Boeing, Boeing…
Robert D. Heverly | TLT President's Report May 2014
A behind-the-scenes factory tour revealed lubrication practices of the highest order.
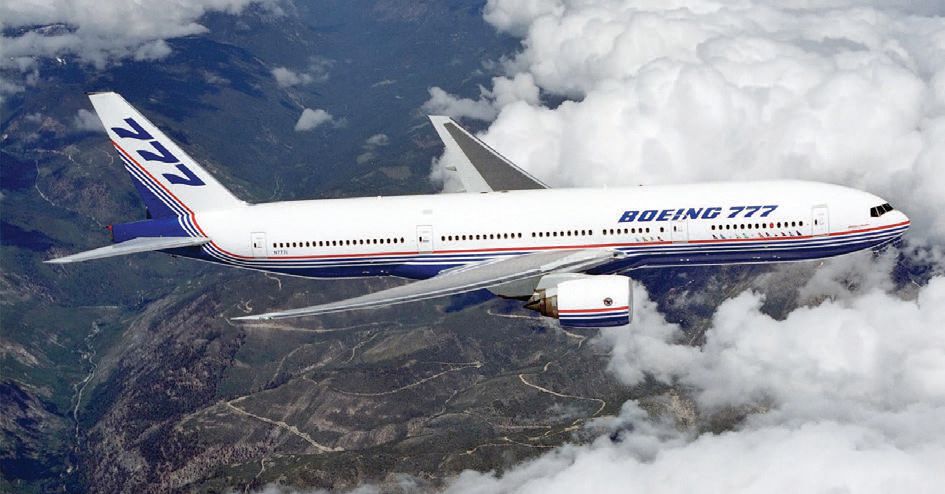
When it comes to lubrication, Boeing’s attention to detail and precision is beyond what I knew possible.
www.canstockphoto.com
ONE OF THE BENEFITS OF BEING STLE PRESIDENT is visiting local sections and meeting long-time members. I recently did a three-day West Coast trip with fellow board member Greg Croce from Chevron where we visited the Northern California, Seattle and Portland Sections. There are lots of positive things going on in all three sections.
Traveling with Greg was fun. We were not quite Planes, Trains and Automobiles (more like the Odd Couple) but all a positive adventure. Greg has had lots of driver safety training and is an avid driving coach from the passenger seat. Our flight from Oakland to Seattle was very bumpy. It turns out Greg does not like to look out the window and see the wings shake. He didn’t need a blindfold, but neither did he look out the window much. My dad was a military pilot, and I spent the early part of my life on airbases. When he was on alert, we’d sometimes meet him for a picnic down by the runway and watch the planes take off and land. I tried to explain wing physics to Greg, but my explanation probably made him more anxious.
Greg had a surprise upon arrival in Seattle. Boeing, an STLE corporate member, offered us a behind-the-scenes tour of its Everett manufacturing complex. We met Chuck Sheldon, an STLE member and CLS holder, and his co-worker, Mark Calkins, early Thursday for a tour focusing on Boeing’s lubrication practices. Chuck is the lubrication program manager, and Mark is the man in charge of reliability for all equipment in the Everett facility, which covers 98.3 acres and encloses 472 million cubic feet of space. Some 7,950 pieces of equipment there require some sort of lubrication or coolant servicing. There are also 10,000 airline lubricators that require regular refilling and calibration.
This site is where Boeing assembles the 747, 767 and 777 planes. Impressive is not a strong enough word to describe this building—it seems like there are a million things happening at once. We headed to our first stop at the Lubrication Resource Center where we met the team responsible for running the lubrication programs. This was no mere oil crib but a spotless shop for all things related to lubrication.
The lubricants are all color-coded to match the color codes on the oil reservoirs and application points. Coalescing filters on the drums eliminate moisture from entering when oil is dispensed with dedicated pneumatic oil pumps. To reduce the potential for cross contamination, these pumps are never open to the atmosphere. An inventory chart near the entrance shows the location of all lubricants, which are transferred to color-coded, sealable and refillable containers to minimize cross contamination and exposure to the industrial atmosphere. A similar organizational system is set up for greases. These guys keep their work areas spotless.
Boeing uses a national lubricant supplier, and the very clean lubricants it specifies have solved reliability issues and prolonged equipment life. This lubrication program, administered by technicians using the latest concepts, has reduced the cost of machinery over its lifecycle, and Boeing has the foundation in place to maintain continuous improvement. We were very impressed.
Now about those wings Greg didn’t like to see bouncing. We saw Boeing making the wings for the 777. Each riveting machine is big as a small house, and the attention to detail and precision is beyond what I knew possible. Boeing tests the wings to failure to determine how much they can bounce. What this means is that after the airplane has been through a thorough fatigue test, the FAA requires the wings to be tested to 150 percent of the designed load, and the wings are pulled to their breaking point. This is much higher than the most extreme flight conditions and is much more than anyone would imagine for flexibility. A wing has never broken in flight.
I have not flown with Greg since our tour, but I’m sure he is now comfortable watching the wing tips vibrate during bumpy flights.
Representing the Houston area, Rob Heverly is a technical sales representative for Vanderbilt Chemicals, LLC, in Norwalk, Conn. You can reach him at rheverly@vanderbiltchemicals.com.