Re-refined base oil quality
R. David Whitby | TLT Worldwide January 2015
Four treatment methods are evaluated.
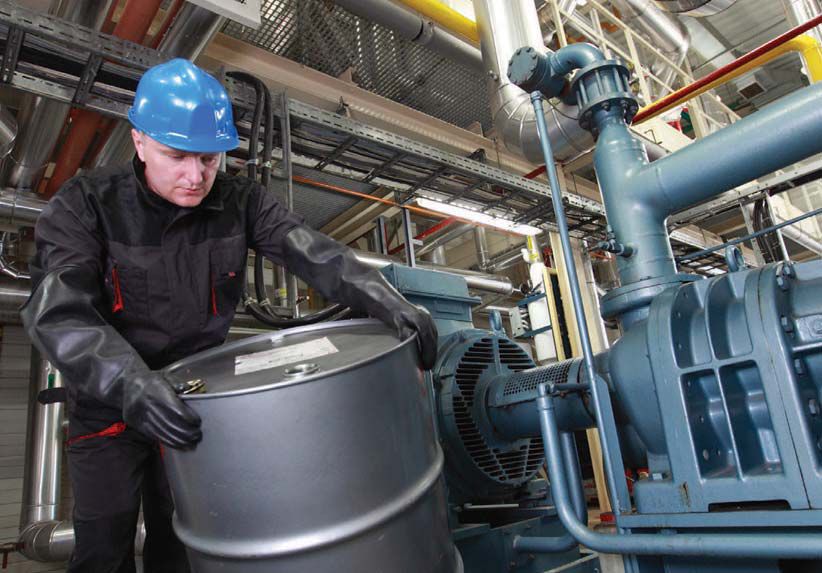
www.canstockphoto.com
RE-REFINING USED LUBRICANTS IS AN ESTABLISHED INDUSTRY that operates in many countries. However, the scale of the industry, types of processes and quality of products vary from one country to another.
All re-refining processes start with the removal of insoluble contaminants such as water and solids. This can be achieved using conventional separators and filters. The clean oil is then lightly distilled to remove the low-boiling solvents and light hydrocarbons that arise either through fuel in engine oils or the thermal degradation of base oils.
After these initial steps, four alternative treatment methods are used to remove non-hydrocarbon components and degraded additives from the oil. These methods are:
1.
Acid and clay treatment. Base oils made by this process are usually darker in color and have inferior quality to virgin mineral oils. Also, they tend to have a noticeable odor.
2.
Propane extraction. Propane is used to dissolve the base oil components of the used oil, leaving behind an asphaltic residue that contains most of the additives and other impurities. A finishing treatment such as clay adsorption is usually used. Significant amounts of byproducts are generated that need to be disposed.
3.
Flash distillation. Used oils subjected to conventional vacuum distillation invariably leads to thermal degradation of the additives and fouling of the plant. However, thin film evaporation under very high vacuum allows the gas and lubricant oil components to be separated from a high-boiling asphaltic residue. The residue contains most of the additives and other contaminants.
4.
Demetallization and hydroprocessing catalysts. During the last 15 years, lubricant recycling processes have begun to focus on hydroprocessing. However, these catalysts are poisoned by many of the metallic compounds found in used lubricants. The demetallization step is used to treat the distillates produced after removal of water, solvents, light fractions and solids and thin film evaporation or vacuum distillation.
In a few re-refining plants that use flash evaporation/distillation, the base oil mixture recovered by thin film evaporation is hydrotreated and separated into different base oil grades by vacuum distillation. The resulting base oils are of considerably higher quality than those produced by most other re-refining processes having a very low sulfur content as a result of the hydrotreatment step.
Some re-refiners process the base oil mixture recovered by thin film evaporation in a conventional solvent extraction and hydrofinishing base oil plant. Solvent extraction further removes aromatics, especially polycyclic aromatics, from the base oil stream. The distillate from used oils is processed through the refinery as a separate stream from virgin vacuum distillates.
Key issues for re-refiners of used lubricants include:
•
The variability of feedstock quality
•
Unknown contaminants and the resulting complexity of the chemical analysis required to determine exact processing conditions
•
The removal of non-recyclable components such as oil-soluble oxidation products, condensed carbonaceous compounds, wear metals and degraded additives
•
Disposal of solid wastes
•
Re-refined base oil quality and acceptance
•
Economics.
Material recycling is preferred by the EU, but traditional re-refining processes face problems of byproduct disposal. The modern refining processes now being used in Europe and North America are also not free of problems, for example with catalyst life.
The older re-refining processes tended to produce lower quality base oils, with darker colors, lower viscosity indices and higher pour points than good quality API Group I base oils. The more recent hydroprocesses for re-refining are able to make good quality API Group II or Group II+ base oils. Some are even able to make API Group III base oils, depending on the quality of the feedstock.
In Europe, re-refined oils have been used for factory-fill by major German OEMs. Although many people are skeptical about the quality of re-refined oils, Mercedes-Benz 228.3, Volkswagen 500.00 and 505.00, and API SN and CJ-4 quality approvals have been obtained in re-refined base oils by several leading lubricant and additive manufacturers.
Mercedes-Benz, Volkswagen, Fiat, Ford and MAN all accept high quality re-refined oils. In addition, Mercedes-Benz and Volkswagen have confirmed that re-refined oils can achieve the same performance as new oils.
David Whitby is chief executive of Pathmaster Marketing Ltd. in Surrey, England. You can reach him at pathmaster.marketing@yahoo.co.uk.