The Lubrizol Corporation
Enhanced Reliability Turbine Oil Additive Technology
By Ying Wang, Industrial Product Manager, The Lubrizol Corporation | TLT CMF Plus November 2014
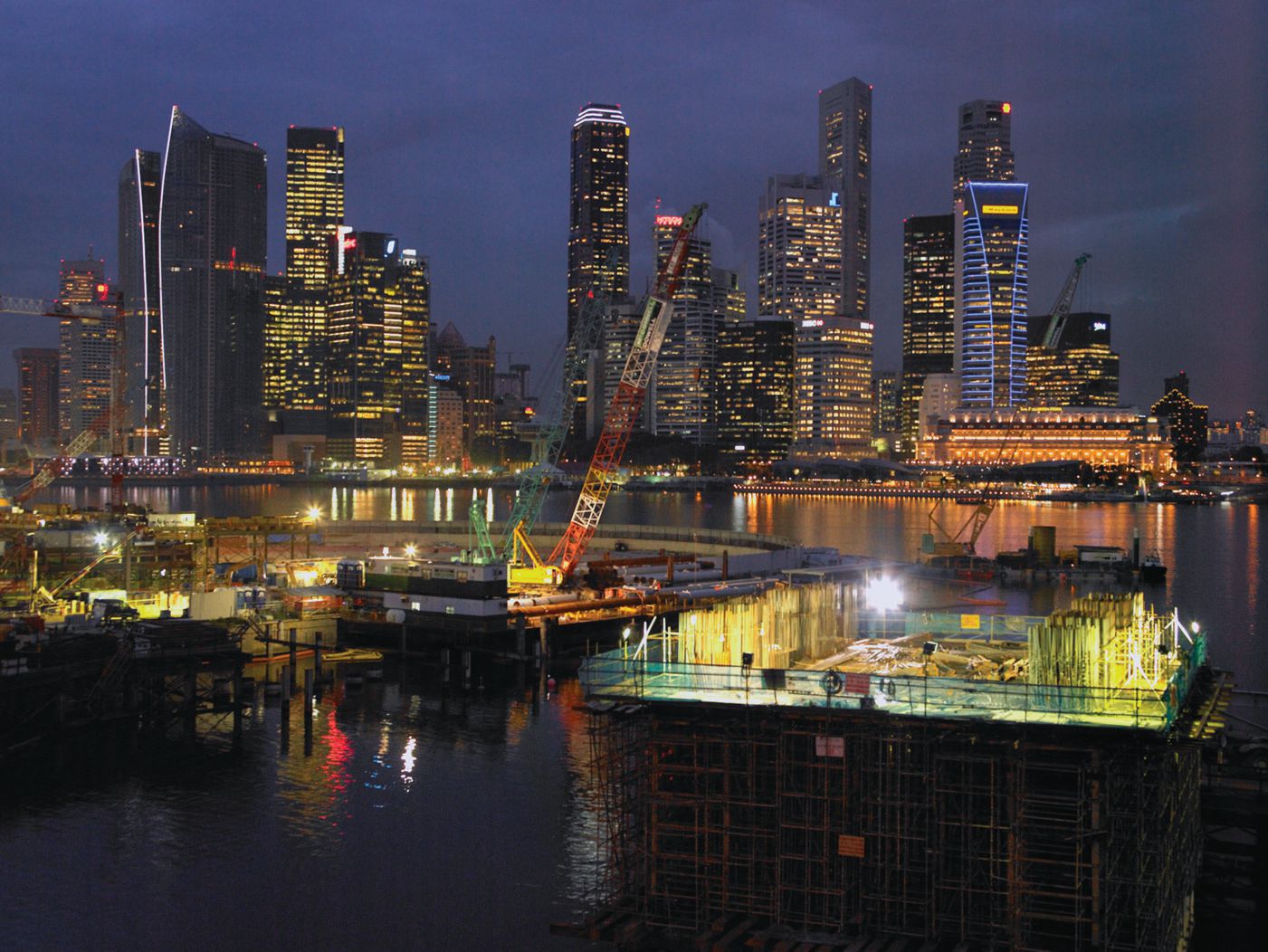
The world needs more power. According to the International Energy Outlook 2014 from the U.S. Energy Information Administration, the 524 quadrillion BTUs consumed globally in 2010 will increase to 820 quadrillion BTUs in 2040, an increase of 56% in 30 years. The need for power in developing countries is one of the key drivers for this increase in energy demand; more than 85% of this increase will come from these nations. As the world needs more power, it will need to be generated more efficiently and reliably.
For power generation plants to operate more efficiently, modern steam, gas and combined cycle turbines need to be lubricated properly and critical system components need to be protected. Power generation end users are looking for turbine oils that can improve system reliability and lower overall operational costs. Turbines are running at increased temperatures and more severe duty cycles, resulting in greater thermal and oxidative stress on the turbine oil. In addition, turbine oils are expected to last for several years in service with minimal fluid and associated system maintenance. It is imperative to help extend the life of turbines in power generation systems.
Lubrizol market research and field experience indicates that operators of power generation plants are concerned about turbine downtime and unexpected interruptions in service. According to this market research, 60% of turbine end users believe that varnish buildup in turbine components is a serious issue and impacts the reliability of their equipment. End users believe that valve sticking is a primary maintenance problem associated with gas turbine lubricants. Varnish deposits lead to valve sticking, which subsequently results in turbine trips. According to end users, a turbine trip can cost from $60,000-80,000 per event. The negative cost impact is not only from equipment repair and maintenance, but also from the plant not supplying power.
Prior to 1998, most turbine oils made oxidation claims of <5,000 hours in the ASTM D943 Turbine Oxidation Stability Test. When Group II and higher saturate base oils became available, turbine oils were reformulated to have outstanding oxidation resistance, and claims of >10,000 hours were common. Lubricant marketers stated that they tested the oil with a modified ASTM D943 because the test was designed for 10,000 hours and oil sampling had to be conducted at greater time intervals. Even with the greater oxidation resistance, turbines still had issues with the formation of varnish, sticking valves and unplanned downtime.
The use of Group II base oils could help in extending the oxidation life of the turbine oil if combined with the right additive system. Once the polar by products of oxidation occur however, they may be less soluble in Group II base oils in comparison to Group I. This means that although an oil may be more oxidatively stable, once the byproducts form, they may more readily deposit on critical surfaces.
Several filtration systems have been marketed to help remove the varnish precursors produced by the turbine oil. Many of these have been used successfully. However, they add an expense to the plant, take up valuable space and may require maintenance from time to time.
Lubrizol research formulators utilized a unique approach to improve turbine reliability through the development of advanced additive technology. Lubrizol RO93LA is a premium turbine oil additive technology designed for use in gas, steam and combined cycle turbines in Group II/III base stocks. This additive technology provides excellent resistance to oxidation and thermal degradation and has been designed to prevent the deposition of varnish on critical surfaces in turbine systems such as IGV valves, pencil filters and bearings. Lubrizol RO93LA also provides excellent rust and corrosion inhibition, rapid water separation, is low foaming and filters readily. It treats at 1.2 percent by weight and data are currently available in Chevron, Mobil EHC, Motiva and PetroCanada base stocks. Lubrizol RO93LA meets or exceeds many key OEM/industry credentials in select base oils as shown in
Table 1.
One of the key performance characteristics of Lubrizol RO93LA is its varnish deposit-mitigating capability. It is impossible to prevent oxidation of a turbine oil, but Lubrizol RO93LA was designed to slow down the thermal and oxidative degradation process. Once byproducts from oxidation form, the technology embedded in Lubrizol RO93LA prevents the deposition of this material onto critical turbine system components. Lubrizol’s turbine oil additive technology provides peace of mind for both the turbine oil supplier and end users because of fewer field issues, less down time and lower operating costs.
Lubrizol has generated extensive laboratory performance data supporting the capabilities of this additive technology. To demonstrate the performance and the market significance of Lubrizol RO93LA, a field demonstration has been in progress for nearly 4.5 years with a power generation end user. Prior to the field demonstration, the end user was experiencing valve sticking – and turbine trips were common. This resulted in unplanned downtime, decreased reliability and increased cost. As part of their proactive maintenance plan, the end user had been replacing valves every six months – at a significant cost in time and money.
The field demonstration was conducted in four GE Frame 7FA combustion turbines that had been experiencing reliability issues due to varnish deposits and resulting turbine trips. All four units were drained and cleaned per ASTM D6439 Protocol, filled with new oil filtered to GE Specification (16/14). There was no additional chemical cleaning or flushing performed on the turbines, which saved time and money for the end user. Two units were filled with turbine oil containing Lubrizol RO93LA and two units were filled using commercial turbine oils. All four units are of similar service and duty cycles and are primarily utilized for peaking power service.
During the 4.5 years of field testing the two units with Lubrizol RO93LA have had no valves replaced and no oil-related trips. The units filled with conventional turbine oil technology have still had preventive maintenance with valves being pro-actively changed every 6 months. Lubrizol RO93LA has shown outstanding performance based on quarterly test results. For example, Lubrizol RO93LA performs superbly in the QSA test that rates varnish level on used oil samples. The photos of QSA test filter pads after 42 months of service showed no signs of varnish at all from the turbine oil containing Lubrizol RO93LA. Varnish Potential Ratings after 42 months were 5. As a comparison, the Varnish Potential Rating for the oil prior to drain was 77 (
Figure 1). Turbine deposits also have been monitored from metal coupons half submerged into the oil sumps in a special set-up. Every 6 months, a metal coupon is removed from the system for both visual and EDS (Energy Dispersive Spectroscopy) analysis and there has been no evidence of varnish formation. In addition, the viscosity has remained constant. There has been little to no loss of oxidation life basis results of RPVOT (ASTM D2272) or RULER™ (Remaining Useful Life) testing.
Figure 1. After 42 months of service, no varnish is present for the turbine oil using Lubrizol RO93LA technology using Varnish Potential Ratings. Shown as a comparison is the result from the final drain of the oil prior to the field demonstration.
The end user has been very satisfied with the performance of this turbine oil technology experiencing no oil related trips, no premature valve changes and no unplanned downtime in a challenging environment with peaking units that have many stops and starts per year. The turbine systems will continue to be monitored closely throughout the remainder of the field trial.
Lubrizol RO93LA is a unique lubricant additive technology that provides the end user with a solution to a problem, common among many turbine oil applications in the market. Products formulated with Lubrizol RO93LA will provide a number of key benefits to end users:
•
Outstanding resistance to the deposition of varnish deposits that can lead to costly turbine trips, which in crease power generation costs and de crease overall plant reliability
•
Excellent oxidation and thermal stability helping to optimize oil drains
•
Meets and/or exceeds many major OEM and industry specifications in globally available base oils, helping to provide peace of mind for end users and reduce complexity
•
Excellent rust and corrosion protection to protect equipment components
•
Excellent lubricant demulsibility, important in operating environments prone to water contamination
•
Excellent filterability, even in the presence of contamination, helping to reduce downtime and extend equipment life
Lubrizol market research confirmed a known problem in the power generation industry. Varnish deposition has had a negative impact on plant reliability and efficiency. Lubrizol RO93LA technology addresses the issue and field testing to date indicates that the problem can be reduced or potentially eliminated with the right choice of additive technology.
RULER is a trademark of Fluitec International LLC