The road to better mileage
Dr. Edward P. Becker | TLT Automotive Tribology February 2014
As much as a third of the fuel burned in today’s vehicles is used to overcome ‘wasteful friction.’
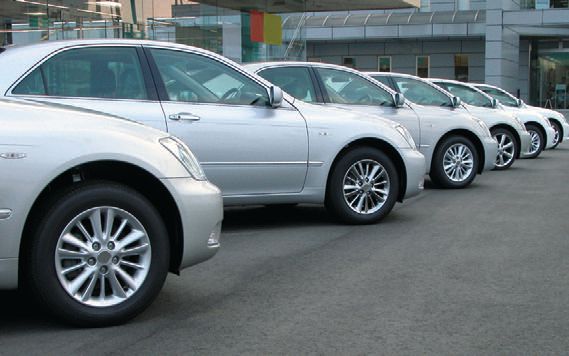
U.S. cars must increase their fuel efficiency to 54.5 miles per gallon by model year 2025.
www.canstockphoto.com
IT’S A GREAT TIME to be a tribologist in the automotive industry!
The automotive industry, indeed, has historically provided much opportunity to those skilled in the arts of friction, lubrication and wear. However, the latest round of fuel economy standards enacted in the U.S. and consumer demand for higher efficiency in light of the increasing cost of fuel will absolutely require the best efforts of tribologists around the world.
In the U.S., current agreements in place require automakers to nearly double the fuel economy from current values to 54.5 miles per gallon (4.36 liters per 100 km) by model year 2025. While there are significant developments in competing powertrains, it is very likely that the vast majority of vehicles sold in the coming decade will be powered by the internal combustion engine. According to research published in 2012 by Drs. Ken Holmberg, Peter Andersson and Ali Erdemir, (
1) as much as a third of the fuel burned in today’s vehicles is used to overcome friction. Roughly another third is lost through heat rejection (as required by thermodynamics), which means that currently only about a third of the energy in the fuel is actually used to propel the vehicle and provide power to the accessories.
So can we double fuel economy by eliminating friction? Actually, that would be a really bad idea. Without friction, tires would just spin on the road, and even if you did get the vehicle moving friction between the road and tires is needed for steering, brakes rely on friction to stop the vehicle, and friction is how force is transferred between components such as clutches, belts and pulleys. So some energy will always be lost through useful friction.
There are, however, many opportunities to reduce wasteful friction, such as in bearings, pistons and valve components. Holmberg and his co-authors estimate that as much as 61 percent reduction in friction losses is possible over the long term.
Thus, reduction in friction losses has the potential to produce more than half of the improvement needed in fuel economy. The remainder must come from other strategies. Fuel economy standards were first implemented in the United States in 1975 (
2), and automakers have responded primarily in two ways.
First, reducing vehicle weight reduces the amount of energy needed to propel the vehicle. This practice, also called downsizing, has resulted in a much smaller and lighter population of cars on the road. However, consumers who wanted larger vehicles responded by purchasing more light trucks and crossover vehicles based on truck chassis, which had different fuel economy requirements. The 2015 requirements take into account the mix of vehicles on the road.
The second method of increasing fuel economy is to use smaller engines, which have fewer moving surfaces where friction occurs. The trend to fewer V6 and V8 engines and more in-line 4 cylinders is well established, with even a few 3-cylinder engines in production. The obvious disadvantage of the smaller engine is less peak power to accelerate the vehicle. This can be ameliorated somewhat by boosting the engine, either turbocharging or supercharging. The turbocharger has the additional advantage of recovering some energy from the exhaust stream, thus further increasing efficiency.
I will cover some of these advances in greater detail in future columns. I’ll also discuss the alternative propulsion systems currently being touted as replacements for the internal combustion engine. In the meantime, I’ll be looking for some great ideas from you automotive tribologists!
REFERENCES
1.
Holmberg, K., Andersson, P. and Erdemir, A. (2012), “Global Energy Consumption Due to Friction in Passenger Cars,”
Tribology International,
47, pp. 221-234.
2.
Click here.
Ed Becker is an STLE Fellow and past president. He is president of Friction & Wear Solutions, LLC, in Brighton, Mich., and can be reached through his website at www.frictionandwearsolutions.com.