Complexity in ISFA (in-service fluid analysis): Part XXI
Jack Poley | TLT On Condition Monitoring March 2015
The job just begins once you correctly set up an ISFA-CM program.
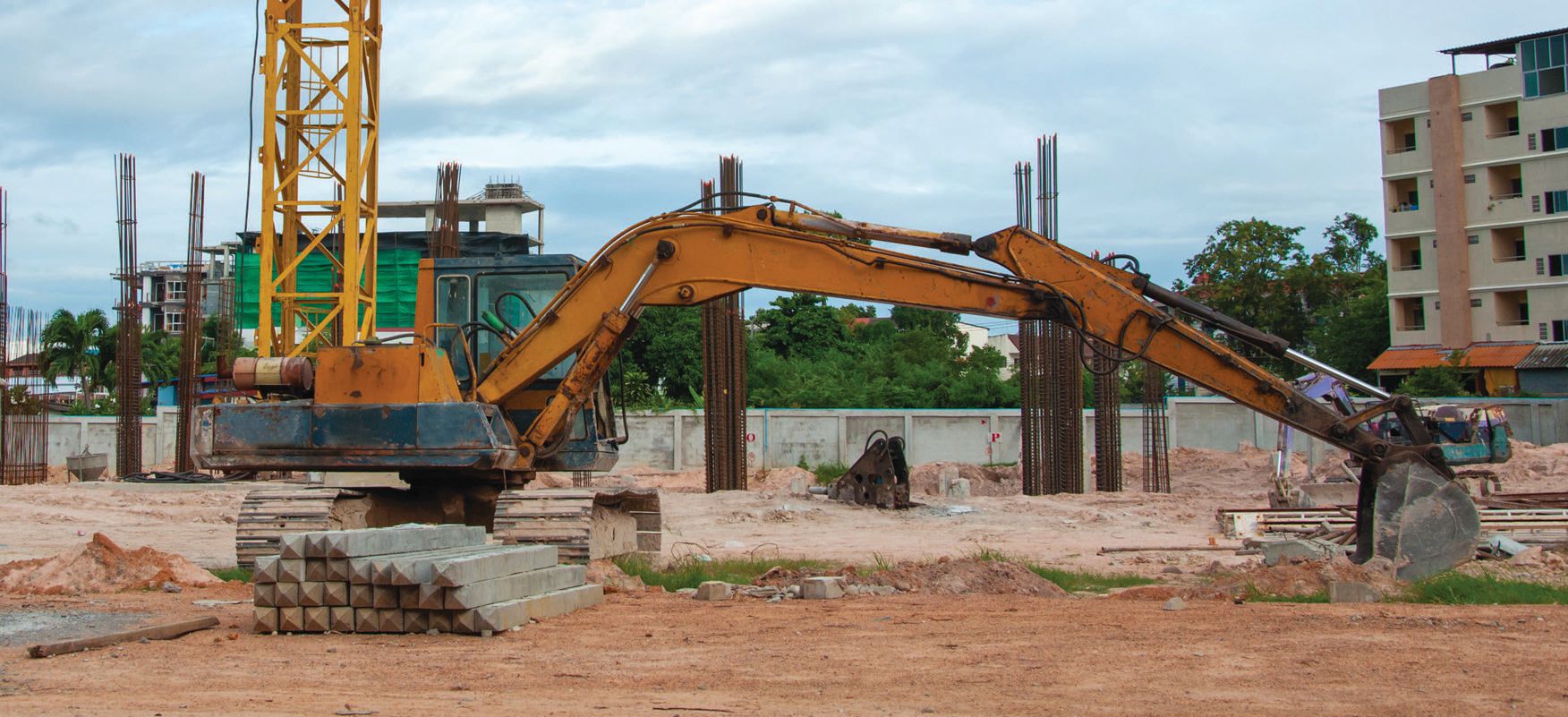
www.canstockphoto.com
EXECUTING AN EFFECTIVE CONDITION MONITORING (CM) PROGRAM IS A MAJOR UNDERTAKING. This is the statement I led off with last column, except I used the words “Preparing for an effective…” in the introductory phrase. Sustaining and taking advantage of the now-declared and ostensibly implemented program is the next and ongoing hurdle. And, yes, it’s a hurdle. It’s a chore. It has to be done well if the program is going to work well.
Recall I cautioned that CM programs do not run themselves. The personnel involved have to coordinate well if the end result is to be truly successful.
And what is that result? It’s about taking money off the table via maintenance savings and maximized production. That continues to be why organizations perform CM—to conserve money—and they spend less on maintenance and/or increase revenue. That’s the bottom line.
COMMON ISFA-CM USER ONGOING ERRORS AND OMISSIONS
•
Failure to set up the database completely and accurately.
o
This causes ineffective or harmful commentary from misinformation.
o
This problem will compound over time—do it right the first time.
•
Poor sampling logistics.
o
Failure to use sampling ports/valves where practicable. Get a good representative sample—skimping here is
extremely short-sighted.
o
Securing cold samples that aren’t as representative as possible (having sampling ports usually prevents this error from occurring because there has to be lubricant flow to secure a sample via a port). Samples should be taken after a component is warmed up, which helps to disperse wear and contamination more evenly, or before a component cools down significantly after being shut down. Significant sampling delays after shutdown result in lost particles due to gravimetric separation.
o
Labels on sample containers should be checked and vetted at time of sampling to be sure they are correctly applied, not applied after several samples have been secured, opening the door for a possibility of a mix-up.
o
Labels should be completely filled out: unique component name, sample date, time on lube, time on component and lube make-up.
o
At times the answer needed to make sense from sample test data is right in front of the person taking the sample, but unless this person is trained to look for the obvious, he or she may see the job as simply collecting a fluid sample and little more. This weak link can be avoided. The sampler should create a note as an advisory if obvious problems are noted. Here are some examples:
•
Sump is/was low on fluid
•
Obvious foaming
•
Visible water
•
Seal leakage
•
Heat
•
Odor.
•
Failure to read and act on reports or reports that do not fully clarify the situation.
o
Failure to read the report. There is no sense to sampling if you are not going to attempt to use the advice provided. Time is often critical when certain types of problems are indicated. I have seen many in baskets stacked with reports that haven’t yet been read by the maintenance team, including supervisory level personnel. Nowadays, given Web delivery of reports and email alerts, there’s no excuse for not being in touch with your program on a near-daily basis. This is nothing more than a relatively easy culture change, wherein the ISFA effort is incorporated in the CM system, not peripherally.
o
Unclear reports. Reports vary in quality and information, and this does put pressure on the recipients of these reports. While report receivers should have knowledge of their machinery and the lubricants used by that machinery, they will not often possess sufficient knowledge of both aspects—machinery and lube—such that assistance from the testing facility could be welcome,
if that assistance is actually contained in the report verbiage. It is important to communicate with the tester when it is not completely clear as to what action should or should not be taken.
o
Changing out the lube but with no preventive follow-up. Unthinkably, there are numbers of maintenance personnel who deem a lube change as a cure for a detected problem. Often that results in a very dangerous outcome, wherein a problem is temporarily masked by the lube change but continues to exist, ultimately putting the machinery at risk. Here are examples of such situations:
•
Abrasives (some type of dirt) seem to be indicating iron and silicon are in lock step in a report trend. Draining the lube will eliminate most of the abrasive but will not stop the continued ingress of abrasive material.
o
A faulty air cleaner, contaminated lube handling and dispensing equipment
o
A compromised vent in a gearset.
These are examples of root cause problems that should be investigated quickly upon seeing such a report. Yes, the lube needs to be changed, but the source of the contaminant needs to be investigated as well to prevent recurrence.
•
Wear increases, where no evidence as to
why is revealed from the tests (it is possible that an additional test would disclose a problem, but let’s remove that from this particular discussion). Sometimes the report recipient assumes that changing the lube will make the problem go away. Unfortunately that results in removal of trending evidence. People who react in this manner have the mistaken notion that every wear problem has to have its root in the lube, but, again, there are other considerations that lube change-outs will not mitigate:
o
There may be a factory defect in a part.
o
The equipment may be abused as to overload.
www.canstockphoto.com
ABRASIVES
As an aside, let’s return to the abrasives example; there are exceptions to any rule, such as a top drive on an offshore drill rig, the gearset transferring power to the drill. I mentioned this in a previous column, but it bears repeating. The daily revenue stream of a drill rig is such that, rather than take a top drive down, the operator would prefer to bring in a replacement drive as soon as possible, but this could take a week or more, depending on availability and the rig’s physical location.
If, for example, drilling mud contamination (an abrasive) were observed via ISFA, and wear was correspondingly on the increase, the rig would continue to drill but would also change out the fluid nearly every day to minimize the top drive’s exposure to the drilling mud ingress. Sampling would be daily as well, to monitor the situation while awaiting the replacement drive.
This wastes lube and creates a modest amount of additional labor expense, but such an approach is not nearly as expensive as shutting the drive down and waiting for a replacement. Here again is the money equation: It is considered a good business decision to risk total wipeout of the drive versus loss of several days of revenue, even more valuable than the entire top drive. Were a similar situation found to exist with a machine that would not shut the rig’s drilling down, this type of action would not take place, but rather the machine would be repaired or replaced in short order, the norm so to speak.
THE BOTTOM LINE
Lastly, but most importantly, we get to money. Few ISFA-CM users actually attempt to investigate ROI on their programs. There are two primary reasons for this:
•
It’s not easy to do—I’ll discuss this in the next column.
•
Any reasonably established ISFA program will be viewed as saving money because numbers of important problems are usually detected and dealt with. But as I like to state, “Lots of money is left on the table when no accountability is actually the norm.”
Jack Poley is managing partner of Condition Monitoring International (CMI), Miami, consultants in fluid analysis. You can reach him at jpoley@conditionmonitoringintl.com.
For more information about CMI, visit www.conditionmonitoringintl.com.