Developing new tests for engine oils
R. David Whitby | TLT Worldwide May 2015
Revised specifications for oils in gasoline will be issued this year.
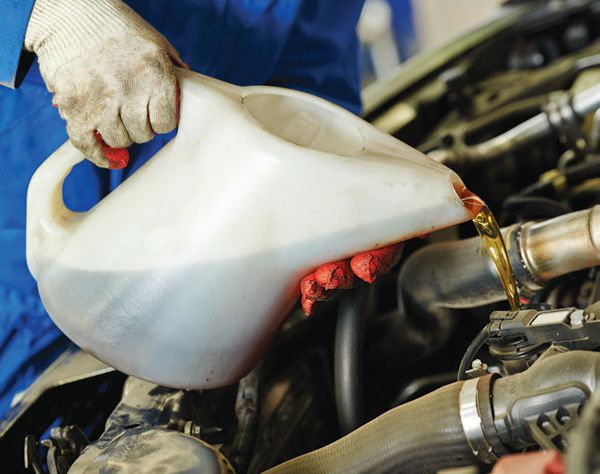
Engine tests are designed to evaluate oils in terms of wear, corrosion, piston-ring sticking, fuel economy, deposits, varnish and/or sludge formation.
www.canstockphoto.com
EVERY FEW YEARS THE AMERICAN PETROLEUM INSTITUTE (API), the International Lubricants Standardization and Approvals Committee (ILSAC), the European Automobile Manufacturer’s Association (ACEA) or the Japanese Automotive Standards Organization issue revised specifications for oils to be used in gasoline, light-duty diesel or heavy-duty diesel engines.
The requirements for these specifications are generated by OEMs, the makers of cars, vans, trucks and buses. They develop the specifications in cooperation with manufacturers of additives used in engine oils and marketers of finished engine oils.
Developing engine tests for the specifications is time consuming and expensive, as is maintaining valid testing in engine testing laboratories. When a new test is developed, it should be relevant to needs in the real world—and it should reflect as far as possible normal operating conditions, metallurgy and fuel quality.
In general, developing engines specifically for test purposes has proved expensive, and doubts have been raised about their relevance to practical use. It is common to use commercial engines of increasing size and complexity as they have evolved. Large engines require large test beds and dynamometers, are thirsty for fuel and require more time for rating and rebuilding than smaller engines. The costs of engine-test evaluation have escalated rapidly in recent years.
Attempts to shorten test time by making conditions very severe are common but become of doubtful merit if outside the extremes of foreseeable operating conditions. A test must correlate with available field service data to be meaningful. A test needs to be as repeatable as possible so that a given oil tested at different times in one laboratory produces the same effective result; it must also be reproducible so different laboratories will agree on the results. To achieve this, tight control of part quality is vital, as are consistent engine-building techniques, operating practices and constant fuel quality.
A test is no good if it is very repeatable but does not discriminate. It must clearly distinguish between oils of different qualities so that when a passing level is defined, oils under test can form a distribution of clear passes, marginal passes, marginal failures and clear failures. Several proposed new engine tests have been abandoned because discrimination was inadequate.
After a test is run, the engine is disassembled and the parts rated. Disassembly and part-washing procedures must be standardized and rating methods carefully spelled out for each test. Skilled and consistent rating comes with experience and training, and for the more important tests worldwide rating meetings are organized where selected raters discuss rating practices and participate in rating exercises.
Engine tests are designed to evaluate oils in terms of wear, corrosion, piston-ring sticking, fuel economy, deposits, varnish and/or sludge formation. During test development, passing limits must be established, usually based on test results of oils known from field experience to be borderline satisfactory.
To control the test after publication, reference oils are needed to define passing, borderline passing and failing results. Reference oils serve several purposes. They permit an engine laboratory to judge if it is obtaining acceptable results. They permit, via blind testing, an approval authority to judge if a laboratory’s results can be considered valid. For some tests and some specifications, it is possible to judge pass/fail criteria in relation to a reference oil. This can be in terms of a difference between a candidate oil test result and a recent reference oil test result, or the reference results can be used to adjust the initial rating of the test oil.
Because of the nuances, engine testing is never as repeatable or reproducible as we would wish. Control of parts and fuel quality is essential, together with clear operating procedures. However, the most important thing is to ensure that the most suitable engine to measure the test parameter is chosen in the first place. Matrix testing is used to check that a new engine test is as repeatable and reproducible as possible.
The next set of ACEA specifications is due to be issued during 2015, and the next set of ILSAC and API specifications is due in early 2016, ready for product introductions early in 2017. It will be very interesting to see what they look like.
David Whitby is chief executive of Pathmaster Marketing Ltd. in Surrey, England. You can contact him at pathmaster.marketing@yahoo.co.uk.