Spring is in the air
Evan Zabawski | TLT From the Editor March 2014
Busy as a bee, trying to solve a problem.
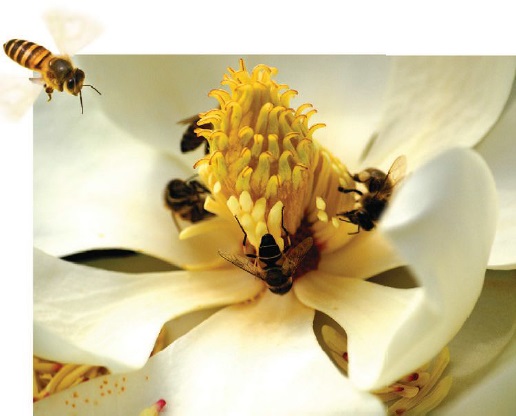
Identifying the adversary allowed the project to finish successfully.
www.canstockphoto.com
ONE MARCH NOT SO LONG AGO, I found myself visiting a power plant nestled beautifully between a river and a grove of majestic magnolia trees. Little did I know this picturesque setting would host one of my greatest challenges in the field of particle count analysis.
The purpose of my visit was to verify the cleanliness of the hydraulic control fluid for a massive nuclear-powered steam turbine undergoing a fairly routine oil flush. The control oil system was being flushed, then rinsed and eventually filled with a new charge of fluid. Samples of all fluids were taken at set intervals and analyzed in a lab that was set up on site.
The baseline sample was unremarkable, and the “as found” sample of the used control fluid was characteristically contaminated. As the flush continued, the turbulence of the flow during the flush produced correspondingly higher particle counts on subsequent samples. Eventually, as was normally expected, the contamination levels reached a plateau and then began to show a decrease in contamination. This indicated that no further debris was being loosened and that it was time to end the flushing portion and begin a manual wipe down of the reservoir. This also meant my services were no longer required that day since the flushing crew needed time to perform these tasks before refilling the system with rinse fluid.
When I arose the next morning, I noticed the morning dew on my rental car had acted like a magnet, some yellowish dust necessitating the use of my wipers before I could drive back to the plant. Upon arrival, I pulled a sample of the rinse fluid to find the system was well on its way to achieving the required cleanliness for termination of the flush. Eagerly anticipating the last step of filling the system with the final fill, I pulled a sample from the discharge of the kidney loop filtration system that had been circulating this fluid for several days, albeit outdoors.
It is worth noting the filtration was comprised of triplex β
3=1000 filters in series, meaning three stages of 1000:1 reduction of 3 μm and larger particles. The expectation was to see virtually no particles under the microscope; however the reality was quite different. Not only was the particle count itself about five times higher than typically measured on other projects performed by this same crew, the particulate found in the 5- to 25-μm range contained some unusually spherical and opaque particles. Being quite perplexed, it was decided to let the kidney loop run overnight and continue circulating the rinse fluid until the final fill was satisfactorily clean.
The next morning I repeated my new ritual of cleaning the windshield before setting off. The first order of business was to take a new sample of the final fill in hopes its results would signal a turning point with regards to the progress of this project. It did—unfortunately not in the intended direction. The results showed no improvement, and a routine sample of the rinse fluid showed that it, too, was now contaminated with these unknown spheres. We had to figure out where the contamination was coming from.
Deciding that a lunch break was in order, I headed back to my car only to find it bathed in that yellow dust again. I immediately headed back and asked a plant employee if he could explain what it was, and the answer was pollen from the trees. Grabbing a sample bottle, I headed to the berm containing the final fill fluid and scooped up some water from a yellow-rimmed puddle of rain water. The particulate in the rain water was a match!
The confirmation created the impetus to move the final fill totes inside to continue to polish the fluid to acceptable levels. It also elicited an admission that the night shift had propped open the man-door to the control oil system in order to cool off. Identifying the adversary allowed the project to finish successfully and establish stricter protocols for the next project on the sister unit the following spring.
Evan Zabawski, CLS, is the senior reliability specialist for Fluid Life in Edmonton, Alberta, Canada. You can reach him at evan.zabawski@fluidlife.com.