The challenges of turbocharging
Dr. Edward P. Becker | TLT Automotive Tribology June 2014
Strategies to manage heat and friction.
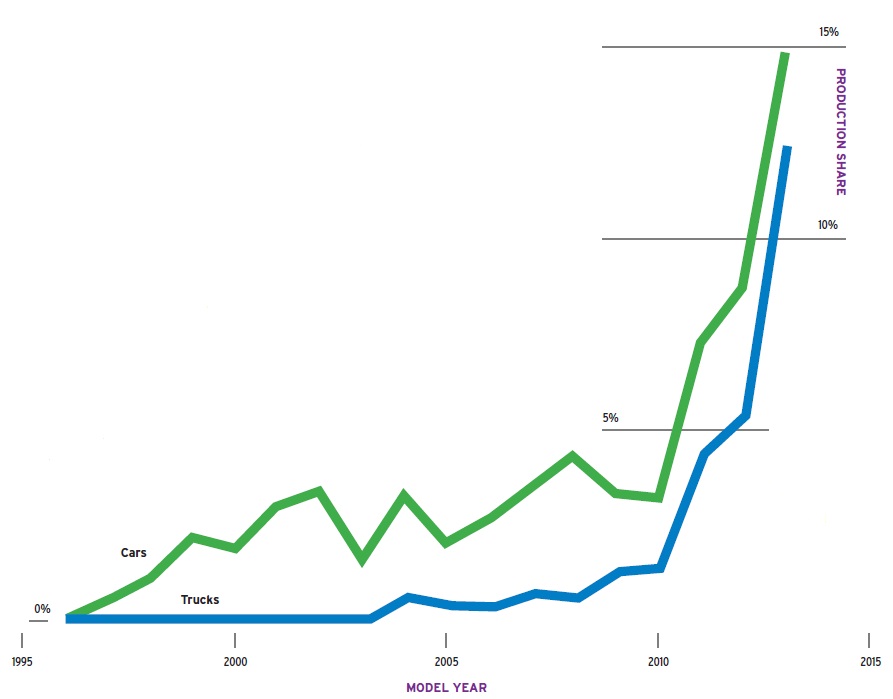
Source: U.S. EPA Report, EPA-420-R-13-011, Light Duty Automotive Technology, Carbon Dioxide Emissions and Fuel Economy Trends: 1975-2013, December 2013.
TURBOCHARGING HAS BEEN AROUND almost as long as the internal combustion engine. However, as the graphic shows, there has been a remarkable increase in the market share of turbocharged engines within just the last three years.
As the U.S. Environmental Protection Agency (EPA) reports, prior to 2010 most turbocharged engines were in large, 8-cylinder performance packages. By the 2013 model year, more than 60 percent of turbochargers were installed on 4-cylinder engines, often replacing larger engines. EPA calls this trend “turbo-downsizing.”
Basically, a turbocharger consists of two turbines connected by a shaft. One turbine is driven by the exhaust gases from the engine, while the other is placed within the intake system and compresses the incoming air. By putting more air in the cylinder, more fuel can be added, resulting in more power per stroke. Thus, it is possible to use a smaller (and lighter) engine to provide the same amount of power to the vehicle.
While the principle is simple enough, the practical problems are manifold. The high temperature of the exhaust gases requires advanced (and expensive) materials for the driven turbine to prevent creep. The turbocharger is not mechanically linked to the engine crankshaft (unlike every other spinning component), so the speed of the turbocharger is more difficult to control.
In addition, under speed results in a loss of engine performance (called turbo lag at low engine rpm), while over speed can result in too much air being forced into the cylinders and damaging the engine. The top speed of a typical engine turbocharger can be in excess of 15,000 rpm, much faster than any other engine component.
For the engine tribologist, the primary challenge is the bearing that supports the common shaft between the turbines. The friction must be kept very low to facilitate the high rotational speed, and the bearing must manage a very high heat load from the exhaust gases.
The primary solution in the modern engine is to use a fluid film bearing, the fluid being engine oil. Pressurized engine oil acts as both a lubricant to minimize friction and as a coolant to remove heat. While these are the two main functions of oil throughout the engine, the turbocharger bearing takes these to new extremes.
The latest specifications for engine oils require testing for resistance to forming high-temperature deposits, primarily to prevent turbocharger bearings from seizing, and resistance to oil aeration. Remember, air is not a coolant, so too much air in oil can result in turbocharger bearing overheating.
So if your car is turbocharged—and if your current one isn’t, there’s a good chance your next one will be—be sure to read your owner’s manual and use only grade of oil recommended for your vehicle.
Ed Becker is an STLE Fellow and past president. He is president of Friction & Wear Solutions, LLC, in Brighton, Mich., and can be reached through his website at www.frictionandwearsolutions.com.