How will oil analysis change five years from now?
TLT Sounding Board February 2014
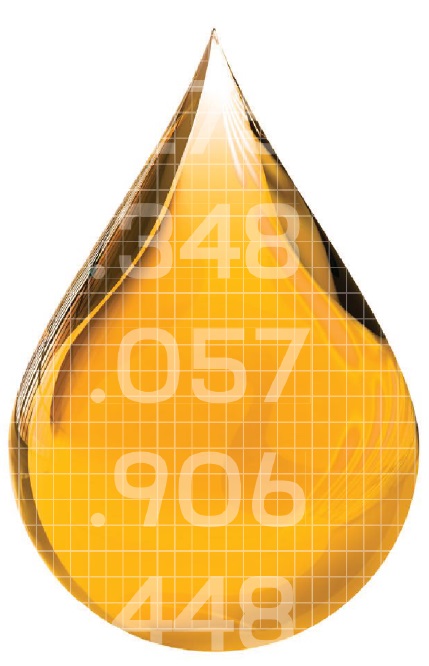
www.canstockphoto.com
Nearly two-thirds of TLT readers believe that oil analysis is on the cusp of major changes compared to how it’s traditionally been conducted. More real-time testing with handheld instruments (potentially mobile devices) at the machine’s location is expected. Most everyone agreed results would be generated quicker and delivered to the customer faster. Asked about the most important elements of oil analysis, readers noted the importance of proper sampling techniques, providing accurate information about the machine’s usage and operating environment, taking consistent reports to establish baselines as opposed to reacting to a single value and acting on the report’s recommendations. Many TLT readers noted the ongoing battle in getting senior managers to buy into the program. “Without their support, the program’s longevity and effectiveness are weakened,” said one respondent.
It will give faster results.
More recovery or decontamination efforts. Offline filtration systems. Possibly more on-site equipment or built-in inline testing.
Basic analysis will occur on-site. More synthetics, more on-site particle counting equipment.
Sensor technology will make oil analysis substantially different.
It will most likely be more done with portable instruments at the plant sites by reliability personnel.
There will be new ASTM tests to better evaluate the suffering points of the newer oil technologies.
As the cost of finished lubes continues to rise, the end-user will want to extract the most value out of a lubricant.
I would expect more automated oil analysis at the local level so samples are no longer sent to an analysis lab but are analyzed by a handheld device that provides results almost immediately.
We will see a significant increase in the use of mobile devices to screen oil condition at first line.
Oil analysis in the field as accurate as any lab.
Less hands-on work as technology becomes more prevalent.
I can definitely see mobile apps and more employees understanding and being trained in oil analysis.
I doubt much will change in the next five years.
I expect real-time, online oil analysis sensors installed directly onto equipment.
The price will be lower and the technology nearer the people.
Testing laboratories will have to get creative and find ways to justify their services. I suspect they will have to offer more than just data.
Increased use of full synthetic lubricants. Increased use of oil analysis requiring better ways to monitor and act on incoming data.
In the future, your reports will come from lab to phone for viewing on the fly.
Testing should remain the same or similar to adapt with new products. However, reporting should certainly be accessible with mobile devices and other Internet access/platform.
I don’t really think it can go much further. With the technology available, it is providing great insights into failure analysis and product life.
Less reliance on the laboratory results. With handheld and bench devices in-house, answers are available within minutes instead of hours/days. Of course, the lab report is still needed.
A continuous inline condition monitoring gadget in diesel truck fleets could dramatically reduce the number of samples sent to traditional used oil analysis labs.
As oil quality continues to improve, there will be a greater percentage of certain applications, such as automatic transmissions, that will be filled for life. As inline oil analysis and remote monitoring capabilities expand, there is likely to be more remote monitoring through a centralized hub.
The use of new technologies will enable more equipment to notify owners when oil needs to be changed.
I think results will be available quicker, and each sample will have more parameters tested.
I think there will be more real-time and online oil analysis, giving operators instant information about when the fluid needs to be changed and when equipment is having issues.
It will be exactly the same. No one will bring a mobile device into a dirty machine shop floor. Maybe in a lab there will be more tablets, but that’s a big maybe. I still like writing on paper.
I think portable devises will continue to gain acceptance and market share. Ultimately, miniaturization of tests to the point of having a “lab on a chip” type design is the goal.
More oil analysis on the fly. Real-time oil analysis will be more common.
I would like to see a reasonably priced portable unit that can do a thorough analysis in the field in real-time.
In-service grease analysis will be more mainstream.
I think with wireless monitoring and the growing understanding of world-class maintenance, more analysis will be done in-house.
More rapid responses focusing on root of problems.
More online real-time analysis. Will trends be monitored adequately?
There will be more exchange of information electronically for sample registration, tracking and reporting. The use of sensor technologies and on-site testing will increase. These will provide basic rapid information to the users. Laboratories will need to become more specialized in filling in the gaps in this information through proper advanced test selection. While sample volumes will drop, revenues should increase due to the increase in specialized services.
All samples will be barcoded for identification and registered using a smartphone app.
Oil testing will be more of an on-site application with the site-maintenance expert conducting the analysis.
Much easier for routine analyses. Much more powerful for specialized analyses.
We see wide variations in analysis use, from zero by some companies, to complete programs covering almost all equipment. I believe in five years we will see more companies taking the plunge and investing more resources to obtain the data. The most important thing is to act on that data.
Do you think oil analysis is on the cusp of major changes compared to how it’s traditionally been conducted?
Yes
63%
No
37%
Based on responses sent to 13,000 readers.
What is the most important issue in analyzing oil analysis reports?
Diagnosis: Is the equipment right or wrong?
Each report is a peek into a specific time element that, in itself, is not necessarily relevant. Trending is the issue.
Read the data yourself. Lab technicians don’t have the time to interpret and often misread data, arriving at wrong conclusions. If you don’t look for yourself, it will cost you.
Trending is just as important as established limits.
Knowing the correct data such as specific lubricant, machine data and seeing a trend.
In addition to lubricant condition, equipment condition also can be determined.
Interpreting how the lubricant condition will affect machine serviceability and condition.
Trends are more important than any particular number of a single constituent.
Proactively understanding oil condition is important in helping customers understand when they need to take actions to change oil and maintain the equipment.
Accuracy of oil analysis to determine oil conditions.
People need to understand these reports can be quite subjective. Often results depend on the person doing the analysis.
Understanding the application and piece of equipment.
Fault diagnosis: Make a judgment on the fault and its main cause.
Relationships between perceived severity of results and actual asset risk.
Trending is critical as well as full information regarding the oil sample.
That the data is only as good as the procedures used to gather the sample.
What a normal sample of that particular product should look like and trending it over time.
Understanding how your current report relates to the new oil and also trending patterns.
The machine’s operating conditions.
You need to understand the chemical processes that may be degrading the fluid.
Trend analysis. Not focusing on just a single sample but how past, current and future data relate to each other.
To actually know what you’re looking at and what you’re looking for.
Knowledge of additive composition and chemistry.
How and where the sample was made.
With best practice sampling and frequent sampling, the results are better understood. Interpreting the data is then simple and not guesswork.
Improper sampling (technique, location, etc.) may create false alarms or a false sense of security.
Taking action on the data is the reason for the program.
Remember that oil analysis is a trending tool. The results of a single oil analysis determination can be inaccurate with regard to the true condition of the lubricant and the equipment.
How are you going to use the data? For example, is it to schedule downtime?
You need to know more about the starting point lubricant formulation before you can really understand what you are monitoring.
Fitness for purpose and evidence of wear or overheating.
Experience and a knowledge of the specific equipment. Don’t do things in a vacuum.
Assuming the test results are accurate, having the proper background information about the sample is important for properly interpreting an oil analysis report.
History—comparisons on a given oil in a given engine in comparable operating conditions.
What it actually means and what the data shows as compared to new oil.
Baselines and how trended analysis is deviating from this baseline.
It is very important to understand the equipment being sampled and environment where the equipment is located.
The importance of reading the recommendation comments from the laboratory prior to reviewing the numerical results. The comments are a good summary of the data to follow and address changes in wear and lubricant physical properties. Jumping directly to the data often brings minor data changes to the front that have no real diagnostic value.
Look for multiple signs and symptoms to diagnose the machine’s condition.
The health of the fluid.
The limits that should be set for that specific type of equipment.
What the numbers mean and how a trend is established.
Trending shows change in operating conditions and wear rates.
What’s wrong and why.
What are the most common mistakes people make with oil analysis?
Improper sample taking and incomplete information.
Improper flush of sample valve and/or tube. The importance of drawing during flow without disturbing sample valve or introducing external dirt, which can result in concentrated, contaminated or unrepresentative sample.
Expecting that the oil analysis is going to describe exactly where the failure is.
Besides cleanliness issues and lack of continuity, it’s thinking that one sample makes a trend.
Trusting the comments section of the report.
Failure to provide the required sample information to provide an accurate oil analysis.
Not following up when a condition indicates a potential problem.
Being solely dependent upon oil tests and not considering other factors such as vibration, operating parameters and maintenance practices.
They do not fully understand the implications of some of the minor constituents and therefore make errors in application of the analytical information.
People assume oil analysis has the same properties in engines.
Waiting until they find problems with equipment before starting to test on oil. This is often too late as the equipment has started being affected from the “bad” oil’s condition.
Oil renewal based on oil analysis.
Relying on the report without taking into account everything that is going on with the specific equipment and operating systems.
They go through the motions of pulling samples but don’t follow through when the reports come back.
Ignoring reports with no alarmed values, waiting for values to exceed alarms before reacting and not properly evaluating what triggers an alarm.
Not understanding how to read the reports and what the data is telling us.
Ignoring environmental factors.
Providing sketchy supporting information to the lab. Not taking actual runtime into account when reacting to changes in results.
Not taking secondary samples.
Sample contamination.
Only looking at highlighted areas or zeroing in on the area where it is passing (green) concerned (yellow) or needs changing (red) and not actually reading the entire report and individual results.
Only looking at the comments and not the actual test data.
Not reading the reports or knowing how to interpret them.
They don’t see trends and element rise (Fe, Cr, Cu).
Assuming that the sample received is representative of the bulk of the oil.
Not recognizing contaminants and diluents.
Equipment and lubricant decisions based on a single set of analysis results.
Testing only when there is a problem.
Most people cannot interpret the results and lack a baseline to understand what those changes really mean about the fluid performance.
They make a conclusion before completing all the tests. They jump the gun with a couple test results when they don’t have the full picture.
Not recognizing that competing physical and chemical processes can counteract each other.
Taking action without confirming an abnormal finding.
Not viewing all results holistically.
Not doing it often enough. The real value is in wear tending and optimizing lubricants and change intervals.
Failure to interpret properly the trending of results away from baseline data, resulting in the customer thinking the oil is satisfactory for continued use when, in fact, it is not.
The program is not sold to the top managers.
People think in terms of Go/No Go when they read reports. Data are seen in black and white with no room for nuance in interpretation.
Sending in samples without a reference point.
They only react to cautions or alerts, have very little ability to understand the data that the analysis produces and don’t do consistent periodic reviews to identify suffering points.
Mislabeling samples can create a lot of false red flags.
Not requesting the correct test slate to meet their goals.
Waiting too long to retest to confirm results.
Taking the analysis as a be-all and end-all. One should take time to make sure that the analysis is a value-added item that enhances equipment life.
Editor’s Note: Sounding Board is based on an e-mail survey of 13,000 TLT readers. Views expressed are those of the respondents and do not reflect the opinions of the Society of Tribologists and Lubrication Engineers. STLE does not vouch for the technical accuracy of opinions expressed in Sounding Board, nor does inclusion of a comment represent an endorsement of the technology by STLE.