Lube. Fail. Repeat.
Evan Zabawski | TLT From the Editor December 2014
Better practices for better reliability.
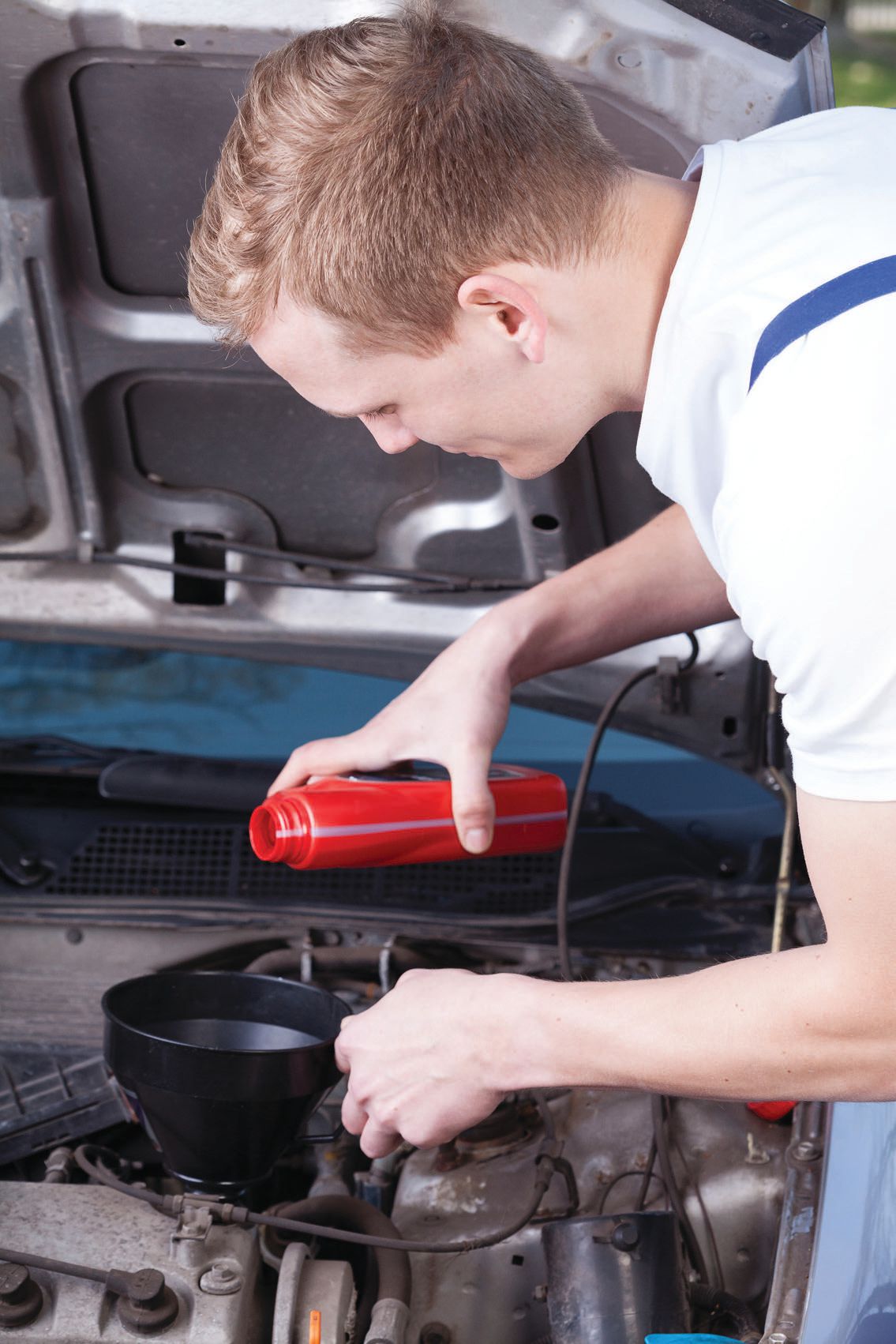
Many unnecessary oil changes could be avoided in the future with a greater emphasis on root cause investigations.
www.canstockphoto.com
PERHAPS THE MOST DIFFICULT PART OF INTERPRETING USED OIL ANALYSIS DATA is not deducing the cause and effects of abnormal data. It is deciding a proper corrective course. Far too often it is suggested that simply changing the oil will fix the problem. That is akin to placing a bucket under a leak. It will barely address the symptom, let alone cure the disease.
Lower levels of wear metals and contaminants are concomitants of oil changes, insomuch as fresh oil will lower these values simply by dilution. Given the same interval since the last oil change, the system is practically guaranteed to achieve the similar values again and only much higher values if a significant problem exists. Why then is the suggestion so common if, at best, this action merely buys some time?
We have probably all heard the following quote or a paraphrased variant: “If you keep doing what you’ve always done, you’ll keep getting what you’ve always gotten.” Sometimes a more humorous slant is taken by suggesting the definition of insanity is simply repeating the same action and expecting a different result. The most concise variant seems to be nothing changes if nothing changes. If we believe these doctrines, we should expect that if an asset fails with changing the oil as the only corrective measure, that same failure will occur again with continued operation under the same conditions.
A common example I use when teaching is an asset whose level of silicon and wear metals has increased in the latest of three samples since the last oil change. Sometimes when I ask what should be done to fix the issue, the answer is to change the oil and sometimes it is to inspect the breather or any other ingression point on the asset’s lube system. If the former, I ask the group if changing the oil really fixes anything, to which there is a general admission that it will have little lasting effect. If the latter, I then propose an assumption that an issue with the breather is discovered and the breather is repaired or replaced. When asked what to do next, the answer follows the familiar refrain.
The next point of discussion is to estimate how many samples it will take to determine if the ingression has been stopped, assuming regular sampling intervals. By changing the oil, the next set of results should almost certainly be lower, but it may take the same interval of three samples before obtaining positive proof.
When asked how many samples it would take if the oil was not changed after the repair, the unanimous answer is only one, though some mistakenly believe the next set of results will be lower rather than simply stabilizing at their current value. One must qualify that the level of silicon and the increase in wear metals be tolerable, since there is little point in leaving the oil in for one more interval if significant damage is occurring.
After such a discussion, the nods of recognition in the crowd indicate that a turning point has been reached, and perhaps many unnecessary oil changes can be avoided in the future with a greater emphasis on root cause investigations. At this point, I believe that oil analysis has a chance to be a successful condition monitoring tool rather than the documenter of failures.
Oil changes are able to address problems directly associated with the oil itself like a buildup of oxidation byproducts such as varnish. But even then, the oil change is not going to prevent the problem from recurring. It will only defer the next occurrence. Corrective measures, like offline filtration, are far more attractive, but they may not be a practical, feasible or economical solution in all cases.
We need to appreciate that changing the oil merely makes an oil analysis report look better. It does not fix contamination ingression, or balance, repair or realign parts. Break the cycle of repeated failures by reconsidering the validity of an oil change as a corrective measure.
Evan Zabawski, CLS, is the senior reliability specialist for Fluid Life in Edmonton, Alberta, Canada. You can reach him at evan.zabawski@fluidlife.com.