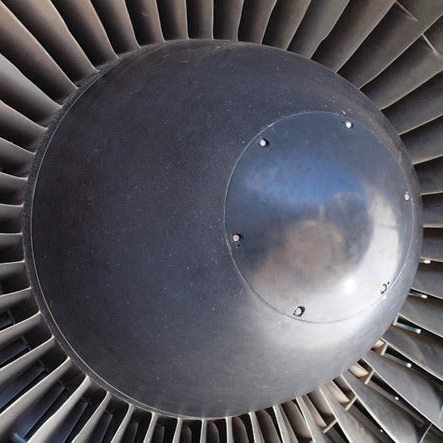
www.canstockphoto.com
KEY CONCEPTS
•
Fretting corrosion is the damage to contacting surfaces experiencing slight relative reciprocating sliding motion of low amplitude.
•
False brinelling, by contrast, is the formation of a worn depression on the raceway of a lubricated rolling element bearing due to the slight rocking of the rolling elements, maybe only a fraction of a degree.
•
Jet engine manufacturers are able to delay the rate of failure of jet engines, particularly smaller engines due to this fretting kind of wear.
TWO WEAR MECHANISMS, FRETTING CORROSION AND FALSE BRINELLING, are in some ways very similar and can cause confusion—or cause one to fret about fretting. Some people over the years have considered these two mechanisms to be the same, but in reality there are subtle differences, and the two processes can even happen simultaneously. They are both caused by small relative motions, usually due to low amplitude
vibration while the components of a machine are relatively stationary or not rotating. Indeed, one immediately envisions the difficulties in shipping cars, trucks and military equipment overseas, on ships (
see Figure 1) and across the country on intercontinental trucks, where for days, weeks or even months the vehicle or machine subtly rocks back and forth on its bearings and gears.
Figure 1. One can see the difficulties in shipping cars, trucks and military equipment overseas on ships, where the vehicle or machine subtly rocks back and forth on its bearings and gears.
Taking a closer look, fretting corrosion is the damage to contacting surfaces experiencing slight relative reciprocating sliding motion of low amplitude. Fretting corrosion is the fretting damage to unlubricated contacting surfaces accompanied by corrosion, mostly oxidation that occurs if the fretting occurs in air. Fretting corrosion of steel in air produces the red iron oxide hematite (Fe
2O
3), as shown in Figure 2, where the wear scar is surrounded by red iron oxide.
Figure 2. Fretting corrosion of steel in air produces the red iron oxide hematite (Fe2O3), where the wear scar is surrounded by red iron oxide.
False brinelling, by contrast, is the formation of a worn depression on the raceway of a lubricated rolling element bearing due to the slight rocking of the rolling elements, maybe only a fraction of a degree. Lack of movement prevents the formation of an elastohydrodynamic oil film and necessarily forces
boundary lubrication on the contact area to prevent it. The worn depressions replicate the shape and the position of the rolling elements. No sliding or skidding marks are found in false brinelling depressions. Even in Figure 3 you also might see a slight reddening, indicating some iron oxide formation on the edges and hinting that these processes could happen simultaneously in some cases.
Figure 3. In false brinelling, you might see a slight reddening indicating some iron oxide formation on the edges, hinting that these processes could happen simultaneously.
In true brinelling, the raceway is basically dented as true brinelling is the result of shock loading with little relative motion. Thus, one can sometimes even see machining marks in the dent, and the dent will occasionally have a slight shoulder due to plastic deformation of the raceway.
In my experience, we worked with jet engine manufacturers to delay the rate of failure of jet engines, particularly smaller engines, due to this fretting kind of wear (
see Figure 4). Jet engines are basically a big rotating turbine fan. Some of the fan blades—which are made from some pretty exotic metals—are static, and some are mounted on the rotator and rotate within the engine. Some of the blades are located toward the front of the engine, the compressor, which compresses air coming into the engine. Some are located toward the rear, the turbine, where the energy of combustion spins the rotator providing thrust and energy to compress more air into the engine.
Figure 4. While there are many different design variations of jet engine blades that are strong, many are subject to fretting wear due to the vibration of the engine. (Photo courtesy of E/M Products Corp.)
While there are a number of design variations, basically the blades are mounted into the stator and rotor via a tongue-and-groove arrangement analogous to the way furniture drawers are constructed. This design is very strong but is subject to fretting wear due to the vibration of the engine. And while engine manufacturers strive to minimize engine vibration, the problem is with the so-called root section of the blade (the tongue of the tongue and groove) “experiencing slight relative reciprocating sliding motion of low amplitude” against the surfaces of the slot into which it is mounted. Because these blades are not made from iron, iron oxide is not seen.
Can you imagine the consequences of wear on the root section of the blade, the part that fits into the slot, and the slot surfaces? As fretting wear continues, the root section gets smaller and the slot gets larger. Clearly one can see that if left long enough, the blade will eventually come loose and could severely damage the engine.
Engine manufacturers have developed a number of techniques for delaying failure due to this wear mechanism. In some cases, a pin is inserted through the root section of the blade to hold it in place, which adds to expense but certainly reduces risk. In other cases, like a missile engine, it only runs for a few seconds and either hits its target or misses; either way the engine is destroyed. In some cases, wear of the root sections and slot surfaces have been reduced through the use of solid film lubricants (think high-tech slippery paint-like coatings,
see Figure 5). Solid film lubricants (SFLs) are excellent boundary lubricants, probably the best there are. And, as we said above, this is fundamentally a boundary lubrication problem. These SFLs will vary themselves depending on what part of the engine they are used for. In the compressor section, where temperatures are comparatively low, conventional SFLs are used; back in the turbine section, where temperatures can be quite high, exotic ceramic-bonded SFLs are used. In each case, the job of the SFL is to lubricate the “slight relative reciprocating sliding motion of low amplitude” that results in fretting wear due to inadequate boundary lubrication.
Figure 5. Wear of the root sections and slot surfaces have been reduced through the use of solid film lubricants. (Photo courtesy of E/M Products Corp.)
Because of the work of tribologists, in conjunction with their vendors, the jet engine manufacturers are able to control the rate of failure due to this problem. And when we fly from place to place, we need not fret about fretting.
Revised from another issue of TLT. Bob Gresham is STLE’s director of professional development. You can reach him at rgresham@stle.org.