Hydraulic fluid efficiency in construction equipment
Jeanna Van Rensselar, Contributing Editor | TLT Feature Article June 2015
Demand has increased for high-performance hydraulic fluids in the marketplace.
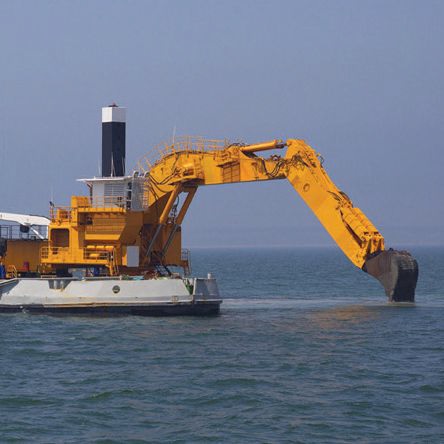
www.canstockphoto.com
KEY CONCEPTS
•
Hydraulic construction equipment makes up 76% of the hydraulic equipment market, endures greater mechanical stress and operates in harsher conditions than its industrial counterparts.
•
Simple but often-overlooked measures such as choosing the correct fluid, thorough monitoring and proper maintenance immediately improve hydraulic system performance, especially for construction equipment.
•
New multigrade hydraulic fluid formulations that improve energy efficiency are on the market. More research is underway.
PEOPLE LEAVE YOU OUTSIDE 24/7. It’s 80 degrees below zero, and you have to bore holes through 12 feet of arctic ice. It’s 130 degrees above zero and you are moving trusses for an oil platform in the middle of a dust storm. It’s hurricane season and you are in the ocean, 400 feet offshore pounding in pilings for a wind turbine. You are a piece of hydraulic construction equipment and you have been working like this pretty much non-stop since you first rolled off the skids.
As far as internal and external working conditions go, there is no comparison between the demands on hydraulic construction equipment and indoor industrial hydraulic equipment. The same goes for the hydraulic fluid for each application. Most construction equipment requires a lot more energy to operate than industrial equipment—so it’s not surprising that OEMs, hydraulic fluid formulators and researchers are taking a hard look at how hydraulic fluid can contribute to energy efficiency.
The fact that hydraulic fluid serves a number of functions makes it a prime candidate for increasing energy efficiency—this is especially true in construction equipment, which comprises 76% of the total hydraulic equipment market (
1). Because of the sheer size and power requirements, it’s not surprising that the competitive advantage of fluid power over electro-mechanical power is also greatest in this market.
Hydraulic fluid is a lot more than diluted engine oil (which has been used as a substitute). Its functions, which extend far beyond lubricating critical components, include:
•
Power transmission
•
Providing a seal
•
Maintaining pressure
•
Transferring heat
•
Preventing corrosion.
What’s missing from this list is
improving energy efficiency.
Hydraulic base fluid options include petroleum/mineral oil, synthetic hydrocarbons, biobased oils and water/oil emulsions. Today’s typical hydraulic fluid is mineral based with 0.3%-0.8% zinc-based antiwear additive (ZDDP). If this looks familiar, it’s because the formulation has been around for more than 40 years. In the last 30 years, engine oil has been significantly reformulated to improve energy efficiency, but hydraulic fluid is pretty much the same.
Hydraulic fluid power is preferred over electromechanical drives in high-power mobile equipment due to its superior energy density, design flexibility and value. It is also a relatively mature technology and ripe for innovation—a blue ocean market for researchers like Chevron and Evonik.
STLE-member Nathan Knotts, lead research scientist at Chevron Lubricants, explains, “Historically the fluid is one of the last areas to focus on when developing the equipment and has been viewed as a commodity. But results show that fluids can be developed to improve overall equipment performance—and with that improve the overall efficiency of the system and increase productivity. These fluids have been a focus area over the past few years and will continue since the off-highway segment is now in the spotlight for reducing emissions and improving overall fuel economy.”
There are only two ways to improve energy efficiency in hydraulic equipment:
1.
Alter the mechanics
2.
Alter the fluid.
HYDRAULIC FLUID IN CONSTRUCTION EQUIPMENT
Hydraulic equipment is usually classified as either mobile or stationary (
2). But since the vast majority of mobile hydraulic equipment is used in the construction industry, the terms
mobile and
construction are often used interchangeably (
3). Of all the hydraulic systems in the world, only 24% are in stationary/industrial applications. The rest are in construction equipment, which breaks down as follows:
•
22% excavators (
4)
•
18% load-carrying construction machinery
•
13.5% cranes
•
13.5% loaders (move aside or load material)
•
13% agricultural, forestry and municipal machines
•
8% concrete mixers, concrete pumps and related-truck applications
•
5% forklifts
•
7% other (
5).
Unlike engine oils, there are no universal specifications for hydraulic fluid (
6). Each OEM specifies the type of hydraulic fluid and viscosity grade that is best for its equipment. Considerations for fluid specification typically include:
•
Load
•
Pump type
•
Applications
•
Internal operating conditions
•
External operating conditions.
CONSTRUCTION EQUIPMENT DEMANDS
Paul Michael, research chemist at the Milwaukee School of Engineering, explains, “In all hydraulic machines, an internal pressure wave is transmitted through the fluid each time the payload is engaged. In construction applications, the dynamic load is unpredictable, and high-pressure excursions, or spikes, can initiate wear and stress the fluid.” In addition to power spikes, there are four other reasons that hydraulic construction equipment has a harder life than its industrial counterparts:
•
Smaller reservoirs. Because construction equipment is constantly moving, reservoirs need to be lighter and smaller than in industrial equipment. This puts stress on the system and increases contaminants.
•
Cooling capacity. Cooling systems in hydraulic equipment used for construction also tend to be smaller. This means that the cooling system may not be capable of maintaining the recommended temperature range—this is especially true if the equipment is operating in a high-temperature environment.
•
Operating environment. Typical construction sites are dirty, dusty and exposed to precipitation and temperature extremes.
•
Operating pressure. Construction equipment tends to run at higher operating pressures—sometimes higher than the OEM-recommended max pressure.
“Mobile equipment has additional challenges that differ from plant manufacturing equipment,” Knotts explains. “It has to operate in a variety of conditions and varying applications or job functions. Weather does have a big impact on the system and the demands it places on the fluid. There is a higher risk of contaminates entering the system as well. The overall size of the system and time to deal with contaminates differs between construction equipment and manufacturing equipment. In a manufacturing setting, the reservoir size is magnitudes larger to allow for adequate cooling and time for particles and water to settle out—longer cycle times. It is just the opposite in construction equipment where the trend is to reduce overall weight and the size of the reservoir. This limits hydraulic fluid volume and cooling capabilities—the fluid is hotter with less time in the reservoir.”
FLUID FORMULATION
There are two main considerations for hydraulic fluid that have a bearing on energy efficiency—the viscosity grade and the hydraulic fluid type. As mentioned earlier, these specifications are typically determined by type of hydraulic pump, operating temperature and pressure ranges. Other considerations are base oil, lubricant quality and additives.
BASE OILS
There are four primary base oil categories:
•
Petroleum/mineral. Petroleum-based fluid that includes an additive package is the most widely used. These fluids cost less than synthetics and can equal synthetics in performance.
•
Synthetic. A full synthetic fluid will provide excellent fluid stability, lubricity and other performance-enhancing characteristics. These fluids are a smart choice where high or low temperatures are present and/or high pressures are required. There are some disadvantages to these fluids including high cost, toxicity and potential incompatibility with certain seal materials.
•
Biobased. When compared with mineral and synthetic-based fluids, advantages include lower-toxicity, higher flash and fire points and higher lubricity. Disadvantages include poor oxidation resistance, low-temperature performance and significantly higher cost.
•
Water-based. These fluids are used in applications where there is a high risk of fire. They are more expensive than petroleum but less expensive than synthetics. Because of the water content, they offer good fire protection but lack wear protection.
ADDITIVES
Viscosity is the most important consideration for selecting hydraulic fluid. But fluid properties other than viscosity can have a profound effect on hydraulic system efficiency.
While base oils provide physical and chemical properties, additives and base oils combined provide performance.
Viscosity Index (VI) Improvers. High temperatures are the enemy of stable viscosity. As temperatures rise, the fluid thins, creating metal-to-metal contact in extreme cases. This strains and contaminates the pump. Poor viscosity resulting from high temperatures creates a destructive cycle of rising temperatures, increased wear and internal leakage.
But low-viscosity conditions during cold start-up are an issue as well. Viscosity variations associated with both low-starting temperatures and high-operating temperatures contribute to system inefficiency and unreliability. Viscosity selection factors include:
•
The minimum-expected cold-cranking temperature
•
The maximum-expected operating temperature
•
The OEM-specified viscosity range for the system’s components.
Detergent Additives. System cleanliness is extremely important for hydraulic fluids. Detergent additives emulsify water, while dispersing and suspending sludge, varnish and other contaminants. While this keeps components free from deposits, contaminants won’t settle and must be filtered out. This is fine for hydraulic systems in construction equipment since contaminants in these systems tend not to settle out anyway (because of the smaller reservoirs). But because of the emulsifying properties, water stays in the fluid, breaks down the oil and wreaks havoc on the components. This can all be avoided by monitoring and mitigating the water content.
Antiwear Additives. Antiwear additives maintain lubrication under boundary conditions. The most common antiwear additive for hydraulic fluid is ZDDP. Stabilized ZDDP is an essential additive for fluid in high-pressure, high-performance hydraulic systems.
Knotts says, “I see increasing demand for high-performance hydraulic fluids in the marketplace. Drivers revolve around differentiating products between suppliers as well as OEM demand. The OEMs are asking for and establishing multitiered product lines to offer their customers more choices and to participate in warranty programs. These drive changes for increased performance in areas of longer drain intervals, efficiency gains, wider-operating temperatures, system cleanliness, etc.”
FLUID SELECTION FOR ENERGY EFFICIENCY
Price and basic performance standards are still the primary purchase considerations for most hydraulic fluids. But this is changing. More end-users are considering the impact of viscosity on energy efficiency.
Thomas Schimmel, Evonik’s global business director for hydraulic fluids, explains, “Primary considerations for selecting viscosity index (VI) improvers include chemistry and sheer stability. A VI improver for hydraulic fluids should be made of polymethacrylate because this guarantees good filterability. Olefin copolymers are inferior in this regard. Filterability is one of the most important properties of hydraulic fluids. Also, only polymethacrylates allow for fine-tuning of their polarity and therefore can be tailor-made to provide the optimum performance in a variety of base oils. As far as shear stability, all VI improver manufacturers offer VI improvers in a wide range of molecular weights. Evonik’s work over the last decade has shown that only shear stable VI improver additives deliver maximum performance, measured as hydraulic power and efficiency.”
He adds, “The fluid viscosity seen by the hydraulic pump is different from the fresh oil viscosity that is mentioned on the technical data sheet of the hydraulic fluid. This is due to temperature, pressure and shear stress. All three parameters vary widely under operating conditions. At Evonik we have focused our work on the effect of VI improvers on efficiency. A high-performance hydraulic fluid can influence viscosity index and shear stability. A shear stable fluid shows significantly less viscosity loss when shear forces are applied and, hence, there is higher volumetric efficiency” (
see sidebar titled Viscosity’s Catch-22).
VISCOSITY’S CATCH-22 (7)
Volumetric (leakage flow) efficiency and hydro-mechanical (friction) efficiency are the two elements of hydraulic efficiency. The overall efficiency of a hydraulic pump is the product of both factors, and both must be considered when selecting viscosity.
The Catch-22 is that as fluid viscosity increases, volumetric efficiency tends to increase while hydro-mechanical efficiency tends to decrease. However, at high temperatures, the rate of change in volumetric efficiency is greater than the rate of change in mechanical efficiency. As a result, additives such as VI improvers that stabilize high-temperature viscosity can improve the overall efficiency of equipment that runs hot.
OEMs are working with hydraulic fluid formulators to optimize performance during the design stage in order to meet fuel economy, tailpipe emission and vehicle performance objectives. This higher level of integration—where hydraulic components and fluids are optimized for efficiency and performance—is thanks (at least in part) to the Center for Compact and Efficient Fluid Power (CCEFP) (
see sidebar titled The CCEFP).
THE CCEFP
The Center for Compact and Efficient Fluid Power (CCEFP) is a network of researchers, educators, students and industries focused on changing how fluid power technology is researched, applied and studied. Established in June 2006, the CCEFP is a National Science Foundation (NSF) Engineering Research Center. In addition to its grant from NSF, the center is supported by 55 industrial partners and seven participating universities. A team of faculty from the universities—each with distinguished academic records and interests that are unique and cross-disciplinary—is engaged in work on research projects and test beds.
While research is ongoing in a variety of areas, field trials and laboratory testing demonstrate that shear stable multigrade hydraulic fluids and friction modifiers improve energy efficiency in hydraulic systems.
The extent of efficiency improvement depends upon the equipment type, system architecture, duty cycle, operator skill and fluid properties. To help ferret out some of this complexity, the National Fluid Power Association (NFPA) recently formed an ad hoc committee on energy efficiency under the leadership of ISO TC131 chairman John Berninger of Parker Hannifin.
This group is working toward the development of ISO standards for rating the energy consumption of hydraulic components and systems. The group has identified several areas where the current ISO 4409 method for performance testing of pumps and motors could be improved. In addition, it has determined that identifying realistic duty cycles for mapping machine losses and efficiency is a priority.
The ISO 4409 standard describes procedures for measuring the efficiency of hydraulic pumps and motors. Motor vehicles are not rated in terms of efficiency percent but, rather, in miles per gallon. This is because efficiency does not accurately predict fuel consumption. For example, a moped is less efficient than a passenger vehicle, but it uses a lot less fuel.
The NFPA’s efforts to create standards that link equipment performance to machine duty cycles is intended to help the formulators of high-efficiency hydraulic fluids and the OEMs that specify them quantify the impact on energy consumption.
MONITORING AND MAINTENANCE
There are three monitoring and maintenance tasks that are often either overlooked entirely or performed so poorly that they negatively affect system performance.
Controlling Contamination. Every hydraulic system has the following basic components:
•
Fluid reservoir
•
Pump
•
Control valves (pressure, flow/volume and directional)
•
Fluid transfer piping
•
Actuator—hydraulic motor, cylinder
•
Hydraulic fluid
•
Filters
•
Coolers, accumulator, seals and gauges (
8).
To achieve a high degree of reliability, contamination control in every component is essential. Fundamentally the efficient transmission of hydraulic fluid power requires separation of high- and low-pressure zones within the hydraulic system. To maintain the integrity of the narrow moving gaps within hydraulic pumps, valves, cylinders and other components, the fluid must be kept extremely clean.
Most of the particle contamination enters the system through openings in the reservoir (lids and breather vents) and through the oil seals on hydraulic cylinders (
see sidebar titled The Effects of Contamination). Particles can be reduced with better seals and filters.
Water is the second most destructive contaminant in a hydraulic system. It can be controlled with sealed systems designed to prevent water from entering and forming in the first place (
9).
THE EFFECTS OF CONTAMINATION (10)
Fluid contamination damages a hydraulic system in two ways.
1.
Reduction in system efficiency. Machine productivity and efficient hydraulics go hand in hand. If a hydraulic system isn’t performing at peak efficiency, performance is compromised. Efficiency losses usually occur slowly and can reach 16%-20% before the operator detects a loss in performance. These efficiency losses can increase fuel consumption.
2.
Accelerated component wear. 75%-85% of hydraulic pump, motor, cylinder and valve failures can be traced to contamination. Due to the extremely small clearances in today’s hydraulic systems, particles can damage pumps, motors, cylinders and valves in the form of abrasive, adhesive and fatigue wear.
More recently, significant effort has gone into improving the cleanliness of hydraulic systems. Now equipment manufacturers use assembly practices that minimize the amount of built-in contamination. They also have implemented roll-off cleanliness specifications to improve equipment reliability and minimize warranty claims. High-efficiency filters also are used routinely in hydraulic equipment. These filters capture particles that are generated in the hydraulic system and reduce the effects of external contaminants.
Assessing Pump Efficiency. A pump’s efficiency can be significantly reduced before it reaches the end of its life. Among the problems contributing to inefficiency are the following:
•
Internal leaks
•
Piping deterioration
•
Valve losses
•
Poor monitoring and maintenance.
That reduction in efficiency often goes undetected because of the closed nature of hydraulic systems. Regular, comprehensive efficiency tests on all system components—especially the pump and motor—can determine energy efficiency and identify areas for improvement.
Monitoring the Reservoir. The reservoir can tell a lot about the health of the fluid and the system. Excessive buildup of varnish and sludge on the side of the reservoir may indicate poor fluid maintenance (
11). These deposits can adversely affect pump performance. Varnish and sludge deposits also will act as insulators that increase the system temperature (
12). Varnish also will coat valves and actuators and cause sticking, leading to poor lubrication and wear (
13).
In the end, to increase energy efficiency in hydraulic construction equipment, it’s first things first. In addition to poor monitoring and maintenance, Schimmel adds, there are two preventable causes of energy loss in hydraulic systems:
1.
Idling. This is responsible for up to 30% of losses. It is prevented in state-of-the-art equipment where pumps and motors automatically shut down when not needed. However, older equipment doesn’t have this functionality.
2.
Using the wrong fluid. Evonik’s market research has shown that up to 40% of all end-users of hydraulic equipment do not follow the recommendations for the lubricant. The results can be manifold: wrong fluid type (use of engine oils and automatic transmission fluids instead of hydraulic fluids), wrong viscosity grade (too low or too high) and monograde fluids when multi-grade fluids are required.
“The reason is lack of awareness or a misguided desire to simplify the inventory (one oil instead of three or more),” says Schimmel. “Any improper hydraulic fluid causes a decrease of efficiency and therefore an unnecessary conversion of mechanical energy into heat. The result can be as extreme as overheating and forced shutdown. In any case it leads to a higher consumption of fuel or electrical energy.”
Schimmel concludes, “The simplest ways to increase efficiency in hydraulic systems include changing from monograde hydraulic fluids to hydraulic fluids with a high viscosity index and good shear stability, changes in the engineering and design of hydraulic systems, switching off pumps and motors when not needed, load sensing systems, etc.”
REFERENCES
1.
From Hitachi’s
Modern technologies in hydraulic power system for construction machinery and requirement for hydraulic fluids. Available
here.
2.
Sets of terms include mobile/stationary, construction/industrial and even outside/inside.
3.
Chevron points out that mining, agriculture, quarrying, waste management and cement industries all use mobile equipment.
4.
Per Thomas Schimmel, excavators contribute 50% of CO
2 emissions.
5.
Reflects 2001 sales of BoschRexroth pumps. From Hitachi’s
Modern technologies in hydraulic power system for construction machinery and requirement for hydraulic fluids. Available
here.
6.
Per Thomas Schimmel; DIN 51524 roughly compares to SAE J300 for engine oils.
7.
From
Hydraulic Systems Take Center Stage, by Jeanna Van Rensselar, TLT Jan. 2011.
8.
From STLE’s Basic Handbook of Lubrication, Third Edition;
Hydraulics Fluids & Related Properties by David L. Banks.
9.
Ibid.
10.
From Caterpillar PDF: Cat® Hydraulic Systems Management Guide. Available
here.
11.
Varnish and sludge are the results of the chemical reaction of water, air and the fluid at elevated temperatures.
12.
The rate of oxidation doubles for each 10 C (18 F) rise in temperature.
13.
From STLE’s Basic Handbook of Lubrication, Third Edition;
Hydraulics Fluids & Related Properties by David L. Banks.
Jeanna Van Rensselar heads her own communication/public relations firm, Smart PR Communications, in Naperville, Ill. You can reach her at jeanna@smartprcommunications.com.