Tiny Bubbles
Nancy McGuire, Contributing Editor | TLT Feature Article February 2015
Entrained air can shorten a lubricant’s life. These steps will help protect your machinery.
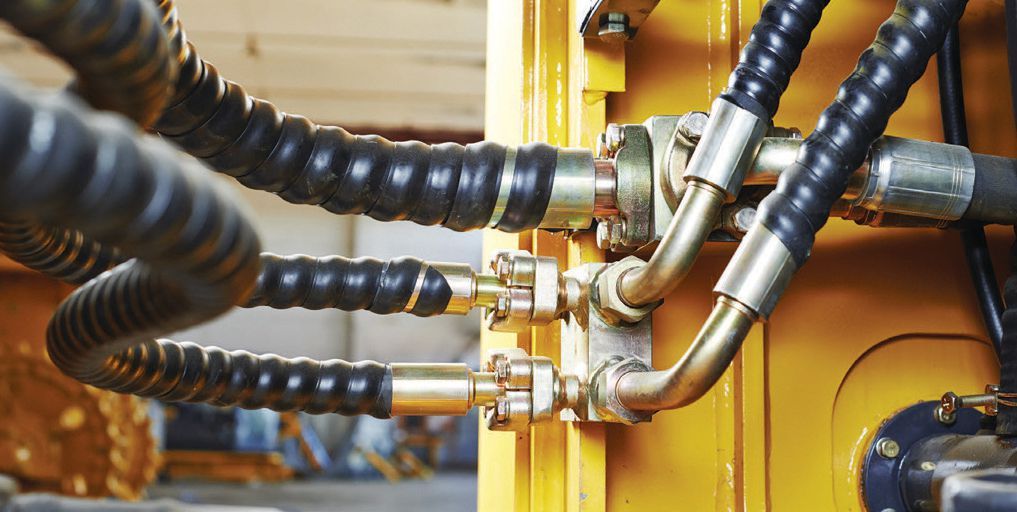
www.canstockphoto.com
KEY CONCEPTS
•
Smaller oil reservoirs and higher power densities are bringing oil-aeration problems to the forefront.
•
Problems caused by entrained air differ from those caused by free air, dissolved air and foam and require their own solutions.
•
Hydraulic oils and engine lubrication oils require different but related approaches for dealing with entrained air.
WHILE GREAT IN CHAMPAGNE, tiny bubbles can cause big problems in lubricating and hydraulic oils. Your equipment’s lubricating oil and hydraulic systems contain air. How this air affects operations depends on how much air is involved, how finely it’s dispersed and whether it is on or under the surface of the oil. Large pockets of free air can span the width of a supply line. Foam bubbles 1 mm in diameter and larger collect at the surface of the oil. Dissolved air mixes with the oil at the molecular level, and the oil itself can release volatile components under certain conditions.
Entrained air—bubbles with diameters smaller than 1 mm dispersed throughout the oil—causes its own problems and requires solutions all on its own. Air is entrained in oil when the oil experiences turbulence or agitation. This can occur as the oil goes through bearings, couplings, gears, pumps and oil-return lines. Air can be entrained when fluid levels are too low or when seals and hoses begin to leak.
Air entrainment affects an oil’s ability to act as a lubricant as well as its effectiveness in transmitting pressure in hydraulic systems. Hydraulic systems and lubricating systems each have their own issues, but many modern gasoline and diesel engines are designed to use the crankcase oil to function as a hydraulic fluid to operate fuel injectors and valve train controls. Thus, it is useful to discuss both types of systems together but also to note the differences.
Lubricants and hydraulic fluids are often formulated with a primary focus on viscosity, oxidation resistance and other properties—then air entrainment and release properties are taken into account. However, trends in equipment manufacturing toward smaller oil reservoirs and higher pressures and power densities are beginning to press the aeration issue.
Hydraulic systems have reservoirs with strainers and baffles that separate out solid impurities and allow entrained air and foam to be released. Smaller reservoirs take up less space and require less material to manufacture, and they reduce the total amount of lubricant needed in the system. However, if the reservoir is too small, the fluid may not have time to cool adequately, allow solid contaminants to settle out or release entrained air bubbles before it goes back into circulation.
STLE Life Member David Phillips, a consultant on hydraulic fluids and lubricants in Cheshire, England, summarized the problems caused when new equipment designs outstrip the capabilities of lubricating and hydraulic fluids. “Unless you are using a fluid that has very good air-release properties or a very low solubility for air, then reducing the size of the tank increases the likelihood of cavitation and microdieseling, as the air will have less time to be released from the fluid before it re-enters the pump,” says Phillips. “This will result in increased foaming and air-release values, as well as oxidation of the fluid—reducing fluid life.
“If air is dispersed in the fluid as bubbles, rather than being dissolved, the response of the fluid to any increase in pressure will become slower, rather like spongy brakes in a car,” Phillips adds. This can have serious consequences where hydraulics are relied on in emergencies to close valves or trip systems. For example, emergency stop valves in a steam turbine are designed to close in milliseconds. Automotive systems that use variable valve timing for fuel efficiency rely on fluids with good aeration resistance and rapid air release to keep them working optimally (
1).
Two photos of oil in a reservoir, downstream of the baffle, just above the pump inlet. Left: The fluid is clear and bright when the pump operated at 1200 rpm. A density balance is visible through the oil. Right: At 2100 rpm bubbles accumulated in the fluid. (Photos courtesy of Helgesen Industries in Hartford, Wis., and Milwaukee School of Engineering.)
PHYSICS AND CHEMISTRY
Entrained air changes the physical and chemical properties of lubricants and hydraulic fluids. Because air is more compressible than the surrounding fluid, the presence of air bubbles reduces the bulk modulus of a hydraulic fluid, decreasing the fluid’s ability to transmit pressure. The result is poor response and spongy behavior.
Air bubbles also change a fluid’s thermal conductivity and, thus, its ability to dissipate heat. Bubbles under high pressure can become very hot, which accelerates the reaction of air with oil components, oxidizing the oil and shortening its service life.
Entrained air can reduce a lubricant’s viscosity, producing a lubricant film that is too thin and fragile to maintain a barrier between metal parts during normal operating conditions. Small regions of metal-to-metal contact may become hot enough to produce small spot welds that break off and form regions of metal strain; these can, in turn, promote cracking and spallation or accelerated corrosion. Small bits of metal also can break off and enter the lubricant stream, causing damage and wear downstream. In addition, pumps perform less efficiently and consume more energy when fluid viscosity levels are too low.
“Viscosity changes are less of a problem for hydraulic systems,” notes Paul Michael, a research chemist at the Milwaukee School of Engineering’s Fluid Power Institute in Milwaukee, Wis. He points out that engine oils make up a large share of the lubricant market. Often engineers apply the same concepts to hydraulic oils, but the two types of systems really should be looked at separately.
“Engine oils experience more oxidation and thermal degradation than hydraulic oils,” says Michael. “At realistic flow rates, temperature and viscosity don’t matter as much (for hydraulic systems) as we expected.”
Michael is referring to his research group’s laboratory studies. “Under normal operating conditions, hydraulic oils do not undergo significant viscosity changes. They don’t accumulate combustion and oxidation products like engine oils do, and hydraulic systems employ filtration systems to remove particulates.” However, Michael also says that hydraulic fluids typically do not remain in the reservoir long enough to allow entrained bubbles to rise to the surface. Thus, the main concern is to keep air bubbles out of the oil in the first place by reducing turbulence or using fluids that resist air entrainment.
Contaminants also contribute to aeration problems. Some antifoam additives are attracted to the surface of particulate contaminants, promoting the formation of clusters of small bubbles. Phillips says, “I don’t think we fully understand the effects of contamination on air release, except that a contaminated fluid usually has a significantly worse air-release value. The result of different types of contamination has not been rigorously studied (to my knowledge) and the question is always whether the lab test data really correlates with what is happening in the tank.”
For lubricating oils, Hind Abi-Akar, fluids technical expert with Caterpillar Inc., notes, “Oils that have poor aeration characteristics can fail even in robustly designed engines. Both mechanical design and oil formulation are critical and have to be designed carefully and adequately.”
Abi-Akar also explains, “Engines and hydraulic systems are affected by multiple factors at the same time: oil flow, temperatures, pressures, contaminants, oil aging, parts geometry and surface composition. These combined effects are difficult to predict or simulate. Collectively, the impact of oil aging in operating engines (or hydraulics) is not clearly understood. It is known that used oil aeration properties are worse than new oils, but a prediction of the aeration decline or aeration level as the oil ages in a specific system (engine or hydraulic) is not established.”
Just as oil ages, engines age as well. “This is known, yet not well understood and difficult to predict and model,” says Abi-Akar. “The best bet is to design oils that have a good aeration performance (per performance in standard tests) and work to design systems that reduce the potential for aeration when possible.”
Cavitation wear and microdieseling damage. (Photos courtesy of Helgesen Industries in Hartford, Wis., and Milwaukee School of Engineering.)
CHEMICAL SOLUTIONS
Michael notes that there is a large opportunity for research in designing hydraulic fluids with good air-release properties. “Manufacturers of concrete and polymers are ahead of lubricating and hydraulic oil manufacturers in understanding the chemistry of air entrainment and release,” he adds. Often, fluid formulations place a primary focus on lubricating capabilities, resistance to oxidation and other factors, with air-release and air-resistance properties coming in as secondary considerations. “Many past approaches were based on empirical experience and engineering concepts rather than physics and chemistry,” Michael says.
“Aeration isn’t a problem if the air doesn’t go in to begin with,” says Mathias Woydt of BAM Federal Institute for Materials Research and Testing in Berlin, Germany. He notes that if air has a low solubility in a particular base oil, the oil will exhibit a lower tendency to foam and entrain air.
Polymeric additives can cause a base oil to retain air longer because bubbles adhere to the macromolecules, Woydt explains. Polyalkaline glycol (PAG) base oils have low gas solubilities in general. Because they have intrinsically high viscosity indices (their viscosity changes very little over a wide temperature range), they do not require polymeric viscosity index improvement additives, which eliminates another source of air retention.
Once air gets into a fluid, various additives can get it out again as quickly as possible. Surfactants, compounds that lower a bubble’s interfacial tension, work well for breaking up foams. The surfactant thins the sheath of the foam bubble until it breaks.
Unfortunately, what works for breaking up foam can actually worsen an entrained air problem. Under the fluid’s surface, the same reduction in interfacial tension promotes the formation of smaller bubbles. The smaller the bubble, the more slowly it rises to the surface of a liquid (Stoke’s Law). If the oil is a more viscous grade (more likely to be needed for power-dense operations), or if it has become sludgy through oxidation and thermal degradation, this also slows the bubble’s release.
Additives that improve an oil’s viscosity index or reduce oxidation and corrosion can also provide nucleation sites for the formation and stabilization of entrained air bubbles. Add in impurities, hydrophilic components that bind to air, or particulate contaminants where bubbles can adhere, and the air-release times go up even more. Increasing operating temperatures can assist in accelerating entrained air release, but it can also increase the release of dissolved air and volatile oil components.
Kumar Kumarasekaran, market development manager for Advanced Lubricants, summarizes some of the challenges in developing new fluids with better air-release properties. “Ninety percent of the world uses mineral oil, so you have to design your equipment to use mineral oils,” he says. Typically equipment manufacturers can’t radically redesign their equipment because fleet operators need interchangeable parts.
Cost and availability problems pose further limitations. Many equipment manufacturers have their own lines of fluids, Kumarasekaran continues. Their equipment can use standard fluids, but manufacturers offer upgrades such as the synthetic oils that some cars can use. The main drivers for innovative new fluids are economic requirements and government regulations.
The trend in lubricating oils for heavy-duty diesel applications is toward lower viscosities. Less energy is required to pump low-viscosity oils through an engine, resulting in significant savings in fuel costs. Less-viscous oils tend to have better air-release properties (
2).
The choice of a base oil has a pronounced effect on a lubricant or hydraulic fluid’s air-release properties. The least expensive base stocks, API Group I, generally have air-release values of 6 to 20 minutes at 0.2 percent air (
3). (
See sidebar called Testing Air Release Properties.) The higher-viscosity Group I base oils are considered to have poor air-release properties, but these can be improved using methods such as methanol extraction (
4).
Testing Air-release Properties
Hydraulic and lubricant fluid manufacturers frequently cite the air-release properties of their products based on air-release times determined using the ASTM D3427 method (
6). In this method, a sample of oil is heated to a standard temperature (commonly 50 C), and compressed air is blown through the oil. The oil is then allowed to sit while the entrained air rises to the surface and is released. A density balance is used to determine how long it takes for the air content of the oil to fall to 0.2 percent by volume.
Paul Michael with the Milwaukee School of Engineering’s Fluid Power Institute notes that typical reservoir sizes for industrial hydraulics run about one to three times the pump flow rate. A pump running at 100 gallons per minute requires a 100-300 gallon reservoir, and hydraulic fluid stays in the reservoir for one to three minutes. Mobile equipment (earthmovers, front loaders, etc.) has reservoirs 0.3 to 1 times the pump flow rate, and hydraulic fluid stays in these reservoirs for 20 seconds to a minute using the same pump flow rate.
Using ASTM D3427, Group I oils have air-release values of six to 20 minutes and Group II oils range from 3.5 to six minutes—longer than the oil’s residence time in a typical reservoir. Thus, this test is good for comparing various oils and additives, but it doesn’t necessarily reflect normal operating conditions. Caterpillar fluids technical expert Hind Abi-Akar notes that fully formulated oils can pass the ASTM tests and still fail in engines.
New oil specifications, driven by environmental regulations and changes in engine construction and technology, are on the horizon. PC-11, a set of specifications for heavy-duty diesel engines, and GF-6, its counterpart for passenger vehicle oils, are prompting the development of new test procedures.
Caterpillar is currently adapting one of its internally used test procedures, the C-13 engine oil aeration test, in preparation for the PC-11 specifications (2). The company is working with other labs to define the hardware and procedural details and to perform validation tests. One part of this method development effort deals with reducing test result variability attributable to individual operators.
Abi-Akar says, “The technique used in this new test (still under development) is real-time measurement based on changes in the oil density due to air entrainment.” The oil density at specific temperature, pressure and flow rate is compared to unaerated oil using a coriolis density meter (Micromotion). She says, “As the engine runs, these parameters are kept constant at the flow meter in order to measure the tendency of the oil to aerate. This is the first time we have observed oil aeration in a running engine, and we are observing certain behaviors that may lead to a better understanding of this phenomenon.”
Group II base stocks have air-release values ranging from 3.5 to 6.0 minutes at 0.2 percent air, and air-release values for Group II base stocks vary less than do Group I base stocks. Group III oils are more expensive, but they also release air very quickly, achieving 0.2 percent air content in less than a minute at 50 C in some cases (
5). Many synthetic base oils, including polyol esters, polyalphaolefins and phosphate esters, typically have lower air-release times than conventional mineral oils.
Several major petroleum companies have developed and patented additives for reducing the amount of air that becomes entrained in oil and reducing air-release times. These include paraffinic materials, ashless detergents, viscoelastic polymer, and polymers that form micelle-like structures in the base oil.
CAVITATION AND MICRODIESELING
Entrained air and dissolved gases both cause damage to turbine blades, propellers and impellers, but the methods of addressing the problems differ. Whatever the source, bubble implosion and ignition cause similar kinds of noise, vibration and damage to mechanical parts.
Entrained air bubbles are usually the result of turbulence. This can be caused by poor location and design of pump inlet ports and reservoir baffle systems, or when the fluid level in the pump becomes too low.
Dissolved air and volatile oil components can come out of solution and form bubbles as a result of pressure drops or temperature increases. Low-pressure regions can form downstream from clogged filters or suction strainers or as a result of restrictions in a pump intake line. Sharp bends or restrictions in intake lines can also cause low-pressure areas. Even in the absence of restrictions, low-pressure regions form as fluid accelerates around the blades of a pump impeller. Fluid flowing around the outside of a bend flows faster and experiences less pressure than fluid near the inside of the bend.
Cavitation occurs when gas bubbles become compressed inside a pump or a cylinder. When pressure on the fluid increases past the point where the bubbles can compress further, the bubbles implode. The resulting shock waves produce noise and vibrations, which can slam parts together, causing them to loosen up and wear out faster.
Cavitation bubbles generally need a surface on which they nucleate. This surface could be the sides of a reservoir, contaminant particles in the oil, entrained air bubbles or the pits and surface roughening caused by previous cavitation and microdieseling damage.
Microdieseling occurs when gas bubbles become hot enough to ignite, and it can damage seals and produce varnish on metal surfaces. Extreme compression can cause localized temperatures near the bubbles to reach as high as 2,000 F (1,100 C). The combination of high localized temperature and shock waves can produce pitting in pump impellers or turbine blades, which serve as nucleation sites for corrosion. Surface pitting produces areas of strain, shortening the lifetime of the metal part.
Volumetric efficiency of the same axial piston pump at high and low aeration levels, the result of two baffle designs. (Graphic courtesy of Helgesen Industries in Hartford, Wis., and Milwaukee School of Engineering.)
MECHANICAL DESIGN
Reducing air entrainment doesn’t always involve redesigning fluids and mechanical systems—routine maintenance goes a long way. This can be as simple as checking inlet strainer filters for clogging and replacing flexible intake hoses before they become porous or brittle. Fluid levels should be maintained at the recommended levels to reduce air intake as well as to maintain enough fluid to dissipate the heat generated by the system. Woydt says, “Gas separators can help in ridding fluids of entrained air, but equipping systems with these can increase costs.”
Many design innovations for new hydraulic equipment are driven by a need to increase power density, Kumarasekaran notes. Manufacturers want to reduce weight, footprint and volume, while increasing power. Smaller reservoirs weigh less and require less material for construction. Reduced weight produces greater fuel efficiency and reduced volume requires less fluid for operations. Michael says, “New emissions regulations, including the Tier 4 standards for off-highway vehicles, require the installation of emissions filters and oxidation catalysts that reduce the space available for other components, including reservoirs.”
Abi-Akar explains, “Development work at Caterpillar deals with both fluid and equipment design. Engines are tested using multiple tilt angles and directions to simulate machines working on inclines and rough terrain, an important factor to determine whether air can be entrained under realistic working conditions.”
Newer hydraulic equipment is designed with smaller cylinders under higher loads, and there is a demand for greater hydraulic pressure. Michael notes that because greater volumes of fluids are needed for hydraulic systems than for lubricating systems, and hydraulic fluids are changed less frequently, aeration is a particularly important issue in hydraulic systems. Hydraulic oils with low air-entrainment and rapid air-release properties allow hydraulic pumps to be operated at higher speeds and, thus, higher flow rates.
Broad, flat reservoirs offer more surface area for releasing bubbles and foam, and they dissipate heat better than long, narrow tanks, but space must be found to accommodate them. Aerated fluid is circulated throughout the system if the fluid reservoir is too small, the amount of fluid used is insufficient or the residence time is too short for the type of fluid being used.
For mobile equipment like road graders, reservoirs are shrinking to provide better visibility. “The operator wants to see the ground directly in front of his machine, and he doesn’t want the view blocked by the engine compartment,” Kumarasekaran says. This type of customer wants new designs that maximize power while minimizing component sizes.
Small reservoirs are also desirable in equipment, including aircraft and elevators, where space is limited. Human prosthetic devices that use hydraulics are an extreme example of miniaturization and putting the most power into the smallest area. Light weight, smooth operation and reliability are key factors in the success of all these devices.
“Some market segments are less concerned with size reduction than they are with reliability, downtime costs and the costs of purchasing new equipment,” says Kumarasekaran. “The hydraulic equipment industry is about 10 to 15 years behind the automotive industry.” He mentions they are behind in adopting newer mechanical designs and fluids, citing a lag time driven by costs for replacing individual units and a need to maintain uniformity in fleets of equipment. Increases in energy efficiency and reduced labor costs must be great enough to offset the costs of buying new equipment within 12 to 18 months to justify buying new technology.
“Expert users don’t need the latest and greatest,” Kumarasekaran says, explaining that professional equipment operators are well versed in getting the best performance out of their existing equipment without the need for new technology. This is in contrast to individual car buyers, for example, who are drawn to features that make the driving experience more convenient.
“Some industrial customers, however, are motivated to adopt new technologies because their downtime costs are high enough to outweigh the costs of purchasing new equipment,” Kumarasekaran notes. For example, tar sands operations in Canada lose about $47 for every second of downtime, Kumarasekaran notes. Wages for workers run high, and every truckload of tar sand not delivered represents unrealized income. One fleet can have 100 vehicles, and each vehicle can require 2-3 hours for an oil change, plus the cost of the oil itself.
“Other customers also require systems that can use fluids with better aeration properties but for totally different reasons,” Kumarasekaran says. Less entrained air corresponds to more efficient energy usage, for example. This is one factor driving new designs for hydraulic hybrid vehicles, including an excavator that Caterpillar introduced in 2013. These vehicles are cheaper and lighter than electric hybrids, he explains. They do not require the heavy batteries used by electric hybrids, and their response is quicker, providing more agile handling. The high demands on the hydraulic systems, however, requires that fluid aeration be kept to a minimum. Because this is an entirely new class of vehicles, they can be designed to use state-of-the-art hydraulic fluids. Customers for these vehicles will be choosing new technology rather than making incremental updates to existing fleets.
KEEPING THE BUBBLES WHERE THEY BELONG
“The desire of equipment builders to use smaller systems, while understandable, is likely to reduce fluid life unless steps are taken to remove the air from the fluid and to keep it out,” says Phillips. “There are devices now appearing on the market that claim to remove air from the fluid in the tank. Assuming they work, they will take up some space in the tank but yet may allow some reduction in size. There is likely to be a variation in the air release of fluids even within the same chemical type depending on fluid purity, additives used (and concentration), fluid viscosity and the sensitivity of the fluid to degradation products.”
Kumarasekaran predicts that hydraulic equipment will increasingly be designed to use new fluids with better air-release and aeration-resistance properties. “The industry has already started to move toward synthetic fluids,” he says. He also notes that advances in equipment design and advances in fluids drive each other forward.
Once a secondary consideration, air-intake resistance and accelerated air release from engine lubricants and hydraulic fluids are becoming critical to the operation of internal combustion engines and hydraulic systems as designs evolve and become more complex. Solving this problem will be reason enough to break out the bubbly—champagne, that is.
REFERENCES
1. Van Rensselar, J. (2013), “The drive for next generation auto engine oils,” TLT,
69 (9), pp 46-53.
2. Van Rensselar, J. (2013), “PC-11 and GF-6: New engines drive changes in oil specs,” TLT,
69 (1), pp 30-38.
3. API Base Oil Interchangeability Guidelines for Passenger Car Motor Oils and Diesel Engine Oils can be found
here.
4. Baker Jr., C., Gooding, B., and Naegely, P. (Feb. 13, 2014), Exxonmobil Research and Engineering Company, assignee. Patent application WO2014025524 A1. Also published as US20140038867.
5. Rosenbaum, J., Abernathy, S., Miller, S., and Bertrand, N. (Oct. 14, 2008), Chevron U.S.A. Inc., assignee. Patent 7,435,327.
6. ASTM method D3427-03. (2003), StandardTest Method for Air Release Properties of Petroleum Oils, ASTM International, West Conshohocken, PA. This can be found
here.
NON-CITED SOURCES USED AS BACKGROUND FOR THIS ARTICLE
•
Baillargeon, D., Bergstra, R., Jackson, A., Maxwell, W., Johnston, G., and Pache, R. (March 30, 2004), Mobil Oil Corp., assignee. Patent 6,713,438.
•
Habeeb, J., Baillargeon, D., and Deckman, D. (Oct. 26, 2010), ExxonMobil Research and Engineering Co., assignee. Patent 7,820,600.
•
Deckman, D., Baillargeon, D., and Horodysky, A. (March 5, 2013), ExxonMobil Research and Engineering Co., assignee. Patent 8,389,451.
•
Gresham, B. (2004), “Lubricant base oils,” TLT,
60 (4), pp 51-53.
•
Pillon, L.Z. (2007), “Chapter 8: Air entrainment,”
Interfacial Properties of Petroleum Products, CRC Press, pp 245-269.
•
Duncanson, M. (2003), “Effects of physical and chemical properties on foam in lubricating oils,”
Lubrication Engineering, 59 (5), pp 9-14.
Nancy McGuire is a free-lance writer based in Silver Spring, Md. You can contact her at nmcguire@wordchemist.com.