Beneath the surface: Why contact mechanics and tribology are a natural match
Jeanna Van Rensselar, Contributing Editor | TLT Feature Article July 2015
Leveraging both disciplines together can yield results neither can achieve alone.
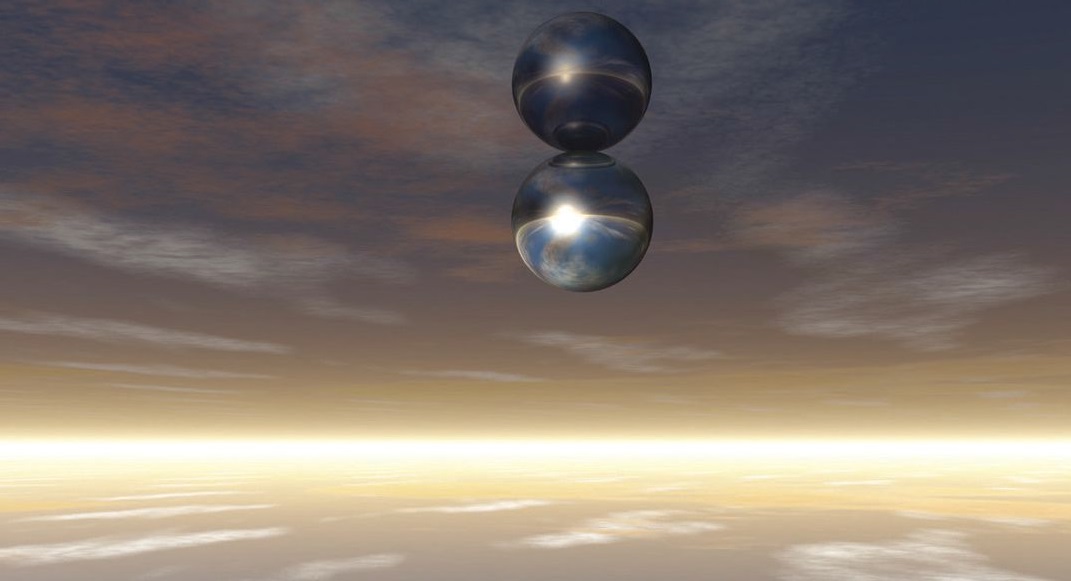
www.canstockphoto.com
KEY CONCEPTS
•
Contact mechanics is a sometimes overlooked but critical aspect of tribology.
•
Friction reduction is maximized by leveraging the dynamic between surface material engineering and lubrication engineering.
•
A textured bearing surface acts as a lubricant reservoir, storing and dispensing the lubricant directly at the point of contact where it makes most sense.
WHEN THE THEORY OF CONTACT MECHANICS WAS FIRST DEVELOPED IN 1882, lubricants were not factored into the equation at all. Experts say that may be due to the lack of powerful analytical and numerical tools that necessitated simplicity (
1). The omission of lubrication from contact mechanics theory was resolved four years later when Osborne Reynolds developed what is now known as the Reynolds Equation. It describes the pressure distribution in nearly any type of fluid film bearing.
Even with that breakthrough, however, it was decades later before contact mechanics was actually factored into tribology.
Today tribology is an integral component of contact mechanics, but contact mechanics still doesn’t have the same status in tribology. Experts say it’s time for a change.
Currently, machine elements are required to work under increasingly severe conditions such as thinner lubrication, minimum lubrication and higher temperatures. Because of this, the effect of surface topography on lubricated contacts is more relevant than ever. This is especially true for heavily loaded lubricated contacts, which are very dependent on the correct description of surface roughness and its associated behavior. Today, with the help of faster computers, better software and significantly more efficient numerical methods, it’s possible to start modeling surface failure modes in real time (
2).
CONTACT MECHANICS
Contact mechanics is the study of how solids that touch each other at one or more points change shape. Central to contact mechanics are the pressures and adhesions perpendicular to the contacting surfaces (the normal direction) (
3). Contact mechanics is a sometimes overlooked but critical aspect of tribology.
Principles of contact mechanics are applied in all tribology-related disciplines that involve the contact of one or more solid surfaces; this would include just about every discipline.
In fact, contact mechanics is one of the fundamental tools for designing bearings. It lays the foundation for raceway profile design and surface roughness specifications. For example, the profile of the rough surface needs to be considered in order to predict the minimum effective film thickness. For bearings operating in a mixed or boundary lubrication environment, contact mechanics is even more important.
Researchers are able to create coupled models that consider both the lubricant behavior and the solid contact between the rough surfaces (the relationship between lubricants and asperities); this is essential for generating a Stribeck curve (
see Stribeck Curve sidebar). This also has opened up the possibility of designing surfaces matched to lubricants (i.e., surface texturing and controlled machining).
WHY IS IT THE STRIBECK CURVE? (4)
Fundamental to both contact mechanics and tribology, the Stribeck curve is named after Richard Stribeck. Developed in the first half of the 20th Century, it defines the form of the friction curve for liquid-lubricated surfaces and is a foundational tribology element.
Stribeck performed his research at Berlin’s Royal Prussian Technical Testing Institute (now the BAM Federal Institute for Materials Research and Testing) around 1900. Similar work was previously performed at the same institute 15 years earlier by Adolf Martens and 15 years before that by Robert H. Thurston at the Stevens Institute of Technology in Hoboken, N.J.
So why is the curve attributed to Stribeck, though both Thurston and Martens achieved similar results considerably earlier? Possibly because Stribeck published in one of the most important journals for engineers at that time, Germany’s Zeitschrift des Vereins Deutscher Ingenieure (VDI). Martens published his results in the lesser known Journal of the Royal Prussian Technical Testing Institute.
But STLE-member Rob Jackson, professor of mechanical engineering at Auburn University, the only school offering a tribology minor, has this caveat, “The Stribeck curve is a popular method often employed to characterize the lubrication regime by the friction coefficient. It can be created from experimental or numerical data. If a solid surface has inherently very low friction, it may be difficult to distinguish between friction from solid contact versus lubricant shearing. It is also very difficult to generate theoretical Stribeck curves that are quantitatively correct.”
HISTORY
In 1882 Heinrich Hertz solved the contact problem of two elastic bodies with curved surfaces. He published his theory in the seminal work On the Contact of Elastic Solids and is considered the father of contact mechanics. Hertz’s solution became the foundation for contact mechanics and is still relevant today.
Hertzian contact stress usually refers to the stress close to the area of contact between two different-sized spheres. In tribology, Hertzian contact stress is the stress within pairs of parts that operate in the same system (the ball and socket of a hip replacement or rolling elements and raceways of a bearing in a gearbox). Hertzian contact stress assumes the following:
•
There is very little pressure (
5) on either sphere and the surfaces have very little yield.
•
The surfaces are continuous and non-conforming; the area of contact is a point or line.
•
Each sphere can be considered an elastic half-space.
•
The surfaces are frictionless.
So basically all this assumes that the surfaces are smooth and frictionless, that there is elastic deformation and half of each surface represents the entire sphere. So while no one would argue that Hertz’s theory is valid, its applicability was and is limited to contact between surfaces that are smooth and where the contact is lightly loaded and frictionless.
In 1970 Johnson, Kendall and Roberts discovered a similar solution for adhesive contact (meaning that the contact itself creates an adhesive boundary between the two surfaces). This theory, known as the JKR model, takes into account the contact area created by the elastic material properties plus Hertz’s interfacial interaction strength: Pressing a ping pong ball into a foam ball would increase the contact area and also create an adhesion (
6) While Hertz’s theory only takes the point of contact into account, the JKR model goes on to address what happens after the contact is made. Like the Hertzian theory, the JKR model only applies to sphere-to-sphere contact.
Shortly after the JKR model was developed, Derjaguin, Muller and Toporov developed the DMT model—which also accounts for adhesion. Both the JKR and DMT models still are used today, and both are still valid. The difference is that each model is more applicable to certain materials. The trick is determining which model to use—another field of study in itself.
In the 1950s Bowden and Tabor were the first to take into account the importance of surface roughness for bodies in contact—this is the point of intersection for contact mechanics and tribology. Bowden and Tabor postulated that, because of positive and negative surface asperities (protrusions and cavities), the
actual contact area is less than the
apparent contact area; the degree of contact reduction is proportional to the degree of roughness. Also in the 1950s, Archard added the dimension of force to the equation. And in 1966, Greenwood and Williamson produced the first practical, engineering-oriented asperity model for contact mechanics.
So while Hertz laid the foundation for contact mechanics, Johnson, Kendall and Roberts; Derjaguin, Muller and Toporov; Bowden and Tabor; Archard; and Greenwood and Williamson made Hertz’s theory significantly more relevant.
Timken Co. scientist and ASME Fellow Xiaolan Ai explains, “Numerical simulations have come to a stage where they can take any digitized surface profile into consideration and study the effect of roughness under more realistic conditions. However, experimental studies are not quite up to modern standards.”
CONTACT MECHANICS AND BEARINGS
Part of the reason that Hertz failed to take asperities into account was the crudeness of microscopes in the late 1800s. If a surface looked smooth under the most powerful microscope, one could assume that it actually was smooth. In actuality, most bearing surfaces are rough at today’s microscopic levels and nearly all are rough at the nanoscopic level.
Jackson says, “Surfaces are now known to possess features over many different scales. This means that there are small features or asperities on the larger ones. This continues all the way down to the atomic scale. They are then often characterized using fractals or spectral mathematics. It is very difficult to determine the effect of these multiple scales of roughness features on lubrication.”
When two bodies come into contact, it’s the positive asperities that touch. Thus, the real area of contact is significantly lower than the geometrical contact area (JKR/DMT models). But as the asperities become bigger and greater in number, the contact stress increases. So asperities equal less contact area but more stress. Because of this, it’s important to determine the spatial pattern of peaks and valleys in addition to the height variation. All of this makes the accurate measurement of bearing asperities extremely important to contact mechanics and by extension, lubrication.
Ball bearings are common subjects of contact mechanics for a number of reasons, not the least of which is that the contact area and stresses are relatively simple to determine.
Ball bearings are typically loaded against the conforming grooves in the inner and outer raceways. For radially loaded ball bearings (where the ball is loaded against the conforming grooves in the inner and outer raceways), the contact between the ball and either the inner or outer raceway will be elliptical. Determining the radii (ball radius, groove radius and radius of the contact track) is straightforward. Assuming that the load carried by a roller bearing is distributed among the individual balls. The load and the contact radii can then be used to determine the contact area and stresses.
THE RELATIONSHIP BETWEEN CONTACT MECHANICS AND LUBRICATION
Excessive contact stress or deformation can lead to bearing failure through:
•
Overload. Components either break apart or fracture from the contact load.
•
Wear. Material is removed from the contacting surfaces, usually through abrasion (
see Stages of Wear sidebar).
•
Rolling contact fatigue. Cyclical contact stress may cause fatigue cracks.
•
Seizure. The surfaces weld due to high contact stress (usually high heat).
•
Loss of tolerance. Usually the result of excessive or repeated deformation of the components.
STAGES OF WEAR
Per basic materials science, the wear rate of contacting surfaces normally goes through three stages:
1.
Run-in. Surfaces are adapting to each other—so the wear rate is difficult to predict. This stage can last longer than either of the two stages that follow—it depends on the materials and the degree of deformity.
2.
Steady state (also called secondary or mid-age). At this point the two surfaces have adapted to each other and are exhibiting a steady rate of wear; the wear rate is fairly predictable. This stage will continue until just before one or both of the contacting surfaces fail. Most of the components’ operational lives occur in this stage. The duration of this stage is affected by severe environmental and operating conditions such as higher and lower temperatures, load, stress and sliding speed. The lubricant also is a major determinant of the duration of this stage.
3.
Catastrophic (also called tertiary or old-age). The components rapidly fail due to either a single catastrophic event or rapid aging.
One of the primary functions of lubrication is to reduce or eliminate each of these friction-induced situations. But bearing friction also can be reduced by the shape, material and surface of the bearing. Friction reduction is maximized by leveraging the dynamic between surface material engineering and lubrication engineering (
see Frictional Mechanics sidebar).
FRICTIONAL MECHANICS (7)
Contact mechanics includes compressive, adhesive and frictional forces, but tribology is mostly concerned with
frictional mechanics, which is a subdiscipline of contact mechanics. It’s the study of the deformation of objects in the presence of frictional forces.
•
At the macroscopic scale, it applies to the observation of contacting objects in motion (a baseball bat contacting a ball).
•
At the intermediate scale, it applies to the local stresses, strains and deformations of the contacting objects in and near the contact area in order to validate macroscopic contact events, or investigate wear and damage of the contacting objects’ surfaces (examining the surfaces of the bat and ball post-contact).
•
At the microscopic and nano scales, frictional mechanics increases the understanding of tribological systems and adds to the friction knowledge base.
www.canstockphoto.com
Jackson says, “Surface roughness is extremely important in determining the required thickness of a lubricant film. One of the main requirements in bearing design is to make sure that the film thickness is large enough so that the surface peaks are not in contact. If there is contact wear, micropitting can occur. The general rule is to have a thickness in order of magnitude larger than the roughness of the surface. However, there is some debate as to what is the actual limit. Depending on the rough surface contact model, this minimum thickness could be between one to six times the roughness. The roughness is also a fairly simplistic surface parameter, and other quantities such as spectral amplitude, skewness and kurtosis could also be useful (
8).”
ENGINEERING BEARING SURFACES TO ENHANCE LUBRICATION
Surface engineering, as a method for improving the friction and lubrication performance of mechanical components, is a relatively new direction for tribology. It improves the performance of load-bearing surfaces in hydrodynamic lubrication by mathematically formulating an optimum texture, which is then etched, stamped or simply machined onto the bearing surface (or the mold). Engineered surface textures are usually in the form of positive and negative asperities of a specific size and geometric pattern.
Considering that it’s generally the properties and characteristics of a surface—not the bearing as a whole—that determine system performance, surface engineering has proven to be a cost-effective performance improvement.
Guillermo E. Morales-Espejel, principal scientist for SKF’s Engineering and Research Centre in the Netherlands, explains, “In the lubrication of lightly and heavily loaded contacts like sliders and rolling bearings, roughness and micro-geometry (
9) in general are very important to the understanding of real surface behavior. Apart from locally modifying the film thickness and surface separation, micro-geometry plays an important role in surface fatigue and surface life.”
He adds, “Phenomena such as surface distress (micropitting), scuffing and wear are substantially influenced by the surface micro-geometry. In the case of heavily loaded contacts (gears, roller bearings), the research on mechanical effects of micro-geometry is very advanced (e.g., elastic-plastic deformation, temperature calculation, contact area fraction, hydrodynamic pressures, material in-homogenates and even surface fatigue). This also includes rheological effects from the lubricant and sliding. In the case of mechanical effects, very fast models are needed to simulate the evolution in time and the fatigue damage accumulation, since millions of cycles must be modeled.”
Coatings and surface treatments. Surface engineering technologies span a range of coatings and surface treatments that combat friction, prevent corrosion and reduce wear.
A straightforward method for reducing wear on bearings is to increase the hardness of the surface. This can be achieved through processes such as hard-anodizing. Hard coatings also can be used to prevent fretting (degradation caused by cyclic rubbing).
Diffusion processes (like case-hardening) broadcast elements such as nitrogen and carbon into the surface. High-energy processes, beyond the limits of traditional diffusion techniques, incorporate ions to increase the relative atomic amount of nitrogen/carbon in the surface layer.
Surface texturing. Surface engineering techniques and lubrication can be synchronized to further improve bearing properties. A textured bearing surface acts as a lubricant reservoir, storing and dispensing the lubricant directly at the point of contact where it makes most sense.
Benefits of surface texturing include:
•
Reducing the coefficient of friction
•
Reducing seal leaks
•
Improving load-carrying capacity
•
Reducing metal-to-metal contact
•
Lower operating temperatures
•
Improved performance
•
Lower running costs
•
Longer service intervals.
The design as well as the direction of the surface texture will affect the performance of tribological components (both bearings and lubricants).
The texture is a well-defined (usually micro-dimpled) pattern on components like bearings. Other shapes include squares, triangles, circles, crosshatches, rectangles, hexagons, a fan of straight lines and curved lines.
Ai explains, “Surface texturing could also lead to noticeable contact pressure fluctuations, which may have adverse effects on rolling contact fatigue. Thus selecting a right surface texture for a right application is by no means an easy task.”
The most favorable pattern is the result of careful research and complex modeling. The main challenge is to determine the optimum value of key dimensions between various geometrical parameters of the surface for a particular bearing operating in a particular set of conditions. These geometrical parameters are length, width and depth of the texture; the distance between texture such as pitch, array and angle; as well as density and orientation of surface textures. The various techniques that can be employed for surface texturing include:
•
Photolithography
•
Laser surface texturing
•
Etching (wet and dry)
•
Mechanical indentation (micro-pits)
•
Abrasive jet machining
•
Vibro-mechanical texturing (
10).
For roller bearings, which are getting progressively smaller and are operating under conditions of increasing speed and load, the role of surface engineering is becoming increasingly important.
Morales-Espejel says, “The main deficiencies in theoretical predictions are related to physical/chemical aspects, the real behavior of the lubricant at the nano-metric scale, the effect of tribolayers (including micro-slip) on the surface walls, wet-ability effects and the wet-ability history. The micro-geometry is constantly evolving during running conditions. With the proper understanding of surface micro-geometry effects in lubrication and surface life, better tools can be developed for life predictions of machine elements by separating out the surface from the subsurface; this is what we are doing in rolling bearings.”
CONCLUSIONS
Morales-Espejel has come to the following conclusions about the current and future state of contact mechanics and tribology:
1.
Micro-EHL (elastohydrodynamic lubrication) concepts and models are now being used not only to understand the simple interaction of fluid and surface, but also as a tool to model the service life of mechanical components (
see Mixed EHL sidebar).
2.
The inclusion of local material behavior in micro-EHL, when it comes to pressure and clearance calculations and assessment of damage, is something that is beginning to be addressed by the scientific community.
3.
Despite what is written in the literature, the mixed lubrication problem needs to be properly solved, bringing together an understanding of physics and engineering.
4.
Promising future developments in molecular dynamics and computational chemistry may help to clarify the mechanisms behind lubricant film rupture, wall slip and friction, nano-wear, tribolayer build-up and destruction, etc. (
12)
MIXED EHL
EHL (elastohydrodynamic lubrication) refers to the full film formation that is enhanced by surface elastic deformation and the resulting increase of lubricant viscosity due to high pressure. There are situations where both boundary lubrication and full film lubrication are key factors in the lubrication of the contacting objects. The lubrication regime between boundary and elastohydrodynamic lubrication is termed
mixed EHL (or partial EHL). Mixed EHL deals with the simultaneously occurring solid-to-solid contact and elastohydrodynamic lubricated contact. The prevailing theory is that if the average film thickness is less than three times the composite surface roughness, the surface asperities will force direct solid-to-solid contact, resulting in mixed-EHL (
11).
Rob Jackson, professor of mechanical engineering at Auburn University, explains, “A great deal of progress has been made toward including roughness in the prediction of hydrodynamic lift. For the elastohydrodynamic regime encountered in rolling element bearings and gears, this has received more attention lately due to the problem of micro-pitting. Micro-pitting has been a major issue in wind energy applications.”
www.canstockphoto.com
Timken Co. scientist and ASME Fellow Xiaolan Ai adds, “I believe the work on molecular dynamic simulation on lubricated contacts will help us to better understand mix mode lubrication contact. In a broader sense, it may help us to redefine the very fundamental concept of
contact.”
Ai adds, “In the area of lubricated contact, theoretical predictions of film thickness and contact pressure are very accurate and match well with experimental results. However, when it comes to friction or traction predictions, there is still a ways to go before high fidelity predictions can be obtained.”
Jackson believes that multiple surface feature scales and how the properties change with scale will receive more attention in the near future. He says, “Several researchers are already looking into this using molecular dynamics, but it is extremely difficult to measure experimentally. The mechanical properties of the surfaces can also effectively change with scale; a small asperity on the surface can be much harder than its bulk material properties.”
REFERENCES
1.
From
Elastohydrodynamic Lubrication: A Gateway to Interfacial Mechanics—Review and Prospect, by Dong Zhu and Q. Jane Wang, Transaction of the ASME, Vol. 133, Oct. 2011. Available
here.
2.
Information in part from “Surface roughness effects in elastohydrodynamic lubrication: A review with contributions,” by Guillermo E. Morales-Espejel,
Proceedings of the Institution of Mechanical Engineers, Part J: Journal of Engineering Tribology, 2014, 228: 1217. Originally published online Dec. 9, 2013.
3.
Contact mechanics also includes the tangential frictional stresses between the surfaces.
4.
From Wikipedia entry Tribology. Available
here.
5.
The pressure is lower than the pressure required for the surface to yield.
6.
Adhesion is roughly defined as the force required to separate two bodies in contact with each other.
7.
From Wikipedia entry Frictional Contact Mechanics. Available
here.
8.
Kurtosis refers to the sharpness of the peaks.
9.
Waviness, roughness, indentations.
10.
From
Study on Effect of Surface Texture on the Performance of Hydrodynamic Journal Bearing (sic), by Krishan Kumar Gupta, Raj Kumar, Harendra Kumar and Medha Sharma. Available
here.
11.
From Mixed EHL Lubrication, Purdue University. Available
here.
12.
From “Surface roughness effects in elastohydrodynamic lubrication: A review with contributions,” by Guillermo E. Morales-Espejel,
Proceedings of the Institution of Mechanical Engineers, Part J: Journal of Engineering Tribology, 2014, 228: 1217. Originally published online Dec. 9, 2013.
Jeanna Van Rensselar heads her own communication/public relations firm, Smart PR Communications, in Naperville, Ill. You can reach her at jeanna@smartprcommunications.com.