10 trends shaping tomorrow’s tribology
Jeanna Van Rensselar, Contributing Editor | TLT Feature Article February 2014
Today’s lubricants won’t fit market needs in 20 years. Here’s a look into the future.
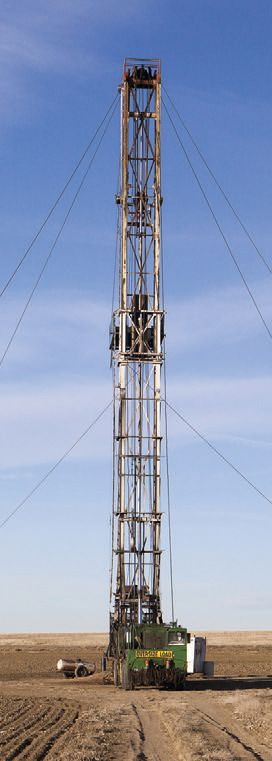
www.canstockphoto.com
KEY CONCEPTS
•
New equipment design is driving rapid evolution in basestocks and additives.
•
Trends such as the push for fuel efficiency and the rapid introduction of alternative fuel vehicles into the market are affecting lubricant requirements.
•
Macro trends such as the emergence of new economies and the widespread availability of natural gas in the U.S. are affecting the lubricant market and lubricant production.
ISSUES LIKE RISING EQUIPMENT TEMPERATURES, increased demands on fluid life and a rapidly changing feedstock landscape raise the question as to whether today’s lubricant technology will be able to satisfy future applications— whether technology can keep pace with new realities.
For example, the global population is projected to increase from 7 billion to 8.3 billion by 2030. This is an increase of less than 12 percent. But income is likely to double over the same period. This significant disparity between projected population and income growth will drive a consumption explosion in emerging economies (
1). These emerging economies and their effect on the lubricants market is just 1 of 10 trends that, say the experts TLT spoke with, will drive lubrication technology and the lubricants market over the next decades.
To prepare for tomorrow, pay attention to these trends today.
THE 10 TRENDS
1.
Extended drain intervals
2.
Better basestock availability
3.
Introducing and eliminating additives
4.
Equipment design changes
5.
New surface treatments
6.
Emerging new economies
7.
Demand for better fuel efficiency
8.
Increase in alternative fuel vehicles
9.
Tighter environmental regulations
10.
Widespread availability of natural gas
1. Extended Drain Intervals
In general, the trend toward longer and longer oil change intervals (up to 20,000 miles) is due to better fluid performance, better machinery engineering and more sophisticated fluid analysis.
The end game would be the development of a fill-for-life fluid endorsed by OEMs. While that’s not on the horizon, several factors could change that, including:
•
A basestock that can retain its properties for the expected life of the machine.
•
A
cost-effective metal coating that eliminates corrosion and wear.
•
The development of better filters.
•
A
cost-effective embedded sensor that monitors for anomalies.
The bottom line is that the primary functions of oil are lubrication, temperature control and cleaning. So an oil that never needs changing would need to do all three for the expected life of the engine, a rather tall order.
2. Better Basestock Availability
Dr. Markus Scherer, director global marketing and product development basestocks, fuel and lubricant solutions for BASF SE, says, “With hydrocarbons performance, we have already reached a plateau for selected industrial applications, and there will be more to follow. There are an increasing number of applications where conventional base fluids cannot be employed anymore.”
One example he cites is aviation turbine lubricants where, due to superior stability, specific ester basestocks are used instead of mineral oils or even PAOs. Another area is the compressor industry. Here, depending on the kind of compressed gas, either ester or polyalkylene glycol (PAG) fluids are the first choice, not only because of gas miscibility characteristics but also due to lower friction resulting in better energy efficiency and extended equipment life.
The performance qualities separating heavily processed mineral oils and synthetic oils will continue to narrow, as researchers manipulate the molecular composition and structure of Group II and Group III base oils through process improvements, better hydroprocessing catalysts and alternative feedstocks, including natural gas. These GTL (gas-to-liquid) feedstocks (informally classified as Group III+) are the result of the natural gas-to-wax Fischer-Tropsch process and have game-changing properties that include VIs significantly higher than PAOs (
2).
Driven by the substantially lower price of Group II and Group III oils, and despite the improved quality of PAOs, the synthetic lubricant market is rapidly shifting to dramatically better Group II and Group III basestock, which delivers performance previously achieved only in niche applications using PAOs and other specialty stocks. The sheer availability of Group II and III mineral oils is accelerating this conversion.
Daniel Zweifel, senior application specialist, Dow Europe GmbH, explains, “In the future, higher requirements for thermo-oxidative stability, longer fluid life and higher thermal and mechanical loads on lubricants can be expected. “The trend toward oils with significant lower viscosities will continue. The demand for high quality base oils with low viscosity to satisfy OEMs is increasing. There is a clear need for high quality Group IV and V oils. The major challenge will be the engineering of formulations with existing Group V base oils to meet these future requirements.”
STLE-member Dr. Vasu Bala, global product development, fuel and lubricant solutions, BASF Corp., adds, “I see a growing demand for use and applications of synthetics or Group III basestocks or thickeners. Performance trends lend to longer drain intervals, higher operating temperatures and reduction in overall maintenance/downtime. End-users are becoming very informed and discriminatory against lower performance lubricants in their expensive vehicles.”
He continues, “We have not reached a plateau with hydrocarbons yet. There are still synergies between additives and base oils that are yet to be exploited. This is facilitated if hardware design incorporates additive/lubricant development at the conception/ inception stage of any new engine/ gearbox.”
FINANCIAL REALITIES
Future lubricants are going to require significant research and development outlays, and not all companies are willing or able to make that commitment anymore for reasons that include feedstock price and availability uncertainty, dwindling government support and an ever lengthening lab-to-market cycle.
Dr. Sigismondo Ferrante, CEO of oil analyst SMOC Europe S.r.l., says, “Engineering a new lubricant requires a considerable investment without a sure payout. You can do everything right and then when it hits the market nobody buys it.”
Dr. Markus Scherer, director global marketing and product development basestocks, fuel and lubricant solutions, BASF SE, believes that when it comes to cost-efficient novel basestock technologies, chemical companies need to partner with lubricant developers. He says, “Chemical companies provide development and manufacturing know-how often in conjunction with backward integration into key raw materials required for novel synthetic base oils. Because of this, partnering of a lubricant company with a chemical company for novel base oils will accelerate time to market.”
3. Introducing and Eliminating Additives
Referring to new equipment design, Bala explains, “Additives (extreme pressure, antiwear, dispersants, antioxidants) have to keep pace with improved stability—measured decomposition between surfaces and bulk phases. The immediate approach is to use higher concentrations of existing additive types in more stable Group IIIV highly refined and synthetic base oils.”
The development of commercially viable green additives that perform as well as mineral-based counterparts is a glaring need that could expand the current market for biobased and biodegradable lubricants.
Nanoparticle-based lubricant additives (mostly boron or carbon) that can compete on performance with traditional additives are being developed. These additives interact with the contact surface to produce a low friction/ protective boundary film. They significantly improve protection against (nearly eliminate) micropitting and can drastically lower friction and wear in industrial and motor vehicle applications. Since they substitute for sulfur- and phosphorous-bearing additives, nano-based additives reduce environmentally hazardous emissions and wastes.
“One interesting trend that we see is the demand for fluids with better air release,” Zweifel says. “This is being driven by the trend to design equipment with smaller reservoir sizes. Entrained air can cause severe equipment damage. Some OEMs recognize this and are specifying lower air release values of newer fluids.”
Relatively newer basestocks may require fewer additives. For example, Group III+ basestock has a naturally higher viscosity and may require little or no VI improver.
RENEWABLE LUBRICANT REGULATIONS
Lubricant renewability is a key requirement of the EU EcoLabel. The second iteration of the U.S. EPA Vessel General Permit (VGP) replaced the initial legislation on Dec. 19, 2013. It requires applicable ships in U.S. navigable waters to use environmentally acceptable lubricants as defined in the legislation for certain applications including bow thrusters and stern tubes.
The EU EcoLabel requirements for biodegradability, aquatic toxicity and bioaccumulation served as a guide in the development of the U.S. EPA’s VGP legislation. STLE-member John Sherman, technical manager, fuel and lubricant solutions, BASF Corp., believes that the next iteration of the VGP legislation will continue to follow the EU Ecolabel requirements, with
minimum renewable content added to the requirements for environmentally acceptable lubricants. If this happens, it would significantly increase the importance of renewable lubricants in the U.S.
4. Equipment Design Changes
“Newer OEM design approaches impose more stress on the lubricants mainly in the form of elevated temperature and shear stress,” Scherer says. “We regard this as a good challenge to base oil and additive producers. Not surprisingly, over the last five years this evolved as a major market driver, both for improved additives and novel, less conventional Group V basestocks.”
OEMs are continually demanding better performance from lubricants. Trends in equipment design include higher-power machines that are often lighter and smaller with reduced fluid reservoir sizes. The two main benefits in downsizing an internal combustion engine are thermodynamic (increased engine efficiency/fuel economy) and mechanical (friction reduction), which lead to higher thermal and thermooxidative stresses and quicker wear. As the trend toward downsized/compacted engines continues, there will be a continual need for lubricants that perform better in a number of regards.
Dr. Sigismondo Ferrante, CEO of oil analyst SMOC Europe S.r.l., explains, “Higher power and smaller reservoirs mean that lubricant has to be adequate for those purposes. Less lubricant equals less thermal dispersive power. So in special cases, such as heavy duty applications, there will be the need for new additives, maybe with the help of nanotechnology—as with boron nitride-based coatings.”
STLE-member John Sherman, technical manager, fuel and lubricant solutions, BASF Corp., explains, “I believe future hydraulic fluids will require additive packages with greater performance in properties that would include thermal oxidative stability and air release to compensate for the added stress put on the hydraulic fluid in compact hydraulic systems. Increased use of compact hydraulic units also may accelerate a transition to synthetic hydraulic fluids, some of which may already meet the performance demands of those systems.”
5. New Surface Treatments
There have been antifriction metal case-hardening treatments on the market for many years that either eliminate or greatly reduce the need for lubricants in some applications. Examples include carburizing, nitriding and boriding.
Boriding is a thermo-chemical surface hardening method that can be applied to a wide range of ferrous and non-ferrous materials. The process diffuses boron atoms into the lattice of the parent metal, forming a hard interstitial boron compound at the surface. Boriding creates a uniform layer of hardness through the entire diffused layer. As with other forms of case hardening, the combination of high hardness and low friction coefficient improves wear, abrasion and surface fatigue properties. Other benefits associated with boriding are corrosion resistance and reduction of lubricants use. But because of the cumbersome process, the use of boriding has historically been limited.
A recent development is ultra-fast boriding, largely developed by STLEmember Dr. Ali Erdemir, senior scientist at Argonne National Laboratory. It is an advanced electrochemical process that is significantly faster than standard boriding, making it economically practical for many applications. Additional research is underway.
Zweifel says, “Equipment builders will implement new sophisticated materials and surface finishes, i.e., on bearing materials such as DLC (diamond- like coating) to lower friction. This will require lubricants which are adapted to the new materials and surfaces designed.”
6. Emerging New Economies
A new market research report, “World Lubricants to 2017,” (
3) predicts the global demand for lubricants will increase 2.4 percent per year to 2017. Growth will be spurred by economic expansion, increased vehicle ownership and the continued industrialization of developing countries in Asia, South America, Africa and the Mideast.
The report goes on to say that there will be very limited lubricant growth in North America and Western Europe where increased lubricant applications will be offset by longer drain intervals. The good news is that while volume growth will be restrained in these regions, there will be greater need for premium, high value products such as synthetics. Globally, the motor vehicle aftermarket will continue to comprise the largest share of lubricant consumption—with greater demand for engine oils and transmission fluids in developing countries as the number of cars and trucks climbs.
The report says that while extended drain intervals will continue to slow growth in the U.S., Western Europe and Japan, extended drain intervals won’t prevent strong growth in rising manufacturing powers that include China and India. The report predicts that the strongest growth will be for process oils since they are less affected by increased lubricant efficiency than other products. Hydraulic fluids, general industrial oils, gear oils and greases widely used in manufacturing can expect better than average growth.
INTERVIEW WITH EXXONMOBIL’S MIKE SHEEHAN
Following is an interview with Mike Sheehan, global technology synthetics, marketing technical service engineer, ExxonMobil Chemical Corp. He has over 28 years of experience in the synthetics division covering new product and process development of synthetic basestocks and formulation development of aviation turbine lubricants. Prior to joining ExxonMobil, he worked for Burmah Castrol Oil (now BP) as a research chemist in the Automotive and Industrial Lubricants Group. Sheehan is a member of STLE, SAE, ACS and ASTM.
Mike Sheehan
TLT: Many OEMs in the industrial and automotive industry are designing more compact equipment with higher power density and smaller reservoirs. What impact will this have on the performance needs of future lubricants?
Sheehan: Higher power density will subject lubricants to increased bulk temperatures resulting in higher oxidation and thermal degradation processes. We would expect future lubricants to have improved oxidative and thermal stability properties, as well as lower volatility to address these severe operating conditions. Smaller reservoirs reduce the time available for lubricants to “relax” and release contaminants such as water and air. Good air release, low foaming and better heat transfer characteristics will be required by new lubricants.
TLT: Looking forward 20-30 years, do you foresee any radical changes to the types of lubricants that will be used or will the performance of today’s lubricants suffice?
Sheehan: We would expect future lubricants to have improved volatility, oxidative stability and lower coefficient of friction, providing improvements in energy efficiency and longer service life. We believe PAO demand will continue to grow as mineral-based lubricants are replaced with advanced synthetic lubricants. We also foresee future lubricant formulations will require higher levels of Group V basestocks to assist in meeting more stringent performance requirements. With a variety of chemistries, Group V basestocks will provide more versatility either as co-basestock to Group I to IV base oils, or as neat base oil.
TLT: Do you think we are reaching a plateau in performance in what is really achievable with hydrocarbon lubricants (based on Group I-IV base oils)?
Sheehan: We foresee room for improvement in volatility, viscometric properties and oxidative stability. The scientific community is always looking at creative ways to improve product performance and extend oil drain intervals. I think that we have definitely seen a plateau in performance for Group I-based lubricants, particularly for automotive lubricants. There have been innovations in catalyst and process technologies that enable improved performance in Group II and III base oils.
TLT: Since product development cycle times and resulting payback are often very long, is it affordable to innovate and bring new technology to market?
Sheehan: Investing in high-performance lubricants can provide significant benefits in terms of energy savings, improved productivity or reduced maintenance. We believe both current and future Group IV and V base oils will assist lubricant formulators in meeting increasingly challenging performance requirements. Indeed, the product development cycle times can be long and costly. However, the pain of change is probably lower than the pain of being the same.
7. Demand for Better Fuel Efficiency
Scherer explains, “Group V oils will be increasingly important for novel fuel economy oils. A key disadvantage of Group I-IV base oils is their hydrocarbon nature, which renders them non polar and thus limits their contribution to friction performance and ultimately fuel economy. This is different in the case of Group V oils, which are much more polar than Group I-IV oils. There are already many studies and field trials proving the superior contribution to fuel economy of Group V against Group I-IV oils. This is one of the major reasons why we expect further innovation leading to novel technologies within the Group V base oil space.”
Generally, fuel efficiency improves when there is less friction. But less friction means a lower viscosity lubricant and possibly less protection for machinery parts. Researchers are currently working on lubricants and additives that provide a meaningful increase in fuel efficiency (greater than the current 1-4 percent) without compromising protection. Experts say that reducing viscosity alone is limited to an approximate 0.5 percent reduction in fuel consumption in heavy-duty vehicles. Reducing boundary friction alone by 90 percent can reduce the fuel consumption of heavy-duty fleets by 1 percent. But combining low viscosity lubricants with low boundary friction technologies enables greater savings in fuel consumption (3-4 percent) (
4).
Scherer explains, “From a volume point of view—for engine oils, which represent the largest sector within the industry—it will be challenging to provide a short- to mid-term alternative technology to hydrocarbons. For other sectors, such as industrial oils or selected lubricants used in the transportation industry (gear, axle or transmission oils), there is no volume concern.”
For gasoline engines, SAE 0W-20 lubricants are not far away. Most auto manufacturers in Japan have already approved SAE 0W-20 oils. For heavy duty diesel engines, SAE 5W-30 and 5W-40 synthetic oils are emerging in the market. HTHS (high-temperature/ high-shear) viscosity is widely seen as the most critical lubricant property for fuel economy. The lower the HTHS, the better the fuel economy (
5).
“Researchers continue to push the boundaries of what is possible with hydrocarbon-based lubricants. For example, the move toward 0W-16 engine oils in Japan and 0W-20 oils in Europe are steps to even greater energy-efficient engine oils,” Zweifel says. “The exploration of even lower viscosity oils continues. Modern hydrocarbon oils may be reaching their limits without compromising engine protection and endurance. Specific properties such as attaining a low base oil viscosity while minimizing volatility losses becomes the limiting factor. That may open up innovation into unconventional or non-hydrocarbon base fluids for the future, and so we may see a swing to more research in this area. In parallel, closer relationships with equipment builders will be needed and perhaps the emergence of newer metallurgies and surface finishes.”
“There is still a significant amount of innovation underway across the lubricant industry,” Zweifel adds. “Dow Chemical is actively involved with industry partners to assess the extent of fuel efficiency gains using polyalkylene glycols as primary base oils in new automotive lubricants. We see a high interest from the industry in the performance properties of these Group V oils. They offer inherently good characteristics such as high VI, good low temperature viscometrics and good film-forming behavior. Furthermore, we have invested in developing a new type of Group V base oil, which we call
Oil Soluble Polylalkylene Glycols (UCON™ OSP) that are now being used as components of modern lubricants. These grades can be used as primary base oils, co-base fluids or additives to upgrade hydrocarbon-based formulations. They offer specifically excellent deposit and friction control and other key features.”
8. Increase in Alternative-Fuel Vehicles
Alternative fuels include bio-based, natural gas-derived, synthetic and hydrogen. The 2013 Annual Energy Outlook significantly dropped predicted 2035 sales of alternative fuel vehicles by more than 37 percent over the 2012 prediction for 2035. The major cause was flex-fuel (
6) vehicles (1.6 million less than the 2.9 million predicted in the 2012 report). Predicted sales of battery- powered electric vehicles also dropped from 340,000 in the 2012 report to 119,000 in the 2013 report.
Partly offsetting the losses from flex-fuel vehicles and electric vehicles is an increase in predicted sales of hybrid and plug-in hybrid vehicles, which are about 20 percent higher than the previous forecast of 1.08 million, reaching about 1.3 million vehicles in 2035. The 2013 report goes on to say that sales of all-electric vehicles are limited by continued fuel economy improvement in other vehicle types, as well as unfavorable attributes in terms of vehicle range, trunk space and cost, particularly regarding batteries. Because of these and other factors, manufacturers are moving toward hybrids and away from electric (
7). This trend plays into the future lubricants market in several ways. For example:
•
All-electric vehicles do not use any engine oil.
•
Formulators are already creating specialized engine oil for alternative fuel vehicles.
•
Alternative fuel vehicles require a tailored oil analysis strategy.
“A continuing trend is the development and use of combustion engines in hybrid vehicles,” Zweifel says. “These hybrid vehicles are equipped with small combustion engines that have specific lubrication needs. Group V base oil formulations are often required (i.e., 0W-20 and below). These oils need to ensure that not only is fuel efficiency improved but also engine protection and durability are maintained at a minimal level to ensure equipment reliability.
Due to emission regulations, internal combustion engines are also equipped with more complex after treatment devices for emission control (NO
x, CO
2, CO, particulates). Because no combustion residues of lubricants should contaminate the catalytic devices, the lubricant needs to burn cleanly and residue-free.”
THE FISCHER-TROPSCH PROCESS (9, 10)
The Fischer-Tropsch process was developed in the 1920s to convert a mixture of carbon monoxide and hydrogen (syngas), into hydrocarbon chains. The process is straightforward: syngas is fed at high temperatures through materials such as cobalt, iron and ruthenium that catalyze the hydrocarbon formation.
When combined with processes such as steam reforming that first convert natural gas into syngas, the Fischer-Tropsch process can effectively be viewed as a method to transform any available carbon source into hydrocarbon chains. An issue with Fischer-Tropsch is that it doesn’t get around the feedstock sustainability problem. Like petroleum, eventually natural gas is going to run out.
9. Tighter Environmental Regulations
Experts say that for mature markets in the U.S., Western Europe and Japan, any growth in the lubricant market will be driven more by the stricter implementation of environmental regulations than by demand for lubricants in general (
8).
Zweifel believes that innovation in the next 30 years will be driven by high levels of regulatory pressure for emission reduction and fuel consumption. This innovation might include the development of new hydrocarbon base oils through newer catalyst technology or the emergence of non-conventional Group V type base oils that offer greater thermal stability and improved friction control.
Scherer says, “Sustainability should be a strong driver behind every novel lubricant technology. Renewability, however, is no prerequisite for sustainability. Strong sustainability characteristics can be achieved with both renewable and petrochemical-based lubricants. For that reason, you will find both renewable and non-renewable basestocks in our existing portfolio and in our innovation pipeline.”
ENVIRONMENTAL REGULATIONS AND THE PRICE OF NATURAL GAS
Hydraulic fracturing (fracking) is responsible for the rapid expansion of U.S. natural gas reserves and thus the sudden and significant drop in natural gas prices. But a number of factors will affect the sustainability of the relatively low price. One is just how tight the (sure to be proposed and imposed) EPA regulations will be.
Current fracking regulations address only the potential pollution generated by the process itself, i.e., diesel emissions from fracking equipment. But the EPA is vigorously working on a set of more stringent regulations.
Compliance is sure to affect the profitability of fracking operations and the resulting price. The future price is, in fact, so uncertain that the South African company Sasol, which plans to build a $14 billion plant in Louisiana partly to convert natural gas to diesel, has said it will reassess the economics of its planned project just before it breaks ground sometime in 2014 (
11).
10. Widespread Availability of Natural Gas
The widespread availability of natural gas has been (or will be) a game-changer in just about every U.S. industry, including lubricants. In fact, natural gas has been a major catalyst for the return of manufacturing to the U.S. Consider that, right now, in the U.S., it costs $300 to make a ton of ethylene in natural gas-operated plants. Just a few years ago, it cost $1,000 for plants operating on oil to produce the same amount. According to an analysis by PricewaterhouseCoopers, it now costs $1,717 to make a ton of ethylene in Asia—because plants depend on high-priced oil instead of natural gas—and $455 to make it in Saudi Arabia, using a combination of ethane and butane (
12). Natural gas prices dropped from a high price of $10.79/MCF (
13) in July 2008 to a low price of $1.89/MCF in April 2012 (
14).
This new, inexpensive energy source is also responsible for the shift toward natural gas fleet vehicles and, as mentioned above, can itself be formulated into a lubricant base. The big question is just how long U.S. natural gas will stay relatively inexpensive. Some analysts say that Wall Street investors have artificially driven the price down to a level that cannot be sustained for long (
15).
As the requirements of consumers, government agencies and OEMs evolve, lubricant manufacturers, formulators and additive developers also are evolving. These 10 trends will all contribute to adoptions that the lubricants market needs to make in coming years.
“Today’s lubricants will not fit market needs in 20 years,” Ferrante concludes. “Remember that not that long ago we were using lead-based lubricants. Another factor that will force change is that the supply of crude oil is finite. In terms of performance improvements, Group I-III base oils are pretty close to a plateau. But for chemically formulated Group IV lubricants, the door is always open to the introduction of a new
miracle molecule.”
REFERENCES
1.
From 2012 BP Annual Report: click
here.
2.
Group III basestock has a VI of at least 120; Group III+ has a VI of at least 140.
3.
Click
here. This study examines the global market for finished lubricants. Products covered include engine oils, process oils, hydraulic fluids, metalworking fluids and other lubricants.
4.
Click here.
5.
Click
here.
6.
Flex-fuel vehicles are capable of running on gasoline or ethanol.
7.
Click
here.
8.
Click here.
9.
For an excellent explanatory video, visit
here.
10.
Click
here.
11.
Click
here.
12.
Click
here.
13.
One MCF is equal to 1,000 cubic feet or 10 therms. A cubic foot of gas is the amount of gas needed to fill a volume of one cubic foot under specific conditions of pressure and temperature.
14.
Click
here.
15.
Click
here.
Jeanna Van Rensselar heads her own communications firm, Smart PR Communications, in Naperville, Ill. You can reach her at jean@smartprcommunications.com.