Gecko’s feet and sticky tape
Drs. Wilfred T. Tysoe & Nicholas D. Spencer | TLT Cutting Edge June 2015
Simple mechanical models reveal how a gecko's feet are released, allowing it to walk.
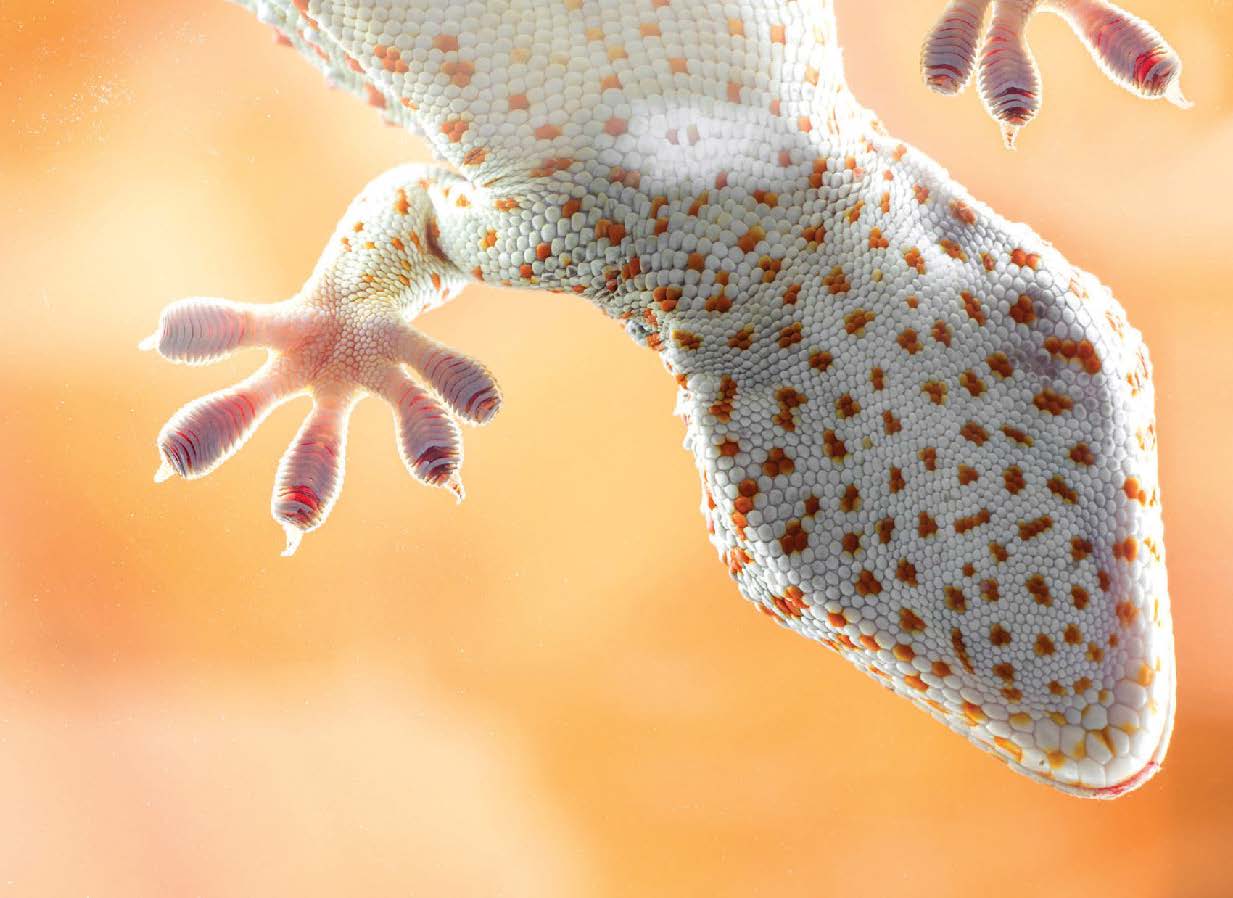
www.canstockphoto.com
A LARGE NUMBER OF CREATURES—FROM BEETLES TO FLIES AND SPIDERS—have the remarkable ability to walk on vertical surfaces. The largest of these, and thus the most interesting, is the gecko (
Gekko gecko) (
1). This ability is achieved by a foot that has a complex, hierarchical structure as shown in Figure 1.
Figure 1. Hierarchy of structures on a gecko toe. (Reproduced with permission from PNAS (2).)
At the highest length scale, each toe has a series of ridges that comprise a mass of tiny hairs, or
setae, that are made from keratin—the same substance as in fingernails. The ends of the
setae terminate in multiple branched, flattened structures known as
spatulae. Each has a shaft about one micron long with a flattened end that is only about 200 nanometers wide and about five nanometers thick (a nanometer is one billionth (10
-9) of a meter). This provides intimate contact between the ends of the
spatulae and the surface, which interact through relatively weak and short-range van der Waals interactions. However, the large number of such interactions leads to strong adhesion between the gecko foot and the surface; it turns out to be quite difficult to pull a gecko from a flat surface.
While this model nicely explains how geckos stick to surfaces, the animals also have to break this strong adhesive contact to be able to walk. The gecko can do this as quickly as it takes to make the contact—in about 20 milliseconds.
How geckos manage this has been explored by Professor John Williams of the University of Cambridge. He argues that the problem of releasing the gecko
spatulae from a surface is analogous to that of releasing an adhesive tape from a surface by pulling its end. Here, as might be expected, the force required to remove the tape depends on the angle at which it is pulled. Pulling at angles closer to perpendicular to the surface needs a smaller force than when pulling parallel to it.
However, in the case of the gecko, the situation is somewhat more complicated since each adhering
spatula tip is connected by its compliant shaft to a
seta. Professor Williams was able to construct a model in which an adhesive
spatula was connected
via an elastic cantilever, and he was thus able to derive relationships between a normalized cantilever length
L and a normalized pulling load
P.
Unfortunately it is rather difficult to experimentally test the results of these calculations on the extremely small
spatulae and
setae of a gecko. To address this problem, Williams made a macroscopic model using a piece of spring steel to represent a spatula shaft, and small ceramic magnets to mimic van der Waals adhesion (
see inset to Figure 2). The magnets were attached to a steel plate so that they could move laterally on ball bearings, and the end of the strip was moved vertically at about 20 mm per minute until the elastic energy stored in the bending steel strip was sufficient to overcome the adhesion between the magnet and the surface to release it. The experimental normalized loads P are plotted
versus the normalized cantilever lengths
L in Figure 2. The results are compared with the theoretical predictions for various approximations and result in good agreement between theory and experiment.
Figure 2. Plot of normalized load P versus normalized length L for pulling and adhesive contact by means of a normal force exerted on a cantilever. (Reproduced with permission from the Journal of Physics D: Applied Physics (3).)
The advantage of using normalized quantities is that the results can be scaled down to the dimensions and material properties of the gecko. Using typical sizes of a
spatula and the elastic modulus of keratin gives a normalized length
L of a
seta of about 0.8. The experimental and theoretical results of Figure 2 therefore predict that the gecko should have to exert a normalized load
P of about 2 to release each
spatula tip. Again, using typical dimensions for a gecko, this corresponds to a force of adhesion of each individual
spatula of ~10 nanoNewtons, close to adhesion strengths readily measured by means of an atomic force microscope.
This nicely illustrates how simple mechanical models can be used to understand how nature works and may one day lead to designing machines that can also walk up walls.
REFERENCES
1.
Tysoe, W.T. and Spencer, N.D. (2007), “Sticking with epizoochory,” TLT,
63 (4), p. 56.
2.
Tian, Y., Pesika, N., Zeng, H., Rosenberg, K., Zhao, B., McGuiggan, P., Autumn, K. and Israelachvili, J. (2006), “Adhesion and friction in gecko toe attachment and detachment,”
Proceedings of the National Academy of Sciences of the United States of America (PNAS),
103 (51), p. 19320.
3.
Williams, J.A. (2015), “Adhesion Instabilities in Gecko Locomotion,”
Journal of Physics D: Applied Physics,
48, p. 015401.
Eddy Tysoe is a Distinguished Professor of Physical Chemistry at the University of Wisconsin-Milwaukee. You can reach him at wtt@uwm.edu.
Nic Spencer is professor of surface science and technology at the ETH Zurich, Switzerland. You can reach him at nspencer@ethz.ch.
Both serve as editors-in-chief of STLE-affiliated Tribology Letters journal.