Mercurial Bearing
Evan Zabawski | TLT From the Editor April 2015
Shining light on a high-density, nearly frictionless lubricant.
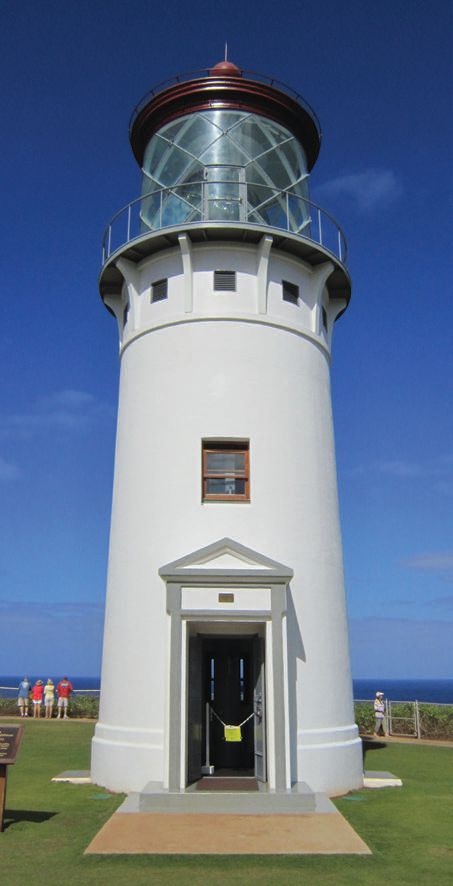
Built in 1913, Hawaii’s Kilauea Lighthouse served as a navigational aid for commercial ships traveling between Hawaii and the Far East. Its 400 hand-ground prisms (left) could be rotated by the push of a single finger.
A FEW MONTHS AGO I HAD THE PRIVILEGE OF VISITING the Kilauea Lighthouse on the Hawaiian island of Kauai. During a guided tour of the lighthouse, which had just reopened after undergoing extensive restoration in celebration of its 100th anniversary the previous year, the docent mentioned that the 4,100-kg (9,000-lb.) lens rotated on a mercury-filled bath. The words were no sooner out of his mouth when my wife turned to me and said, “Next month’s TLT.”
This unique bearing design greatly improved the speed at which the lens could rotate compared to earlier designs. Burdened by the extreme weight and coupled with the weak power of the clockwork-drive mechanism, early lighthouses could take as long as eight minutes to complete one revolution with each light flash lasting 20 seconds or more. It was thought that the shorter the flash, the easier it would be for the mariner to see the light.
The first attempt to shorten the flash involved using larger clockworks and the interval between flashes was decreased by increasing the number of bull’s-eye panels. A 24-panel lens could produce a five-second flash every 15 seconds.
When French engineer Augustin-Jean Fresnel invented his eponymous lens, he relied on a chariot wheel
roller bearing system that only worked well at low speeds. The wheels were not only expensive to manufacture, but they (and the track they rode on) needed replacing every few years. A later attempt to use ball bearings increased speed but still produced significant friction.
Fresnel first suggested floating his lens on a bath of mercury in 1825, but it was not until 1890 that Leon Bourdelles, chief engineer of the French Lighthouse Service, designed and built a workable system. His design consisted of an annular trough filled with mercury and a slightly smaller annular float supporting the apparatus. Using this design, about 90 kg (200 lbs.) of mercury could support 2,700 kg (6,000 lbs.).
Widespread adoption of mercury flotation led to flashes of three-tenths of a second and intervals of 10 seconds becoming quite common. Pushing the envelope, the French achieved a one-tenth second flash with their ‘feux-éclair’ or lightning lens. Mariners, however, complained this was too fast for use under all weather conditions. Three-tenths of a second eventually became the de facto standard.
One problem with mercury is that it evaporates; another is its poisonous vapor. Lighthouse keepers cleaned the surface of the mercury and adjusted the level on an as-needed basis, which put them into periodic contact with the mercury and its vapor. To minimize the fumes, it was common practice to pour a layer of motor oil onto the surface of the mercury.
The Kilauea Lighthouse produced its signature double-flash every 10 seconds, which could be seen nearly 34 km (21 miles) out to sea. It used only a gallon of mercury, and when balanced correctly with compressed air, its 400 hand-ground prisms could be rotated by the push of a single finger. Ultimately the Fresnel lens was decommissioned in February 1976 due to mercury exposure. The light was moved to a smaller tower nearby, and the original tower was sealed.
Though the lighthouse has reopened to the public, it has not been recommissioned permanently, only lit for its anniversary. A newer beacon—the size of a large soup bowl—was installed on the smaller tower and continues the task of alerting passing ships. It is hard to accept the replacement of such majesty with an exceedingly plain-looking device. One cannot help but admire the beauty of the original design and appreciate the dedicated effort to preserve it.
Evan Zabawski, CLS, is the senior reliability specialist for Fluid Life in Edmonton, Alberta, Canada. You can reach him at evan.zabawski@fluidlife.com.